When it comes to plumbing, choosing the right type of pipe connection can make all the difference in terms of durability, leak prevention, and ease of installation. Two of the most commonly used fittings in plumbing systems are compression fittings and pipe unions. While both are essential for connecting pipes, they serve different purposes and come with their own set of advantages and challenges.
What Are Compression Fittings?
Definition and Purpose of Compression Fittings
Compression fittings are a type of plumbing connection used to join two pieces of pipe or tubing without the need for welding or soldering. The primary function of compression fittings is to create a tight, leak-proof seal between pipes, ensuring that water, gas, or other fluids flow through the system without escaping. They are designed for use in both residential and commercial plumbing systems and can be used in a variety of materials, including copper, brass, steel, and plastic.
What makes compression fittings unique is their ability to provide a strong seal through the compression of a ferrule (or ring) around the pipe. This creates a pressure-tight connection that holds securely, making compression fittings a popular choice for installations where a permanent or semi-permanent connection is needed.
Common Applications of Compression Fittings in Plumbing
Compression fittings are used in a wide range of plumbing applications, including:
Pipe repairs: Compression fittings are ideal for repairing damaged or leaking pipes without the need for cutting or replacing entire sections of pipe.
Connecting fixtures and appliances: They are commonly used for connecting water supply lines to faucets, toilets, dishwashers, and other household appliances.
Water, gas, and heating systems: Compression fittings are used in a variety of systems, from water supply to heating, where a secure and leak-proof connection is critical.
Tight spaces: Since compression fittings do not require any welding or soldering, they are often used in areas with limited access, where other connection methods may not be feasible.
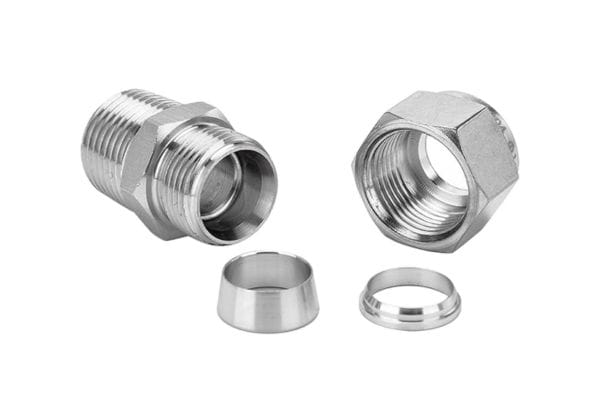
The Anatomy of a Compression Fitting
A typical compression fitting consists of several key components:
Nut: The nut is the outermost part of the compression fitting and is used to tighten the connection.
Ferrule (or compression ring): The ferrule is placed around the pipe and is compressed by the nut. As the nut tightens, the ferrule creates a tight seal around the pipe, preventing leaks.
Body or Fitting: The body of the compression fitting is the central component that connects to the pipe. It is typically made of brass or stainless steel and contains a threaded opening for the nut to be attached.
Seal: The seal is created by the compression of the ferrule around the pipe, ensuring that the connection is watertight or airtight.
What Are Pipe Unions?
Definition and Purpose of Pipe Unions
Pipe unions are specialized fittings used to connect two sections of pipe while allowing for easy disassembly and reassembly. Unlike other fittings, unions are designed with a simple mechanism that enables quick removal and reconnection of pipes, making them ideal for systems that require regular maintenance, repair, or modification. They consist of three main parts: a body, a nut, and a ring (or face), all of which work together to provide a secure, leak-proof connection.
Unions are particularly useful in situations where frequent disassembly is required, or where a pipe may need to be replaced or modified without affecting the rest of the system. They are widely used in both residential and commercial plumbing and can be found in applications such as water and gas systems, heating systems, and even in industrial environments.
Key Features of Pipe Unions and How They Differ from Other Fittings
Easy Disassembly: One of the main advantages of pipe unions is their ability to be easily disconnected and reconnected. This makes unions ideal for systems where parts need to be replaced, repaired, or maintained regularly.
Versatility in Pipe Sizes: Unions can accommodate a range of pipe sizes, and they can be used with different types of piping materials, including copper, PVC, steel, and brass.
Reliable Seal: Like compression fittings, pipe unions are designed to create a leak-proof seal between connected pipes. This ensures that fluids or gases can flow safely through the system.
