Ball valve specification refers to the set of criteria and characteristics that define a valve’s performance and suitability for a specific application. These specifications include factors such as valve size, pressure rating, material composition, and temperature tolerance. Properly understanding these elements ensures that the ball valve can handle the demands of the system, preventing issues like leaks, poor flow control, and premature wear.
Understanding Different Ball Valve Types
Choosing the right ball valve type is critical for ensuring optimal system performance. Ball valves come in various designs, each suited for different applications and operating conditions.
Floating Ball Valves vs. Trunnion Ball Valves
Floating ball valves and trunnion ball valves are both widely used in industrial applications, but they differ in their design and how they handle pressure.
Floating Ball Valves: In floating ball valves, the ball “floats” between two seats, and its position is determined by the pressure from the pipeline. These valves are ideal for lower-pressure applications, typically in systems with up to 3000 psi. Floating ball valves are relatively simple and cost-effective, making them a popular choice for many standard fluid control systems.
Trunnion Ball Valves: Trunnion ball valves have a fixed ball that is supported by trunnions or bearings at the top and bottom. This design reduces the stress on the ball and makes it more suitable for higher pressure and larger valve sizes. Trunnion ball valves are commonly used in high-pressure and high-flow systems, such as oil and gas pipelines, where valve integrity is critical.
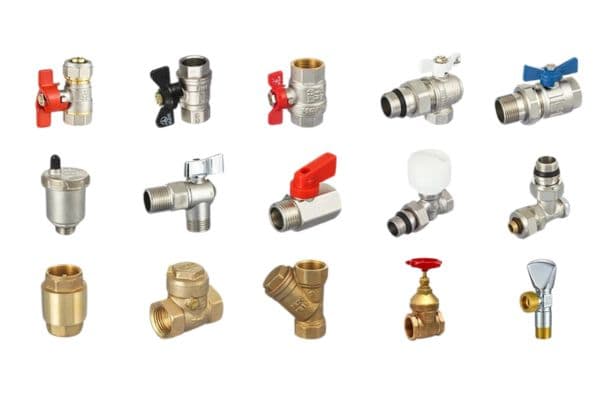
Full-Bore vs. Reduced-Bore Ball Valves: What’s the Difference?
The primary difference between full-bore and reduced-bore ball valves lies in the internal diameter of the valve compared to the pipe it is connected to.
Full-Bore Ball Valves: A full-bore ball valve has an internal diameter equal to the pipeline diameter, providing unrestricted flow. These valves are typically used in systems where maintaining the full flow capacity is crucial, such as in pipelines for liquids and gases where minimal pressure loss and maximum flow are required.
Reduced-Bore Ball Valves: Reduced-bore ball valves have a smaller internal diameter than the pipeline, which can result in some flow restriction. These valves are often more cost-effective and are used in systems where flow capacity is less critical, but where space or cost considerations are a concern. They are commonly found in smaller industrial applications or systems where full flow is not necessary.
Common Ball Valve Types and Their Applications
Ball valves come in several other types, each designed to meet the needs of specific applications. Here are some of the most commonly used ball valve types and their typical uses:
2-Way Ball Valves: These valves allow fluid to flow in one direction, either open or closed. They are commonly used in simple on/off applications, such as controlling the flow of water in residential plumbing systems or regulating gas in industrial lines.
3-Way Ball Valves: A 3-way ball valve can direct flow in three different directions. These are commonly used for mixing or diverting applications, such as controlling the flow of fluids in HVAC systems or complex chemical processing plants.
V-Port Ball Valves: V-port ball valves have a “V” shaped ball that allows for more precise flow control, particularly in throttling applications. These valves are ideal for regulating flow in systems like steam control, water treatment, and chemical dosing.
Multi-Port Ball Valves: These valves feature multiple ports to allow fluid flow through different passages, typically used in complex systems requiring control in multiple directions or for combining fluids from different sources. Multi-port ball valves are often seen in large-scale industrial systems, such as refineries and power plants.
Key Ball Valve Components
When choosing a ball valve, it’s essential to understand the different components that contribute to its performance, reliability, and longevity. Each part plays a specific role in ensuring the valve operates efficiently under various conditions.
