The hydraulic hose manufacturing process involves a series of precise steps, including material selection, reinforcement, vulcanization, and testing, to ensure the hoses are durable, reliable, and capable of withstanding extreme pressure. Each stage in the process plays a pivotal role in the final product’s performance, making the quality of hydraulic hoses crucial for the safe and efficient operation of hydraulic systems.
Step 1: Sourcing Raw Materials for Hydraulic Hose Production
Types of Materials Used in Hydraulic Hoses (Rubber, PVC, Stainless Steel, etc.)
The foundation of any hydraulic hose lies in the materials used to construct it. Hydraulic hoses are typically made from a combination of synthetic rubber, PVC (polyvinyl chloride), stainless steel, and other specialized compounds. Each material serves a specific purpose in the hose’s overall structure and performance:
Rubber: The most commonly used material for the inner tube and outer cover. Rubber offers excellent flexibility, resistance to abrasion, and the ability to withstand varying temperatures and pressures. Synthetic rubbers like nitrile, EPDM (ethylene propylene diene monomer), and neoprene are commonly used for hydraulic hoses due to their resistance to oil, chemicals, and ozone.
PVC (Polyvinyl Chloride): Often used in lightweight or non-high-pressure applications, PVC is cost-effective and resistant to chemical corrosion. However, it has a lower flexibility and pressure tolerance compared to rubber-based hoses.
Stainless Steel: Used for the reinforcement of hoses, stainless steel wire braids or spirals enhance the strength and pressure resistance of the hose. Stainless steel is preferred for its durability, corrosion resistance, and ability to withstand high-pressure environments, especially in more demanding hydraulic systems.
Other Materials: In some specialized hoses, materials such as polyurethane, polyester, or fluoropolymer coatings may be used for added resistance to abrasion, high temperatures, or chemical exposure.
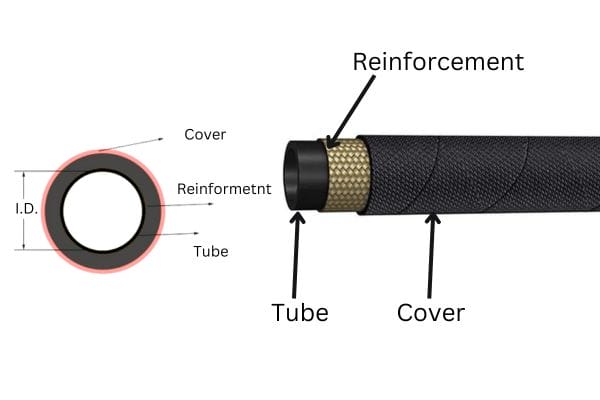
How Material Selection Impacts Hose Durability and Performance
The choice of materials significantly influences the durability, flexibility, and performance of hydraulic hoses. Several factors determine the selection of materials, including:
Pressure Rating: Hydraulic hoses must withstand high pressures without bursting or losing structural integrity. Reinforcing materials like stainless steel wire braid are crucial for enhancing pressure resistance, ensuring the hose can handle the demands of heavy machinery and equipment.
Flexibility and Bend Radius: Hydraulic hoses often need to navigate tight spaces and perform in dynamic systems where the hose is subject to frequent movement. Rubber-based hoses are often preferred for their flexibility, allowing them to bend without kinking or restricting fluid flow.
Chemical and Environmental Resistance: In industrial environments, hoses can be exposed to oils, solvents, UV rays, ozone, and extreme temperatures. The material’s resistance to these elements is essential for maintaining the hose’s performance and longevity. For instance, nitrile rubber hoses are often used in systems exposed to petroleum-based fluids, while EPDM hoses are preferred in environments with exposure to ozone and UV light.
Abrasion Resistance: For hoses exposed to rough surfaces or high-wear areas, materials with excellent abrasion resistance, such as polyurethane or rubber covers, are vital. This prevents the hose from wearing out prematurely and ensures that it can withstand harsh environments without compromising its functionality.
