When hydraulic hoses fail, the results can be catastrophic, impacting both safety and productivity. Hose failures can lead to injuries, equipment damage, costly downtime, and environmental hazards, highlighting the importance of understanding their causes and implementing effective safety measures.
Understanding Hydraulic Hose Failures
What Constitutes a Hose Failure?
A hydraulic hose failure occurs when a hose is no longer able to perform its intended function—safely and effectively transferring pressurized fluid within a hydraulic system. Failures can range from minor leaks to complete ruptures, each with varying levels of risk and consequences.
Minor Leaks:
Minor leaks are often due to small cracks or pinholes in the hose. While not immediately catastrophic, they compromise system efficiency, increase the risk of fluid contamination, and can eventually lead to more significant failures if left unaddressed.
Major Ruptures:
Major ruptures involve a sudden, large-scale release of pressurized fluid, often accompanied by loud noise and rapid fluid loss. These can cause serious safety risks, including potential injuries, extensive equipment damage, and environmental hazards.
Understanding the differences between minor leaks and major ruptures is crucial for identifying potential failure points and taking appropriate preventive measures.
Analyzing Hydraulic Hose Failures
Types of Hose Failures
Hydraulic hose failures can present themselves in various forms, each with its distinct characteristics:
Abrasions:
Abrasions occur when hoses rub against surfaces, equipment, or other hoses. This results in the outer layer wearing down, eventually exposing the inner reinforcement, which weakens the hose structure and leads to failure.
Pinhole Leaks:
Pinhole leaks are tiny holes that develop in the hose due to gradual internal or external wear. While they might seem insignificant, pinhole leaks can release pressurized fluid at high speeds, posing safety hazards and increasing maintenance costs.
Cracks:
Cracks in the hose material are usually caused by exposure to extreme temperatures, chemical incompatibility, or material fatigue over time. Cracks can develop internally or externally, leading to fluid seepage or sudden ruptures.
Fitting Blow-Offs:
Fitting blow-offs occur when hoses detach from their fittings due to improper installation or excessive pressure. This often results in immediate fluid release and can cause significant damage to the system.
Complete Bursts:
Complete bursts are catastrophic failures where the hose ruptures entirely, causing a large and sudden fluid discharge. These failures typically happen under conditions of extreme pressure or when the hose material has significantly degraded.
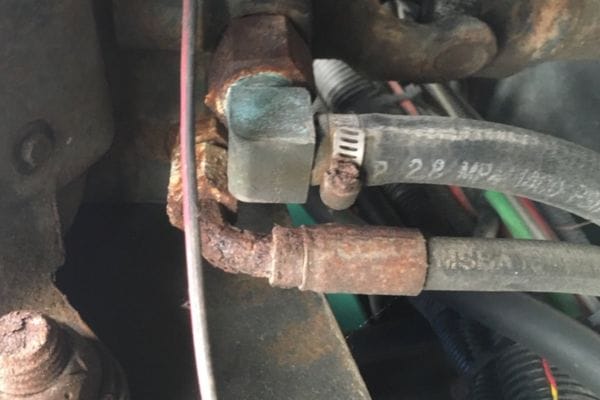
Root Causes of Hydraulic Hose Failures
Identifying the root causes of hydraulic hose failures is critical for implementing effective preventive measures. Hydraulic hoses face a variety of stresses and environmental factors that can weaken their integrity over time. These causes are categorized as follows:
Mechanical Stress
- Pressure Spikes: Caused by sudden valve closures, blocked lines, or unexpected loads.
- Pulsation: Repetitive pressure fluctuations lead to fatigue in hose material.
- Excessive Bending: Leads to delamination or kinking if beyond minimum bend radius.
Thermal Stress
- High-Temperature Exposure: Causes softening, leakage, or rupture.
- Low-Temperature Exposure: Makes hoses brittle and crack-prone.
- Temperature Fluctuations: Expansion/contraction stresses internal layers.
Chemical Exposure
- Incompatible Hydraulic Fluids: Degrade inner lining, causing swelling, leaks, or bursts.
- External Chemical Contact: Cleaning agents, solvents, or industrial chemicals degrade outer layers.
Improper Installation
- Incorrect Routing: Causes sharp bends, abrasion, or fitting misalignment.
- Twisting During Installation: Damages reinforcement layers.
