Your multi-ton rock drill grinds to a halt. A high-pressure hose, whipped back and forth and battered by falling rock, has finally given out. A messy, dangerous failure that stops your entire operation cold.
For high-impact mining, you need a hose system, not just a hose. This means a six-spiral wire reinforced hose (like SAE 100R15) for maximum impulse resistance, protected by a super abrasion-resistant “tough cover” and an external plastic spiral guard to defend against crushing physical impacts.
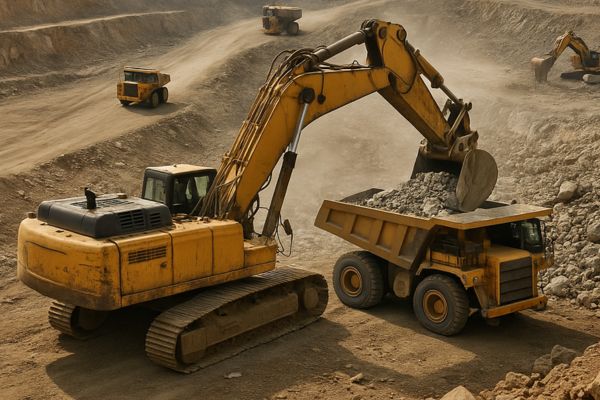
Why Does Spiral Wire Outperform Braided Wire in Mining?
You see that a six-wire hose is recommended, but you also see two-wire braided hoses with a high-pressure rating. Since they are more flexible and cheaper, you wonder if they are “good enough” for the job.
No, they are not. While a braided hose can handle high static pressure, it will fail quickly under the relentless, high-frequency pressure impulses of mining equipment. The parallel construction of spiral-wire hose is specifically designed to absorb these shocks without fatiguing.
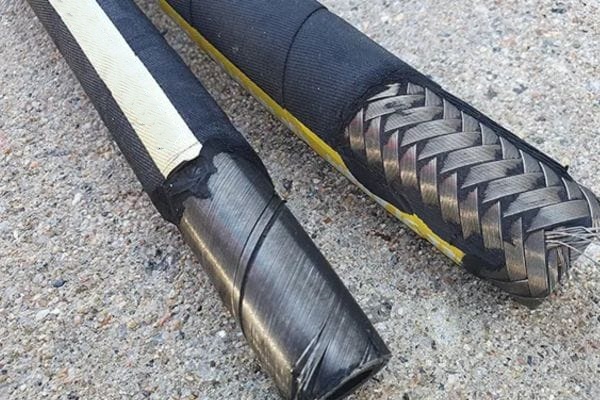
This is the most critical technical distinction to understand. The reinforcement inside the hose is its skeleton, and a mining application demands a skeleton that can withstand a constant barrage of pressure shocks.
The Problem with Braided Wire Under Impulse
In a braided hose, the wires cross over and under each other. Every time the hose is hit with a pressure impulse (like a hydraulic hammer striking), these wires rub against each other at the crossover points. This internal friction generates heat and slowly saws away at the wires. After hundreds of thousands of cycles, the wires begin to fail one by one, leading to a surprise burst. It’s a fatigue failure caused by the hose’s own construction.
The Superiority of Spiral Construction
In a spiral hose (SAE 100R12, R13, or R15), the layers of high-tensile steel wire are wound in parallel, with each layer spiraling in the opposite direction. They do not cross over or rub against each other. This design allows the reinforcement package to absorb and dissipate the energy from pressure spikes much more effectively. It is built for a high-cycle life. The industry standard impulse test requires a hose to survive a specified number of cycles, and spiral hoses vastly outperform their braided counterparts.
Matching the Hose to the Standard
For a professional buyer, knowing the standards is key.
Standard | Reinforcement | Common Application |
SAE 100R2 | Two layers, braided wire | General purpose, medium-high pressure |
SAE 100R12 | Four layers, spiral wire | High pressure, high impulse |
SAE 100R13 | Four/Six layers, spiral wire | Very high pressure, heavy construction |
SAE 100R15 | Four/Six layers, spiral wire | Mining, demolition, extreme duty |
For any hydraulic hammer, rock drill, or primary excavator circuit, an R13 or R15 hose is the correct engineering choice. The lower initial cost of a braided hose is quickly erased by the far higher cost of downtime.
