Clamping solutions play a crucial role across a wide range of industries, ensuring secure connections and the efficient operation of various systems. Clamps are essential in maintaining the integrity of fluid or airlines, preventing leaks, and ensuring that connections remain stable even under high pressure or temperature variations. Among the various clamping options available, crimp clamps and hose clamps stand out as two of the most widely used types due to their effectiveness in different applications.
Understanding Crimp Clamps
A. Definition and Mechanism
Crimp clamps are specialized fastening devices used to secure hoses, pipes, and other fittings by applying pressure around the circumference of the material. Unlike adjustable clamps, crimp clamps provide a permanent, non-adjustable seal by deforming around the object they secure. This deformation creates a tight, uniform seal that is resistant to leaks and loosening, making crimp clamps ideal for applications where a long-lasting, reliable connection is essential. The mechanism of a crimp clamp involves the use of a crimping tool that exerts force on the clamp, compressing it around the hose or fitting it until it is permanently secured.
The crimping process works by collapsing the clamp around the object, often utilizing a specific tool that ensures the clamp conforms exactly to the shape and size of the hose or fitting. Once crimped, the clamp cannot be reused or adjusted, providing a one-time, secure connection. This characteristic makes crimp clamps especially useful in high-pressure environments or where vibration might cause other types of clamps to loosen over time.
B. Types of Crimp Clamps
Crimp clamps come in various types, each designed for specific applications and materials. Some of the most common types include:
Ear Clamps: These clamps feature one or more “ears” that are compressed to tighten the clamp around the hose. Ear clamps are simple yet effective and are often used in automotive and plumbing applications. They are typically made of stainless steel, which offers excellent corrosion resistance and durability.
Oetiker Clamps: A specific type of ear clamp, Oetiker clamps are known for their precise and secure fit. They are widely used in automotive, aerospace, and medical applications where reliability is critical. Oetiker clamps are also available in a variety of materials, including stainless steel and plastic, to suit different environmental conditions.
Pinch Clamps: These clamps are used primarily in industrial settings and are known for their ability to provide a strong, leak-proof seal. They are often made from robust materials like stainless steel and are ideal for use in harsh environments.
Stepless Clamps: These clamps are designed to provide a 360-degree seal without any gaps, ensuring uniform compression around the entire circumference of the hose. Stepless clamps are commonly used in situations where a precise, consistent seal is required, such as in hydraulic systems.
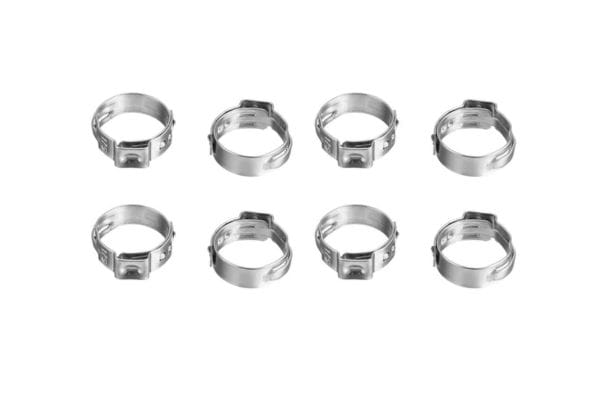
C. Applications of Crimp Clamps
Crimp clamps are used in a wide range of industries due to their strength and reliability. Some common applications include:
Automotive Industry: Crimp clamps are extensively used in vehicles to secure hoses in fuel lines, cooling systems, and air intake systems. Their ability to withstand high pressure and vibration makes them ideal for automotive applications where safety and reliability are paramount.
Plumbing: In plumbing, crimp clamps are used to secure PEX tubing and other types of plastic pipes. They provide a secure, leak-proof connection that is essential for preventing water damage in residential and commercial buildings.
Industrial Machinery: Crimp clamps are employed in industrial machinery to secure hoses that carry fluids, gases, or air. Their durability and resistance to harsh environmental conditions make them suitable for use in heavy-duty applications.
