Hydraulic hoses play a crucial role in fluid power systems, serving as the vital link that carries hydraulic fluid between components, enabling efficient power transmission. Whether in construction equipment, manufacturing machinery, or agricultural tools, hydraulic hoses ensure seamless operation by maintaining consistent fluid flow. Their performance directly impacts the overall efficiency and safety of hydraulic systems, making them indispensable in numerous industries. However, despite their importance, hydraulic hoses are often subject to harsh conditions that can compromise their durability.
Understanding Hydraulic Hose Lifespan
What is Hydraulic Hose Lifespan?
The “hydraulic hose lifespan” refers to the period during which a hydraulic hose can function effectively within a system, delivering consistent fluid flow without compromising safety or performance. The lifespan begins from the point of installation and extends until the hose either fails or its performance degrades to an unacceptable level, necessitating replacement. Several factors influence this lifespan, including hose construction, application type, operating environment, and maintenance practices.
Hydraulic hoses are often exposed to demanding conditions, including high pressure, temperature variations, and harsh chemicals, making it crucial to understand their lifespan. A well-maintained hose can maximize system performance and minimize unexpected downtime. Recognizing the lifespan of a hose helps operators and maintenance teams plan replacements effectively, preventing catastrophic failures that can disrupt operations and incur additional costs.
Expected Lifespan Range for Hydraulic Hoses
Hydraulic hoses are generally designed to withstand years of operation, but their lifespan can vary based on type and usage conditions. Here are some common categories of hydraulic hoses and their expected lifespan:
Standard Rubber Hoses:
Typically designed for moderate operating conditions, these hoses have a lifespan of around 2 to 3 years. They are made of synthetic rubber materials that offer good flexibility and abrasion resistance. However, they may be more vulnerable to chemical degradation and temperature extremes than other types.
Thermoplastic Hoses:
These hoses are known for their resistance to chemical exposure and wear, making them suitable for more demanding applications. Due to their construction, thermoplastic hoses can last up to 4 to 5 years under normal operating conditions. They are often used in environments where chemical compatibility is crucial, as they are less prone to swelling or degradation.
Reinforced Hoses (e.g., Wire-Braided or Spiral-Wound Hoses):
Reinforced hoses are built to withstand higher pressures and more severe conditions, making them ideal for heavy-duty applications. The incorporation of wire braids or spiral layers provides extra strength, allowing these hoses to handle pressure spikes more effectively. Their lifespan can vary significantly, but under optimal conditions, they can last longer than standard rubber hoses.
Specialty Hoses:
Designed for extreme environments, specialty hoses may use materials like PTFE, high-strength thermoplastics, or specialized rubber blends. These hoses are tailored to withstand specific conditions, such as extreme temperatures, high abrasion, or exposure to aggressive chemicals. Their lifespan varies based on the material used and the level of exposure, making regular inspection and testing essential.
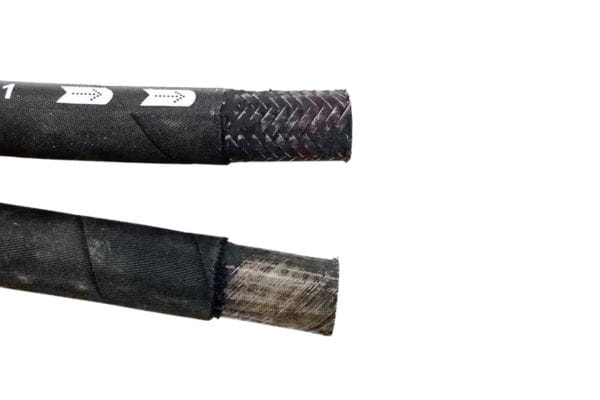
Importance of Monitoring Hose Condition
Proactive monitoring of hydraulic hose condition is key to maximizing its lifespan. Regular inspections allow operators to identify early signs of wear, reducing the risk of sudden failures that can lead to safety hazards, costly repairs, and operational downtime. Monitoring focuses on identifying visible damage and performance issues, including:
Surface Cracks: Cracks on the outer layer of the hose can indicate aging, UV exposure, or material fatigue. If not addressed, these cracks can lead to leaks or even sudden bursts.