Compared to Other Fittings: Unlike compression fittings, which use a ferrule to create a seal, unions have a nut and a ring that fit together to allow for a secure connection. While compression fittings are typically permanent or semi-permanent, unions are more suitable for systems that require flexibility and disassembly.
When and Where Unions Are Typically Used in Plumbing Systems
Pipe unions are commonly used in plumbing systems that require:
Frequent maintenance: Since they allow for easy disconnection, unions are ideal for systems that need to be accessed for repair or inspection, such as water heaters or filtration systems.
Pipes subject to wear and tear: In situations where pipes may need to be replaced or swapped out frequently, unions are a convenient option.
Industrial applications: Unions are often used in industrial and commercial settings where heavy-duty systems require flexible and secure connections for pipes that carry gases, chemicals, or water.
Large-scale installations: Unions are typically used in larger plumbing systems where sections of pipe may need to be reworked or adjusted without dismantling the entire setup.

Compression Fitting vs Union: Key Differences Explained
Physical Differences Between Compression Fittings and Unions
While compression fittings and pipe unions both serve the purpose of connecting two sections of pipe, their designs and structures are quite different:
Compression Fittings: These fittings consist of a nut, a compression ring (ferrule), and a body. The nut tightens around the ferrule, which then compresses against the pipe, creating a tight, leak-proof seal. The fitting itself is relatively small, and its components fit closely around the pipe.
Pipe Unions: Unions, on the other hand, are larger and consist of three main components: a body, a nut, and a face or ring. The nut screws onto the body and connects the two halves of the union to the pipe. Unions are designed to provide easy disassembly and are often bulkier than compression fittings because they need to accommodate for the joint that allows them to be unscrewed.
Comparison of Their Working Mechanisms
Compression Fittings: The primary mechanism behind compression fittings is the compression of the ferrule (ring) against the pipe. When the nut is tightened, it compresses the ferrule against the pipe, forming a seal. This method does not rely on threads (except for the connection of the nut) and is often used in smaller pipe systems or when space is tight.
Pipe Unions: Unions rely on threaded components to secure the two sections of pipe. The nut and the face ring are designed to create a leak-proof connection, but unlike compression fittings, unions have a quick-connect/disconnect feature that allows for easy removal of the connected pipes. Unions are ideal for situations where disassembly is needed frequently, such as in systems that require maintenance or repairs.
How Compression Fittings Work: The Sealing Mechanism
Step-by-Step Explanation
Compression fittings create a leak-proof seal by compressing a ferrule (or compression ring) around the pipe, using pressure to form a tight connection. Here’s how the sealing process works:
Placement of the Compression Ring: The compression ring is placed on the pipe before the fitting is screwed on.
Tightening the Nut: When the nut is tightened around the fitting, the compression ring is forced against the pipe, applying inward pressure.
Compression of the Ring: As the nut tightens, the ferrule compresses around the pipe, sealing the connection. The compression creates a strong, watertight or airtight barrier.
Fitting Against the Pipe: The fitting itself does not move; rather, the seal is achieved by the compression ring creating friction between the pipe and the fitting. This ensures that there are no gaps where water, gas, or other fluids can leak through.
The Role of the Compression Ring and Nut in Securing the Fitting
The compression ring (ferrule) is the key to the leak-proof seal. The ring is made of a soft material, such as brass, that deforms slightly as the nut is tightened. This deformation helps create a tight fit against the pipe, preventing any leakage. The nut applies pressure to the ferrule, pushing it into the pipe and causing the compression. The tightness of the nut determines the effectiveness of the seal, which is why proper installation is essential.
Pipe Material Compatibility for Compression Fittings
Compression fittings are versatile and can be used with a wide range of materials, including:
Copper Pipes: One of the most common applications for compression fittings, as they offer a strong and secure connection without the need for soldering.
Brass Pipes: Brass is durable and resistant to corrosion, making it ideal for compression fittings in both plumbing and gas systems.
Plastic Pipes (e.g., PVC, PEX): Compression fittings can also be used with certain plastic pipes, though the type of compression fitting must match the material.
Steel Pipes: Stainless steel compression fittings are commonly used for industrial plumbing systems, where strength and corrosion resistance are crucial.
How Pipe Unions Work: A Simple Breakdown
The Design and Function of a Pipe Union
A pipe union consists of three main components:
Body: The central piece that attaches to the pipe. It has internal threads for securing the pipe.
