The defining feature of a 3-way ball valve is its ability to control multiple flow paths. Using a rotating ball with an internal “L” or “T” port configuration, these valves can align different ports to open or close specific pathways within the system. This allows operators to control fluid flow in various ways, such as diverting fluid from one pipe to another, combining flows, or even isolating one part of a system for maintenance.
Basics of 3-Way Ball Valves
What is a 3-Way Ball Valve?
A 3-way ball valve is a type of ball valve specifically designed to manage fluid flow between three distinct ports. Unlike standard two-way ball valves, which simply allow or block flow along a single path, 3-way ball valves are built to direct flow in multiple directions. This flexibility makes them ideal for systems where fluid needs to be diverted, mixed, or directed between different paths, such as in mixing applications or systems requiring multiple outputs. By offering multiple configurations and options for fluid routing, 3-way ball valves bring enhanced control and adaptability to fluid management.
Structure and Components
Like standard ball valves, 3-way ball valves share several key components, each contributing to the valve’s ability to control complex flow paths:
Valve Body: The outer casing of the valve that houses the ball, ports, and seals. It is typically made from durable materials such as stainless steel, brass, or plastic, chosen based on the intended application and fluid type.
Ball: The core of the valve, this sphere has a drilled pathway (L- or T-shaped) that determines how fluid flows through the ports. The ball rotates within the valve body to align the ports, controlling which paths are open or closed.
Ports: Three openings, labeled A, B, and C, through which fluid can enter or exit the valve. These ports allow for diverse flow path options depending on the ball’s position.
Handle or Actuator: The mechanism used to operate the valve. Manual handles allow for direct, quarter-turn control, while actuators (pneumatic, electric, or hydraulic) can automate the valve’s movement, making it suitable for remote or automated systems.
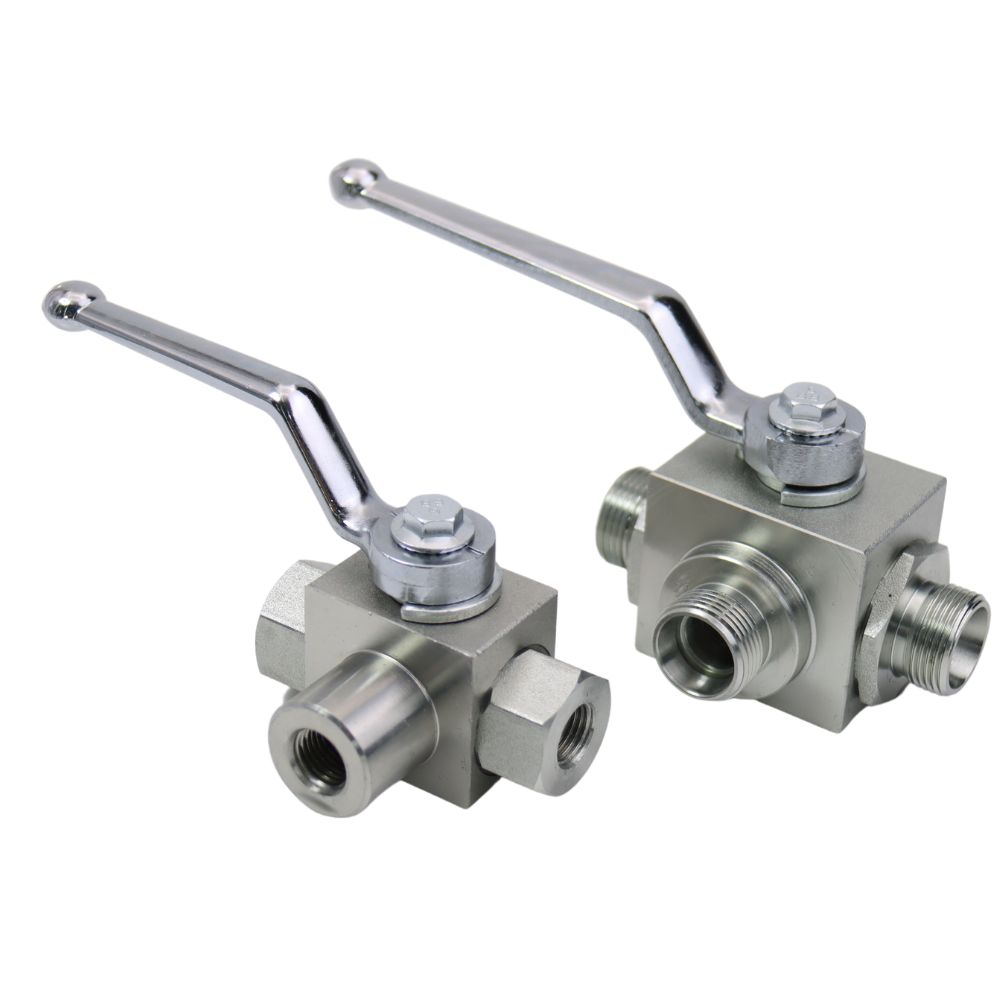
Flow Paths
The defining feature of a 3-way ball valve is its ability to control fluid flow through three separate ports. By adjusting the ball’s position within the valve, operators can direct flow between different ports in multiple configurations. This makes 3-way valves versatile for various fluid control needs, such as diverting, mixing, or isolating fluid paths.