- Unsecured Hoses: Movement causes wear or disconnection.
Consequences of Failures
Hydraulic hose failures can have severe consequences, affecting both safety and operations:
Safety Hazards:
The sudden release of pressurized fluid can cause serious injuries, such as burns or fluid injection injuries. These injuries can be life-threatening and require immediate medical attention.
Environmental Contamination:
Leaked hydraulic fluid can contaminate soil, water sources, and the surrounding environment. Cleaning up spills is not only costly but also subject to strict regulatory compliance, which can lead to fines and reputational damage.
Downtime:
When a hose fails, the hydraulic system must often be shut down for repairs. Unplanned downtime disrupts production, causing delays and reduced efficiency.
Financial Loss:
Beyond repair costs, failures can lead to loss of productivity, regulatory penalties, and increased maintenance expenses. Replacing damaged components and cleaning up spills add to the overall financial impact.
Early Detection of Hose Failures
Visual Inspection Techniques
Visual inspection is the most straightforward method for detecting early signs of hose wear. It helps identify physical damage that can indicate impending failure:
Cracks:
Cracks often appear on the outer surface of the hose and are commonly caused by excessive bending, chemical exposure, or age-related degradation. Cracks may start as small lines but can spread quickly, leading to leaks or bursts.
During inspections, check for fine lines, especially at bends and connections, where pressure and stress are usually highest.
Bulges:
Bulges indicate that the hose’s internal reinforcement has weakened, allowing the hose to expand under pressure. This is a critical warning sign of imminent failure, as bulging is usually caused by internal material separation or pressure surges beyond the hose’s capacity.
Inspect hoses along their length, paying close attention to any areas that appear swollen or distorted, as these require immediate replacement.
Abrasions:
Abrasions occur when hoses rub against surfaces, equipment, or other hoses. They can range from minor scuff marks to severe wear that exposes the internal reinforcement.
To prevent abrasions, use protective sleeves or re-route hoses to avoid contact with rough or sharp surfaces. During inspections, ensure that hoses remain free from heavy wear, as worn sections are more prone to leaks and ruptures.
Leaks:
Leaks can start as slow seepage or as droplets of fluid appearing at hose connections or damaged areas. Even small leaks indicate a compromised hose, signaling potential for more significant failures.
Check for wet spots, oil stains, or puddles around hoses and fittings. Use absorbent pads to test for slow seepage that may not be immediately visible.
Worn Fittings:
Fittings can loosen, wear out, or crack over time, leading to leaks or fitting blow-offs. During visual inspections, ensure that fittings are securely attached, free of corrosion, and aligned properly.
If fittings show signs of wear, tighten or replace them to prevent fluid leakage and maintain system integrity.
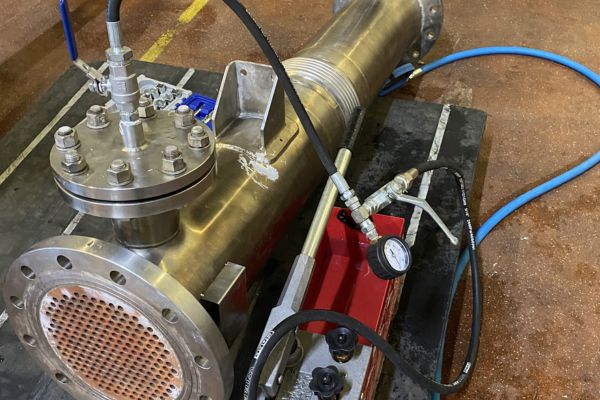
Auditory Signs of Imminent Failures
In addition to visual inspections, listening for unusual sounds can provide valuable insights into hose condition:
Hissing:
A hissing sound indicates pressurized fluid escaping from a small hole, crack, or loose fitting. Hissing can be a sign of pinhole leaks that may not be easily visible but pose a significant safety risk due to the high-pressure fluid release.
If hissing is detected, inspect the system immediately to identify and repair the source of the leak.
Whistling:
Whistling sounds are caused by fluid being forced through a restricted or damaged hose section. This often signals an internal blockage, delamination, or pressure buildup, which can lead to sudden failure.
Whistling should prompt immediate inspection and possible hose replacement to prevent further damage.
Using auditory monitoring as part of routine checks can help identify hidden leaks and failures that are not immediately visible.