Nut: The nut screws onto the body, creating a tight connection.
Face or Ring: This part of the union is designed to form a seal between the two pipe sections, ensuring that the union connection is leak-proof.
Unions work by threading these three components together, holding the pipes in place securely. When the nut is tightened, the two ends of the union are joined tightly, allowing fluid to flow through without leakage. The ability to easily disconnect and reconnect the pipes makes unions versatile and ideal for systems requiring regular maintenance or adjustments.
How Unions Create Easy-to-Assemble and Disassemble Connections
The main advantage of unions over compression fittings is their ability to allow for quick disassembly. Unlike compression fittings, which are designed to be a more permanent connection, unions can be unscrewed without damaging the pipes, making them perfect for:
Repair and maintenance: When pipes need to be replaced or worked on regularly, unions allow for quick removal and reconnection.
Flexibility in pipe layout: Since unions can be unscrewed easily, they give plumbers more flexibility when adjusting or reconfiguring piping systems.
Union Sealing Mechanisms and Their Reliability
The sealing mechanism in a pipe union relies on the connection between the union body and the face ring. As the nut is tightened, the face ring is pressed against the pipe, creating a strong seal. The reliability of the seal is typically enhanced by the use of rubber gaskets or O-rings in the union’s design. These gaskets help prevent leaks by filling any small gaps between the metal parts of the union and the pipe. Unions are designed to be just as reliable as compression fittings when installed correctly, ensuring that water, gas, or other fluids flow without issue.
Common Problems with Compression Fittings and Unions
When using compression fittings and pipe unions, some common issues may arise during installation or over time due to wear and tear. Understanding these problems will help you troubleshoot effectively and maintain a leak-free plumbing system. Here’s an overview of the most frequent issues associated with each fitting type, along with solutions to resolve them.
Frequent Issues with Compression Fittings
Leaks at the Connection
Cause: One of the most common issues with compression fittings is leakage at the connection point. This is usually due to an improper seal created by a loose or incorrectly tightened nut or a damaged compression ring.
Solution: Ensure that the compression fitting is tightened properly. The nut should be turned until it feels firm, but avoid overtightening, which can damage the ferrule. If leaks persist, check the compression ring (ferrule) for damage, and replace it if necessary. Also, confirm that the pipe is clean and free of burrs or damage that could affect the seal.
Over-tightening the Nut
Cause: Over-tightening the compression nut can cause damage to the pipe or compression ring, potentially leading to cracks or deformities that prevent a proper seal.
Solution: Always use a wrench to tighten the nut until it’s snug, but avoid applying excessive force. Use the right-sized fitting for your pipe to ensure a proper fit, and check for signs of stress or damage to the parts before installation.
Deformed Compression Ring (Ferrule)
Cause: The ferrule can become deformed or damaged, especially if it’s installed incorrectly or reused. A deformed ferrule will not create a tight seal, leading to leaks.
Solution:Replace the ferrule if it’s damaged or deformed. Always use a new ferrule when reinstalling or making adjustments to the compression fitting. Additionally, ensure the ferrule is properly aligned with the pipe during installation to avoid deformation.
Incorrect Pipe Size or Material
Cause: Compression fittings are designed for specific pipe sizes and materials. Using the wrong combination can cause leaks or poor performance, as the fitting won’t create an adequate seal.
Solution: Double-check that the compression fitting matches the size and material of your pipe. For example, using a brass compression fitting on copper pipes is common, but a plastic compression fitting may not work on metal pipes.
Fittings Becoming Loose Over Time
Cause: Over time, vibrations, pressure changes, or temperature fluctuations can cause the compression fitting to loosen, resulting in leaks.
Solution: Periodically check and retighten compression fittings. If the fitting continues to loosen, consider replacing the fitting with a more robust one or using additional sealing measures like thread sealant to prevent further loosening.

Problems That Can Occur with Pipe Unions
Gasket or O-ring Failure
Cause: Pipe unions rely on gaskets or O-rings to provide a watertight seal. If these seals become damaged or worn, they can lead to leaks at the union joint.
Solution: If you notice water around the union, check the gasket or O-ring for cracks or wear. Replace the damaged gasket or O-ring with a new one that matches the size and material of the union. Regularly inspect these components to ensure they are intact and properly seated.
