Hydraulic hoses are critical components in any hydraulic system, responsible for transferring pressurized fluid to power machinery and equipment. However, hoses are subject to harsh operating conditions, including extreme temperatures, abrasive environments, and high-pressure demands, all of which can impact their durability.
Size
Why Size Matters
The size of a hydraulic hose plays a critical role in system performance and efficiency, as it directly influences fluid velocity and flow rate. When the hose size is properly matched to the system’s requirements, fluid flows smoothly at an optimal speed, ensuring efficient power transfer. However, if the hose diameter is too small, fluid velocity increases beyond safe levels, which can cause turbulent flow, excessive pressure loss, and even system damage. Conversely, an oversized hose may reduce fluid velocity too much, leading to low system pressure and poor performance. Therefore, choosing the correct hose size is essential for maintaining consistent operational efficiency and avoiding unnecessary strain on the hydraulic system.
Determining Hose Size
To determine the appropriate hose size, it’s essential to calculate the required inside diameter (I.D.), as this dimension governs fluid velocity and flow rate. Flow rate, measured in gallons per minute (GPM), and fluid velocity (feet per second) are both affected by the I.D. of the hose. For a given flow rate, a smaller I.D. increases fluid velocity, while a larger I.D. decreases it. Achieving the right balance is key; industry guidelines generally recommend keeping fluid velocity within certain limits to avoid excess friction and pressure loss. A simple formula or flow-sizing nomogram can help operators calculate the correct I.D. based on flow rate and desired velocity, ensuring the hose meets the specific application needs without compromising efficiency.
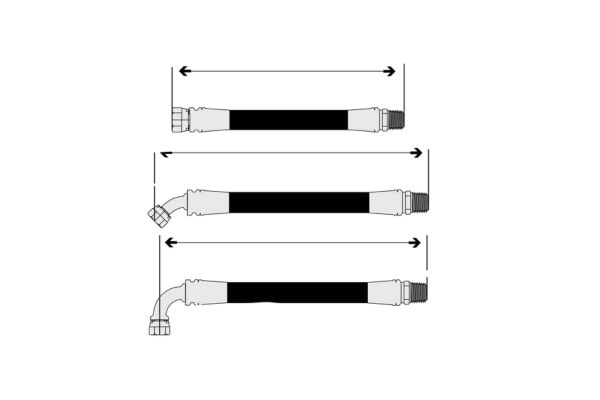
Common Sizing Mistakes
Selecting a hose size that is too large or too small can lead to various performance issues. A hose that is too small for the application increases fluid velocity, which can cause higher levels of friction within the hose, increasing pressure drop and wear on the hose lining. This can also result in overheating and premature hose failure. On the other hand, a hose that is too large may decrease fluid velocity to the point where performance is suboptimal, causing sluggish system response and reducing operational efficiency. Both scenarios create undue stress on the hydraulic system and can lead to increased maintenance needs, reduced hose life, and overall inefficiency.
Using Sizing Charts and Tools
To avoid sizing errors, using specialized sizing charts and tools can be invaluable. A nomogram—a visual chart that relates flow rate, fluid velocity, and hose diameter—can help operators select the appropriate hose I.D. for their application. Many hydraulic hose manufacturers provide such tools in their technical catalogs, allowing users to match hose dimensions to their system’s flow requirements quickly. By referencing these charts and tools, operators can make informed sizing choices that align with best practices, ensuring that their hydraulic hoses deliver optimal performance and durability.
Temperature
Effects of Temperature on Hose Life
Temperature plays a significant role in the longevity and performance of hydraulic hoses. Both the temperature of the fluid being conveyed (internal temperature) and the ambient temperature surrounding the hose (external temperature) can impact hose materials over time. When exposed to high temperatures, the rubber or synthetic materials in hoses may harden, crack, or lose flexibility, leading to premature degradation. Excessive heat can also compromise the integrity of the hose’s reinforcement layers, weakening its ability to handle pressure and reducing its service life. Conversely, extremely low temperatures can make hoses stiff and brittle, increasing the likelihood of fractures and reducing flexibility. To maintain optimal performance and hose life, it’s essential to consider both internal and external temperature factors.
