ISO 8434-2 standards are internationally recognized standards that specify the requirements for 37° flared connectors used in hydraulic systems. This standard is crucial in ensuring the compatibility and reliability of hydraulic connections across various applications, promoting safety and efficiency. The 37° flared connector, a key component of ISO 8434-2, is known for its unique design that provides a robust sealing surface.
Background of ISO 8434-2
ISO 8434-2, established by the International Organization for Standardization (ISO), is a vital standard in the realm of hydraulic systems. It specifically addresses the requirements for 37° flared connectors, which are essential components in a variety of applications where reliable fluid transfer is critical. The origins of this standard can be traced back to the increasing need for uniformity and compatibility in hydraulic fittings, particularly as industries evolved and expanded.
Historical Context and Development
The development of ISO 8434-2 reflects a broader trend toward standardization in engineering practices. As industries grew and globalized, the demand for interchangeable parts became paramount. Early hydraulic systems often relied on a patchwork of designs and specifications, leading to compatibility issues that could compromise system efficiency and safety. In response to these challenges, ISO and other standards organizations sought to create a cohesive framework that would promote uniformity across different manufacturers and regions.
ISO 8434-2 was officially published in the early 2000s, with its foundation laid on extensive research and collaboration among industry experts. This standard was designed to replace and improve upon existing connector specifications, ensuring that new designs would meet the rigorous demands of modern hydraulic applications. By establishing a common set of criteria, ISO 8434-2 aimed to facilitate international trade and improve safety across various sectors that depend on hydraulic systems.
Relation to ANSI/SAE J514
A significant aspect of ISO 8434-2 is its relationship to the American National Standards Institute (ANSI) and the Society of Automotive Engineers (SAE) standard J514. ANSI/SAE J514 outlines specifications for hydraulic tube fittings and is widely used in North America. ISO 8434-2 builds upon this framework, adopting the 37° flare design and unified inch threads, which allows for compatibility with existing ANSI/SAE J514 fittings. This alignment between the two standards enables users to interchange components without extensive modifications to their systems, promoting greater flexibility and ease of maintenance.
The integration of ISO 8434-2 with ANSI/SAE J514 reflects a commitment to creating harmonized standards that cater to a global market. Manufacturers and distributors can offer products that are compatible across various regions, thus enhancing customer satisfaction and minimizing the risk of installation errors.
Overview of Standards and Their Significance
Standards like ISO 8434-2 serve multiple purposes that are crucial for both manufacturers and users. First and foremost, they establish a baseline for quality and performance, ensuring that products meet specific technical requirements. This not only enhances the safety and reliability of hydraulic systems but also fosters trust among users who depend on these components for critical operations.
Moreover, standards play a vital role in facilitating international trade. By adhering to recognized specifications, manufacturers can expand their market reach and reduce barriers to entry in new regions. This is particularly important in industries where compliance with safety and quality standards is non-negotiable.
Key Features of ISO 8434-2 Connectors
ISO 8434-2 connectors are integral components in hydraulic systems, providing reliable and efficient fluid transfer. Their design specifications, material requirements, and performance ratings are critical to their functionality and compatibility in various applications.
Design Specifications
ISO 8434-2 connectors are defined by specific design criteria that ensure they meet the operational demands of hydraulic systems. The most notable feature is the 37° flare angle, which provides a robust sealing surface. This design minimizes the potential for leaks, creating a secure and stable connection even under high-pressure conditions. The flare angle is a crucial aspect that distinguishes these connectors from others, such as those with 45° or 90° flares, which may not offer the same level of sealing effectiveness.
In addition to the flare angle, the connectors utilize unified inch threads as specified by ISO 263. This thread standardization is essential for ensuring compatibility across different manufacturers and systems. The use of unified inch threads means that these connectors can be easily integrated into existing hydraulic setups without requiring modifications to tubes or hoses. This interoperability is particularly beneficial for industries that rely on legacy equipment, as it simplifies maintenance and replacement processes.
37° Flare Angle
The 37° flare angle is specifically designed to create a tight seal when the connector is tightened. This angle allows for optimal surface contact between the male and female components of the connection, enhancing the sealing performance. As a result, the likelihood of leaks is significantly reduced, which is paramount in high-pressure hydraulic systems where even minor leaks can lead to inefficiencies and potential hazards.
Moreover, the 37° flare design accommodates a wide range of fluids, including oils, water, and various hydraulic fluids, making it a versatile choice for diverse applications. This adaptability is a key reason why the 37° flare connector has become a standard in hydraulic engineering.