Valve Seat
The valve seat is a crucial component of the ball valve as it directly influences the sealing effectiveness and performance. The seat provides a tight seal around the ball when the valve is in the closed position, preventing leaks and ensuring fluid is effectively contained within the pipeline.
Material Considerations: Valve seats can be made from a variety of materials, including elastomers (such as Viton or EPDM), PTFE (Teflon), and metal alloys. The choice of material depends on factors like temperature, pressure, and the type of fluid being controlled. For example, PTFE seats are highly resistant to chemicals and are ideal for corrosive environments, while elastomeric seats provide excellent sealing at lower pressures.
Types of Valve Seats: There are two main types of seats:
Soft Seats: Made of materials like PTFE or elastomers, these are used for sealing in lower pressure applications and provide a softer, more flexible seal.
Metal Seats: Typically used in higher pressure and high-temperature applications, these seats provide a more durable seal under harsh conditions but may require more maintenance.
Impact on Performance: The performance of a valve seat is directly linked to how effectively it seals the valve. A poor-quality seat can lead to leakage, reduced system efficiency, and even valve failure. When selecting a valve, ensure the seat material and design are compatible with the fluid properties and operational conditions of your system.
Valve Stem and Stem Packing
The valve stem and stem packing play a critical role in the operation and sealing of a ball valve. The stem connects the valve’s actuator (manual or automated) to the ball, allowing the valve to open and close. The stem packing ensures that the valve stem is tightly sealed, preventing fluid leakage around the stem during operation.
Stem Functionality: The valve stem is responsible for transmitting the rotational motion from the actuator (or manual handle) to the ball. It must be durable and able to handle the forces exerted during valve operation. In addition to providing the mechanical connection, the stem must also maintain a tight seal to prevent fluid from leaking through the stem area.
Stem Packing Materials: The stem packing is typically made from soft materials like PTFE, graphite, or elastomer compounds, depending on the pressure, temperature, and fluid in the system. These materials provide the necessary sealing without causing excessive wear on the stem. For higher pressure systems, more robust packing materials are often required.
Maintenance and Performance: Over time, stem packing can wear out, especially in high-cycle applications. Regular inspection and replacement of the packing are necessary to maintain a tight seal and prevent leakage around the stem. When choosing a ball valve, ensure that the stem packing is compatible with the operating conditions of the system and offers the necessary sealing performance.
Valve Body
The valve body is the main structure of the ball valve, housing the ball, seat, and stem. Its design and material selection are critical to the valve’s overall performance, durability, and resistance to corrosion, especially in harsh operating environments.
Design Considerations: Ball valve bodies come in various designs, including:
Two-Piece Body: The body is split into two parts that are bolted together, allowing easy access for maintenance or replacement of internal components.
Three-Piece Body: This design features three sections, with the middle section being removable for easy service and cleaning. This design is ideal for applications where frequent maintenance is required.
Forged Body: A one-piece forged design provides added strength and resistance to high pressure, making it suitable for high-pressure applications.
Material Choices: The material of the valve body determines its strength, corrosion resistance, and suitability for certain fluids. Common materials include:
Stainless Steel: Known for its durability, corrosion resistance, and versatility, stainless steel is commonly used for industrial and chemical applications.
Carbon Steel: Often used in lower-cost applications, carbon steel is strong and durable, but it is less resistant to corrosion than stainless steel.
Brass and Bronze: These materials are typically used for smaller valves in lower-pressure applications, such as residential plumbing or HVAC systems.
Impact on Valve Performance: The body material should be chosen based on the fluid’s temperature, pressure, and corrosiveness. A poor material choice can lead to premature wear, corrosion, and failure of the valve body. It’s essential to match the body material with the operating conditions to ensure optimal performance and longevity.
