Using standard hydraulic equipment in extreme cold is a recipe for disaster. Components that work perfectly in normal climates can become dangerously unreliable when the temperature plummets to -40°C.
To use hydraulic fittings successfully at -40°C, you must use components made from appropriate low-temperature alloys like 316 stainless steel, fit them with specialized low-temperature seals like low-temp Nitrile or Silicone, use arctic-grade hydraulic fluid, and follow specific cold-weather installation and maintenance protocols.
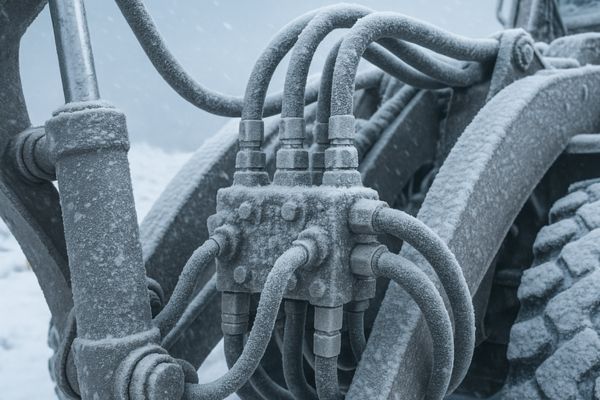
The challenge of operating hydraulic systems in freezing environments is something we deal with regularly, especially with our clients in colder regions like Romania, Iceland, and parts of the USA and Canada. It’s not just one single problem; it’s a series of interconnected challenges that must be addressed as a complete system. You can have the best fitting in the world, but if the seal inside it isn’t right or the oil is too thick, the system will fail. Understanding how extreme cold attacks each part of the hydraulic connection—the metal fitting, the elastomeric seal, and the fluid itself—is the only way to build a system that is both reliable and safe when the temperature drops far below freezing.
Why Do Standard Fittings and Systems Fail in Extreme Cold?
Your equipment suddenly fails on the coldest day of the year. A steel fitting has fractured, not from overpressure, but simply from the cold, causing a major hydraulic leak and bringing your entire operation to a standstill.
Standard hydraulic systems fail in extreme cold due to two primary material science principles: the ductile-to-brittle transition in common carbon steels, and the hardening of standard elastomeric seals below their glass transition temperature, causing them to lose their ability to seal effectively.
When we talk about failure at -40°C, we are entering the realm of material physics. It’s a completely different world from the typical operating conditions most hydraulic components are designed for. At these temperatures, materials behave in ways that can seem unpredictable if you are not prepared. The fundamental mistake is to assume that a component’s properties are constant regardless of temperature. They are not. A tough, reliable carbon steel fitting at 20°C can become as fragile as glass at -40°C. This change is not gradual; it can be sudden and catastrophic, leading to equipment failure that occurs without any prior warning signs like bulging or deformation.
The Brittle Fracture Phenomenon
The most dangerous failure mode in cold weather is brittle fracture. This is a primary concern for the fitting itself and other metal components.
Understanding the Ductile-to-Brittle Transition Temperature (DBTT)
Most common carbon steels, the material used for many standard, economical hydraulic fittings, are ductile at normal temperatures. This means if you overload them, they will stretch and deform before they break. This provides a warning. However, these steels have a Ductile-to-Brittle Transition Temperature (DBTT)[^1]. Below this temperature, the steel’s molecular structure changes its behavior. Instead of deforming, it will fracture instantly when subjected to an impact or shock load, with very little energy required. The fracture surface often has a crystalline appearance. For many common carbon steels, this transition temperature is dangerously close to the -40°C mark.
The Failure of Standard Seals
While the metal fitting is turning brittle, the soft seal inside it is also undergoing a critical transformation.
