Hydraulic hoses are essential components in various industrial systems, facilitating the transfer of hydraulic fluid under pressure to power machinery, tools, and equipment. When working correctly, these hoses ensure efficient operation, smooth production, and minimal downtime. However, when a hydraulic hose ruptures, the results can be catastrophic, impacting safety, operational efficiency, and finances. The release of pressurized fluid can cause severe injuries, prolonged downtime, and costly repairs, not to mention potential environmental damage due to fluid leaks.
Understanding Hydraulic Hose Ruptures
What is a Hydraulic Hose Rupture?
A hydraulic hose rupture is the sudden failure or breaking of a hose, leading to an uncontrolled release of pressurized hydraulic fluid. This can be a sudden burst, a small leak, or even a pinhole that allows fluid to escape under pressure. These ruptures compromise the performance and safety of hydraulic systems, often resulting in hazardous situations, equipment damage, and productivity loss.
How Do Ruptures Occur in Hydraulic Systems?
Hydraulic systems operate under immense pressure, often exceeding thousands of pounds per square inch (psi). Over time, the hoses that channel this pressurized fluid can weaken due to constant stress, exposure to harsh chemicals, temperature variations, and mechanical wear. When a hose’s material can no longer withstand these stresses, it can break, tear, or develop small holes—leading to ruptures. In some cases, ruptures can occur instantaneously, while in others, they develop gradually, making early detection challenging.
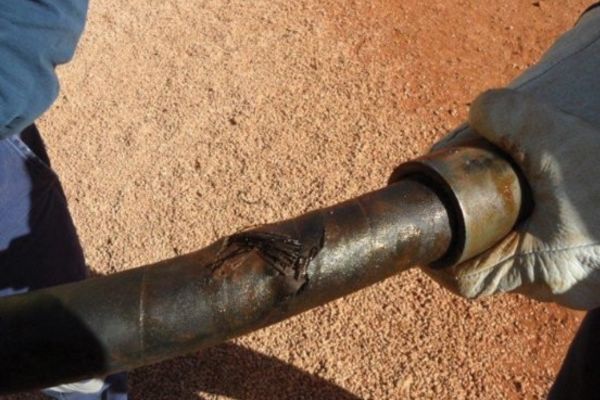
Types of Ruptures
Hydraulic hose ruptures can manifest in several ways:
Abrasions:
Hoses may rub against other components or surfaces, causing the outer layers to wear down. Over time, this weakens the hose’s structure, making it prone to failure. Abrasions can lead to leaks or full-blown bursts.
Leaks:
Leaks are often caused by wear or damage to the hose material, resulting in fluid seeping from small holes or cracks. Leaks may start small but can escalate into more severe ruptures if not addressed promptly.
Bursts:
A burst is a sudden and catastrophic failure of the hose, releasing a large volume of hydraulic fluid instantly. Bursts usually occur due to excessive pressure or a severely weakened hose structure.
Pinholes:
Pinholes are small, often barely visible holes that develop in the hose due to gradual material degradation or internal pressure exceeding the hose’s capacity. Though small, pinholes can still release pressurized fluid at dangerous speeds.
Causes of Ruptures
Several factors contribute to hydraulic hose ruptures, including:
Excessive Pressure:
Hydraulic hoses are designed to handle specific pressure ranges. If the system’s pressure exceeds the hose’s rating, it can lead to rapid deterioration and failure.
Improper Installation:
Incorrect hose routing, bending, or twisting can create unnecessary stress points, increasing the likelihood of ruptures. Using the wrong fittings or connections can also compromise the hose’s integrity.
Chemical Degradation:
Exposure to harsh chemicals, such as certain hydraulic fluids or external contaminants, can weaken the hose material over time, making it more susceptible to leaks or bursts.
Age and Wear:
Hydraulic hoses have a finite lifespan. As they age, they become more brittle, and their internal reinforcements can degrade, leading to potential failure.