Abrasion: Abrasive damage to the hose cover often occurs from contact with machinery, sharp edges, or debris. This can weaken the hose and reduce its pressure capacity.
Leaks: Small leaks around fittings or along the hose body may indicate internal damage, pressure issues, or improper fitting installations.
Bulging: A bulging hose is a clear sign of internal wall failure or delamination, which can lead to rupture under pressure.
Reduced Fluid Flow or Inconsistent Pressure: Changes in performance, such as reduced flow rates or pressure fluctuations, can signal internal hose degradation or blockages, affecting the overall efficiency of the system.
Advanced Monitoring Technologies for Hydraulic Hoses
Advanced technologies can help monitor hose condition more accurately, providing real-time data on hose health. Some of these technologies include:
Pressure Sensors: Measure real-time pressure levels in the hose, allowing operators to identify abnormal pressure fluctuations that could indicate leaks or internal blockages.
Temperature Sensors: Track temperature changes within the hose, providing insights into overheating or exposure to extreme temperatures that can accelerate wear.
Flow Meters: Detect changes in fluid flow, which can signal internal hose damage, blockages, or narrowing.
Wear Sensors: Advanced hoses may be equipped with wear sensors that alert operators to potential damage, offering early warnings and preventing sudden failures.
Key Factors Impacting Hydraulic Hose Lifespan
Hydraulic hoses are subjected to various stresses that can impact their lifespan. This section explores four major factors that significantly affect hose durability: temperature variations, pressure levels, fluid compatibility, and environmental conditions.
Temperature Variations
Temperature plays a critical role in the performance and longevity of hydraulic hoses. Hydraulic systems often operate under extreme temperature conditions, both high and low, which can have adverse effects on the hose material.
Effects of High Temperatures: Excessive heat accelerates the degradation of hose materials, causing them to lose flexibility and strength. High temperatures can lead to the hardening of the hose’s inner tube, making it more susceptible to cracking and leaks. Rubber hoses, in particular, may experience embrittlement, which compromises their structural integrity. Furthermore, extreme heat can cause the hose to soften, expand, and weaken, increasing the risk of bursting under pressure.
Effects of Low Temperatures: Low temperatures can make hoses rigid and less flexible, increasing the likelihood of cracking when bent or twisted. Thermoplastic hoses often handle cold better than standard rubber hoses, but any hose can become brittle in freezing conditions.
Temperature Fluctuations: Rapid and frequent temperature changes can have a compounding effect on hoses, causing them to expand and contract repeatedly. This fluctuation stresses the material, leading to premature fatigue and cracking. For example, hoses operating in environments that alternate between intense heat during operation and freezing conditions during downtime can experience accelerated wear.
To manage temperature-related issues, operators should select hoses specifically rated for the expected temperature range and apply insulation or cooling measures where possible.
Pressure
Hydraulic hoses are designed to handle specific pressure ratings, but how they respond to pressure levels can significantly affect their lifespan.
Role of Constant and Peak Pressure Levels: Hydraulic hoses are exposed to both constant operating pressures and occasional peak pressures. Constant pressure is the regular load the hose endures during normal operations, while peak pressure is the occasional surge that exceeds the usual limit. Hoses that consistently operate near their maximum rated pressure tend to experience faster wear. Exceeding the rated capacity, even briefly, can damage the internal lining, reduce flexibility, and create micro-tears that weaken the hose structure.
Pressure Spikes and Hose Fatigue: Sudden pressure surges, often referred to as hydraulic shocks, can occur due to system malfunctions, rapid valve operations, or sudden load changes. These spikes place immense stress on the hose walls, causing fatigue over time. Frequent pressure fluctuations can also cause the hose to weaken internally, making it more prone to leaks and ruptures.
To minimize pressure-related damage, it is essential to use hoses with appropriate pressure ratings and safety margins. Additionally, installing pressure regulators or accumulators can help manage sudden surges, protecting the hose from extreme stress.
Fluid Compatibility
Hydraulic fluid compatibility is another critical factor that influences hose longevity. The hydraulic fluid not only transmits power but also interacts with the hose material, potentially affecting its performance and lifespan.