The Glass Transition Temperature (Tg)
Elastomers, like the rubber used in O-rings and seals, get their sealing properties from their flexibility. As they get colder, they lose this flexibility and become stiff and hard. Every elastomer has a Glass Transition Temperature (Tg)[^2] where it transitions from a rubbery, flexible state to a hard, glassy, and brittle state. A standard Nitrile (NBR) O-ring, one of the most common seals in hydraulics, can have a Tg around -35°C. At -40°C, it is no longer a flexible rubber seal. It’s a hard plastic ring that cannot conform to surfaces or respond to pressure changes, leading to inevitable leaks.
How Does Material Selection Prevent Brittle Fracture?
Your system has failed, and you see that a fitting has shattered. You realize the material was simply not rated for the arctic conditions you are working in.
Preventing brittle fracture is achieved by selecting a metal alloy that does not exhibit a ductile-to-brittle transition at a low temperature. Austenitic stainless steels, such as the 304 and 316 grades, are the premier choice for this application due to their fundamental metallurgical structure.
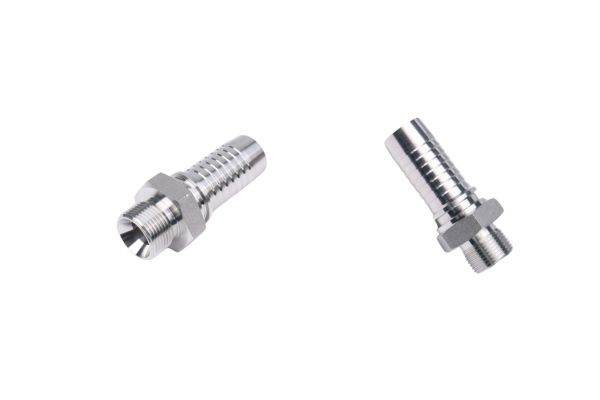
The choice of the fitting’s base metal is the single most important decision for ensuring structural integrity in extreme cold. The risk of brittle fracture is so significant that it must be the primary consideration, often taking precedence over pressure rating or even cost. As a supplier, it is our responsibility to guide customers away from materials that pose a risk in their specific operating environment. While a zinc-plated carbon steel fitting might be a cost-effective solution for a customer in the Philippines, it would be an irresponsible recommendation for a customer operating equipment in Iceland. The physics of the material simply does not support its use in that environment.
The Weakness of Carbon Steel
As discussed, the primary issue with most standard ferritic-pearlitic steels (common carbon steels) is their DBTT. Their body-centered cubic (BCC) crystal lattice structure makes them susceptible to becoming brittle at low temperatures. While some specially treated carbon steel alloys can be rated for low-temperature service, standard, off-the-shelf fittings should be considered unsafe for critical applications at -40°C.
The Superiority of Austenitic Stainless Steels
The solution lies in using a material with a different crystal structure.
Why 300-Series Stainless Steel Excels
Austenitic stainless steels, like the widely used 304 and 316 grades, have a face-centered cubic (FCC) crystal structure. A key property of this FCC structure is that it does not exhibit a DBTT. This means it retains its ductility and toughness even at cryogenic temperatures, far below -40°C. When a 316 stainless steel fitting is impacted at -40°C, it will dent and deform, not shatter. This inherent material property makes it an exceptionally safe and reliable choice for low-temperature hydraulic systems.
Material | Crystal Structure | Low-Temp Behavior | Recommended Use at -40°C |
Carbon Steel (Std) | BCC | Becomes brittle; risk of fracture | Not Recommended |
Brass | FCC | Stays ductile, but lower strength than steel | Low-pressure applications |
304 Stainless Steel | FCC | Stays ductile and tough; excellent performance | Recommended |
316 Stainless Steel | FCC | Stays ductile; superior corrosion resistance vs. 304 | Highly Recommended |
Why 316L is a Premier Choice
While both 304 and 316 stainless steel are excellent for cold weather, we often recommend 316L. The “L” stands for low carbon, and this grade includes molybdenum. This not only gives it superior corrosion resistance (a bonus in environments where corrosive de-icing agents might be used) but also ensures its excellent properties are maintained even after welding, making it ideal for creating robust, fabricated systems.