Step 2: Creating the Inner Tube – The Core of the Hydraulic Hose
The Extrusion Process for Forming the Inner Tube
The inner tube is the most critical component of a hydraulic hose, as it is responsible for carrying the pressurized fluid. The process of creating the inner tube begins with extrusion, a method that involves forcing heated rubber or synthetic materials through a mold or die to form a continuous tube shape. The extrusion process ensures that the inner tube has a smooth and consistent surface, which is essential for maintaining fluid flow without obstruction or turbulence.
Material Heating and Melting: The rubber compound is first heated to a molten state, making it soft enough to flow through the extrusion die.
Extrusion Through a Die: The molten rubber is then pushed through a specifically shaped die, which forms the tube to the required diameter and thickness. This step is critical to ensuring the correct wall thickness and smoothness of the inner tube, which directly affects its ability to withstand pressure and resist wear.
Cooling and Setting: Once the rubber has been extruded through the die, it is cooled using a water bath or air cooling system, solidifying the shape of the tube.
The extrusion process allows manufacturers to produce inner tubes with precise dimensions, ensuring uniformity and consistency across every hose produced.
Types of Rubber Compounds Used for Inner Tubes
The type of rubber compound used in the inner tube plays a vital role in the hose’s ability to resist pressure, abrasion, and chemical degradation. The most common types of rubber compounds used for hydraulic hose inner tubes include:
Nitrile Rubber (NBR): Nitrile rubber is widely used for hydraulic hoses, especially in applications involving petroleum-based fluids and oils. NBR is known for its excellent oil resistance and durability under high-pressure conditions. It is ideal for hydraulic systems in industries like automotive and machinery, where petroleum-based fluids are common.
EPDM Rubber (Ethylene Propylene Diene Monomer): EPDM rubber is resistant to ozone, UV rays, and weathering, making it suitable for hydraulic hoses exposed to outdoor environments. While it is not as oil-resistant as nitrile rubber, it offers excellent resistance to water, steam, and many chemical compounds.
Neoprene Rubber: Neoprene is used for applications that require resistance to oil, fuel, and a wide range of chemicals. It also provides flexibility and durability, making it suitable for hydraulic systems with more demanding fluid types.
Fluoroelastomers (FKM): For extreme chemical resistance, fluoropolymers such as FKM (Viton®) are used. These are ideal for high-temperature applications where the fluid may contain aggressive chemicals, acids, or high-temperature oils.
The choice of rubber compound depends on the type of fluid being conveyed, the temperature range, and the environmental conditions the hose will be exposed to.
Step 3: Reinforcement – Strengthening the Hose for High Pressure
Different Types of Reinforcement Materials (Steel Wire, Braiding, Spiraling)
Reinforcement is a critical part of the hydraulic hose manufacturing process. It adds the strength and durability necessary to handle high-pressure conditions, while also preventing the hose from expanding or bursting under pressure. There are several types of reinforcement materials used to achieve this:
Steel Wire: The most common reinforcement material used in hydraulic hoses is steel wire, which provides excellent tensile strength. Steel wire is ideal for high-pressure applications and is resistant to wear and abrasion. The wire is typically formed into braids or spirals to increase the hose’s resistance to pressure.
Braiding: In braided reinforcement, multiple steel wires are woven together in a criss-cross pattern to form a layer that strengthens the hose. The braiding method is ideal for hoses that need flexibility as well as high pressure resistance. Braided reinforcement helps distribute pressure evenly along the hose, preventing localized weak points that could cause ruptures.
Spiraling: Spiral reinforcement involves winding steel wires around the inner tube in a helical or spiral pattern. Spiral reinforcement provides higher resistance to higher pressures and is often used in hoses exposed to severe or dynamic conditions. It is more rigid than braided reinforcement but offers superior pressure resistance, especially in applications where the hose must withstand pulses or fluctuations in pressure.