Importance of Using Compatible Fluids: Hydraulic hoses are designed to work with specific fluids, and using an incompatible fluid can lead to various issues, including chemical degradation. Hoses are typically constructed with inner tubes made from materials like rubber, thermoplastics, or specialized synthetic compounds, each designed to resist certain chemicals and maintain integrity over time.
Examples of Incompatible Fluid Issues:
Corrosion: Incompatible fluids can cause chemical reactions that corrode the inner lining of the hose. For example, certain fluids may contain aggressive additives that react with rubber compounds, leading to the deterioration of the hose wall.
Swelling and Delamination: Some fluids can cause the inner tube to swell or soften, resulting in delamination (separation of the inner lining from the hose structure). This not only reduces flow efficiency but also increases the risk of leaks and bursts.
Permeation and Fluid Loss: Incompatible fluids may permeate through the hose wall, causing fluid loss and contamination of the surrounding environment. This reduces system efficiency and can pose environmental hazards.
To ensure optimal fluid compatibility, always check the manufacturer’s recommendations for both the hose and the hydraulic fluid. Testing new fluids for compatibility before full-scale implementation can prevent costly hose failures.
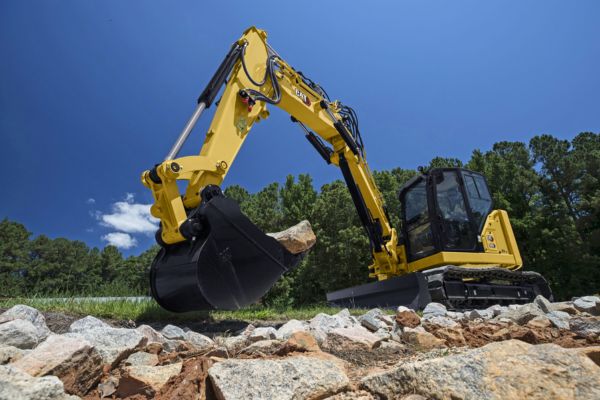
Environmental Conditions
The environment in which hydraulic hoses operate can have a significant impact on their longevity. Factors such as UV exposure, ozone levels, chemical contact, and physical abrasions can degrade hoses over time.
Impact of UV Exposure and Ozone: Hoses exposed to direct sunlight for prolonged periods can suffer from UV damage, leading to surface cracks and weakening of the outer cover. Similarly, ozone exposure can cause cracking and oxidation of the rubber, reducing flexibility and increasing the risk of failure.
Harsh Chemicals: If hoses are used in environments where they are exposed to chemicals such as acids, solvents, or fuels, they may experience chemical degradation. Even when the inner tube is resistant, the outer cover can still be vulnerable to chemical damage, which compromises hose integrity and safety.
Physical Damage from Debris and Abrasion: Hoses that come into contact with sharp edges, moving parts, or debris can suffer from cuts, abrasions, or punctures. Abrasion, in particular, is one of the most common causes of hydraulic hose failure. Even a minor abrasion can weaken the hose wall, increasing the likelihood of leaks or bursts.
To minimize environmental damage, protective measures like hose guards, sleeves, or proper routing can help shield hoses from harsh conditions. Selecting hoses with abrasion-resistant covers or chemical-resistant outer layers is also advisable for demanding environments.
Installation and Maintenance Factors
Proper installation and maintenance are crucial for maximizing the lifespan of hydraulic hoses. Even the best-quality hoses can fail prematurely if not installed correctly or maintained regularly.
Installation Best Practices
The way hydraulic hoses are installed has a significant impact on their lifespan and performance. Proper installation not only enhances durability but also minimizes the risks of leaks, pressure losses, and unexpected failures.
Correct Hose Routing and Avoiding Twists/Kinks:
Correct routing ensures that hoses are free from stress and potential damage during operation. Hoses should be routed in a way that minimizes contact with sharp edges or moving parts that could cause abrasions. Twisting or kinking a hose during installation can lead to internal damage and create weak points, making the hose more susceptible to failure. Twisting can also reduce flow capacity, leading to inefficient operation.
Avoid sharp bends by ensuring hoses follow a smooth, curved path with gentle transitions. Using clamps, brackets, and guides helps maintain hose position and alignment, preventing rubbing and minimizing vibration.