Corrosion and Rusting
Cause: Unions, especially those made from metal, can be susceptible to corrosion or rusting, particularly in high-moisture environments or systems with poor water quality.
Solution: Inspect unions regularly for signs of corrosion, particularly at the nut and body. If corrosion is present, replace the union. To prevent corrosion, use corrosion-resistant materials (such as stainless steel unions) or apply a protective coating to prevent rust from forming.
Leaks Due to Improper Tightening
Cause: If the union nut is not properly tightened, or if it’s overtightened, it can lead to leaks at the connection, as the seal between the union body and the pipe face is not secure.
Solution: Ensure that the union nut is tightened to the correct torque. Tighten the nut snugly but not excessively. If the nut is overtightened, it could damage the sealing components. If it’s too loose, it will fail to create a proper seal.
Misalignment of Union Components
Cause: Sometimes, if the components of the union (nut, body, and face) are misaligned or improperly assembled, it can cause an imperfect seal, leading to leaks.
Solution: Carefully check the alignment of the union parts. Ensure the nut is properly threaded, the union body is secure, and the face is aligned to meet the pipe properly. Any misalignment could cause uneven pressure and lead to leaks.
Thread Damage
Cause: Union threads can become worn or damaged from repeated assembly and disassembly or from the union being improperly handled during installation.
Solution: Inspect the threads on the union body and nut for any signs of damage or wear. If the threads are compromised, replace the union with a new one to ensure the integrity of the connection. Additionally, use thread sealant to prevent damage from corrosion and wear.
How to Troubleshoot and Fix These Issues for Both Types
For Compression Fittings:
Check for Leaks: Inspect the fitting for leaks, especially around the nut and ferrule. If leaks are detected, check for a properly aligned ferrule, tightened nut, and clean pipe ends. If necessary, replace the ferrule and retighten the fitting.
Avoid Over-tightening: Use the appropriate tool to tighten the fitting just enough to create a secure connection. Over-tightening can damage the ferrule and pipe, causing leaks.
Inspect for Deformation: If the ferrule is deformed, replace it with a new one. Always ensure the fitting and pipe size match before installation.
For Pipe Unions:
Inspect Gaskets and O-rings: If leaking occurs, remove the union and check the gasket or O-ring for wear. Replace damaged components and reassemble the union.
Check for Corrosion: Examine metal unions for rust or corrosion, especially in wet environments. Replace any corroded unions and consider using more corrosion-resistant materials or protective coatings.
Proper Tightening: Always tighten the union nut by hand first and finish with a wrench. Do not overtighten, as it can damage the threads or the sealing components.
Thread Care: Regularly check union threads for wear or damage. If threads are worn, replace the union. Use thread sealant as needed to prevent leaks.
Conclusion
At the end of the day, the decision should be guided by your project’s specific requirements. Consider factors such as the type of pipe material, the need for future disassembly, available space for installation, and the potential for regular maintenance. Choosing the right fitting not only impacts the immediate success of your installation but also ensures the durability and performance of your plumbing system over time.
FAQ
What’s the main difference between compression fittings and unions?
Compression fittings create a permanent or semi-permanent seal by compressing a ferrule around the pipe, while unions allow for easy disassembly and reconnection, making them ideal for systems that need frequent maintenance or adjustments.
Can I reuse a compression fitting?
While you technically can reuse a compression fitting, it’s recommended to replace the compression ring (ferrule) each time to ensure a proper seal. Reusing a ferrule can lead to leaks.
Are pipe unions more expensive than compression fittings?
Generally, pipe unions tend to be more expensive than compression fittings due to their larger size and design for easy disassembly. However, their cost is often justified for systems requiring frequent repairs or modifications.
Can compression fittings be used for gas lines?
Yes, compression fittings are often used in gas lines as they provide a strong, leak-proof seal. However, it’s crucial to choose fittings specifically rated for gas applications.
How do I fix a leak in a compression fitting or pipe union?
For compression fittings, try retightening the nut and check if the ferrule is damaged. For unions, inspect the gasket or O-ring for wear and replace if necessary. If leaks persist, the fitting may need to be replaced.
Which is better for a DIY plumbing project—compression fittings or unions?
For most DIY projects, compression fittings are easier to install and require less space. Unions are best for larger systems or if frequent disassembly is needed, but compression fittings are typically simpler for home plumbing tasks.