What is the Critical Role of Seals in Low-Temperature Sealing?
You see fluid weeping from a connection. The fitting isn’t broken, but the seal inside has become hard as a rock from the cold, losing its ability to contain pressure.
The seal is the dynamic component of the connection, and its ability to remain flexible and elastic at -40°C is critical. Standard seals will harden and fail, so you must select a specialized low-temperature elastomer that maintains its properties well below the target operating temperature.
If the metal fitting is the skeleton of the connection, the seal is its muscle. It needs to be able to flex, compress, and rebound to maintain a positive seal as pressures fluctuate and surfaces minutely shift. At room temperature, this is easy. At -40°C, it is a significant engineering challenge. The most common point of failure in a well-chosen fitting is often an incorrectly specified seal. When a customer comes to us with a low-temperature application, our second question, right after confirming the metal choice, is always about the seal material. The two must be considered together to create a viable connection.
Understanding Seal Performance Metrics
When selecting a low-temperature seal, you need to look beyond the general material type and consider specific temperature ratings.
TR-10 and Glass Transition Temperature (Tg)
The Glass Transition Temperature (Tg) is the point where the material becomes glassy and brittle. A more practical metric for seals is the TR-10 (Temperature Retraction) value. This test measures the temperature at which a stretched elastomer retracts 10% of the way back to its original length. It is a good indicator of the true low-temperature functional limit of a seal. A seal should have a TR-10 rating significantly lower than the lowest expected operating temperature.
Comparing Low-Temperature Seal Materials
Not all elastomers are created equal when it comes to cold performance.
Seal Material | Common Name | Typical Low-Temp Limit | Notes |
Nitrile (Standard) | NBR, Buna-N | -35°C (-30°F) | Very common, but inadequate for -40°C. Becomes hard and brittle. |
Low-Temp Nitrile | LT-NBR | -55°C (-65°F) | Specially formulated for cold; good balance of cost & performance. |
Fluorocarbon (Standard) | FKM, Viton® | -20°C (-4°F) | Poor standard low-temp performance. Special grades exist. |
Silicone | VMQ | -60°C (-75°F) | Excellent low-temp flexibility. Poor abrasion/tear resistance. |
Ethylene Propylene | EPDM | -55°C (-65°F) | Good low-temp performance. Incompatible with petroleum oils. |
Polytetrafluoroethylene | PTFE, Teflon® | -200°C (-328°F) | Excellent temp range, but is a rigid plastic, not an elastomer. |
For most hydraulic applications using petroleum-based fluids, Low-Temperature Nitrile (LT-NBR) is often the best choice. It offers the chemical compatibility of standard NBR with a much-improved cold-weather performance. For static applications where abrasion is not a concern, Silicone (VMQ) is also an excellent option.
How Does Low Temperature Affect Hydraulic Fluid and System Performance?
You start your machine, and the hydraulics are extremely slow and noisy. The pump is whining as it struggles to pull the thick, molasses-like oil from the tank.
Low temperature dramatically increases the viscosity (thickness) of hydraulic fluid. This thick oil can starve the pump, causing cavitation and damage, increase system pressure, slow down all machine functions, and even prevent the system from starting at all.
The fluid is the lifeblood of the hydraulic system, and at -40°C, that blood can thicken to the point of being unusable. We can provide the best low-temperature fittings and seals, but if the customer is using a standard hydraulic oil, the system is doomed to fail. The performance of the fluid is a critical third leg of the low-temperature reliability stool, alongside fittings and seals. Think about trying to suck honey through a thin straw—that’s what the hydraulic pump is trying to do with cold, standard oil. It’s an impossible task that will quickly lead to pump failure.
The Problem of High Viscosity
Viscosity is a fluid’s resistance to flow. As oil gets colder, its viscosity increases exponentially.