Importance of Proper Bend Radius and Secure Fittings:
Each hydraulic hose has a specified minimum bend radius, which should be maintained to prevent structural damage. Bending a hose beyond its minimum radius can cause internal damage, leading to leaks or bursts. It’s crucial to allow for sufficient length in the hose layout to accommodate movement without exceeding bend limits.
Equally important is securing the fittings properly. Loose or over-tightened fittings can cause leaks, compromise pressure integrity, and lead to potential detachment under pressure. Always use the correct fittings for the hose type and application, and ensure they are tightened to the manufacturer’s specifications using appropriate tools and torque values.
Regular Inspection
Regular inspection is one of the most effective ways to identify potential issues before they lead to failure. Visual inspections should be part of any preventative maintenance plan and can significantly extend the hose’s lifespan by catching signs of wear early.
What to Check for During Visual Inspections:
During inspections, look for the following:
Leaks: Check for any signs of fluid leakage around hose connections, fittings, or along the length of the hose.
Surface Wear: Inspect the outer cover for abrasions, cuts, or cracking. Surface damage can be an indicator of internal wear or external abrasions.
Bulges or Blisters: These indicate internal damage or hose wall separation, which can precede failure.
Corrosion: Look for signs of rust or corrosion around fittings, which can compromise sealing and connection integrity.
Stiffness or Hardening: A hose that becomes unusually stiff or hard is likely degrading internally, especially if exposed to high temperatures or incompatible fluids.
Recommended Inspection Frequency:
The frequency of inspections depends on the operating environment and application. However, it’s generally recommended to inspect hoses:
Daily: Perform a quick visual check for obvious leaks or damages.
Weekly: Conduct a more thorough inspection, including checking for surface wear and proper routing.
Monthly: Include a detailed inspection of all hoses, fittings, and connections. During these checks, verify pressure and temperature levels to ensure they are within safe operating ranges.
Annually: A comprehensive review of the entire hydraulic system, including pressure testing and performance evaluation, should be conducted at least once a year.
Preventative Maintenance Routines
Proactive maintenance is essential for extending the life of hydraulic hoses. By implementing a consistent maintenance routine, operators can prevent unexpected breakdowns and ensure the system operates efficiently.
How Regular Maintenance Can Extend Hose Life:
Regular maintenance helps maintain the hose’s integrity, prevents leaks, and reduces the risk of catastrophic failure. It also improves overall system performance by ensuring that hoses operate within optimal parameters. Consistent maintenance reduces the likelihood of sudden hose failure, which can lead to downtime, safety risks, and higher costs.
Steps to Include in a Maintenance Routine:
Cleaning: Periodically clean the exterior of the hoses to remove debris, dirt, or chemicals that may contribute to abrasion or material degradation.
Lubrication: In some cases, fittings or connectors may require lubrication to maintain proper sealing and prevent wear. Ensure that the lubricant is compatible with both the hose and the hydraulic fluid.
Checking Connections: Tighten any loose connections and replace worn fittings to prevent leaks.
Testing Pressure and Flow: Regularly test the hydraulic system’s pressure and flow to ensure that hoses are handling the demands properly.
Protective Measures: Add protective sleeves or guards in areas with high abrasion risks or exposure to harsh chemicals. This extra protection can help prevent damage to the outer hose cover.
Replacement Timing
Knowing when to replace a hydraulic hose is crucial to avoid unexpected failures and maintain safe operations. Hose replacement is often driven by either visible wear or predefined time intervals.
How to Recognize When a Hose Needs Replacement:
There are several signs that a hydraulic hose may need to be replaced:
Visible Wear and Tear: If a hose shows signs of severe surface wear, cracking, or bulging, it’s time to replace it, even if it is not yet leaking.
Frequent Leaks: Hoses that frequently develop leaks, even after repair, may be nearing the end of their lifespan.
Reduced Performance: If the system’s performance is noticeably reduced, and other factors have been ruled out, hose degradation could be the cause.
Age of the Hose: Even if a hose appears to be in good condition, replacement should be considered if it has exceeded its recommended lifespan, as internal damage may not always be visible.