Depending on the valve’s configuration, the 3-way ball valve can either open a flow path between two of the ports or link all three ports, allowing fluid to flow through the system in distinct pathways. This control over multiple paths is what makes 3-way valves so valuable in applications where fluid needs to be managed dynamically.
How the Ball Controls Flow
The ball inside the 3-way valve is drilled with an internal passage that aligns or blocks specific ports based on its rotation. In a manually operated 3-way valve, rotating the handle (usually a quarter turn) moves the ball to a position where the desired ports are connected. In automated systems, actuators perform this rotation, allowing for remote control and precise timing.
L-Port: When the ball is rotated, the L-shaped passage aligns two of the ports while blocking the third, creating a flow path between two chosen ports. A 90-degree rotation changes the flow path, switching the connection to a different pair of ports.
T-Port: The T-shaped passage in a T-port valve allows for more complex configurations. By rotating the ball, the operator can connect all three ports, enabling a combined flow, or align two ports while blocking the third. This makes T-port valves versatile in creating multiple flow options based on system needs.
Types of 3-Way Ball Valves
L-Port vs. T-Port Configurations
L-Port Configuration
The L-port configuration is a popular design for 3-way ball valves and is named for its L-shaped internal passage within the ball. This design allows the valve to direct flow from one port to another at a 90-degree angle, connecting two of the three ports at any time. The L-port configuration is commonly used for applications requiring the switching of fluid flow between two outputs or isolating one line while allowing flow in another.
How It Works: With an L-port ball, a quarter-turn (90-degree rotation) can align the passage to connect ports A and B, isolating port C. A further quarter-turn can switch the flow to connect ports A and C, isolating port B. This straightforward switching mechanism allows users to alternate between two paths without needing multiple valves.
Best Uses: L-port valves are ideal for applications where fluid must be directed from a single input to one of two possible outputs, such as selecting between two storage tanks or isolating parts of a system. They are commonly found in fuel systems, plumbing applications, and wastewater management, where quick switching between paths is essential.
T-Port Configuration
The T-port configuration features a T-shaped internal passage that allows more versatile flow control, as it can connect all three ports simultaneously or isolate any one of them. T-port valves can be used to mix flows from two inlets into a single output, divert flow from one source to two destinations, or simply block one port while connecting the other two.
How It Works: When the T-port ball is rotated, it can connect all three ports, creating a pathway where fluid flows through each port at the same time. Alternatively, rotating the valve can isolate any one of the three ports while connecting the other two, providing flexible routing options. A 90-degree turn typically connects ports in a T-shape, while a 180-degree turn can isolate one port.
Best Uses: T-port valves are preferred in fluid mixing applications where two sources need to be combined, or in distribution systems where fluid needs to be diverted to multiple outputs. They are commonly used in chemical processing, pharmaceuticals, and HVAC systems to achieve precise flow routing, mixing, and control.
Manually Operated vs. Automated 3-Way Ball Valves
Manual Valves
Manually operated 3-way ball valves are controlled using a handle or lever that enables the operator to switch between flow paths. By simply turning the handle, the internal ball is rotated to align with the desired ports, allowing for easy and immediate control over fluid direction. Manual valves are generally cost-effective and are suitable for applications where infrequent adjustments or local control is sufficient.
Best Uses: Manual 3-way ball valves are ideal for smaller systems, residential plumbing, and non-critical applications where operators can directly access the valve and make adjustments as needed. They are often used in simple mixing or diverting tasks, such as switching between two water tanks or combining two fluid lines at a point of use.