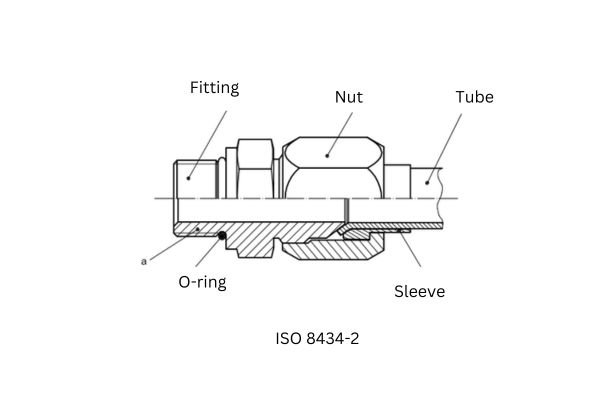
Unified Inch Threads as per ISO 263
The adoption of unified inch threads in ISO 8434-2 connectors is another defining feature. According to ISO 263, these threads are designed to provide consistent and reliable engagement between connectors and their respective fittings. The choice of inch threads rather than metric threads allows for compatibility with a broad spectrum of existing equipment and components, minimizing the need for conversions or replacements.
This thread standardization not only facilitates easy integration but also enhances the durability of the connections. Properly threaded connections are less prone to stripping and wear, which can compromise the integrity of the hydraulic system over time. By utilizing a well-established threading system, ISO 8434-2 connectors contribute to the overall reliability and longevity of hydraulic assemblies.
Material Requirements
Material selection is critical in the manufacturing of ISO 8434-2 connectors, as it directly impacts their performance, durability, and resistance to environmental factors. The standard specifies that connector bodies must be constructed from carbon steel, stainless steel, or copper alloys. Each material offers unique advantages that cater to different application needs.
Carbon Steel: Often chosen for its strength and affordability, carbon steel connectors are ideal for applications where cost is a primary concern. They provide excellent performance in many hydraulic environments but may require protective coatings to prevent corrosion.
Stainless Steel: Known for its resistance to corrosion and high-temperature stability, stainless steel is preferred for applications in harsh environments or where fluids may cause corrosion. The durability of stainless steel connectors ensures long-term reliability, making them suitable for critical systems.
Copper Alloys: Copper alloy connectors offer excellent thermal conductivity and corrosion resistance, making them a good choice for specific applications that require these properties. Their use is typically limited to specialized hydraulic systems.
Pressure and Temperature Ratings
ISO 8434-2 connectors are designed to withstand significant pressure and temperature ranges, ensuring safe and effective operation in demanding conditions. The standard specifies minimum pressure and temperature ratings based on the materials used and the design of the connectors.
These ratings are critical for ensuring that the connectors can handle the operational stresses typical in hydraulic systems. For instance, connectors must be able to endure high-pressure environments without failure, which could lead to leaks or catastrophic failures. Additionally, the ability to function effectively at elevated temperatures is essential for maintaining system performance, particularly in applications where heat generation is common.
Advantages of Using ISO 8434-2 Connectors
ISO 8434-2 connectors offer numerous advantages that make them an ideal choice for hydraulic systems across various industries. Their compatibility with existing applications, cost-effectiveness, and proven performance reliability underscore their value in modern fluid conveyance systems.
Compatibility with Existing Applications
One of the most significant advantages of ISO 8434-2 connectors is their compatibility with existing hydraulic systems. The standardized 37° flare design and the use of unified inch threads, as specified in ISO 263, enable these connectors to seamlessly integrate with pre-existing tubes and hoses. This is particularly beneficial for industries that rely on legacy systems, allowing operators to replace or upgrade components without the need for extensive modifications.
This compatibility not only simplifies maintenance and repairs but also reduces downtime. Businesses can swiftly replace worn-out connectors with ISO 8434-2 compliant options, ensuring that their operations continue smoothly. Furthermore, because these connectors are widely used and recognized internationally, sourcing replacement parts is often easier and more efficient, further enhancing operational reliability.
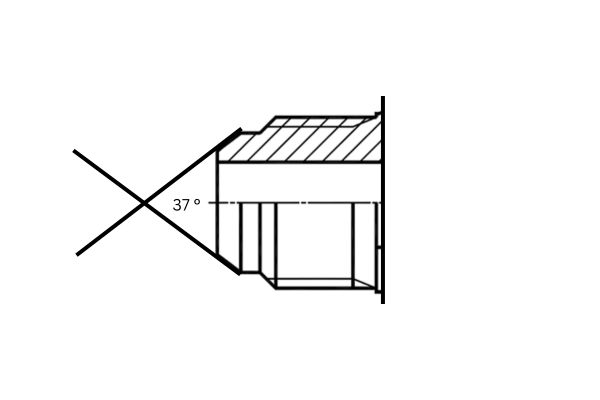
Cost-Effectiveness of Using Established Standards
Utilizing ISO 8434-2 connectors is also a cost-effective choice for manufacturers and maintenance providers. By adhering to established standards, companies can avoid the costs associated with custom or non-standard fittings, which often require specialized equipment or processes for installation. The availability of standardized connectors ensures that parts are readily accessible, reducing both procurement and inventory costs.