Consequences of Hose Ruptures
Safety Hazards:
Pressurized fluid releases can result in serious injuries, such as burns, lacerations, or even death. High-pressure fluid jets can penetrate the skin, causing severe internal damage.
Downtime and Financial Impact:
Ruptures often require immediate system shutdowns, causing unplanned downtime and lost productivity. The costs of replacing damaged hoses, cleaning up spills, and repairing equipment can add up quickly.
Environmental Risks:
Ruptured hoses can release hydraulic fluid into the environment, contaminating soil and water sources. Cleanup and regulatory compliance costs can be significant, especially if the spill is large or occurs in sensitive areas.
Best Practices for Preventing Hose Ruptures
Proper Installation
Correct installation is the first line of defense against hose ruptures. Here are some critical guidelines:
Correct Hose Routing:
Hoses should be routed in a manner that minimizes stress and strain. Avoid sharp bends, as they can weaken the hose structure and cause premature failure. Use large, sweeping curves that match the hose’s minimum bend radius specifications to maintain proper flow and pressure.
Securing the Hose:
Use clamps, brackets, and other securing mechanisms to hold hoses in place. This helps prevent unnecessary movement, which can cause rubbing, vibration, and excessive stress on fittings. Ensure that hoses are not stretched or pulled tightly, as this can lead to tension-induced ruptures.
Avoiding Sharp Bends:
Sharp bends and kinks restrict fluid flow and increase pressure on specific hose sections, accelerating wear and tear. If tight bends are unavoidable, use bent fittings or 90-degree elbows to reduce stress. In confined spaces, consider using flexible hoses that are specifically designed to accommodate tighter bends.
Proper installation not only enhances hose longevity but also optimizes hydraulic system efficiency by maintaining consistent fluid flow and pressure.
Regular Maintenance
Proactive maintenance is crucial for preventing hose ruptures and ensuring reliable operation. Key maintenance practices include:
Scheduled Inspections:
Regular inspections help detect early warning signs such as cracks, abrasions, leaks, and bulging. Create a routine inspection schedule based on the manufacturer’s recommendations and the operating environment. Inspections should include a thorough check of both hoses and fittings.
Replacing Hoses Before Visible Damage:
Hoses should be replaced based on age and usage, not just visible wear. Waiting until a hose shows signs of failure can lead to unexpected downtime and safety risks. Follow the manufacturer’s suggested replacement intervals, even if a hose appears to be in good condition.
Cleaning Hoses:
Hydraulic fluid residues, dirt, and other contaminants can degrade the hose material over time. Regular cleaning helps prevent chemical degradation and ensures smooth fluid flow. Use appropriate cleaning agents that are compatible with both the hose material and hydraulic fluid.
Regular maintenance not only extends the life of hoses but also helps maintain overall system efficiency, preventing issues like fluid contamination and pressure imbalances.
Pressure Regulation
Maintaining proper pressure levels in the hydraulic system is vital for preventing hose failure:
Pressure Relief Valves:
Pressure relief valves help regulate system pressure by allowing excess pressure to escape. Install these valves at critical points in the hydraulic circuit to prevent sudden spikes that could damage hoses. Regularly test the relief valves to ensure they are functioning correctly.
Regular Pressure Checks:
Monitoring system pressure with gauges or sensors can help detect abnormal fluctuations that may indicate internal hose problems or potential failure points. Regular pressure checks also ensure that the system is operating within the hose’s rated pressure capacity.
Pressure Accumulators:
Pressure accumulators can absorb sudden surges and fluctuations, stabilizing the hydraulic system and reducing stress on hoses. Using accumulators where pressure spikes are common can be a highly effective preventive measure.
Pressure regulation measures not only enhance hose safety but also improve the efficiency and reliability of the entire hydraulic system.