Selecting Temperature-Resistant Hoses
Choosing a hydraulic hose with a temperature rating that meets or exceeds the requirements of both the fluid and the environment is essential. Each hose is rated for a specific temperature range, indicating the maximum and minimum temperatures it can handle without compromising durability. For example, if the conveyed media has a high operating temperature, such as hot oil, the hose must have a heat-resistant inner tube capable of withstanding these conditions. Similarly, if the application involves exposure to extreme ambient heat or cold, a hose with an appropriate external temperature rating should be selected to prevent material degradation. By matching hose temperature ratings to the application’s requirements, operators can avoid issues like hardening, cracking, and material breakdown, ensuring a longer hose life.
External and Internal Temperature Considerations
When assessing temperature-related needs, it’s crucial to evaluate both internal and external temperature factors:
Internal Temperature (Conveyed Media): This refers to the temperature of the fluid or media running through the hose. Different media types—such as oil, water, or chemicals—can have varying effects on the hose materials depending on their temperature. For instance, oil at high temperatures can soften certain hose linings, leading to leaks and weakening over time. Always select a hose rated for the highest expected fluid temperature to ensure it withstands internal thermal stresses.
External Temperature (Operating Environment): The surrounding temperature can also impact hose performance, especially when hoses are positioned near hot machinery components like engines or exhaust systems. Likewise, hoses exposed to extreme cold, such as outdoor or refrigerated environments, need materials that retain flexibility at low temperatures. By considering both internal and external temperature effects, operators can choose hoses designed to perform reliably under specific environmental conditions.
Protective Solutions for Temperature
In high-temperature applications, additional protective solutions can help manage thermal stress and preserve hose life. These include:
Heat-Resistant Sleeves: These sleeves provide a thermal barrier around the hose, shielding it from nearby heat sources. Materials like silicone-coated fiberglass are excellent choices for high-temperature environments, as they can withstand intense heat while protecting the hose.
Insulation Wraps: For environments with extreme temperature fluctuations, insulation wraps help maintain a consistent temperature within the hose, reducing the thermal stress that causes material hardening or cracking.
Rerouting Hoses: Where possible, position hoses away from direct heat sources to reduce exposure to high ambient temperatures. This can prevent overheating and extend the hose’s service life in hot environments.
Application
Understanding the Application Requirements
Selecting the right hydraulic hose requires a deep understanding of the application’s specific demands. Different applications expose hoses to unique challenges, such as high-frequency impulse cycles, environmental exposure to harsh elements, and varying levels of flexibility. A hose in a high-vibration industrial setting, for example, will require different specifications than one used in a static, low-pressure system. By evaluating each factor, including duty cycle, environmental conditions, and space constraints, operators can select a hose that not only meets the demands of the job but also maximizes performance and durability.
Key Factors in Application Suitability
Several critical factors influence hose suitability in any given application:
Impulse Frequency: Hydraulic hoses often experience frequent pressure fluctuations or surges. High impulse frequency subjects hoses to repetitive stress, which can lead to fatigue and premature wear. For these applications, hoses with spiral reinforcement are typically more durable than braided ones, as they are designed to handle continuous pressure spikes and high-frequency impulses.
Duty Cycle: The duty cycle refers to how often and under what conditions the hose operates. Heavy-duty applications with continuous or near-continuous operation demand hoses designed for durability and wear resistance, while lighter-duty applications may not need as robust a solution.
Flexibility Needs: Some applications require hoses that can flex and move frequently without risk of cracking or kinking. In such cases, choosing hoses with flexible reinforcement layers, like braided constructions, ensures greater adaptability to movement. Conversely, applications that involve little to no movement benefit from rigid, high-pressure spiral-reinforced hoses that offer maximum pressure resistance.