Pressure and Temperature Monitoring
Real-time monitoring of pressure and temperature levels is an advanced method for detecting hose weakening:
Using Gauges:
Pressure gauges placed at critical points in the hydraulic system can help detect fluctuations that may indicate hose wear. Spikes or drops in pressure can signal blockages, leaks, or internal delamination within hoses.
Regularly check and calibrate gauges to ensure accurate readings, and investigate any abnormal pressure readings promptly.
Temperature Sensors:
Temperature sensors help monitor fluid and external temperatures, identifying cases where the hose is exposed to temperatures beyond its rated limits. High temperatures can cause softening or swelling of the hose material, while low temperatures can make the hose brittle and prone to cracking.
Use temperature sensors to monitor conditions in real time, and set up alerts for temperatures approaching or exceeding hose ratings.
Digital Monitoring Systems:
Advanced hydraulic systems may use digital monitoring systems connected to IoT devices, allowing operators to track pressure, temperature, and flow rates remotely. These systems provide real-time alerts when readings deviate from normal parameters, helping detect potential failures before they occur.
By integrating pressure and temperature monitoring into the maintenance routine, operators can catch early signs of hose degradation and take corrective action quickly.
Maintenance Records
Maintaining detailed records of hose usage and performance is critical for predicting potential failures:
Tracking Hose Lifespan:
Every hydraulic hose has a recommended lifespan based on the manufacturer’s specifications and operating conditions. Tracking installation dates and expected replacement intervals helps prevent unexpected failures due to age.
Keep a log of each hose’s installation date, operating hours, and maintenance history to ensure timely replacements.
Recording Operating Conditions:
Documenting the conditions under which hoses operate—including pressure, temperature, and fluid type—provides insights into how different factors impact hose longevity. This data can help identify patterns and potential failure points, leading to more informed maintenance decisions.
Analyzing Failure History:
If a hose fails, record the failure details, including the type of failure, probable cause, and affected areas. Analyzing this information helps identify recurring issues and improve maintenance practices.
Safety Solutions for Preventing Hose Failures
Implementing effective safety measures is essential to prevent hydraulic hose failures. These solutions focus on proper hose selection, installation, maintenance, pressure management, and protective accessories.
Proper Hose Selection
Choosing the right hydraulic hose is the foundation of a safe and reliable system. The following factors should be considered:
Application-Specific Requirements:
Hoses should be selected based on the specific requirements of the hydraulic application. Consider factors like pressure, temperature, and fluid compatibility to ensure optimal performance.
For example, high-pressure applications require hoses with a higher burst rating, while high-temperature operations demand hoses with heat-resistant materials.
Use the STAMPED criteria—Size, Temperature, Application, Material, Pressure, Ends, and Delivery—as a guide for selecting the appropriate hose type.
Pressure and Temperature Ratings:
The hose must have a pressure rating that matches or exceeds the maximum operating pressure of the hydraulic system. Using a hose with insufficient pressure capacity can lead to bulging or bursting under stress.
Ensure that the hose’s temperature rating is suitable for both the fluid it carries and the external environment. For example, use heat-resistant hoses near engines or furnaces, and cold-resistant hoses in low-temperature settings.
Fluid Compatibility:
Verify that the hose material is chemically compatible with the hydraulic fluid used. For example, synthetic rubber hoses may not be suitable for certain synthetic hydraulic fluids, which can cause swelling or softening.
Always check the manufacturer’s compatibility charts or guidelines to prevent material degradation, leaks, or contamination.
Correct Installation Practices
Proper installation is crucial to prevent hose damage and ensure reliable performance. Follow these guidelines for effective installation:
Proper Routing:
Route hoses to avoid sharp bends, twists, or kinks, as these can weaken the hose material and lead to premature failure. Use gentle, sweeping curves that adhere to the hose’s minimum bend radius specifications.
Avoid routing hoses through tight spaces or over rough surfaces, which can cause abrasions or compress the hose, restricting fluid flow and increasing internal pressure.
Securing Hoses:
Use clamps, brackets, and ties to secure hoses in place and prevent movement during operation. Loose hoses can vibrate excessively, leading to wear at contact points or fitting blow-offs.
Ensure that the hose is not under tension or stretched too tightly, as this can place undue stress on both the hose and its fittings.