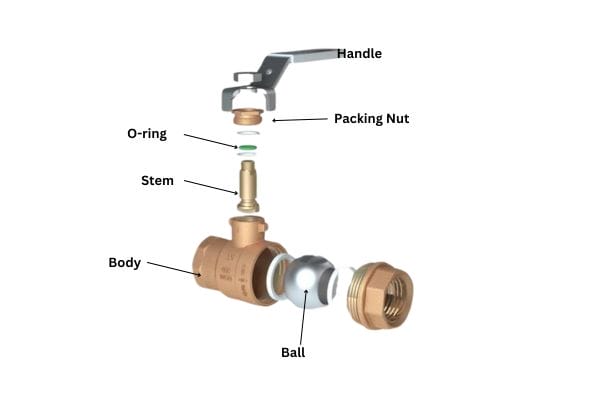
Valve Actuators
The actuator is the mechanism that operates the ball valve, either manually or automatically. The type of actuator selected depends on the application and the level of control required for the system. Understanding the differences between manual and automated actuators will help you select the best option for your system.
Manual Actuators: These actuators are typically operated by a handle or lever that allows the operator to manually turn the ball to open or close the valve. Manual actuators are simple, cost-effective, and ideal for small-scale systems or where limited operation is required. They provide direct control over the valve and are commonly used in low-pressure or non-critical applications.
Automated Actuators: Automated actuators are powered by either electricity, pneumatic pressure, or hydraulics and allow for remote or automatic control of the ball valve. These actuators are ideal for high-volume, high-precision applications, as they can be integrated with control systems for precise, real-time valve management. Automated actuators offer advantages such as:
Increased Safety: Automated control eliminates the need for manual intervention in hazardous environments.
Remote Operation: Automated actuators can be controlled from a distance, making them ideal for large-scale or hard-to-access systems.
Increased Efficiency: Automated valves can be programmed to open, close, or throttle based on specific conditions or system requirements, improving operational efficiency.
Choosing the Right Actuator: When selecting an actuator, consider factors such as the size of the valve, required response time, operating environment, and control system integration. Automated actuators tend to be more expensive but are necessary for large-scale or high-precision applications, whereas manual actuators are sufficient for simpler systems.
Determining the Right Ball Valve Size
Choosing the right ball valve size is essential for ensuring optimal flow control, reducing energy consumption, and preventing system issues. If a ball valve is too small, it may cause flow restrictions and increased pressure loss; if it’s too large, it could result in inefficient operation and higher costs.
How to Calculate the Correct Valve Size for Your System
Determining the right ball valve size involves several key calculations and considerations. The following steps will guide you through the process:
Determine the Flow Rate: The flow rate is the amount of fluid (liquid or gas) passing through the system per unit of time, usually measured in gallons per minute (GPM) or liters per second (L/s). It is essential to know the flow rate to ensure the valve is sized to allow adequate fluid passage without causing restrictions.
Consider the Pipe Diameter: The diameter of the pipe in your system plays a direct role in selecting the correct valve size. The ball valve size should typically match or slightly exceed the pipe diameter to avoid creating bottlenecks. For example, if you have a 2-inch pipe, the valve should generally be a 2-inch ball valve.
Account for Pressure Loss: Pressure loss can occur when the valve restricts flow, which is more common with undersized valves. When sizing the valve, you need to consider the acceptable pressure loss in the system to avoid damaging equipment or decreasing performance. For high-pressure systems, calculating the valve’s pressure drop under normal operating conditions is essential.
Use Valve Sizing Equations: Valve manufacturers often provide sizing charts and equations that factor in the flow rate, pipe diameter, and system pressure. These tools help to determine the optimal valve size based on the system’s specific requirements. You can also use the Cv (flow coefficient), which represents the flow capacity of the valve. The formula for calculating the required valve size is often based on the Cv value and flow rate.
The Role of Pipe Size and Flow Rate in Valve Sizing
Both pipe size and flow rate play crucial roles in determining the correct ball valve size:
Pipe Size: As the pipe size increases, so does the flow capacity. If the ball valve size is too small relative to the pipe, the valve will restrict flow and cause a significant pressure drop, leading to inefficient operation. On the other hand, if the valve is too large, it can be costly and lead to unnecessary space usage. The general rule is to match the valve size to the pipe size or use a slightly larger valve to accommodate future flow increases.
Flow Rate: The flow rate is directly related to how much fluid will pass through the valve. If the valve is undersized for the required flow rate, it will cause the fluid to pass through too quickly, creating turbulence and potential cavitation or erosion. On the other hand, an oversized valve will reduce flow velocity, causing inefficiency in systems that require precise flow control. The valve size should be selected to ensure the flow rate is handled smoothly without excessive pressure loss or flow restriction.
