A well-functioning ball valve ensures that fluids are controlled precisely, minimizing wastage, improving flow rates, and preventing dangerous leaks or system malfunctions. Proper operation also prevents damage to downstream equipment and protects against system failures that could lead to costly downtime, safety incidents, or regulatory non-compliance.
Understanding Ball Valve Construction and Components
Core Components of a Ball Valve
A ball valve is a simple yet effective device, and its reliable performance depends on several key components, each of which plays a vital role in its operation. Understanding these components will help you appreciate how the valve works and how to maintain or troubleshoot it.
Valve Body:
The valve body is the outer casing that holds all the internal components together. It is the largest part of the valve and is designed to withstand the pressure and temperature conditions of the system. The body provides the connection to the pipeline and serves as the support for the other internal components, ensuring they function properly under pressure.
Ball:
The ball is the central component of the valve and controls the flow of fluid. It has a hole or port through the middle, and by rotating 90 degrees, the ball either aligns the hole with the pipeline to allow fluid flow or turns the hole away from the flow path to block it. The ball is typically made of materials like stainless steel, brass, or a ceramic compound, depending on the valve’s application.
Seats:
The valve seats are placed around the ball and provide the sealing surface that ensures the valve creates a tight shut-off when closed. The seats are designed to create a pressure-tight seal against the ball to prevent leakage. They can be made from various materials, such as PTFE (Teflon), PEEK, or elastomers, depending on the media being controlled and the temperature and pressure requirements.
Stem:
The stem connects the valve handle or actuator to the ball inside the valve. It transmits the motion of the actuator (manual or automated) to the ball, allowing it to rotate. The stem is usually fitted with seals to prevent leaks of fluids around it. This component is essential for ensuring the valve opens and closes smoothly.
Actuator:
The actuator is the mechanism used to operate the ball valve. It can be manual (a handwheel or lever), electric (electrically powered motors), pneumatic (air-driven), or hydraulic (fluid-driven). Actuators make it easier to operate valves, especially in systems where the valve is located in hard-to-reach places or needs to be automated for efficiency and safety.
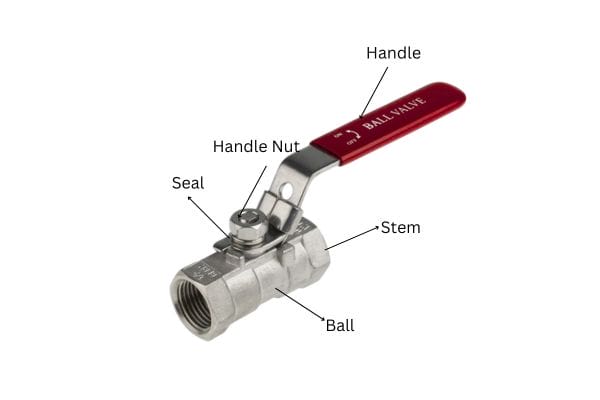
Types of Ball Valves
Ball valves come in several configurations, each designed for different applications. The operation of these valves can vary based on their design and the specific needs of the system.
Standard Ball Valve:
The most common ball valve type, where the ball “floats” and is held in place by the pressure of the fluid. The ball rotates freely inside the valve body. This type of valve is ideal for on/off control in systems with moderate pressure and flow.
Trunnion Ball Valve:
This type of ball valve uses a trunnion-mounted ball that is supported by bearings on both sides, making it more stable under high-pressure conditions. This design reduces the load on the valve seats and is often used in larger valves or systems with higher flow rates and pressures, such as in the oil and gas industry.
Floating Ball Valve:
In a floating ball valve, the ball is not mounted but is instead “floating” and held in place by the pressure of the fluid. This design is more cost-effective for smaller valves and systems with moderate pressure. The floating ball design provides better sealing under low-pressure conditions but is not as suitable for high-pressure applications.
Materials Used in Ball Valves
The materials used in the construction of ball valves are critical to their performance, longevity, and ability to withstand the demanding conditions of different industrial environments.
Stainless Steel:
Stainless steel is one of the most commonly used materials for ball valves due to its excellent corrosion resistance, strength, and durability. It is ideal for handling harsh fluids, high temperatures, and corrosive environments. Stainless steel is often used in the chemical, food processing, and water treatment industries.