Pump Cavitation and Starvation
The pump is designed to pull fluid from the reservoir. If the oil is too thick, it cannot flow into the pump inlet fast enough. This creates a vacuum, and bubbles of vapor form in the oil. When these bubbles collapse under pressure inside the pump, it’s called cavitation. This process is incredibly destructive, eroding internal pump components and leading to rapid failure. At the very least, a pump struggling with thick oil will be noisy and inefficient.
Sluggish Performance and Pressure Spikes
Thick oil also flows very slowly through hoses, fittings, and valves. This means actuators (cylinders and motors) will respond very slowly, making the machine difficult to control. Furthermore, the high resistance to flow creates enormous backpressure in return lines and can cause pressure-relief valves to open unnecessarily, generating heat and wasting energy.
The Solution: Arctic-Grade and Synthetic Fluids
The solution is to use a hydraulic fluid specifically designed for cold weather. These are often synthetic-based fluids or special mineral oils. The key property to look for is a **High Viscosity Index (VI)**. The Viscosity Index is a measure of how much a fluid’s viscosity changes with temperature. A fluid with a high VI will remain much thinner and more flowable at -40°C than a standard fluid with a low VI. Using an arctic-grade fluid with a high VI is not optional for reliable operation; it is a fundamental requirement.
What Are the Best Practices for Installing Fittings in a -40°C Environment?
You need to replace a fitting in the field in freezing weather. You tighten it as usual, but it either leaks or you hear a crack. The cold has changed the rules of installation.
Installing fittings in extreme cold requires special procedures. This includes pre-warming components where possible, using a calibrated torque wrench to avoid over-stressing brittle metal, and being meticulously clean to prevent contamination from ice and condensation.
The assembly process itself is fraught with peril in extreme cold. Human factors and physics both work against you. Metal is less forgiving, lubricants don’t perform the same way, and the simple act of moisture in your breath can create a contamination problem. Assuming that the installation procedure is the same at -40°C as it is at +20°C is a dangerous mistake. We always advise our clients to provide their field technicians with specific training on cold-weather maintenance procedures to ensure both the reliability of the repair and the safety of the technician.
The Importance of Pre-Warming
When feasible, components should be gently warmed before installation.
- Safe Warming Methods: Store fittings and hoses in a warm vehicle cab or use a portable, flameless heater.
- Danger of Direct Flame:Never use a blowtorch or other direct flame to heat a hydraulic component. This can damage seals, degrade metal properties, and poses an extreme fire hazard with hydraulic fluid.
Torque Application in the Cold
Applying the correct torque is always important, but it is absolutely critical in the cold.
- Risk of Over-Torquing: Cold metal is less ductile. Over-tightening a fitting can easily lead to a brittle fracture of the fitting or the port it’s threaded into.
- Use a Torque Wrench: Do not rely on “feel.” Use a properly calibrated torque wrench and adhere to the manufacturer’s specifications. Be aware that the performance of thread sealants and lubricants can also be affected by the cold, which can alter the torque-to-clamp-load relationship.
Preventing Ice and Condensation Contamination
Moisture is your enemy. At -40°C, any moisture will instantly turn into hard ice crystals.
- Keep Components Dry: Keep all new fittings and hose ends capped and sealed until the moment of installation.
- Ice as a Contaminant: A single ice crystal can be enough to score a seal surface or block a tiny orifice in a valve.
- Cleanliness is Key: Ensure both the fitting and the port are perfectly clean and dry before assembly. Even breathing on a cold component can cause frost to form.
Successfully operating hydraulics at -40°C is a science of specifics. It requires a total system approach: using the right metals, the right seals, the right fluid, and the right procedures.
Reference
[^1]: Understanding DBTT is crucial for preventing brittle fractures in cold weather, ensuring safety and reliability in hydraulic systems.
[^2]: Exploring Tg helps in selecting the right materials for seals, preventing leaks and failures in hydraulic applications.