Common Sizing Mistakes and How to Avoid Them
Choosing the wrong size for your ball valve can lead to several operational issues. Below are some common mistakes made during valve sizing and how to avoid them:
Oversizing the Valve While it may seem like a larger valve would be better, oversizing a ball valve can result in:
Increased upfront costs.
Inefficient operation and potential system damage.
A slower response time in flow control applications.
How to Avoid: Carefully consider the system’s flow rate, pressure, and future expansion needs. Don’t just opt for the largest valve available.
Undersizing the Valve Undersizing the valve can lead to:
Increased pressure drop and flow resistance.
Potential for cavitation and valve failure.
Reduced overall system efficiency.
How to Avoid: Ensure you account for the maximum flow rate and pressure conditions your system will experience, and use appropriate sizing tools or manufacturer recommendations to match the valve to the system’s needs.
Ignoring Pressure and Temperature Variables Not considering the operating pressure or temperature can result in selecting a valve that cannot handle the system’s demands, potentially leading to failure.
How to Avoid: Always account for both pressure and temperature when sizing a valve, particularly in high-pressure or extreme temperature applications, as these conditions will affect the valve’s flow capacity and durability.
Failing to Account for Future Growth If you anticipate increased flow requirements in the future, choosing a valve that only meets current needs can result in having to replace the valve prematurely.
How to Avoid: Consider potential changes in system capacity and allow room for future expansion when selecting the valve size.
Not Consulting Manufacturer Sizing Guides Different manufacturers may use varying specifications and methods for valve sizing, and neglecting to consult these guidelines can result in improper selection.
How to Avoid: Always consult the manufacturer’s sizing charts and use their recommendations to ensure accurate sizing based on your system’s specific requirements.
Valve Pressure Rating: Choosing the Right Rating for Your Needs
Selecting the correct valve pressure rating is a critical factor in ensuring that your ball valve operates effectively and safely within your system. The pressure rating determines the maximum pressure the valve can withstand during operation without compromising its integrity.
Understanding Valve Pressure Ratings and Their Impact on System Performance
Valve pressure ratings indicate the maximum internal pressure that a valve can handle without risking damage, leakage, or failure. These ratings are typically specified in pounds per square inch (PSI) or bar, and they reflect the valve’s ability to withstand internal pressures during normal operation, as well as during pressure surges or fluctuations.
The pressure rating is determined by several factors:
Material Strength: The material used in the valve body, seats, and other components affects its ability to withstand pressure. For example, stainless steel valves tend to have higher pressure ratings compared to plastic or brass valves.
Design and Construction: The valve’s design—such as the thickness of the valve body, the structure of the valve stem, and the type of seals used—contributes to its pressure tolerance.
Valve Type: Different types of valves (e.g., floating ball vs. trunnion ball) are rated for different pressures. Trunnion ball valves, for example, tend to handle higher pressures better than floating ball valves due to their structural support.
The right pressure rating ensures that the valve will operate safely without failing, preventing costly downtime, equipment damage, or even safety hazards. It’s essential that the pressure rating is matched to the system’s operational and surge pressures.
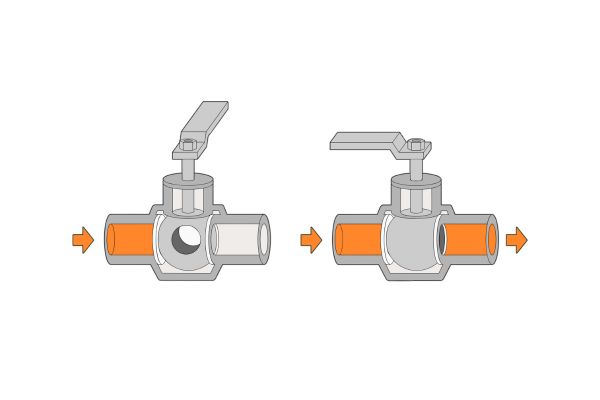
How to Match Pressure Ratings with Operating Conditions
To ensure your ball valve functions correctly, it’s crucial to match its pressure rating with your system’s operating conditions. Here’s how you can do this:
Assess Operating Pressure: The operating pressure is the normal pressure the fluid or gas will experience during system operation. This should be carefully calculated based on the pressure within the pipeline at the valve’s location. It’s also essential to account for pressure fluctuations, which can occur during system startup, shutdown, or in response to changes in flow rate.