Brass:
Brass is another popular material, especially for smaller ball valves used in residential or light industrial applications. It is durable, corrosion-resistant, and offers good thermal conductivity, making it suitable for moderate temperature and pressure conditions. Brass valves are commonly used in plumbing and HVAC systems.
PVC (Polyvinyl Chloride):
PVC ball valves are used in applications involving water or low-pressure systems, such as irrigation, pool systems, and wastewater treatment. PVC is lightweight, corrosion-resistant, and cost-effective, though it is not suitable for high-temperature or high-pressure environments.
How Ball Valves Operate
Basic Function of a Ball Valve
A ball valve is a quarter-turn valve used to control the flow of fluids in a pipeline system. The core component of the valve is the ball, a spherical element with a hole or port through the center. The operation of the ball valve relies on this ball rotating within the valve body to either allow or stop fluid flow.
Opening and Closing Mechanism:
When the valve handle or actuator is turned, the ball inside the valve rotates 90 degrees. In the open position, the hole in the ball aligns with the pipeline, creating an unobstructed flow path. When the valve is closed, the ball is rotated so that the hole is perpendicular to the flow path, effectively blocking the flow of fluid.
Control of Fluid Flow:
Ball valves are typically designed for on/off control, meaning they are either fully open or fully closed. However, ball valves with adjustable flow controls can be used for throttling applications, where the valve is partially open, and fluid flow is modulated. The ball’s smooth surface and rotation allow for easy, efficient control of fluid passage with minimal pressure drop and flow resistance.
Valve Operation Modes
Ball valves can be operated manually or automatically, depending on the application and system requirements. Understanding the different modes of operation is essential for ensuring efficient valve control in various settings.
Manual Operation:
In manual operation, the ball valve is typically operated by a lever, handwheel, or gear actuator, which requires human intervention to turn the valve. This type of operation is common in smaller systems where ease of operation and control is sufficient, such as in residential plumbing, small industrial systems, and some HVAC applications.
Lever Operation: The lever is attached directly to the valve stem and is turned by hand to rotate the ball inside the valve. This simple form of operation is used for smaller, low-pressure systems.
Handwheel Operation: A handwheel is connected to the valve stem and provides greater mechanical advantage to open or close the valve. This is used for larger valves where more torque is required.
Gear Actuator: A gear actuator is often used when precise control and higher torque are needed. The gear mechanism helps with turning the valve stem in industrial settings or where the valve is hard to access.
Automated Operation:
For more complex or remote-controlled systems, ball valves are operated by actuators, which can be pneumatic, electric, or hydraulic. Automated operation is essential in large-scale industrial applications where valves need to be operated frequently, precisely, and often remotely.
Pneumatic Actuators: Pneumatic actuators use compressed air to move the valve ball. These actuators are fast, reliable, and widely used in automated systems, particularly in industries like oil & gas, chemical processing, and water treatment.
Electric Actuators: Electric actuators are powered by electricity and provide precise, controlled movement. They are ideal for environments where precise positioning and adjustable flow control are required. These actuators are often used in systems that require frequent cycling and are commonly found in control systems and automation processes.
Hydraulic Actuators: Hydraulic actuators use pressurized hydraulic fluid to drive the movement of the valve. These are ideal for high-pressure applications, such as in power plants, refineries, and large industrial systems where high force is needed to operate the valve.
The type of actuator used affects the response time, precision, and power requirements of the valve, and each type is suited to different application conditions and operational needs.
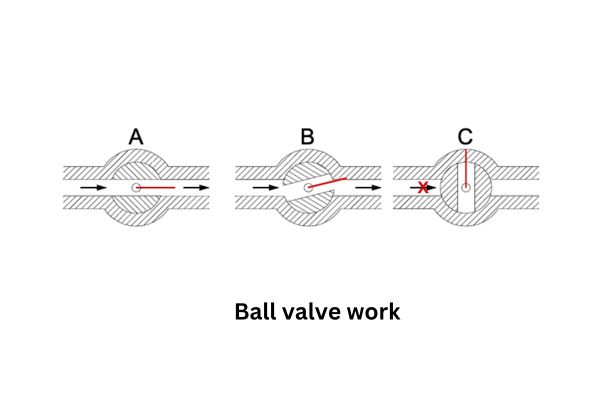
Fluid Flow Control
The way a ball valve is designed influences its ability to control fluid flow. Two primary factors are critical in determining the flow characteristics of a ball valve: the type of ball valve (full-port or reduced-port) and its size.