Aerospace and Medical Devices: Due to their precision and reliability, crimp clamps are used in sensitive applications such as aerospace components and medical devices where failure is not an option.
D. Advantages of Crimp Clamps
Crimp clamps offer several distinct advantages, making them a preferred choice in many applications:
Strong, Reliable Seal: The permanent deformation of crimp clamps ensures a tight, leak-proof seal that is difficult to achieve with other types of clamps. This makes them ideal for high-pressure applications.
Vibration Resistance: Crimp clamps are highly resistant to vibration, which can cause other types of clamps to loosen over time. This makes them especially useful in automotive and industrial settings.
Compact and Neat Appearance: Crimp clamps provide a streamlined, professional look, with no loose ends or bulky adjustments. This is particularly important in applications where aesthetics or space is a concern.
E. Disadvantages of Crimp Clamps
While crimp clamps are highly effective, they also have some disadvantages that may limit their use in certain situations:
Non-Reusable Nature: Once a crimp clamp is installed, it cannot be adjusted or reused. This can be a drawback in situations where future modifications or repairs are anticipated.
Requires Specific Tools for Installation: The installation of crimp clamps requires specialized crimping tools, which can add to the cost and complexity of the installation process.
Potential Difficulty in Removing or Adjusting: If a crimp clamp needs to be removed, it often has to be cut off, which can be challenging and may require additional tools. This makes crimp clamps less convenient in applications where frequent maintenance is required.
Understanding Hose Clamps
A. Definition and Mechanism
Hose clamps are versatile fastening devices designed to secure hoses onto fittings, pipes, or other connections. They work by applying adjustable tension around the circumference of the hose, creating a tight seal that prevents fluid or air from escaping. Unlike crimp clamps, which are permanently deformed during installation, hose clamps can be adjusted and reused, making them ideal for applications where flexibility and maintenance are important. The basic mechanism of a hose clamp involves a band that wraps around the hose, with a screw or bolt that tightens or loosens the band to achieve the desired level of compression.
Hose clamps are commonly used in situations where hoses need to be connected to barbed fittings or other smooth-surfaced connectors. By tightening the clamp, the band compresses the hose against the fitting, creating a seal that can withstand moderate levels of pressure and vibration. The adjustability of hose clamps allows for easy installation and removal, making them a popular choice for applications that require frequent maintenance or adjustments.
B. Types of Hose Clamps
There are several types of hose clamps, each designed for specific applications and varying in material, strength, and ease of use. Some of the most common types include:
Worm Drive Clamps: These are the most widely used type of hose clamps, consisting of a stainless steel or galvanized steel band with a screw thread pattern cut into it. As the screw is tightened, it engages with the band and tightens the clamp around the hose. Worm drive clamps are known for their ease of use and adjustability, making them suitable for a wide range of applications.
T-Bolt Clamps: T-bolt clamps are designed for high-pressure applications where a stronger seal is required. They feature a T-shaped bolt that provides an even distribution of pressure around the hose, ensuring a more secure connection. T-bolt clamps are commonly used in automotive and industrial settings, especially in turbocharger and coolant systems.
Spring Clamps: Also known as constant-tension clamps, these clamps are made from spring steel and are designed to automatically adjust to changes in hose size caused by temperature fluctuations. They are often used in automotive cooling systems to maintain a secure connection even as the hose expands and contracts.
Wire Clamps: Wire clamps are a simple, lightweight option, typically used for low-pressure applications. They consist of a single wire loop that is twisted around the hose and tightened with a screw or bolt. While not as strong as other types of hose clamps, wire clamps are easy to install and are often used in applications where space is limited.