Benefits of Scheduled Hose Replacements vs. Reactive Replacements:
Proactively replacing hoses at scheduled intervals reduces the risk of unexpected failures, minimizes downtime, and ensures safer operation. Reactive replacements, done only after a failure, can lead to unplanned downtime, safety risks, and higher costs due to potential system damage.
Scheduled replacements also allow maintenance teams to plan replacements during downtime, aligning with maintenance schedules and reducing operational disruptions. By using historical data and inspection results, operators can develop a replacement schedule that aligns with hose performance trends.
Choosing the Right Hydraulic Hose for Longevity
Material Selection
The material of a hydraulic hose is one of the most important factors affecting its durability, as different materials offer varying levels of resistance to pressure, temperature, and chemical exposure.
Different Materials and Their Lifespan Characteristics:
Rubber: Rubber hoses are flexible and suitable for a wide range of applications. They offer good resistance to abrasion and are effective in handling hydraulic fluids. Standard rubber hoses typically have a lifespan of 2-3 years under moderate conditions but can degrade faster in extreme temperatures or when exposed to aggressive chemicals.
Thermoplastic: Thermoplastic hoses offer better resistance to chemicals, making them suitable for applications involving harsh fluids. They are also more resistant to abrasion, which helps in high-friction environments. Thermoplastic hoses can last up to 4-5 years, making them a preferred choice for many industrial settings.
PTFE (Polytetrafluoroethylene): PTFE hoses are excellent for high-temperature and high-pressure environments, as well as applications involving corrosive fluids. They have a longer lifespan and can perform well in demanding conditions, including temperatures up to 500°F (260°C). PTFE hoses are widely used in chemical processing, food-grade applications, and other specialized settings.
Steel-Reinforced: Hoses with steel reinforcement, such as wire-braided or spiral-wound hoses, offer higher pressure capacity and increased durability. They are well-suited for heavy-duty applications, such as construction or mining, where pressure spikes and physical stress are common.
How to Select Materials Based on System Requirements:
The choice of hose material should be guided by system requirements, including:
Operating Pressure: High-pressure systems require hoses with reinforcement, such as steel wire or aramid fibers, to handle pressure without deforming or bursting.
Fluid Compatibility: Use hoses that are compatible with the hydraulic fluid to prevent chemical degradation. For example, thermoplastic or PTFE hoses are better suited for aggressive fluids than standard rubber.
Temperature Range: Consider the temperature of both the fluid and the operating environment. Hoses with heat-resistant materials like PTFE or reinforced rubber are ideal for high-temperature applications.
Abrasion and Wear: In environments with a high risk of wear or contact with rough surfaces, choose hoses with abrasion-resistant covers, such as polyurethane-coated hoses.
Selecting the right material ensures that the hose can withstand the specific demands of the system, ultimately extending its lifespan.
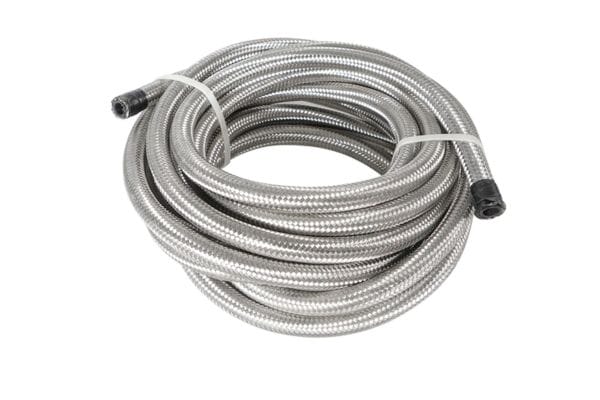
Hose Specifications
Proper hose specifications, such as sizing and pressure ratings, play a vital role in ensuring hydraulic hose longevity and safety.
Importance of Correct Hose Sizing and Pressure Ratings:
Sizing: The internal diameter of the hose determines the flow rate and system efficiency. A hose that is too small can create excessive fluid velocity, increasing friction, pressure drops, and heat generation. Conversely, an oversized hose can result in inefficient fluid transfer. Ensuring correct hose diameter reduces wear and tear, improving system performance and extending hose life.