Hybrid Reinforcement: Some hydraulic hoses use a combination of braided and spiral reinforcement layers. This hybrid approach combines the flexibility of braiding with the strength of spiraling, providing both durability and the ability to withstand extreme pressure.
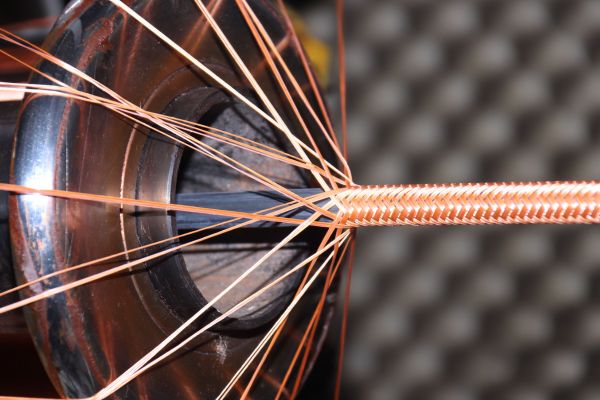
The Process of Braiding and Spiraling Reinforcement Wires
The process of reinforcing the hydraulic hose with steel wire involves two main methods: braiding and spiraling.
Braiding Process:
In the braiding process, multiple steel wires are woven together using high-speed machines. The wire is arranged in a pattern where it crisscrosses over and under each other, creating a strong and flexible layer. This method allows the hose to bend more easily while maintaining high tensile strength.
During the braiding, machines automatically move the wires in a way that ensures the proper tension and coverage, providing uniform reinforcement across the entire length of the hose. The braided layer is applied over the inner tube after it has been formed, and the number of braids (e.g., single or double braid) will affect the overall strength of the hose.
Spiraling Process:
In the spiraling process, steel wire is wound around the hose in a continuous spiral, forming multiple layers of reinforcement. The wire is wound at a precise angle to ensure maximum strength and pressure resistance.
Typically, the spiral layer is applied in stages, with additional layers of wire added for extra strength. The spiral reinforcement provides more rigid support for the hose, particularly in high-pressure applications or hoses subjected to external abrasion or pressure spikes.
Spiral reinforcement is often used for hoses that require heavy-duty applications, such as those in oil and gas drilling, mining, and other high-pressure environments.
Step 4: Adding the Outer Cover
Types of Outer Cover Materials (Rubber, PVC, Thermoplastic)
The outer cover of a hydraulic hose plays a crucial role in protecting the hose from environmental factors such as abrasion, UV radiation, chemical exposure, and extreme temperatures. It acts as the first line of defense against damage from external sources, ensuring that the inner layers (tube and reinforcement) remain intact and function properly. There are several materials commonly used for the outer cover of hydraulic hoses, each offering specific benefits based on the application:
Rubber: Rubber is the most widely used material for hydraulic hose covers due to its excellent abrasion resistance, flexibility, and ability to withstand a variety of harsh environments. It is often chosen for its resilience to heat, ozone, UV exposure, and chemicals. Synthetic rubbers such as EPDM (ethylene propylene diene monomer) and NBR (nitrile rubber) are commonly used for the outer cover, providing additional resistance to oils, fuels, and chemicals.
PVC (Polyvinyl Chloride): PVC is a more cost-effective material used in hydraulic hoses where abrasion resistance is less critical. It offers basic protection from environmental elements like moisture and some chemicals, though it has lower resistance to high temperatures and pressure than rubber. PVC-covered hoses are typically used in lighter-duty or low-pressure applications.
Thermoplastic: Thermoplastic materials, such as polyurethane and nylon, are also used for hydraulic hose covers, especially in situations requiring extreme flexibility and lightweight hoses. Thermoplastic hoses provide excellent resistance to abrasion, oils, and ozone, making them ideal for demanding environments. These materials are often used in applications where hoses must bend easily or be exposed to fluctuating temperatures.