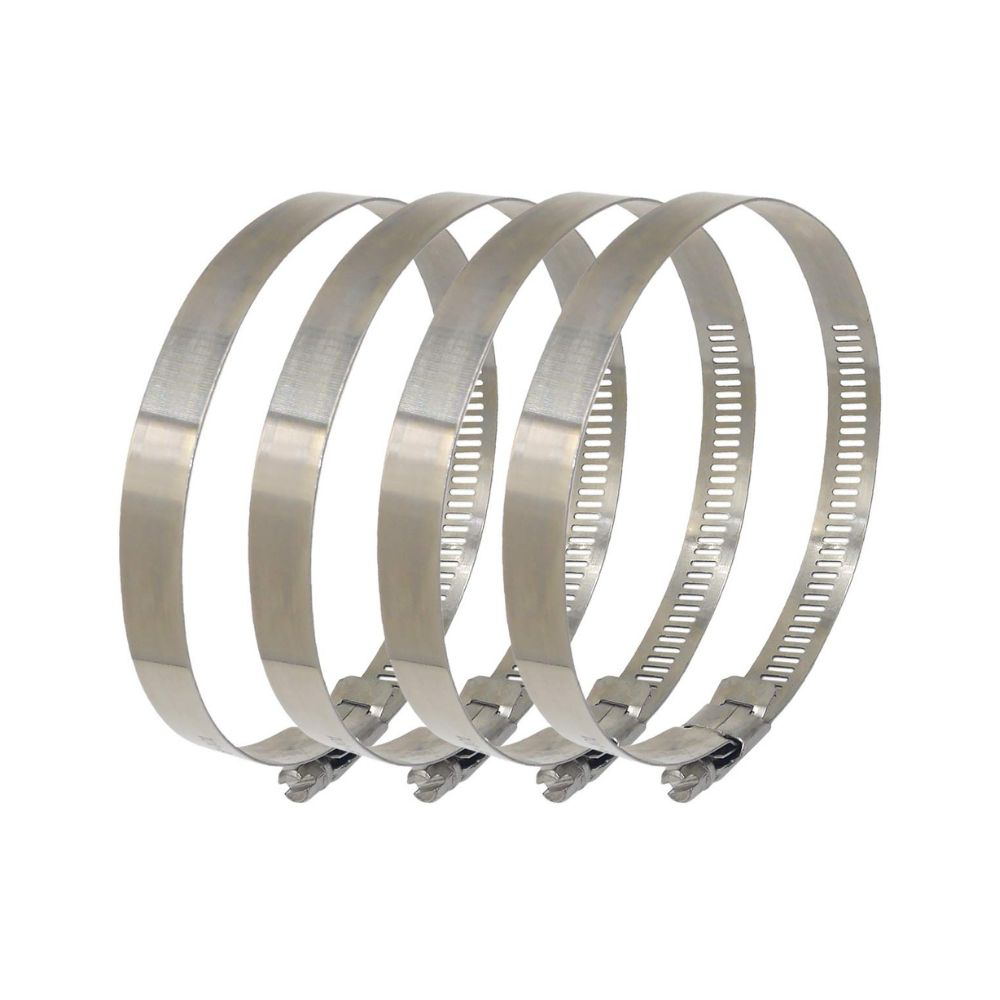
C. Applications of Hose Clamps
Hose clamps are used in a variety of industries due to their versatility and ease of use. Some common applications include:
Home Plumbing: Hose clamps are frequently used in household plumbing to secure hoses and pipes in water supply and drainage systems. Their adjustability makes them ideal for situations where hoses need to be replaced or adjusted regularly.
Automotive Industry: In vehicles, hose clamps are used to secure hoses in fuel, cooling, and air intake systems. They are particularly useful in applications where regular maintenance is required, as they can be easily loosened and retightened without damaging the hose.
Industrial Machinery: Hose clamps are used in industrial settings to secure hoses that carry fluids, gases, or air in machinery and equipment. Their ability to be adjusted and reused makes them a cost-effective solution for maintaining and repairing industrial systems.
Marine Applications: In boats and marine environments, hose clamps are used to secure hoses in bilge systems, fuel lines, and cooling systems. Stainless steel hose clamps are often preferred for their corrosion resistance in these harsh environments.