Pressure Ratings: Each hose has a maximum operating pressure, which includes the working pressure and a safety margin for pressure spikes. It’s essential to select hoses with pressure ratings that match or exceed the system’s maximum pressure requirements to prevent bursts, leaks, and premature wear. Overpressurizing a hose can lead to rapid internal damage, while under-pressurizing can result in inefficient performance.
Matching Hose Specifications to Application Demands:
The specifications of a hydraulic hose must align with the demands of the specific application:
Flow Requirements: Choose a hose with the right diameter to accommodate the system’s flow requirements, reducing pressure loss and preventing overheating.
Pressure Surges: If the system experiences frequent pressure spikes, select a hose with a higher pressure rating to handle these surges without damage.
Flexibility: For systems with moving parts or frequent hose bending, choose hoses designed for high flexibility, such as thermoplastic or spiral-wire reinforced hoses.
Correct sizing and pressure ratings not only enhance hose performance but also reduce maintenance costs and downtime.
Hose End Fittings
The choice of hose end fittings is as crucial as the hose material and specifications, as fittings ensure a secure connection and proper sealing, which are essential for safe and efficient operation.
How the Right Fittings Can Prevent Leaks and Extend Hose Life:
Leak Prevention: Proper fittings prevent leaks by ensuring a tight and secure seal at the hose ends. Leaks can lead to pressure loss, fluid contamination, and environmental hazards. Correct fitting installation minimizes the risk of leaks, which in turn reduces wear on the hose and connected components.
Reduced Stress: The right fittings, combined with the correct installation, help minimize stress at the hose ends. Stress at the connections can lead to cracking, internal damage, and eventual failure. For high-pressure or high-vibration systems, swivel fittings or angled connections may be needed to accommodate hose movement without stressing the connection point.
Enhanced Durability: Quality fittings made from materials compatible with the hydraulic fluid can extend hose life by resisting corrosion and ensuring consistent sealing over time. Stainless steel fittings, for example, are suitable for corrosive environments, while plated steel fittings offer good performance in general hydraulic applications.
Importance of Matching Fittings with Hose Type:
Fittings must be compatible with both the hose material and the hydraulic fluid. For instance:
Rubber Hoses: Use crimped fittings with rubber hoses to ensure a tight seal and prevent leaks.
Thermoplastic Hoses: Choose fittings that accommodate the hose’s flexibility and material characteristics, ensuring a secure connection without damaging the hose structure.
PTFE Hoses: Use fittings specifically designed for PTFE hoses, as these fittings are often flared to prevent leakage and handle higher temperatures and pressures.
Proactive Strategies to Maximize Hydraulic Hose Lifespan
Implementing proactive strategies can significantly extend the lifespan of hydraulic hoses, minimize maintenance costs, and enhance system performance.
Using Protective Coverings
Protective coverings act as a barrier between hydraulic hoses and external elements, preventing physical damage and enhancing durability.
Abrasion-Resistant Sleeves:
Abrasion is one of the leading causes of hydraulic hose failure. Hoses that frequently rub against other components or surfaces are prone to wear. Installing abrasion-resistant sleeves or spiral wraps around hoses helps reduce surface friction and prevent damage, especially in high-vibration environments. These sleeves can be made of materials like nylon or polyurethane, which provide a durable protective layer without compromising hose flexibility.
Heat Shields:
In applications with high temperatures or proximity to heat sources, heat shields or insulation wraps can protect hoses from direct heat exposure. Excessive heat can cause hoses to degrade rapidly, leading to cracks, leaks, or bursts. Insulating hoses in high-temperature zones helps maintain the integrity of the hose material and prolong its lifespan.
Chemical-Resistant Coatings:
For hoses exposed to corrosive chemicals, applying a chemical-resistant coating can prevent damage from fluid splashes or spills. This protective layer shields the outer cover of the hose from aggressive chemicals that can cause degradation or swelling, thereby extending hose durability.
Proper Storage and Handling
Proper storage and handling of hydraulic hoses are essential to prevent premature aging or damage before they are installed.
Storage Conditions:
Dry and Cool Environment: Store hoses in a dry, cool area to prevent degradation due to moisture, excessive heat, or UV exposure. High humidity can lead to mold growth, while direct sunlight can cause rubber hoses to dry out, crack, and lose flexibility.