Minimizing Stress Points:
Stress points, such as areas near fittings, bends, or moving components, are more prone to wear and failure. To reduce stress, use support brackets or guides that distribute pressure evenly along the hose’s length.
Consider using flexible hoses or swivel fittings in applications that require frequent movement, as this helps prevent twisting and reduces stress.
Proper installation not only extends the lifespan of the hose but also improves system efficiency by maintaining consistent fluid flow and pressure.
Routine Maintenance and Inspections
Regular maintenance and inspections are vital for identifying early wear signs and ensuring hose longevity:
Establishing a Regular Inspection Schedule:
Develop a maintenance schedule based on the manufacturer’s recommendations and the operating environment. Inspect hoses for cracks, abrasions, leaks, bulging, and fitting integrity.
Conduct visual inspections before each use, with more thorough checks weekly or monthly, depending on the system’s intensity and working conditions.
Cleaning Hoses:
Hydraulic fluid residues, dirt, and other contaminants can degrade the hose material over time. Regularly clean hoses with compatible cleaning agents to maintain optimal performance.
Clean fittings as well, as built-up debris can affect the seal quality and increase the risk of leaks.
Proactive Hose Replacement:
Replace hoses based on usage history, not just visible damage. Waiting for a hose to show signs of failure can lead to unexpected downtime. Follow manufacturer guidelines for replacement intervals, even if hoses appear to be in good condition.
Routine maintenance reduces the likelihood of sudden failures, lowers overall maintenance costs, and improves system safety.
Pressure Regulation
Managing system pressure is another critical step in preventing hose failures:
Implementing Pressure Relief Valves:
Pressure relief valves help control pressure surges, preventing spikes that could damage hoses. Install these valves at critical points in the hydraulic circuit to protect hoses from excessive pressure.
Regularly test and maintain pressure relief valves to ensure they function properly, as malfunctioning valves can lead to catastrophic system failures.
Regular System Pressure Checks:
Use pressure gauges to monitor system pressure and identify any deviations from normal operating conditions. Pressure fluctuations can signal hose weakening, blockages, or leaks, prompting further inspection or replacement.
Install digital pressure sensors for real-time monitoring and alerts, ensuring immediate response to abnormal pressure levels.
Maintaining stable system pressure not only protects hoses but also optimizes hydraulic system performance.
Use of Protective Accessories
Protective accessories enhance hose durability by preventing damage from abrasions, heat, and external impact:
Hose Sleeves:
Hose sleeves are flexible protective coverings that shield hoses from abrasions, cuts, and chemical exposure. Made from materials like nylon, polyester, or steel mesh, they add an extra layer of protection, especially in high-wear areas.
Use hose sleeves in applications where hoses are likely to rub against surfaces, machinery, or other hoses.
Hose Guards:
Hose guards, often spiral or spring-shaped, protect hoses from impact and prevent kinks. They are particularly useful in heavy-duty applications where hoses are exposed to physical damage.
Spiral guards can be wrapped around hoses to provide added strength and resilience against crushing or sharp edges.
Protective Covers:
In environments with extreme temperatures, protective covers help insulate hoses from heat sources or freezing conditions. Heat-resistant covers prevent hoses from softening or swelling while insulating covers maintain flexibility in cold temperatures.
Conclusion
Proactive safety measures, such as proper hose selection, correct installation, routine maintenance, and pressure regulation, form the foundation of a reliable hydraulic system. Integrating advanced techniques like predictive maintenance, employee training, and structured hose management further enhances safety and performance, reducing the likelihood of sudden failures.
FAQ
What are the common causes of hydraulic hose failures?
Mechanical stress, thermal extremes, chemical exposure, improper installation, and natural aging.
How can I prevent hydraulic hose failures?
Use proper hose selection, correct installation, routine maintenance, pressure regulation, and protective accessories.
What is predictive maintenance for hydraulic hoses?
It involves using IoT sensors and real-time monitoring to detect potential hose failures before they occur.
How often should hydraulic hoses be inspected?
Hoses should be visually inspected before each use, with more thorough checks performed weekly or monthly based on usage.
What should I do if a hydraulic hose fails?
Immediately shut down the system, contain any fluid leaks, and follow emergency response protocols to prevent injuries.
Why is proper training important for hose maintenance?
Proper training ensures that employees know how to handle, inspect, and respond to hose issues, reducing failure risks and improving safety.