Thermoplastic Elastomer (TPE): TPE combines the properties of rubber and plastic, offering flexibility, weather resistance, and enhanced abrasion protection. TPE-covered hoses are commonly used in food processing, pharmaceutical, and industrial applications where high levels of cleanliness and flexibility are necessary.
The Process of Extruding the Outer Cover
The process of adding the outer cover to the hydraulic hose involves extrusion, a manufacturing method that shapes the material into a continuous cover over the reinforced hose core. The extrusion process ensures that the outer cover adheres securely to reinforcement and provides uniform protection against environmental hazards.
Material Selection and Preparation: The chosen material (rubber, PVC, or thermoplastic) is prepared by mixing it with specific additives that enhance its performance. For example, UV stabilizers, anti-aging agents, and anti-abrasion compounds may be added to improve the longevity and durability of the cover.
Extrusion Process:
The raw material is heated and softened, typically in an extrusion machine where it is forced through a die that shapes it into the desired form. The extruder applies pressure to push the material around the braided or spiraled reinforcement, ensuring the cover bonds securely to the underlying layers.
The extruder is designed to maintain consistent pressure and temperature, which is crucial for achieving an even and smooth outer layer. The material is shaped into a continuous tube that fits snugly over the hose’s reinforcement layer.
Cooling and Setting: After the outer cover is extruded, it is rapidly cooled to set the shape and ensure it retains its structure. This cooling phase helps solidify the material and allows it to harden, creating a protective barrier around the hose.
Cutting to Length: Once the extruded outer cover has cooled and solidified, the hose is cut to the required lengths. This ensures that the finished hose is ready for assembly or further processing, such as fitting installation.
Step 5: Vulcanization – The Secret to Durability and Flexibility
What is Vulcanization and Why It’s Essential for Hose Quality
Vulcanization is a critical process in the manufacturing of hydraulic hoses, where heat and pressure are applied to the rubber compounds used in the hose. This process chemically bonds the rubber molecules, improving the material’s strength, durability, and flexibility. Essentially, vulcanization transforms raw rubber into a more stable and versatile material that can withstand the demanding conditions of hydraulic systems.
Vulcanization involves the addition of sulfur or other cross-linking agents to the rubber compound, which creates cross-links between the polymer chains. This curing process results in the rubber becoming harder, more heat-resistant, and more resistant to abrasion, chemicals, and other environmental factors. For hydraulic hoses, this means the hose will last longer, resist damage from friction, and perform reliably under high-pressure conditions.
How Heat and Pressure Create Durable, Flexible Hoses
The vulcanization process is achieved through a combination of heat and pressure, which together cause the rubber molecules to bond in a way that enhances the material’s properties. Here’s how the process works:
Preparation of Rubber Compound:
Before vulcanization, the rubber material is mixed with other chemicals, such as sulfur, accelerators, and activators, to create the right balance of hardness, flexibility, and durability. This compound is then ready to undergo the curing process.
Vulcanization Chamber:
The rubber compound, along with the reinforced hose (inner tube, braiding, and outer cover), is placed into a vulcanizing chamber (also known as an autoclave or curing oven). In this chamber, the hose is exposed to high temperatures (usually between 160-200°C or 320-390°F) and pressure for a specified period.
Cross-Linking:
The combination of heat and pressure initiates a chemical reaction in the rubber, causing the polymer chains to link together, creating a more complex network structure. This cross-linking process is what gives the rubber its enhanced durability, flexibility, and resistance to wear.
The cross-links formed during vulcanization are what make the rubber more stable, preventing it from deteriorating under high pressure, extreme temperatures, or exposure to chemicals.
Cooling and Setting:
Once the vulcanization process is complete, the hose is cooled gradually to allow the rubber to harden and set into its final shape. The cooling process solidifies the chemical bonds created during vulcanization, ensuring that the hose retains its new properties.