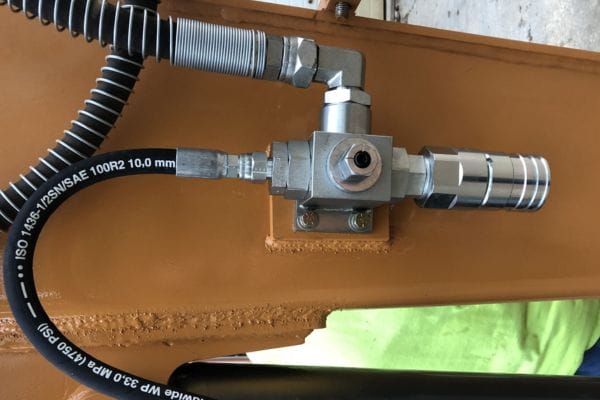
Bend Radius and Flexibility
Meeting the required bend radius is essential for optimal hose performance, particularly in applications with tight or constrained spaces. The bend radius is the minimum radius at which a hose can be bent without compromising its structural integrity. If a hose is bent beyond this radius, it puts excessive stress on the reinforcement layers, leading to potential kinking, restricted flow, or early failure. Selecting hoses that meet the necessary bend radius is especially important in compact spaces where hoses may need to curve tightly around machinery. When routing hoses in constrained areas, operators should consider using elbow fittings or adapters to achieve the necessary angles without compromising the hose’s bend radius.
Protective Accessories for Application-Specific Needs
In certain applications, additional protective accessories are necessary to enhance hose durability and safety:
Abrasion-Resistant Covers or Guards: In high-abrasion environments, such as mining or construction, hoses may be exposed to sharp surfaces or heavy friction. Abrasion-resistant covers or guards provide an extra layer of protection, helping to prevent wear and extend hose life.
Clamping Solutions: Long hose runs, especially those exposed to vibrations or movement, can benefit from clamps to prevent sagging and unwanted friction. Clamps secure hoses in place, reducing wear and protecting hoses from rubbing against each other or nearby surfaces. Proper clamping also improves the organization of hose installations, reducing the risk of accidental damage or interference.
Media
Importance of Media Compatibility
Ensuring compatibility between the conveyed media and the hose materials is crucial for system integrity and safety. Hydraulic hoses are designed to handle specific media types, whether they be oils, chemicals, water, or air, and the materials used in both the hose and fittings must be compatible with these substances. When the media is incompatible with the hose material, it can lead to breakdowns in the hose’s inner lining or outer cover, potentially contaminating the system and risking equipment failure. Proper media compatibility not only extends the hose’s lifespan but also maintains the quality and reliability of the entire hydraulic system.
Potential Issues with Incompatible Media
When a hose material is not suited for the conveyed media, several issues may arise that compromise hose performance and safety:
Hose Cover Blisters: Certain chemicals or oils can cause blistering on the hose cover, which weakens the hose’s exterior layer and exposes it to environmental damage.
Internal Erosion: Incompatible fluids may erode the hose’s inner lining over time, causing leaks and contaminating the fluid. This erosion gradually degrades the hose, increasing the risk of sudden failure.
Chemical Reactions: Some media can chemically react with the hose material, leading to hardening, softening, or other alterations in the hose’s structure. Such reactions weaken the hose’s ability to withstand pressure, potentially leading to ruptures or leaks.
Using a hose that is not compatible with the conveyed media results in early wear, frequent maintenance, and ultimately higher replacement costs. Ensuring compatibility is essential for a safe, efficient, and long-lasting hydraulic system.
Choosing the Right Hose Material
Different hose materials offer unique benefits and limitations when handling specific types of media:
Synthetic Rubber: Commonly used in hydraulic applications, synthetic rubber hoses are generally resistant to oils and non-corrosive fluids. However, they may not perform as well with certain solvents or chemicals, which can cause degradation over time.
Thermoplastic: Thermoplastic hoses are versatile and chemically resistant, making them suitable for applications involving a wide range of chemicals, fuels, and gases. They are often more resistant to abrasion than rubber hoses and can be a good choice in chemically challenging environments.
PTFE (Polytetrafluoroethylene): Known for its chemical inertness, PTFE hoses are highly resistant to a wide range of chemicals, making them suitable for applications involving aggressive or corrosive media. They also handle high temperatures well, making them ideal for hot fluid applications.
Selecting a hose with materials designed to handle the conveyed media ensures that the hose remains resilient, reduces wear and tear, and maintains fluid integrity throughout the system.
Using Chemical Compatibility Charts
To avoid media-related hose damage, it’s essential to consult chemical compatibility charts provided by hose manufacturers. These charts list the compatibility of different hose materials with various chemicals, oils, fuels, and other fluids, providing a clear guide to selecting the best hose for each application. By cross-referencing the conveyed media with compatibility charts, operators can verify that the chosen hose material will safely handle the media without causing degradation. Relying on these charts helps prevent costly mistakes, reduces the risk of premature hose failure, and supports safer and more reliable hydraulic operations.