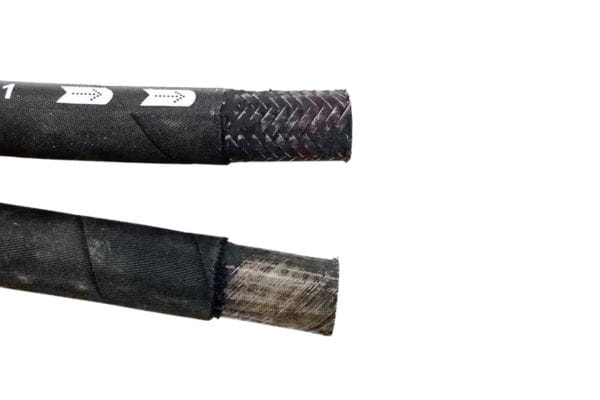
Proper Hose Selection
Choosing the right hose is essential for minimizing the risk of rupture. Consider the following factors when selecting a hose:
Material Compatibility:
Select hose materials that are compatible with the hydraulic fluid used. For instance, certain fluids may degrade rubber hoses more quickly, necessitating the use of reinforced or synthetic materials. Consider environmental factors, such as temperature extremes, chemical exposure, and UV radiation, which can affect hose durability.
Temperature and Pressure Ratings:
Ensure that the hose’s temperature and pressure ratings match the system’s operating conditions. Using hoses rated below the actual pressure or temperature can lead to premature failure. When in doubt, choose hoses with a safety margin above the anticipated operating conditions.
Fluid Compatibility:
Verify that the hose’s inner lining is compatible with the hydraulic fluid. Some fluids may cause swelling, weakening, or chemical degradation of the hose material, increasing the likelihood of leaks or bursts.
Proper hose selection reduces the likelihood of premature failures and ensures that the hose can withstand the demands of the hydraulic system.
Using Protective Accessories
Protective accessories enhance hose durability by preventing common damage like abrasion and punctures:
Hose Sleeves:
Hose sleeves are flexible protective coverings that shield hoses from abrasions, cuts, and chemical exposure. They are especially useful in applications where hoses may rub against surfaces or other hoses. Sleeves can be made from various materials, including nylon, polyester, and steel mesh.
Hose Guards:
Hose guards, often spiral or spring-shaped, provide additional protection in areas prone to physical damage. They are effective in preventing kinks and protecting against impact damage, making them ideal for heavy-duty applications.
Protective Covers:
In environments with high temperatures, protective covers can insulate hoses from heat sources. Heat-resistant covers are particularly useful near engines, furnaces, or other heat-generating equipment.
Incorporating protective accessories into the hydraulic system not only prolongs hose life but also enhances operator safety by reducing the likelihood of sudden failures.
Emergency Response and Mitigation
Despite best efforts, hydraulic hose ruptures can still occur. Having a clear emergency response plan is essential to mitigate the risks, minimize injuries, and prevent further damage.
Immediate Steps During a Rupture
The first priority during a hydraulic hose rupture is to ensure the safety of personnel and equipment. Follow these steps:
Shut Down the Hydraulic System Safely:
As soon as a rupture is detected, immediately stop all operations. Use the emergency stop button to halt the hydraulic system, if available. This minimizes the release of pressurized fluid and prevents further damage to the system or surrounding equipment.
If manual shutdown is necessary, locate the main power source and carefully turn it off. Be aware that high-pressure fluid may still be present in the system, so take precautions to avoid contact with the hose or leaked fluid.
Containment Measures to Prevent Further Hazards:
Quickly establish a safety perimeter around the ruptured hose to prevent personnel from coming into contact with escaping fluid, which can cause injuries such as burns, skin absorption, or injection injuries.
Use spill containment kits, including absorbent mats, barriers, and drain covers, to prevent hydraulic fluid from spreading and contaminating other areas or entering drainage systems.
If the rupture involves flammable fluid, ensure that ignition sources (sparks, open flames) are eliminated from the area to prevent fires.