Automated Valves
Automated 3-way ball valves use actuators—such as pneumatic, hydraulic, or electric mechanisms—to rotate the ball and control flow paths. Automated valves allow for remote or automated control, making them suitable for applications that require frequent adjustments, quick response times, or integration into automated systems.
Types of Actuators:
Pneumatic Actuators: Operate the valve using compressed air, providing quick and reliable control. Pneumatic actuators are often used in high-cycle industrial settings where safety and speed are priorities.
Hydraulic Actuators: Utilize pressurized hydraulic fluid to move the valve, ideal for systems requiring high torque or that handle thick or viscous fluids.
Electric Actuators: Operate the valve with an electric motor, allowing precise control over flow paths and easy integration into control systems. Electric actuators are often chosen for remote operations or where precise adjustments are necessary.
Best Uses: Automated 3-way ball valves are valuable in industrial applications, process automation, and systems where remote or hands-off control is needed. They are commonly used in water treatment, chemical processing, and HVAC systems where flow adjustments need to be made without manual intervention.
Diverter Valves vs. Mixing Valves
Diverter Valves
Diverter valves are a type of 3-way ball valve designed to redirect fluid from a single source to different destinations. The internal ball’s configuration allows fluid to enter from one port and then be routed to either of the two other ports based on the ball’s position. Diverter valves are commonly configured as L-port valves, as they allow easy switching between two outputs.
How They Work: In a diverter setup, the ball is oriented so that fluid entering through port A can be directed either to port B or port C. By rotating the handle or actuator, the operator can select the desired flow path to control where the fluid is directed.
Best Uses: Diverter 3-way valves are ideal for switching applications where fluid needs to be directed to different outputs, such as in irrigation systems, fuel distribution, or systems that alternate between two tanks or processing units.
Mixing Valves
Mixing valves are 3-way ball valves designed to combine fluid from two sources into a single output. These valves typically use a T-port configuration to link two inlet ports to one outlet, allowing fluid from both sources to flow together into a combined stream. Mixing valves are useful in applications requiring precise blending or combination of fluids.
How They Work: In a mixing setup, the ball is oriented to allow fluid from ports A and B to flow into a combined output through port C. By adjusting the valve, operators can control the mix ratio or divert one of the sources to an alternate path as needed.
Best Uses: Mixing 3-way valves are essential in chemical processing, pharmaceutical production, and HVAC systems where fluids or gases need to be blended. They are also used in temperature control applications, where hot and cold fluids are mixed to reach a desired output temperature.
How 3-Way Ball Valves Work
Flow Path Control
The core function of a 3-way ball valve is its ability to control the flow path by adjusting the orientation of the internal ball. The ball has a drilled passageway (either L-shaped or T-shaped) that determines how the flow is directed through the ports based on its position.
Open and Closed Positions
In a 3-way ball valve, the open and closed positions are controlled by rotating the ball. When the handle or actuator is turned, it rotates the ball within the valve body, aligning the internal passageway with different ports to create or block flow paths.
Open Position: When the ball aligns with two or three of the valve’s ports, it creates a flow path, allowing fluid to pass through. For example, in an L-port valve, the ball’s L-shaped passage can align two ports (such as A and B) while isolating the third port (C), establishing an open connection between two selected ports.
Closed Position: In configurations where one port needs to be isolated, the ball is rotated to block that port while maintaining flow between the other two. In a T-port valve, a specific position can be chosen to connect only two of the three ports, blocking the remaining port to prevent any fluid flow through it.
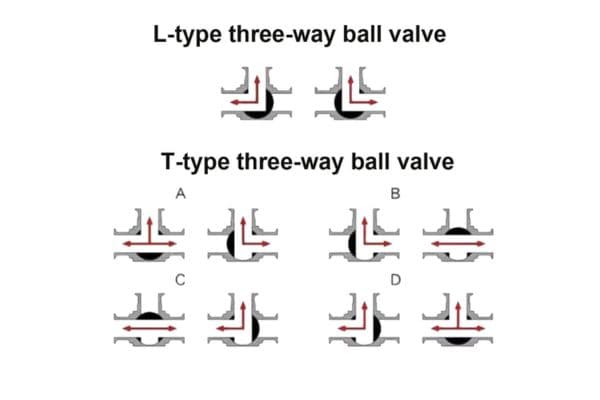
Switching Between Ports
The ball inside a 3-way valve is typically rotated at either a 90-degree or 180-degree angle. This rotation aligns the drilled passage with different ports to change the flow path. The mechanism allows for easy switching between flow paths, making the 3-way ball valve highly adaptable for applications where flow needs to be redirected or adjusted frequently.