Is a Standard Hose Cover Enough for Mining Operations?
You’ve selected a tough, spiral-wire hose. But the outer cover is just standard black rubber. In the harsh mining environment, this cover gets ripped and worn away quickly, exposing the steel reinforcement wires to moisture and damage.
A standard cover is not enough. It’s the first line of defense, and in a mine, it’s under constant attack. You need an upgraded, proprietary “tough cover” that offers dramatically higher abrasion resistance to protect the structural integrity of the hose.
I speak with many maintenance managers from operations in places like Ghana and Zimbabwe. A common issue they face is hose failure due to corrosion. The hose didn’t burst from pressure; it burst because the cover was worn away, the reinforcement wires rusted, and the hose lost its strength. The cause of failure wasn’t pressure—it was abrasion.
The Harsh Reality of the Mining Environment
A hose cover in a mine faces a relentless assault from:
- Constant Abrasion: Dragging over rock, ore, and gravel.
- Rubbing: Constant vibration against steel machine frames.
- Contaminants: Exposure to acidic mine water and chemicals.
- Impact: Being hit by falling debris.
A standard rubber cover is simply not formulated to survive this. It will be breached, allowing moisture to attack the steel wires beneath.
The Science of an Abrasion-Resistant Cover
A “tough cover” or “super abrasion” cover is not just thicker rubber. It’s a different material science. Manufacturers like us use advanced polymer blends and fillers to create a material that is measurably tougher. These proprietary compounds are engineered to resist being cut and torn at a molecular level.
When Must You Add External Protection to Your Hose?
You’ve chosen a top-of-the-line spiral hose with a super tough cover. But on a demolition shear or excavator bucket, the hose is still being crushed and cut by direct, heavy impacts.
When the threat changes from rubbing abrasion to direct impact and crushing, even the best hose cover is not enough. You must add a sacrificial layer of external protection, most commonly a heavy-duty plastic spiral guard.
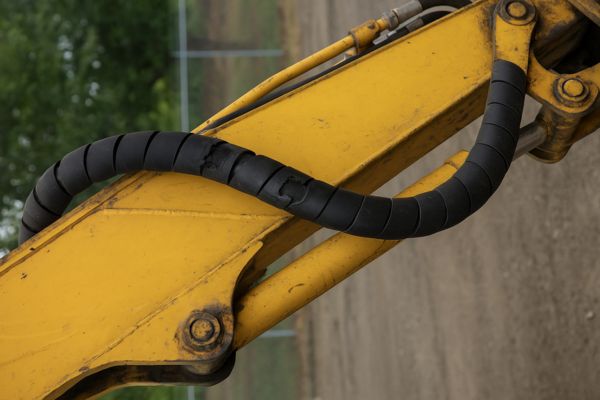
This is where we move from specifying a component to engineering a system. The external guard is not an optional accessory in mining; it is an essential piece of armor. I once had a customer in the US who kept having failures on the same hose line on his excavator. I asked for a photo, and the hose was routed right next to a point where rocks would fall. The hose was being used as a bumper. We specified a spiral guard, and the problem was solved. The guard’s cost was less than 5% of the cost of one downtime event.
Beyond Abrasion: Defending Against Crushing and Impact
A tough cover is great for sliding abrasion, but it can’t stop a sharp, 50-pound rock from cutting it. A spiral guard serves two functions:
- Standoff: It creates a thick, physical barrier between the hose and the threat. The guard takes the hit, not the hose.
- Impact Spreading: It distributes the force of an impact over a larger area, reducing the chance of a localized cut or crush.
The Plastic Spiral Guard: Your Sacrificial Armor
The most common and effective solution is a helical guard made from High-Density Polyethylene (HDPE). It’s incredibly tough, has beveled edges to prevent snagging, and can be easily installed on the hose before or after it is fitted. It is designed to be destroyed. It’s a cheap, replaceable component that protects your very expensive and critical hose assembly.