Pressure
Impact of Pressure on Hose Selection
Choosing a hydraulic hose with the appropriate pressure rating is essential for safe and reliable operation. Each hydraulic hose is designed with a specific working pressure limit, which defines the maximum continuous pressure it can handle without risk of damage. To ensure the hose can withstand the demands of the system, the hose’s pressure rating must match or exceed the system’s operating pressure. Underestimating this requirement can lead to dangerous scenarios, such as hose bursts or leaks, which pose safety risks, interrupt operations, and increase maintenance costs. Selecting a hose with the correct pressure rating helps maintain system integrity, ensures operational reliability, and prevents premature hose wear.
Understanding System vs. Impulse Pressure
In hydraulic systems, it’s essential to consider both continuous system pressure and impulse pressure, as both can affect hose durability.
System Pressure: This is the constant, sustained pressure within the hydraulic system when it is in operation. Hoses must be rated to handle this continuous pressure over extended periods without failure.
Impulse Pressure: Impulse pressure refers to sudden spikes or surges in pressure, often resulting from rapid valve closures, start-ups, or load changes. These surges can significantly exceed the system’s regular operating pressure, creating brief but intense pressure peaks. High-pressure hoses designed to handle impulse pressures are built with reinforced materials to withstand these repetitive spikes without compromising the hose structure.
Understanding the distinction between system and impulse pressures is key to selecting a hose that can perform under both steady and fluctuating pressure conditions, ensuring the hose’s longevity and minimizing the risk of failure.
Pressure Rating Guidelines
When selecting a hydraulic hose, operators must ensure that the hose’s pressure rating meets or exceeds the maximum pressure expected within the system, including any potential surges. Hoses typically have ratings for minimum burst pressure, working pressure, and sometimes maximum surge pressure, which provides insight into their suitability for different pressure conditions. Adhering to these pressure rating guidelines ensures that hoses are well-equipped to handle both continuous and occasional peak pressures, reducing the likelihood of unexpected failures. Overrating the pressure capacity—by choosing a hose with a margin above the required working pressure—adds a safety buffer, further protecting the system in high-stress situations.
Preventing Hose Failure Due to Pressure
In high-pressure applications, several preventive measures can help avoid hose failure:
Whip Restraints: Whip restraints are essential safety components in high-pressure systems, especially where pressure surges or disconnections are possible. A whip restraint system prevents a hose from whipping or flailing uncontrollably in the event of a sudden release from its fitting. By securely containing the hose, whip restraints protect nearby personnel and equipment, minimizing the risks associated with sudden hose disconnections.
Properly Rated Fittings: Choosing fittings with pressure ratings that match the hose’s capacity is equally important. Mismatched fittings may become weak points, increasing the risk of hose separation or leaks. By ensuring that both hoses and fittings have compatible pressure ratings, operators can achieve a safer, more resilient system that reduces maintenance and replacement needs.
Conclusion
Using the S.T.A.M.P. method as a checklist for hydraulic hose selection and replacement helps operators make informed decisions that align with system requirements and operating conditions. This proactive approach allows for optimal performance, greater durability, and enhanced safety, ensuring that each hose in the system is tailored to its unique role.
FAQ
What does S.T.A.M.P. stand for in hydraulic hose selection?
S.T.A.M.P. stands for Size, Temperature, Application, Media, and Pressure—the five key factors to consider when selecting a hydraulic hose.
Why is hose size important in hydraulic systems?
The correct hose size ensures optimal fluid flow, reduces pressure loss, and prevents excessive wear, which improves system efficiency.
How does temperature affect hydraulic hoses?
High or low temperatures can cause hoses to harden, crack, or lose flexibility. Selecting a hose with the right temperature rating prevents premature wear.
What is media compatibility, and why does it matter?
Media compatibility ensures that the hose materials won’t react with the fluid inside, preventing leaks, contamination, and damage to the hose.
How do I choose a hose for high-pressure applications?
Select a hose with a pressure rating that meets or exceeds the system’s maximum operating pressure and use whip restraints to enhance safety.
Should I consult a specialist when choosing a hydraulic hose?
Yes, consulting a specialist can help you select hoses that meet specific S.T.A.M.P. criteria, ensuring optimal performance and system safety.