90-Degree Rotation: This is common in L-port valves, where a quarter turn switches the alignment to connect two out of three ports. By rotating the ball 90 degrees, the operator can direct fluid from one source to either of two destinations, switching between two output paths or isolating a path as needed.
180-Degree Rotation: In T-port configurations, a half turn may be used to connect or block specific ports based on system requirements. A 180-degree turn might connect all three ports for mixing or diverting purposes, or it could block one port while connecting the remaining two.
Flow Configurations for Different Applications
3-way ball valves offer different configurations to meet specific application needs, particularly for diverting or mixing fluid flows.
Diverting Flow
In a diverting setup, the 3-way ball valve is used to redirect fluid from a single input to one of two outputs. This is particularly useful in systems where fluid needs to be directed to different locations, such as supply lines, waste management systems, or fuel distribution networks.
Application Example: In a wastewater system, an L-port 3-way ball valve might be used to divert flow between two tanks, directing waste to one tank until it’s full, and then switching the flow to the second tank. The L-shaped passage in the ball makes it easy to control which port receives the flow by rotating the handle.
Mixing Flow
Mixing configurations are used when two sources of fluid need to be combined into a single output. T-port 3-way valves are especially suitable for mixing, as the T-shaped passage in the ball allows two inlet ports to connect to a single outlet, enabling the fluids to merge in a controlled manner.
Application Example: In chemical processing, a T-port 3-way valve can be used to mix two reactants into a combined stream before they enter a reaction chamber. The T-port enables smooth blending of the two fluids, ensuring even distribution and precise control over the flow.
HVAC Systems: In heating and cooling systems, T-port valves can mix hot and cold water to achieve the desired temperature for climate control. By adjusting the flow from each source, operators can control the temperature of the mixed output, creating a stable environment in various heating or cooling applications.
Pressure and Temperature Considerations
When selecting and operating 3-way ball valves, pressure, and temperature play a crucial role in determining their performance and suitability for specific applications.
High-Pressure Applications
In systems with high pressure, the materials and design of the 3-way ball valve must be robust enough to handle the load. For example, valves made from stainless steel or brass are generally more capable of withstanding higher pressures, making them suitable for industrial applications like fuel distribution, chemical processing, or hydraulic systems. High-pressure environments require precise seals and sturdy construction to prevent leaks and maintain reliable flow control.
Considerations: In high-pressure systems, automated 3-way valves with pneumatic or hydraulic actuators are often preferred for remote operation and quick response. Actuators provide additional control over the valve under pressure, minimizing the risk of leaks or damage due to manual handling.
Low-Pressure Applications
For low-pressure applications, such as residential plumbing or light commercial uses, 3-way ball valves made from materials like PVC or brass are often adequate. These valves can manage the lower flow rates and temperatures typical in such settings without compromising performance.
Considerations: Low-pressure 3-way ball valves are typically operated manually, as the lower operating force required allows for easy handle control. This setup is both cost-effective and efficient for small-scale applications where high durability and pressure resistance are less critical.
Temperature Tolerance
The materials and seals of a 3-way ball valve must also withstand the operating temperatures of the system. High temperatures, as found in industrial processes or hot water systems, can affect the valve’s performance if the materials are not rated for heat resistance. Stainless steel and reinforced plastic are common materials used in high-temperature applications, as they provide durability under heat without warping or degrading.
High-Temperature Use: In applications with high heat, like steam distribution or chemical processing, the seals should be made from heat-resistant materials (e.g., PTFE or Teflon) to prevent breakdown over time.
Low-Temperature Use: For cold environments, such as refrigeration, valve materials must withstand freezing temperatures without becoming brittle or prone to cracking. Valves used in these conditions should be checked to ensure the materials and seals are designed for low-temperature tolerance.
How to Choose the Right 3-Way Ball Valve
Consider Flow Path Needs
L-Port vs. T-Port Configurations
The primary decision when choosing a 3-way ball valve is selecting between an L-port or T-port configuration, as each is suited to different flow path requirements:
L-Port: An L-port valve has a 90-degree passageway in the shape of an “L,” allowing it to switch between two different flow paths. This configuration is ideal if you need to direct flow between two separate outputs or alternate between two destinations. For instance, an L-port valve is commonly used in applications where fluid must be routed to one of two tanks or lines, providing straightforward switching.