D. Advantages of Hose Clamps
Hose clamps offer several advantages that make them a popular choice in many applications:
Reusability and Adjustability: One of the key benefits of hose clamps is their ability to be adjusted and reused. This makes them ideal for applications where hoses need to be replaced or modified frequently, reducing waste and cost.
Ease of Installation and Removal: Hose clamps are easy to install and remove, requiring only a simple screwdriver or wrench. This makes them convenient for both professionals and DIY enthusiasts, allowing for quick and efficient maintenance.
Versatility in Various Applications: Hose clamps are available in a wide range of sizes and materials, making them suitable for a diverse array of applications. Whether used in automotive, plumbing, or industrial settings, hose clamps provide a flexible solution for securing hoses.
E. Disadvantages of Hose Clamps
Despite their many advantages, hose clamps also have some disadvantages that should be considered:
Potential for Loosening Over Time: Hose clamps can loosen over time, especially in applications where they are subject to vibration or temperature fluctuations. This can lead to leaks or disconnections, requiring regular checks and maintenance.
Less Secure Under High Pressure Compared to Crimp Clamps: While hose clamps are effective in many applications, they may not provide the same level of security as crimp clamps in high-pressure environments. In situations where maximum sealing strength is required, crimp clamps may be a better choice.
Bulkier Design in Some Cases: Some types of hose clamps, particularly T-bolt clamps, can be bulkier than crimp clamps. This can be a disadvantage in applications where space is limited or where a more streamlined appearance is desired.
Key Differences Between Crimp Clamps and Hose Clamps
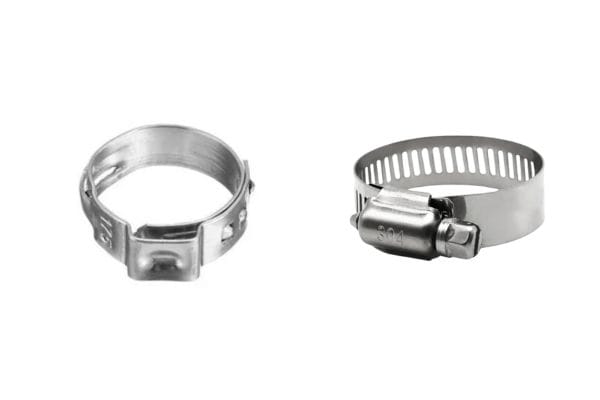
A. Installation Process
One of the most significant differences between crimp clamps and hose clamps lies in their installation process. Understanding these differences is crucial for selecting the appropriate clamp type for your application.
Crimp Clamps Installation: Crimp clamps require a specialized installation process that involves the use of a crimping tool. This tool is designed to compress the clamp around the hose or fitting, creating a permanent, secure seal. The crimping process deforms the clamp, ensuring it tightly grips the material it encloses. Once installed, the clamp cannot be adjusted or removed without being cut off, making it a one-time use solution.
The installation process for crimp clamps is typically more involved and requires specific tools and expertise. For instance, in the automotive industry, technicians use hydraulic crimping tools to ensure precise and consistent pressure is applied during installation. This results in a uniform seal that is highly resistant to leaks and vibration.
Hose Clamps Installation: In contrast, hose clamps are designed for easy installation and adjustment. The most common type, the worm drive clamp, uses a screw mechanism to tighten or loosen the clamp around the hose. This can be done with a simple screwdriver or wrench, making the installation process straightforward and accessible to both professionals and DIY users.