Avoid Sharp Bends: When storing hoses, avoid bending them sharply, as this can damage the inner lining and create weak points. Use hose reels or racks to maintain a natural curve, preventing kinks that could compromise flow capacity.
Seal Hose Ends: Always cap hose ends during storage to prevent debris or moisture from entering the hose. Contamination can lead to blockages or corrosion inside the hose, reducing its lifespan once installed.
Handling Practices:
Avoid Dragging: Never drag hoses across rough surfaces, as this can cause abrasion, cuts, or punctures. Lift and carry hoses properly to prevent surface damage.
Use Correct Tools: When installing or disconnecting hoses, use the appropriate tools to avoid damaging the fittings or connections. Tightening hoses improperly can lead to leaks while overtightening can cause stress at the hose ends.
Monitoring System Performance to Detect Hose Issues Early
Effective monitoring of system performance is crucial to identifying potential hose issues before they lead to failure. By keeping track of system indicators, operators can detect and address hose problems early, preventing unplanned downtime and costly repairs.
Pressure Monitoring:
Installing pressure sensors in the hydraulic system allows operators to monitor pressure levels in real time. Sudden pressure drops may indicate a leak, while pressure spikes can suggest blockages or hose weakening. Tracking pressure trends helps identify performance deviations, enabling timely inspections and repairs.
Temperature Monitoring:
Excessive heat can cause hoses to degrade faster, leading to cracks or bursts. Temperature sensors help detect abnormal heat levels within the hose, allowing operators to take corrective actions, such as adjusting fluid flow or improving cooling measures.
Flow Rate Monitoring:
Flow meters are effective in detecting changes in fluid flow, which can indicate internal hose damage or blockages. Reduced flow rates can be an early warning of hose degradation, kinks, or delamination, while inconsistent flow can point to internal obstructions. By regularly reviewing flow rate data, operators can identify potential issues and schedule preventative maintenance.
Visual Inspections:
While advanced sensors provide real-time data, regular visual inspections remain one of the simplest and most effective monitoring strategies. Inspect hoses for surface wear, leaks, cracks, bulging, or corrosion. Visual checks, combined with sensor data, offer a comprehensive overview of hose health, enabling more accurate maintenance decisions.
Implementing a Predictive Maintenance Plan
Integrating proactive strategies into a predictive maintenance plan helps maintain optimal hydraulic hose performance and extends hose lifespan.
Data Analysis for Maintenance Scheduling:
Use data from sensors and inspections to establish maintenance schedules based on actual hose conditions rather than fixed intervals. This predictive approach ensures that hoses are maintained or replaced only when necessary, maximizing their use while preventing unexpected failures.
Record Keeping:
Maintain detailed records of hose inspections, repairs, and replacements. By tracking hose performance data over time, maintenance teams can identify patterns of wear or degradation, allowing for better planning and selection of hoses for specific applications.
Training Operators:
Train operators and maintenance personnel on the importance of proactive strategies and how to recognize early signs of hose damage. Empowering staff with knowledge about hose care and maintenance helps ensure that issues are addressed promptly and correctly, preventing further damage.
Conclusion
To ensure longer-lasting hydraulic systems, it’s crucial to apply the best practices discussed, such as using abrasion-resistant coverings, storing hoses correctly, selecting suitable materials, and performing regular inspections. Proactive maintenance not only extends hose life but also improves system performance and operational efficiency. If you found this post helpful, consider sharing it with others who may benefit from these insights.
FAQ
What is the typical lifespan of a hydraulic hose?
The lifespan varies based on hose type and conditions but generally ranges from 1 to 5 years.
How can I extend the life of a hydraulic hose?
Regular inspections, proper installation, using protective covers, and proactive maintenance can extend hose life.
What are the signs that a hydraulic hose needs replacement?
Look for visible wear, leaks, bulging, cracking, and reduced system performance.
Why is hose material selection important?
The right material ensures compatibility with operating pressure, temperature, and fluids, enhancing hose durability.
What role do fittings play in hose lifespan?
Proper fittings prevent leaks, reduce stress at hose ends, and ensure a secure connection, contributing to longer hose life.
How often should I inspect hydraulic hoses?
Hoses should be inspected daily for leaks, weekly for wear, and monthly for a comprehensive review.