Other Protective Options
While plastic spiral guard is the most common, other options exist for specific threats:
- Metal Spring Guards: Offer even higher crush resistance but are heavier and less flexible.
- Textile Sleeves: Good for bundling hoses and adding a layer of abrasion resistance, but offer little impact protection.
- Silicone Fire Sleeves: Absolutely essential for hoses near hot engines or in case of fire, common on underground mining equipment.
How Do Fittings Contribute to Reliability Under High Impact?
You’ve built the perfect armored hose, but you connect it with an standard, low-grade fitting. The constant vibration and massive pressure spikes from the machinery work the fitting loose, causing a leak or a dangerous blowout.
The fitting is the critical link between the hose and the machine. In a high-vibration, high-impulse mining environment, you must use high-performance fittings, like O-Ring Face Seal (ORFS) or robust DIN Bite-Type couplings, that are specifically designed to resist loosening.
For hard-to-please, detail-oriented buyers, this is a point I always emphasize. The integrity of the entire assembly depends on the quality of the crimp and the design of the fitting connection. A cheap, poorly plated fitting will rust, and a poor sealing design will leak.
Why Standard Fittings Can Fail
Many common fittings, like JIC 37° Flare, create a metal-to-metal seal. While very reliable in many applications, under extreme vibration and impulse, this metal-to-metal contact can be susceptible to “fretting” and loosening over time. Tapered thread fittings like NPT should never be used in high-pressure hydraulic lines on mobile equipment.
The Case for High-Performance Fittings
To combat these forces, you need a superior sealing design.
- O-Ring Face Seal (ORFS – ISO 8434-3): This is often the best choice. The seal is made by a soft O-ring compressed between two flat faces. The threads are only for clamping force, not sealing. This design is extremely resistant to vibration and provides a zero-leak connection, making it ideal for mining.
- DIN Bite-Type (ISO 8434-1): This is a very popular and robust standard we supply to clients across Asia and Europe. A hardened ferrule or “cutting ring” bites into the steel tube, creating a powerful mechanical grip that is also highly resistant to vibration and pressure.
The Critical Importance of the Crimp
Finally, the fitting must be crimped onto the hose correctly using the manufacturer’s specified dies and crimp diameter. An incorrect crimp, even by a millimeter, can lead to the fitting blowing off under pressure. As a supplier, we provide our customers with complete, factory-crimped assemblies or the precise crimp specifications to ensure a safe and reliable connection is made every time.
How Do You Specify a Complete, Impact-Ready Hose Assembly?
You understand the individual components, but how do you put it all together in a clear specification for a supplier? You need to ensure you get a complete solution that is built to survive your specific mining challenge, with no weak links.
You must specify the system, not just the parts. This means defining the requirements for the hose core, the cover, the external guarding, and the fittings as a single, engineered assembly designed to combat pressure, impulse, abrasion, and impact simultaneously.
This is how we help our most successful clients. They don’t just send a part number; they describe the problem. We then work with them to build the perfect “recipe” for a hose assembly that will last.
Step 1: Identify Pressure and Impulse
First, define the system’s maximum working pressure and the nature of the application. Is it a high-impulse hammer line or a steady-pressure return line? This determines the hose standard (e.g., R15 for the hammer, maybe R12 for a boom lift).
Step 2: Assess the External Threat Level
Next, honestly assess the external environment. Rate the abrasion and impact risk from 1 to 10. A score of 7 or higher in either category means a tough cover is mandatory. A score of 7 or higher in impact means an external guard is mandatory.
Step 3: Build Your System Specification
With this information, you can build a clear specification. Here is a clear comparison.
Component | Standard Hydraulic Application | High-Impact Mining Application |
Hose Core | SAE 100R2 (Braided) | SAE 100R15 (Six-Spiral) |
Hose Cover | Standard Rubber | Super Abrasion “Tough” Cover |
Protection | None | HDPE Plastic Spiral Guard |
Fittings | JIC or BSPP | ORFS or DIN Bite-Type |
When you send a request for quotation to a knowledgeable supplier like Topa with this level of detail, it shows you are a professional who understands the challenge. It allows us to quote you the exact, correct solution that will provide the lowest total cost of ownership by maximizing uptime.