Full-Port vs. Reduced-Port Ball Valves:
Full-Port Ball Valves: In full-port ball valves, the diameter of the ball’s hole is the same size as the pipe it is connected to. This design allows for unrestricted flow and minimal pressure drop across the valve. Full-port valves are ideal for applications requiring maximum flow rates and low resistance, such as in large piping systems, oil & gas pipelines, and water distribution systems.
Reduced-Port Ball Valves: In reduced-port ball valves, the ball’s hole is smaller than the pipe diameter, which results in some restriction of the flow when the valve is open. While they are often used for applications where flow rates can be controlled, reduced-port valves may cause higher pressure drops due to the smaller opening. These valves are often used in smaller systems or where less flow is needed.
Impact of Valve Size on Flow Rate and System Pressure:
The size of the ball valve has a direct impact on flow rate and pressure. Larger valves generally allow for higher flow rates and are suitable for high-demand systems with large volumes of fluid. Conversely, smaller valves provide better control over fluid flow and are often used in more confined spaces or for precise control in smaller systems.
Large Ball Valves: Larger ball valves are ideal for high-flow applications, where large volumes of fluid need to be regulated or stopped, such as in pipelines, industrial plants, and water treatment systems.
Small Ball Valves: Smaller ball valves are used for applications that require tight control over flow, such as in laboratory settings, pharmaceutical processes, or HVAC systems.
Key Factors That Affect Ball Valve Operation
Pressure and Temperature
Impact of Pressure and Temperature on Valve Performance:
Ball valves are designed to operate within certain pressure and temperature limits, which vary depending on the materials used in the valve construction and the type of valve. Exceeding these limits can cause the valve to malfunction or even fail.
Pressure:
The pressure inside the pipe has a significant impact on the operation of the ball valve. At high pressure, the valve must withstand the force exerted by the fluid. If the pressure exceeds the valve’s rating, the valve body, ball, or seals can become deformed or damaged, leading to leakage, difficulty in operation, or complete failure to open or close.
A ball valve with an insufficient pressure rating will struggle to perform its intended function, resulting in system inefficiency and potential damage to downstream equipment.
Temperature:
Temperature extremes also play a vital role in valve performance. High temperatures can cause thermal expansion of materials, leading to leakage around seals or deformation of valve components. In contrast, extremely low temperatures may cause materials like elastomers or plastics to become brittle, leading to cracking or failure of seals and gaskets.
Operating Pressure Ratings and Temperature Limitations:
Most ball valves are rated with a maximum working pressure and temperature range. For example, a valve designed for use in high-temperature environments may feature heat-resistant seals and materials like stainless steel or alloys that can handle temperatures up to 800°F or higher.
It is essential to ensure that the ball valve selected for an application falls within the pressure and temperature limits required by the system to avoid damage and maintain optimal operation.
Seals and Gaskets
Role of Seals and Gaskets:
Seals and gaskets play a crucial role in ensuring that the ball valve performs correctly by preventing leaks and maintaining a tight seal around the ball and valve body. These components are essential in preventing fluid from escaping when the valve is in the closed position, and they also help maintain the correct internal pressure and flow characteristics when the valve is open.
Impact of Damaged or Worn Seals:
Seals and gaskets can wear down due to continuous exposure to high pressure, high temperature, or aggressive fluids. Once seals are damaged or degraded, they can no longer form a reliable barrier, resulting in fluid leakage around the valve body or stem.
Leaking Around the Valve Body: If the seals between the valve body and the ball are compromised, the valve will leak when in the closed position. This can cause system inefficiencies and even safety hazards in certain applications.
