You need to disconnect a hydraulic line, but you’re dreading the messy oil spill and the struggle to reconnect it later. This common frustration leads to unsafe working conditions, environmental contamination, and costly downtime.
To solve this, you must choose the right type of quick coupling for your specific job. The main connection styles are Poppet, Flat Face, and Screw-to-Connect, each designed with distinct advantages for different pressures, environments, and performance requirements.
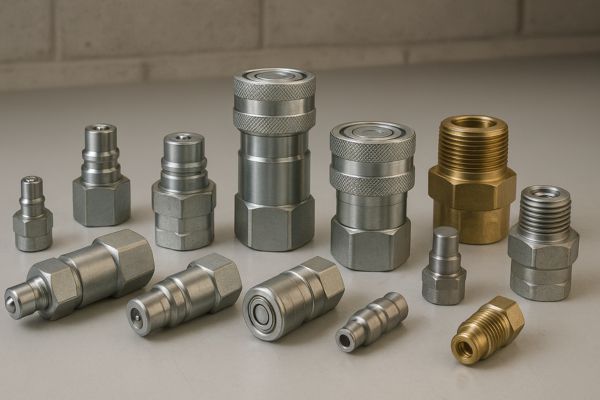
What is the Most Common General-Purpose Quick Coupling?
You see a standard-looking “nipple and sleeve” quick coupler on most machinery. You assume it’s a universal solution, but then you experience minor leaks, oil spillage upon disconnection, and difficulty in dirty environments.
This is a Poppet-style coupling, the industry’s workhorse for general-purpose applications. It uses an internal valve that is pushed open upon connection. While cost-effective and widely available (conforming to ISO 7241 standards), its design can allow for fluid spillage and air inclusion.
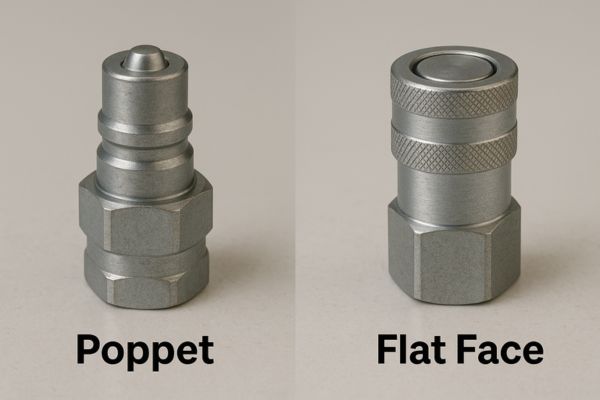
The poppet-style coupling is likely what most people picture when they think of a hydraulic quick coupler. It’s the most established design and is ubiquitous in agriculture and general industrial applications. Its popularity stems from a good balance of performance and cost.
How the Poppet Mechanism Works
Inside both the male tip (plug) and the female body (coupler), there is a small valve, shaped like a mushroom or a cone (the “poppet”). This valve is held shut by a spring. When you push the male tip into the female body, the tip physically pushes the female poppet off its seat, and the female body pushes the male poppet off its seat. This opens a path for the fluid to flow. The connection is held secure by a ring of ball bearings in the female coupler that lock into a groove on the male tip. A retractable sleeve on the female body holds these balls in place.
Common Standards – ISO A vs. ISO B
Even within the general “poppet” category, there are important standards that are not interchangeable.
- ISO 7241-A (ISO A): This is the most popular standard globally for agricultural and general industrial applications. It uses a poppet valve and a ball-locking mechanism. As a major supplier to farms in the Philippines and construction companies in the USA, this is one of our highest-volume products.
- ISO 7241-B (ISO B): This standard is more common in North American industrial applications. It uses a poppet valve but has a different physical profile and often uses a sleeve-lock mechanism. It is dimensionally different from ISO A and they cannot be connected.
Feature | Poppet-Style Couplings |
Pros | – Highly cost-effective – Widely available and standardized (ISO A/B) – Good flow characteristics for the price |
Cons | – Spillage occurs during connection/disconnection – Air can be included in the system on connection – Exposed poppet can trap dirt, leading to seal damage – Can be difficult to connect with residual pressure |
This type of coupling is an excellent choice for applications where a small amount of oil spillage is acceptable and the working environment is relatively clean.
Why Are Flat Face Couplings Essential for Cleanliness and Safety?
You’re working in a clean factory or on a modern construction site where hydraulic oil spills are absolutely unacceptable. A small drip from a standard coupler can create a safety hazard, contaminate products, and damage the environment.
Flat Face quick couplings, designed to the ISO 16028 standard, are the definitive solution. Their unique design allows the two flat faces to mate and create a seal before the internal valves open, resulting in a near-drip-free connection and disconnection process.
The development of the flat face coupling was a true revolution in hydraulic connectivity, driven by demands for higher efficiency and stricter environmental and safety standards. On modern skid steer loaders and other compact construction equipment, they are now the standard, and for good reason.