Consider Pressure Surges and Peaks: In many systems, pressure can spike above the normal operating pressure, especially during start-up or shut-down sequences. This is known as water hammer or pressure surge. When selecting a valve, make sure it can withstand these spikes. A valve with a higher pressure rating may be necessary to prevent failure during these unpredictable events.
Evaluate Fluid Characteristics: Different fluids, whether they are gases, liquids, or slurries, exert different pressures on the system. For example, gases can expand and create pressure fluctuations, while liquids may create a more constant pressure. For highly corrosive or abrasive fluids, a higher pressure rating may be needed to ensure the valve withstands these aggressive conditions without compromising safety.
Temperature Considerations: The temperature of the fluid affects the pressure rating of the valve. As temperature increases, the pressure capacity of many materials decreases. It’s essential to verify the valve’s temperature rating to ensure it’s compatible with your system’s operating temperatures. If your system operates at high temperatures, you may need to select a valve rated for higher pressures or a material that can withstand both high pressure and temperature.
Standards Compliance: Many industries follow established standards that specify pressure ratings for different types of valves. These standards help ensure that valves are selected according to recognized safety and performance criteria.
High Pressure vs. Low Pressure Ball Valves
When selecting a ball valve, it’s crucial to determine whether you need a high-pressure or low-pressure valve. The difference between these two types lies in the maximum pressure they can handle and their typical applications.
High Pressure Ball Valves: High-pressure ball valves are typically rated for pressures above 1500 PSI (100 bar) and are designed for applications where the fluid or gas is under significant pressure. These valves are commonly used in industries such as:
Oil and gas: For managing high-pressure pipelines.
Chemical processing: In systems where pressurized chemicals need to be controlled.
Power plants: In steam and gas systems under high pressure.
High-pressure valves are often constructed with thicker bodies and stronger materials like stainless steel to withstand the stresses of high-pressure environments. They may also feature specialized sealing systems to ensure leak-tight operation under extreme conditions.
Low Pressure Ball Valves: Low-pressure ball valves are typically rated for pressures less than 1500 PSI and are often used in systems with lower fluid or gas pressures. These valves are found in applications such as:
Water treatment plants: Where pressures are moderate.
HVAC systems: For controlling airflow or fluid flow at lower pressures.
Food and beverage processing: Where relatively low-pressure systems are common.
Low-pressure valves tend to be less robust than high-pressure valves, making them lighter, more cost-effective, and easier to maintain. However, they still need to be selected carefully to ensure they match the pressure conditions of the system.
Key Differences:
Material: High-pressure valves often use stronger, more durable materials like carbon steel or stainless steel, while low-pressure valves may use lighter materials like brass or PVC.
Design: High-pressure valves tend to have thicker bodies, reinforced seals, and other design features that allow them to handle significant stress. Low-pressure valves have simpler designs.
Cost: High-pressure ball valves are typically more expensive due to the materials, design, and testing involved.
Valve Standards and Certifications
Valve standards and certifications are essential for ensuring that ball valves meet industry-specific quality, safety, and performance requirements. Adhering to these standards helps manufacturers and end-users select valves that are reliable and safe for use in various applications.
Key Industry Standards: API, ANSI, and More
Several industry standards help define ball valves’ quality, design, and operational limits. These standards ensure that valves perform reliably, meet safety requirements, and are suitable for specific applications. Some of the most important standards include:
API (American Petroleum Institute): API standards are critical for the oil and gas industry. API 6D, for example, sets the specifications for pipeline ball valves, ensuring they meet the required safety, durability, and operational performance standards. API standards cover the design, testing, and material specifications to ensure the valves can handle the extreme pressures, temperatures, and corrosive environments typical in the oil and gas sector.