Final Inspection and Quality Control – Ensuring Each Hose is Ready for Use
Detailed Inspection Process to Check for Defects or Inconsistencies
The final inspection and quality control phase is one of the most critical steps in the hydraulic hose manufacturing process. This stage ensures that each hose meets the required performance standards and is free from defects or inconsistencies that could compromise its safety and functionality. During this process, a variety of visual, mechanical, and dimensional checks are performed:
Visual Inspection:
The hoses are carefully inspected for surface defects such as cracks, cuts, blisters, or any foreign contaminants embedded in the material. Any imperfections in the outer cover or reinforcement can affect the performance of the hose, especially under high pressure.
Dimensional Checks:
The hose’s length, diameter, and wall thickness are measured to ensure they conform to the specified tolerances. Even small variations in size can lead to improper fitment or reduce the hose’s pressure tolerance.
Pressure Testing:
Each hose undergoes pressure testing to verify that it can handle the specified operating pressure without any signs of failure. This is usually done by pressurizing the hose to a higher level than its rated working pressure to check for any leakage, bulging, or ruptures.
Abrasion and Environmental Testing:
Some hoses undergo abrasion tests or environmental stress testing to simulate real-world conditions. This could involve bending, flexing, or exposure to UV light or extreme temperatures. These tests ensure that the hose will maintain its integrity in the environments it will be used in.
Leakage Tests:
Leak detection is done by using air or fluid to check for leaks along the hose assembly. This test ensures that the hose is completely sealed and will not leak under normal working conditions.
Reinforcement Inspection:
The reinforcement layers (braided or spiral steel wires) are also checked for uniformity and strength. Any inconsistencies in the reinforcement can affect the hose’s pressure tolerance and flexibility.
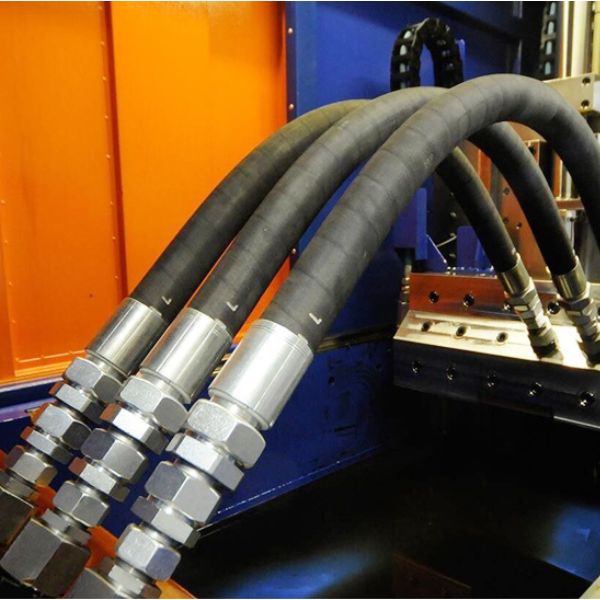
How Each Hose Undergoes Final Checks Before Leaving the Factory
Once the individual inspection steps are completed, the hose is subject to a final round of checks before being approved for shipment or installation:
Marking and Labeling:
Each hose is marked with key information such as part number, pressure rating, manufacturing date, and batch number. This ensures that each hose can be traced back to its production lot in case of any future quality concerns.
Final Assembly:
If applicable, the hydraulic hose will undergo final assembly, which involves attaching the necessary fittings or connectors. These fittings are also inspected to ensure they are securely attached and correctly aligned with the hose ends.
Documentation Review:
The production records are reviewed to confirm that all materials, specifications, and manufacturing steps meet the required standards. This includes reviewing test results from earlier stages of the manufacturing process, ensuring that all tests were passed.
End-of-Line Inspection:
An experienced quality control technician performs a final visual check of the hose to ensure that it is free from defects. If everything meets the criteria, the hose is approved for shipment.