The Ingenious Flat Face Design
The magic of the flat face coupler is its flush-mating sequence.
- As you push the two halves together, the two flat metal faces make contact first.
- With the outer seal made, you continue to push. This internal movement then pushes the two internal valves off their seats, opening the flow path.
- Upon disconnection, the internal valves close before the two flat faces separate
This sequence traps any residual oil, resulting in virtually zero spillage. This same feature also prevents dirt, dust, and water from getting into the hydraulic system, as there is no cavity on the coupling face to trap contaminants.
Key Advantages Over Poppet Couplers
For a professional buyer like Tony, comparing the technical advantages directly shows the value proposition.
Feature | Poppet Coupler | Flat Face Coupler (ISO 16028) |
Spillage | High | Near Zero |
Contamination Risk | High (has a cavity) | Low (smooth, easy-to-clean face) |
Flow Rate | Good | Excellent (less turbulence) |
Connect Under Pressure | Difficult / Impossible | Can be difficult, but special versions exist |
Cost | Standard | Premium |
Where Flat Face Couplings Shine
Based on our sales data and customer feedback from regions like Europe and North America where standards are very high, we see flat face couplers as essential for:
- Skid Steer Loaders & Compact Equipment: Where attachments are changed frequently.
- Indoor Factory Automation: Where a clean floor is a safety requirement.
- Food Processing Lines: To prevent any risk of hydraulic fluid contamination.
- Environmentally Sensitive Areas: To prevent soil and water contamination.
For any application where cleanliness, safety, and system longevity are top priorities, the higher initial investment in flat face couplings pays for itself many times over.
When Do You Need the Ultimate Strength of a Screw-to-Connect Coupling?
Your equipment operates under bone-jarring vibration and experiences massive, repetitive pressure spikes. A standard push-to-connect coupler could potentially wiggle loose or fail under these extreme forces, leading to a dangerous and costly failure.
Screw-to-Connect couplings are engineered for these exact conditions. Instead of a retractable sleeve, they use heavy-duty threads to manually screw the two halves together, creating an incredibly strong and vibration-resistant physical connection that can withstand the highest pressures and impulses.
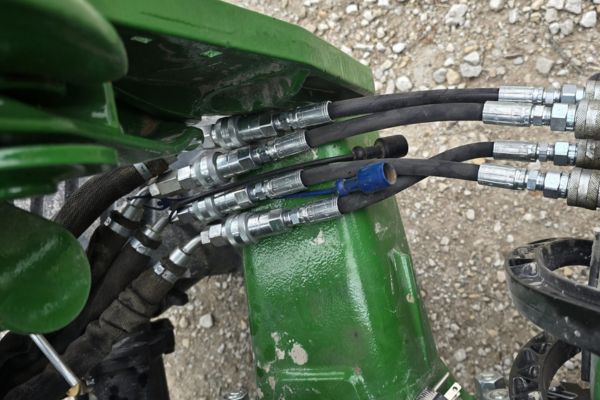
There are some hydraulic applications that are simply too brutal for standard couplers. I’m talking about demolition shears, rock crushers, and large-scale hydraulic presses. For my clients in mining and heavy demolition, screw-to-connect couplers are not a luxury; they are the only safe and reliable option.
The Brute Force Connection Method
The design principle is simple and incredibly effective. The male and female halves have machined threads. To connect, you push them together and then rotate the sleeve on the female coupler. This threading action physically pulls the two halves together and locks them into place. This offers two massive advantages:
- Vibration Resistance: The threaded connection cannot be shaken loose by vibration, unlike a ball-lock which could potentially experience fretting under extreme conditions.
- Connect Under Pressure Capability: The mechanical advantage of the threads is powerful enough to overcome the force of trapped residual pressure in a line, allowing you to make connections that would be physically impossible with a push-to-connect style.
Unmatched Performance in Extreme Conditions
Let’s be clear about where these heavy-duty couplers belong.
Feature | Screw-to-Connect Couplings |
Pros | – Highest pressure ratings (up to 10,000 PSI+) – Extreme resistance to pressure spikes and impulses – Best resistance to heavy vibration – Can be connected against high residual pressure |
Cons | – Slower to connect and disconnect – Can be bulky and heavy – Highest cost of all coupling types |
These are a specialty product for the most demanding 5% of applications. We supply these to clients operating high-impulse tools where reliability is a matter of operational survival. If you have a hydraulic hammer or a high-tonnage press, you need the absolute security that only a screw-to-connect coupling can provide.
What is the Critical Role of the Locking Mechanism?
You push a coupler together and it clicks, but how does it actually stay locked? Understanding the locking mechanism is key to diagnosing issues and selecting a coupler that is easy and safe to operate for your specific needs.