Additionally, the long lifespan and durability of ISO 8434-2 connectors contribute to their cost-effectiveness. These connectors are designed to withstand harsh operating conditions, including high pressures and temperatures. The use of materials such as carbon steel, stainless steel, and copper alloys ensures that they can endure the rigors of their environments without significant wear. As a result, companies experience fewer replacements and repairs, translating into lower long-term operational costs.
Testing and Performance Reliability
The performance reliability of ISO 8434-2 connectors is supported by extensive testing and validation. These connectors undergo rigorous assessments to evaluate their sealing capabilities, pressure ratings, and overall performance under varying conditions. This thorough testing ensures that they meet the stringent requirements set forth by the standard, providing confidence to users regarding their reliability in critical applications.
Moreover, the connectors’ design minimizes the risk of leaks, which is crucial in maintaining system efficiency and safety. The robust sealing achieved through the 37° flare angle significantly reduces the likelihood of fluid loss, which can lead to operational inefficiencies and safety hazards. The reliability of these connectors is a key factor in industries such as automotive and aerospace, where even minor failures can have serious consequences.
Installation and Maintenance Tips
Proper installation and maintenance of ISO 8434-2 connectors are essential for ensuring their longevity and optimal performance in hydraulic systems. Adhering to best practices, troubleshooting common issues, and following maintenance recommendations can significantly enhance the reliability of these connectors.
Best Practices for Installing ISO 8434-2 Connectors
Preparation and Cleaning: Before installation, ensure that all surfaces of the connectors and tubing are clean and free of debris. Contaminants can compromise the integrity of the seal and lead to leaks. Use a clean cloth or solvent to wipe down the threads and flared surfaces.
Proper Alignment: Align the connectors carefully to avoid cross-threading. Ensure that the male and female components are matched correctly, and hand-tighten them to establish initial contact before using a wrench.
Torque Specifications: Follow the manufacturer’s torque specifications when tightening the connectors. Over-tightening can damage the threads or flared surfaces while under-tightening may lead to leaks. Using a calibrated torque wrench is recommended to achieve the correct tightness.
Use of Sealants: While ISO 8434-2 connectors are designed for a leak-free connection, in some cases, using a thread sealant may be beneficial. Ensure that the sealant is compatible with the hydraulic fluid being used and does not interfere with the connection.
Common Issues and Troubleshooting
Leaking Connections: If a connection is leaking, first check for proper alignment and tightness. If the connector is not sufficiently tightened, use a torque wrench to adjust it. If leaking persists, inspect the flared surfaces for damage or wear, as these may need to be replaced.
Cross-Threading: Cross-threading can occur if connectors are misaligned during installation. If this happens, disconnect the connector, inspect the threads, and replace any damaged components. Always ensure proper alignment before re-installation.
Fluid Contamination: Contaminants within the hydraulic system can lead to premature connector failure. Regularly check and replace filters, and ensure that all components are clean during installation and maintenance.
Maintenance Recommendations for Longevity and Performance
Regular Inspections: Schedule routine inspections of connectors and associated hydraulic components. Look for signs of wear, corrosion, or leaks. Early detection can prevent costly repairs and system failures.
Tightness Checks: Periodically check the tightness of connectors, especially in high-vibration environments. Re-torque as necessary to maintain a secure connection.
Fluid Quality Monitoring: Ensure that the hydraulic fluid is clean and of the correct type. Contaminated or incorrect fluid can lead to system malfunctions and connector degradation.
Replacement of Worn Components: If any components show signs of wear or damage, replace them immediately. Using worn connectors can compromise system integrity and lead to failure.
Conclusion
As you consider the needs of your hydraulic systems, we encourage you to explore the benefits of ISO 8434-2 connectors. Investing in high-quality, standardized components will not only enhance the performance of your systems but also contribute to the overall safety and efficiency of your operations. Whether you are upgrading existing equipment or designing new systems, ISO 8434-2 connectors should be a key consideration in your selection process. Embrace the advantages of standardized hydraulic connectors and ensure the longevity and reliability of your fluid conveyance solutions.
FAQ
What is ISO 8434-2?
ISO 8434-2 is an international standard that specifies the requirements for 37° flared connectors used in hydraulic systems.
What is the significance of the 37° flare angle?
The 37° flare angle provides a robust sealing surface, minimizing leaks and ensuring a secure connection in high-pressure applications.
Are ISO 8434-2 connectors compatible with existing systems?
Yes, these connectors use unified-inch threads, allowing them to seamlessly integrate with existing tubing and hoses without modifications.
What materials are used for ISO 8434-2 connectors?
Connectors can be made from carbon steel, stainless steel, or copper alloys, ensuring durability and suitability for various fluids.
How should I install ISO 8434-2 connectors?
Clean the surfaces, align the connectors properly, and follow torque specifications to ensure a secure and leak-free installation.
What maintenance is required for these connectors?
Regularly inspect for wear, ensure tightness, and replace any damaged components to maintain performance and longevity.