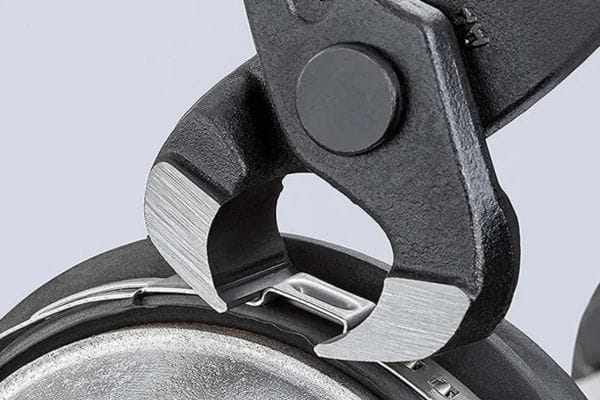
B. Reusability and Adjustability
Reusability and adjustability are key factors that differentiate crimp clamps from hose clamps, influencing their suitability for various applications.
Crimp Clamps: Crimp clamps are designed for single use, offering a permanent solution that cannot be adjusted or reused once installed. This makes them ideal for applications where a long-term, maintenance-free connection is required. For example, in automotive fuel lines or high-pressure hydraulic systems, crimp clamps provide a secure and reliable seal that remains intact over time, without the need for periodic tightening or adjustments.
Hose Clamps: Hose clamps are highly valued for their reusability and adjustability. After installation, hose clamps can be loosened or tightened as needed, allowing for easy modifications or maintenance. This makes hose clamps particularly useful in applications where hoses may need to be replaced or where connections require periodic inspection and adjustment.
The ability to adjust hose clamps also means they can accommodate slight variations in hose size or pressure changes over time. This flexibility is essential in dynamic environments, such as automotive cooling systems, where components may expand or contract with temperature fluctuations.
C. Sealing Strength and Reliability
Crimp Clamps: Crimp clamps are known for their exceptional sealing strength and reliability. The crimping process creates a uniform, tight seal around the hose or fitting, minimizing the risk of leaks. This makes crimp clamps particularly effective in high-pressure environments where a strong, leak-proof connection is essential. For example, in hydraulic systems, the crimped connection is highly resistant to pressure surges and vibration, ensuring consistent performance over time.
The uniform pressure applied by the crimping tool ensures that the clamp grips the hose evenly, reducing the likelihood of weak spots that could lead to leaks. Additionally, the permanent nature of the crimped connection means there is no risk of the clamp loosening over time, providing a reliable, maintenance-free solution.
Hose Clamps: Hose clamps, while versatile and adjustable, may not offer the same level of sealing strength as crimp clamps, especially under high-pressure conditions. The adjustable nature of hose clamps means that the seal may not be as uniform, particularly if the clamp is not tightened evenly. This can lead to potential weak spots where leaks could occur.
In applications where the hose is subjected to significant vibration or pressure fluctuations, hose clamps may require periodic tightening to maintain their sealing strength. Over time, the clamp may loosen, reducing its effectiveness and potentially leading to leaks or disconnections.
Conclusion
When selecting between crimp and hose clamps, the specific needs of the application should be considered, including pressure, environmental conditions, and maintenance requirements. Crimp clamps are recommended for high-pressure or critical applications that require a permanent, maintenance-free seal. In contrast, hose clamps are well suited for applications requiring adjustability, reusability, and ease of maintenance, especially in less demanding environments. Feel free to contact Topa with any hose clamp questions or needs!
FAQ
What is the main difference between crimp clamps and hose clamps?
Crimp clamps provide a permanent, secure seal, while hose clamps are adjustable and reusable.
Which type of clamp is better for high-pressure applications?
Crimp clamps are generally better for high-pressure applications due to their strong, permanent seal.
Can hose clamps be reused?
Yes, hose clamps can be reused and adjusted as needed, making them ideal for applications requiring frequent maintenance.
Do crimp clamps require special tools for installation?
Yes, crimp clamps require specific crimping tools for installation, which provide a tight, uniform seal.
Are hose clamps suitable for use in corrosive environments?
Hose clamps made from corrosion-resistant materials like stainless steel can be used in corrosive environments, but crimp clamps may offer better durability.
Which clamp type is easier to install?
Hose clamps are generally easier to install and do not require specialized tools, making them more convenient for quick adjustments or repairs.