T-Port: A T-port valve has a T-shaped passage that enables all three ports to connect simultaneously, or allows one port to be isolated while the other two remain connected. This configuration is best suited for combining flows from two sources into one output or diverting flow to two destinations simultaneously. T-port valves are commonly used in mixing applications in chemical processing or HVAC systems where fluid sources need to be blended or distributed.
Manual vs. Automated Operation
The next consideration is whether the valve will be operated manually or requires automation:
Manual Operation: Manually operated valves use a handle for control, making them ideal for systems that do not require frequent adjustments or where the valve is easily accessible. Manual 3-way valves are cost-effective and provide direct, simple operation, suitable for smaller systems or non-critical applications.
Automated Operation: For systems requiring frequent flow adjustments, remote control, or precise timing, automated 3-way ball valves are recommended. These valves are equipped with actuators—either pneumatic, hydraulic, or electric—that allow remote or hands-off operation. Automated valves are ideal for industrial settings, water treatment, or complex fluid processing applications where quick responses and remote access are essential. Automation provides greater control and efficiency, especially in high-cycle applications.
Material and Construction
Choosing the right material for your 3-way ball valve is essential for ensuring compatibility with the fluid type, pressure, and temperature requirements of the application:
Stainless Steel: Highly durable and resistant to corrosion, stainless steel is ideal for industrial applications involving harsh chemicals, high pressure, or extreme temperatures. It is commonly used in chemical processing, oil and gas, and food industries.
Brass: Brass is resistant to corrosion and suitable for moderate-pressure applications, making it a good choice for residential or light commercial plumbing, as well as HVAC systems. However, brass is not recommended for highly corrosive or high-temperature fluids.
Plastic (e.g., PVC): Plastic 3-way ball valves, often made of PVC, are lightweight, resistant to corrosion, and suitable for low-pressure applications. They are widely used in water treatment, irrigation, and systems handling non-corrosive fluids. However, plastic valves are generally not suitable for high temperatures or industrial-grade pressures.
Selecting the right material ensures that the valve can withstand the system’s operating conditions, reducing the risk of corrosion, leaks, or valve failure over time.
Installation Environment
Finally, consider the physical environment where the valve will be installed to ensure compatibility with the surrounding equipment, piping layout, and space constraints:
Space Constraints: Ensure that the valve can fit within the available space, especially if the valve needs to be turned manually or if there are space restrictions that could limit actuator installation.
Piping Layout: Evaluate the piping configuration to make sure the valve’s ports align with existing pipes and that there is adequate space for maintenance or adjustments. T-port valves, for example, may require more complex piping arrangements due to their multi-path capabilities.
Surrounding Equipment: Consider any nearby equipment that could affect or interfere with the valve’s operation, particularly if you are using an automated valve with an actuator. The valve should have clear access for control, maintenance, and adjustments without being obstructed by other system components.
Conclusion
For complex or critical applications, it is wise to consult with valve suppliers or engineers who can guide the best valve type, configuration, and material for your unique requirements. If you have any need for ball valves, please contact us!
FAQ
What is a 3-way ball valve?
A 3-way ball valve is a type of valve with three ports that allows for more versatile flow control, enabling the fluid to be directed, mixed, or diverted between multiple paths.
What’s the difference between L-port and T-port configurations?
An L-port directs flow between two of the three ports, ideal for switching between two paths. A T-port can connect all three ports or isolate one, allowing for mixing or more complex routing.
When should I use a manual vs. an automated 3-way ball valve?
Manual valves are suitable for systems needing infrequent adjustments. Automated valves, with actuators, are ideal for high-cycle or remote operations, allowing for precise and quick adjustments.
Which materials are best for 3-way ball valves?
Stainless steel is suitable for high-pressure, high-temperature, and corrosive applications. Brass is good for moderate pressure and temperatures, while PVC is ideal for low-pressure water systems.
What are common applications of 3-way ball valves?
They are commonly used in chemical processing, HVAC systems, water treatment, and fuel distribution for their ability to direct, divert, or mix flows.
How does a 3-way ball valve work
By rotating the ball, operators align the internal passage with specific ports to control the flow path, allowing the valve to switch between different flow configurations.