The locking mechanism physically secures the male and female halves of a push-to-connect coupler. The most common type is a ball-lock, held in place by a retractable sleeve. The design of this sleeve (e.g., manual vs. automatic) impacts the ease of use and safety of the coupling.
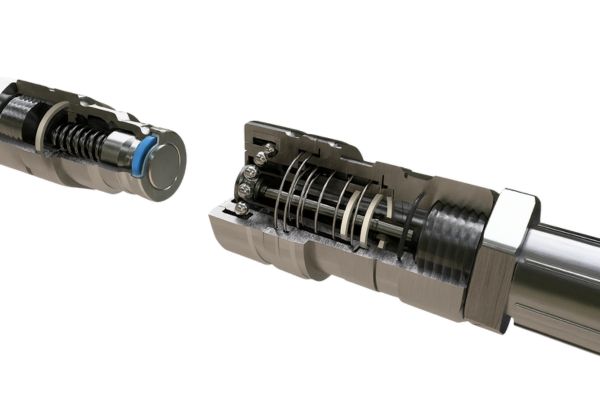
While we have focused on the internal valve types (poppet, flat face), the external mechanism that holds them together is just as important for the user experience.
The Ball-Locking System
This is the most prevalent system on poppet and flat face couplings.
- Mechanism: The female coupler has a ring of hardened steel ball bearings. The male plug has a corresponding hardened groove. When you push the plug in, the balls retract, allow the plug to pass, and then snap into the groove.
- The Sleeve: The sleeve is the critical component that holds the balls in place. If the sleeve is retracted, the balls can move out of the groove, and the coupling will disconnect.
Different Sleeve Types
The operation of the sleeve is a key differentiator.
- Manual Sleeve: This is the most basic design. To connect, you must manually pull back the sleeve, insert the male plug, and then release the sleeve. To disconnect, you pull back the sleeve again. This is a very secure two-handed operation.
- Push-to-Connect Sleeve: This is a more user-friendly design. The sleeve is spring-loaded. You can simply push the male plug into the coupler, and it will click and lock automatically. Disconnection still requires manually retracting the sleeve. This is the standard for most modern flat face and many ISO A couplers.
- Double Shut-Off vs. Single Shut-Off: Nearly all hydraulic couplers are “double shut-off,” meaning both the male and female halves have valves and seal when disconnected. “Single shut-off” couplers only have a valve in the female half; the male half is just an open probe. These are only suitable for fluids like air or water where spillage is not a concern. At Topa, we deal almost exclusively in double shut-off couplers for hydraulic systems.
Understanding these mechanisms helps a user troubleshoot. If a coupler won’t stay locked, the issue is likely with worn balls, a damaged groove on the male plug, or a faulty sleeve that isn’t fully returning to its forward position.
What Does “Interchangeability” Mean for Quick Couplings?
You need to replace just one half of a quick coupling, but you don’t know the original brand. Can you just buy any other brand that follows the same standard (e.g., ISO 16028) and expect it to work perfectly?
In theory, yes. Interchangeability means that a male half from one manufacturer will connect and function with a female half from another manufacturer, as long as they both adhere to the same dimensional standard. However, minor tolerance differences can sometimes lead to slight leaks or connection issues.
This is a constant source of questions from professional buyers. They want to source parts economically but need to guarantee performance. The concept of interchangeability is central to this.
The Power of ISO Standards
The International Organization for Standardization (ISO) creates the documents that define the exact dimensions, performance requirements, and testing procedures for many common couplers. This allows for a competitive global market.
- ISO 7241 Series A: Defines the common agricultural poppet style.
- ISO 7241 Series B: Defines the common industrial poppet style.
- ISO 16028: Defines the general-purpose flat face style.
- ISO 5675: A specific standard for agricultural poppet couplers (largely harmonized with ISO 7241-A).
The Reality of Mixing Brands
While the standards are excellent, they do allow for small manufacturing tolerances.
- The Ideal Scenario: 95% of the time, mixing major brands that are certified to the same ISO standard will work without issue. For example, a Topa ISO 16028 male half will connect perfectly with another major brand’s ISO 16028 female half.
- The Potential Problem: In some rare cases, if one manufacturer is at the high end of a tolerance band and another is at the low end, you might experience a “weep” leak or a connection that feels too tight or too loose.
- Proprietary Designs: Be aware that some manufacturers produce couplers that look like a standard but are intentionally proprietary. They have slightly different dimensions to lock customers into their specific brand.
The Guaranteed Solution
As a trusted supplier, my advice to customers, especially for critical new builds, is always this: for guaranteed, leak-free performance, purchase both the male and female halves from the same trusted manufacturer. By sourcing your matched pairs from us, we can guarantee that the two halves were manufactured and tested together to provide a perfect seal and smooth operation right out of the box. This eliminates any small risk associated with mixing brands and gives you complete peace of mind.