First Aid and Safety Measures
Hydraulic fluid exposure can cause various injuries, including chemical burns, skin irritation, and injection injuries. Quick first aid response is vital:
Basic First Aid for Fluid Injection:
Fluid injection injuries are particularly dangerous as high-pressure fluid can penetrate the skin and enter the bloodstream. If fluid injection occurs, it is a medical emergency—call for immediate medical assistance.
Do not attempt to treat the injury on-site. Keep the affected area still and elevated, if possible, and cover it with a clean cloth or bandage until medical help arrives.
First Aid for Chemical Burns:
If hydraulic fluid comes into contact with the skin, remove any contaminated clothing and wash the affected area with water and mild soap for at least 15 minutes.
For eye exposure, use an eyewash station to flush the eyes with water continuously for 15 minutes, keeping the eyelids open. Seek medical attention immediately after initial first aid.
Personal Protective Equipment (PPE):
Ensure that responders wear appropriate PPE, such as gloves, goggles, and long-sleeved clothing, to prevent further exposure to hydraulic fluid. Supply clean water and first aid kits near hydraulic equipment to facilitate rapid response.
Cleanup and Environmental Protection
Spilled hydraulic fluid poses significant environmental risks, including soil and water contamination. Follow these cleanup steps:
Managing Hydraulic Fluid Spills:
Use absorbent materials, such as spill pads, granules, or sand, to contain and soak up the fluid. Start from the outer edge of the spill and work inward to prevent further spread.
For large spills, consider using berms or barriers to create a containment zone. This limits the spill to a designated area, reducing the risk of contamination.
Ensuring Proper Disposal:
Collect the used absorbent materials and place them in designated hazardous waste containers. Hydraulic fluid-soaked materials must be disposed of according to local environmental regulations.
If the spill reaches drainage systems or water sources, contact the appropriate environmental protection agency to handle containment and cleanup. Never attempt to flush hydraulic fluid spills into regular drainage systems, as this can cause severe environmental damage.
Proper cleanup and disposal not only protect the environment but also comply with safety regulations, preventing potential fines and legal consequences.
Reporting and Documentation
Effective incident reporting and documentation are essential for maintaining safety standards, identifying failure patterns, and preventing future incidents:
Importance of Incident Reports:
After the initial response, a detailed incident report should be completed as soon as possible. Include information about the date, time, location, and circumstances of the rupture, as well as any injuries, cleanup efforts, and equipment damage.
The report should also detail the immediate response actions taken, including system shutdown, containment measures, and first aid provided. Include the names of individuals involved and any witnesses.
Maintaining Accurate Records for Safety Audits:
Keep all incident reports on file for safety audits and regulatory compliance. Analyzing these reports helps identify common causes of ruptures, equipment vulnerabilities, and potential procedural improvements.
Use incident records to develop and update safety protocols, training programs, and maintenance schedules, ensuring continuous safety improvement.
Advanced Prevention Techniques
As hydraulic systems become more complex, the need for advanced prevention techniques grows. While basic maintenance and safety practices are essential, modern technology and proactive management can significantly enhance the effectiveness of prevention strategies, reducing the likelihood of unexpected hose ruptures.
Predictive Maintenance Using Technology
Predictive maintenance leverages advanced technology to monitor the condition of hydraulic hoses in real time. This approach allows operators to identify potential issues before they escalate into failures.
Utilizing Sensors and IoT Devices:
Sensors and Internet of Things (IoT) devices can be integrated into hydraulic systems to continuously track hose performance parameters, such as pressure, temperature, and vibration levels.
Pressure sensors can detect abnormal fluctuations that might indicate internal hose wear or blockages. Temperature sensors help ensure that hoses are not operating beyond their thermal capacity, which could lead to material degradation.
Vibration sensors can identify unusual movements that could signify a loose connection or external abrasion.
IoT-enabled devices transmit data to a central monitoring system, allowing operators to track hose health remotely. Real-time alerts can be set up to notify maintenance teams of critical conditions, enabling quick intervention and reducing the risk of sudden ruptures.