ANSI (American National Standards Institute): ANSI standards, particularly ANSI/ASME B16.34, set the requirements for valves used in industrial piping systems. ANSI standards provide guidelines for valve pressure classes, materials, and design specifications, ensuring that the valves are suitable for a wide range of industries, from chemical processing to power generation.
ISO (International Organization for Standardization): ISO standards are globally recognized and cover a broad range of valve types and applications. ISO 9001 focuses on quality management systems, ensuring manufacturers maintain high standards for product consistency. ISO 5211, for instance, provides guidelines for valve actuators, helping manufacturers and end-users select compatible valve-actuator combinations for optimal performance.
BS (British Standards): The British Standards Institution (BSI) provides standards for valve designs and testing procedures to ensure valves can withstand the demanding conditions of the UK market. One notable standard is BS 5351, which addresses the design and construction of ball valves.
DIN (Deutsches Institut für Normung): The German standards organization, DIN, provides specific standards for valves used in industrial applications across Europe. DIN 3357 governs the design and performance of ball valves, ensuring they are suitable for use in the chemical, food, and pharmaceutical industries.
How Valve Certification Ensures Quality and Safety
Valve certification is the process by which manufacturers prove that their products meet established standards for quality, safety, and performance. Certification is often required to demonstrate that a valve can safely and effectively operate within its specified parameters. Here’s how valve certification helps ensure quality and safety:
Consistency and Reliability: Certified valves are produced to meet consistent quality standards, ensuring that they perform reliably over time. Manufacturers must adhere to strict production processes and quality control measures to achieve certification, which guarantees that each valve meets or exceeds industry standards for performance and durability.
Material Integrity: Certification ensures that the materials used in valve construction—whether stainless steel, brass, carbon steel, or others—are of the correct grade and strength to withstand the system’s operating pressures, temperatures, and fluids. This helps prevent premature failure or material degradation, which can lead to leaks or hazardous conditions.
Design Compliance: Certified valves must adhere to design specifications set by regulatory bodies (like ANSI, API, and ISO), ensuring that they are structurally sound and capable of handling the intended fluid flow, pressure, and operating conditions. This minimizes the risk of malfunction and extends the service life of the valve.
Testing and Performance Validation: During the certification process, valves undergo rigorous testing—such as pressure tests, leakage tests, and performance tests—to validate their suitability for various applications. This ensures that the valve operates correctly within its pressure and temperature limits, offering peace of mind to operators and users.
Regulatory Compliance: In many industries, using certified valves is not just a best practice; it’s a legal requirement. Regulatory bodies like the Occupational Safety and Health Administration (OSHA), the American Society of Mechanical Engineers (ASME), and the Environmental Protection Agency (EPA) mandate the use of certified components to ensure worker safety, environmental protection, and system reliability.
Conclusion
By carefully selecting and maintaining your ball valve, you can ensure reliable operation and long-lasting performance, ultimately improving system efficiency and driving long-term cost savings.
FAQ
What is a ball valve used for?
A ball valve is used to control the flow of liquids or gases in a piping system. It has a spherical ball with a hole through the middle that can rotate to either allow or stop the flow.
How do I know what size ball valve I need?
To select the right size ball valve, consider the pipe diameter, flow rate, and pressure requirements of your system. Valve sizing charts and manufacturer guidelines can help ensure you choose the correct size for optimal performance.
What is the difference between a floating and a trunnion ball valve?
A floating ball valve has a ball that “floats” and is moved by the fluid pressure, while a trunnion ball valve has a ball that is fixed in place by trunnions (supports) at the top and bottom, making it more suitable for higher pressure applications.
What materials are used in making ball valves?
Common materials for ball valves include stainless steel, brass, carbon steel, and PVC. The material choice depends on factors like pressure, temperature, and the type of fluid being handled.
What is the pressure rating of a ball valve?
The pressure rating of a ball valve indicates the maximum pressure the valve can safely handle without failure. It is important to match the valve’s pressure rating with the operating conditions of your system to prevent damage or leaks.
Why is valve certification important?
Valve certification ensures that the valve meets industry standards for quality, safety, and performance. Certified valves are more reliable, meet regulatory requirements, and are less likely to fail under critical conditions.