Worn Stem Seals: Worn seals around the valve stem can also lead to leakage, especially in higher-pressure applications where stem seals are critical in maintaining the pressure integrity of the valve.
Maintaining Seals and Gaskets: Regular inspection and replacement of worn seals and gaskets can prevent leaks and ensure continued smooth operation of the valve. Use of the right materials for seals and gaskets based on the specific fluid, pressure, and temperature conditions is also crucial for valve longevity.
Valve Alignment
Importance of Proper Alignment for Optimal Valve Function:
Proper valve alignment ensures that all components of the ball valve function correctly, without excess wear or damage. Misalignment can lead to improper sealing, friction, and uneven wear on valve components, which in turn can reduce the valve’s efficiency and lifespan.
Misalignment Issues:
Misalignment often occurs during installation, and common causes include improper handling, incorrect mounting angles, or errors in the piping system design. When a valve is misaligned, the ball may not rotate freely, resulting in resistance during operation. This can lead to increased wear on the valve stem and seals, as well as difficulty in opening and closing the valve. Misalignment may also cause the valve ball to not fully seat, resulting in fluid leaks even when the valve is in the closed position.
Preventing Misalignment:
Careful installation procedures, including correct torque application and alignment of the valve to the pipeline, are critical to ensure proper valve function. Ensuring that the valve is properly aligned with the surrounding piping can prevent these issues and reduce the likelihood of operational problems in the future.
Lubrication
How Lubrication Affects Ball Valve Operation:
Lubrication plays an essential role in ensuring smooth operation of the ball valve, particularly in valves with manual actuators or those used in high-pressure and high-temperature applications. Lubrication reduces friction between the valve ball and the valve seat, making it easier to open or close the valve and reducing wear on these components.
Impact of Proper Lubrication:
Proper lubrication ensures that the valve components move smoothly, prevents corrosion, and reduces the chances of seizing or sticking due to friction. This is especially important in environments where valves are exposed to extreme temperatures, pressure fluctuations, or corrosive fluids.
Best Practices for Lubrication:
Lubrication Frequency: Regular lubrication schedules should be followed based on manufacturer recommendations and the operating conditions of the valve.
Choosing the Right Lubricant: The choice of lubricant depends on the operating temperature, pressure, and fluid being controlled. High-performance lubricants, such as synthetic oils or greases designed for extreme conditions, may be required for valves operating in harsh environments.
Avoid Over-lubrication: Excess lubricant can cause dirt and debris to accumulate, leading to valve fouling. It is essential to apply the correct amount of lubricant to avoid potential issues.
Conclusion
We encourage readers to assess their ball valves regularly for these key factors, including pressure and temperature conditions, seal wear, alignment, and lubrication status. Regular maintenance, timely repairs, and appropriate lubrication practices are essential to ensure the longevity and reliability of ball valves.
FAQ
What is a ball valve and how does it work?
A ball valve is a type of valve that uses a spherical ball to control the flow of fluid through a pipe. The ball has a hole in the center, and when aligned with the pipe, fluid flows freely. When rotated 90 degrees, the hole is perpendicular to the pipe, blocking the flow.
What are the common causes of ball valve failure?
Common causes of ball valve failure include high pressure, extreme temperature, worn-out seals and gaskets, misalignment, and insufficient lubrication. Regular maintenance and proper installation can prevent most of these issues.
How do I know if my ball valve is failing?
Signs of a failing ball valve include leaks around the valve body or stem, difficulty in opening/closing the valve, unusual noises (like grinding or squeaking), and inconsistent flow or pressure.
What is the role of lubrication in ball valve operation?
Lubrication helps reduce friction between the valve ball and seat, ensuring smooth operation. Proper lubrication also prevents corrosion and extends the valve’s lifespan.
What materials are used in ball valves?
Common materials for ball valves include stainless steel, brass, PVC, and alloys, chosen based on the application. Stainless steel is popular for high-pressure or corrosive environments, while PVC is commonly used for low-pressure and non-corrosive fluids.
How do pressure and temperature affect ball valve operation?
Pressure and temperature extremes can affect the performance of ball valves. High pressure can cause leaks or deformation of valve components, while excessive temperature can degrade seals and gaskets, causing leaks or valve failure.