Benefits of Predictive Maintenance:
By identifying issues early, predictive maintenance reduces downtime, lowers repair costs, and extends the lifespan of hydraulic hoses. It also minimizes the risk of injury and environmental damage, making it a safer and more efficient approach.
Training for Employees
Training is a crucial aspect of preventing hose ruptures, as even the best equipment can fail if not handled properly. Educating operators and technicians on correct procedures ensures a safer working environment and more reliable hydraulic operations.
Educating Operators and Technicians:
Operators and technicians should receive comprehensive training on proper hose installation, routing, and maintenance procedures. This includes understanding the minimum bend radius, correct connection techniques, and the importance of regular visual inspections.
Training should also cover emergency response protocols for hose ruptures, ensuring that staff can quickly and effectively manage unexpected incidents. This includes safely shutting down the system, applying containment measures, and administering first aid if necessary.
Hands-on Training and Simulations:
In addition to classroom instruction, hands-on training is vital for developing practical skills. Technicians should practice inspecting hoses, detecting early warning signs, and replacing worn components under supervision.
Simulations of potential hose failure scenarios can also be useful, allowing staff to rehearse emergency responses in a controlled environment. This not only builds confidence but also ensures faster, safer reactions in real-life situations.
Continuous Learning:
Training should be an ongoing process, with periodic refresher courses to keep employees updated on new technologies, safety regulations, and best practices. As new equipment and techniques are introduced, operators should be trained accordingly.
Implementing a Hose Management System
A comprehensive hose management system is one of the most effective ways to ensure proactive maintenance and prevent failures. This system involves a structured approach to hose selection, tracking, and replacement.
Developing a Proactive Hose Replacement and Monitoring Program:
A proactive hose replacement program identifies hoses that are approaching the end of their expected lifespan and schedules replacements before visible damage occurs. This minimizes the risk of unplanned downtime and reduces the likelihood of safety incidents.
The program should include detailed tracking of each hose’s installation date, usage conditions, and maintenance history. Use barcodes or RFID tags to track individual hoses, making it easier to monitor their condition and schedule timely replacements.
Routine Inspections and Documentation:
As part of the management system, conduct routine inspections to assess hose condition and performance. Document all findings, including any signs of wear, repairs, and replacements. Consistent documentation helps identify trends and recurring issues, enabling more targeted preventive measures.
Data Analysis for Continuous Improvement:
Analyze the data collected from hose tracking and predictive maintenance systems to identify patterns and improve overall performance. For example, if certain hoses consistently show signs of abrasion, consider using protective sleeves or re-routing to reduce contact with abrasive surfaces.
Use insights from the hose management system to refine maintenance schedules, improve training programs, and optimize hose selection based on real-world performance data.
Conclusion
Implementing these best practices not only reduces the risk of costly failures but also ensures a safer working environment, minimizing downtime and environmental impact. Proactive maintenance is the cornerstone of hydraulic safety—by addressing potential issues before they escalate, you can protect both personnel and equipment.
FAQ
What causes hydraulic hose ruptures?
Common causes include excessive pressure, improper installation, chemical degradation, and hose aging.
How can I identify early signs of hose failure?
Look for cracks, abrasions, leaks, bulging, unusual sounds (hissing or whistling), and pressure fluctuations.
How often should hydraulic hoses be inspected?
Hoses should be visually inspected before each use, with more thorough inspections scheduled based on the manufacturer’s recommendations and operating conditions.
What should I do immediately after a hydraulic hose rupture?
Shut down the system, establish a safety perimeter, apply containment measures, and provide first aid if needed.
How can predictive maintenance help prevent ruptures?
Predictive maintenance uses sensors and IoT devices to monitor hose conditions in real-time, detecting early signs of wear or pressure fluctuations.
When should hydraulic hoses be replaced?
Replace hoses based on manufacturer guidelines, before visible damage appears, or whenever they show signs of wear, cracks, or leaks.