Customization – Tailoring Hydraulic Hoses to Specific Needs
Custom Lengths, Diameters, and Pressure Ratings
Customization is an essential service for clients who require hydraulic hoses to meet the specific demands of their operations. Every hydraulic system is unique, with varying needs based on the machinery, environment, and fluids being handled. Customization allows manufacturers to tailor hoses precisely to those requirements.
Custom Lengths: Clients may require hoses in specific lengths to fit the exact measurements of their hydraulic systems. Whether a hose needs to connect distant components, or it must fit into a compact space, custom lengths ensure that there is no excess hose, reducing clutter and preventing safety risks associated with slack or coiled hoses.
Custom Diameters: Hydraulic hoses come in a range of inner and outer diameters to accommodate different fluid flow rates and pressure requirements. Custom diameters ensure that the hose fits perfectly into connectors and ports, minimizing the risk of leaks, pressure loss, or system inefficiency. Whether the system requires a small-diameter hose for precision control or a larger hose for high-volume applications, tailored sizing ensures optimal flow.
Custom Pressure Ratings: Not all hydraulic systems operate at the same pressures. Some systems require hoses rated for very high pressure (up to 10,000 psi or more), while others may only need hoses rated for low-pressure conditions. Custom pressure ratings allow clients to choose hoses that can safely handle the pressures of their specific applications without unnecessary over-specification, which can lead to higher costs.
Custom Labeling, Printing, and Packaging Options
In addition to functional customization, many clients also require branding and aesthetic customization for their hydraulic hoses, especially for retail, distribution, or specialized equipment. Custom labeling and packaging help reinforce brand identity, improve product traceability, and enhance the presentation of the final product.
Custom Labeling: Custom labels allow manufacturers to provide key product details, such as part numbers, pressure ratings, manufacturing dates, and safety warnings, directly on the hose. This ensures that users can easily identify the hose’s specifications and understand its intended application. It also helps with maintenance schedules, as hoses can be traced back to their production batch for any quality checks.
Custom Printing: Some clients may want specific logos, company names, or other marketing messages printed directly onto the hose or its cover. This not only promotes brand visibility but can also make it easier to identify hoses in a complex system, improving maintenance efficiency. Custom printing may also include barcodes or QR codes for easy digital access to product specifications and usage guidelines.
Custom Packaging: Packaging plays an important role in protecting the hydraulic hose during shipping and storage. Customized packaging options, such as specific reel sizes or protective wraps, ensure the hoses are stored safely and are presented in a way that is convenient for end-users. Packaging customization can also help with reducing packaging waste, optimizing storage, and facilitating easier handling.
Conclusion
To ensure the highest quality, it’s essential to choose a reliable manufacturer that prioritizes expertise, quality control, customization capabilities, and customer support. If you have any needs, you can contact Topa and we will provide you with the highest quality hydraulic hose products.
FAQ
What materials are used in hydraulic hose manufacturing?
Hydraulic hoses are made from materials like rubber, PVC, stainless steel, and thermoplastics, each chosen for its specific properties such as flexibility, durability, and pressure resistance.
How is the inner tube of a hydraulic hose made?
The inner tube is formed through an extrusion process, where rubber compounds are shaped to provide fluid containment and pressure resistance, ensuring optimal performance.
What is the purpose of reinforcement in hydraulic hoses?
Reinforcement, typically made of braided or spiraled steel wire, adds strength to the hose, enabling it to withstand high-pressure environments without failure.
Why is vulcanization important in hydraulic hose manufacturing?
Vulcanization is a process that bonds rubber molecules together, increasing the hose’s strength, flexibility, and heat resistance, essential for long-lasting performance.
Can hydraulic hoses be customized for specific needs?
Yes, hydraulic hoses can be customized in terms of length, diameter, pressure rating, and even labeling or packaging to meet the unique requirements of different industries.
What are the key factors when choosing a hydraulic hose manufacturer?
When selecting a manufacturer, consider factors like expertise, quality control processes, customization capabilities, and reliable customer support to ensure high-quality products.