Hydraulic fluids are crucial in hydraulic systems, enabling machinery and equipment to operate efficiently by transmitting force through pressure and flow. Understanding these fluids is essential because it affects system performance, component longevity, safety, and cost efficiency. Key characteristics to be explored include the types of fluids, their properties, performance factors, and best practices for selection and maintenance. This knowledge ensures effective management and optimal operation of hydraulic systems.
Types of Hydraulic Fluids
Mineral Oils
Mineral oils are the most prevalent type of hydraulic fluid, primarily due to their cost-effectiveness and established performance characteristics. These fitting fluids are derived from the refining of crude oil and have been used in hydraulic systems for decades. Their composition generally includes a base oil with various additives to enhance performance.
Advantages:
Good Lubrication Properties: Mineral oils provide effective lubrication, which reduces friction and wear on hydraulic components.
Broad Applicability: They are versatile and can be used in a wide range of hydraulic systems and applications.
Cost-Effectiveness: Mineral oils are generally less expensive than specialized hydraulic fluids, making them a popular choice for many applications.
Disadvantages:
Limited Fire Resistance: Mineral oils are flammable and can pose a fire hazard in high-temperature environments or in applications where sparks or open flames are present.
Potential Environmental Hazards: When spilled or improperly disposed of, mineral oils can cause environmental contamination. Their disposal often requires special handling procedures to minimize ecological impact.
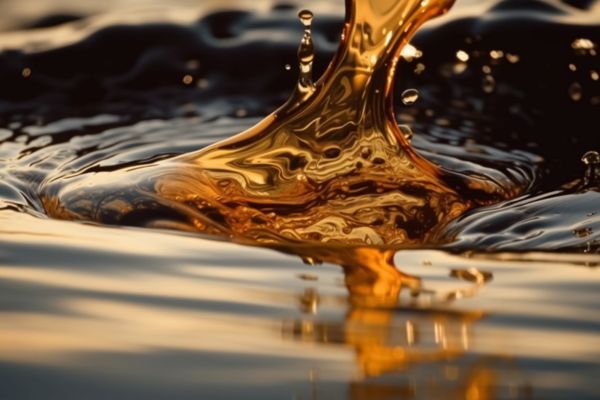
Water-Based Fluids
Water-based fluids are designed to offer improved fire resistance compared to mineral oils, making them suitable for applications where fire risk is a concern. These fluids come in several types, including water-glycol solutions and water-oil emulsions.
Water-Glycol Solutions: Water-glycol solutions consist of a mixture of water and glycol. They offer significant fire resistance due to the high water content. However, they have some limitations in performance.
Benefits:
Enhanced Fire Safety: The high water content provides excellent fire resistance, reducing the risk of fire in high-temperature environments.
Reduced Flammability: The presence of water makes these fluids less flammable compared to pure mineral oils.
Limitations:
Lower Lubrication Properties: Water-glycol solutions generally have poorer lubrication properties compared to mineral oils, which can affect the efficiency and lifespan of hydraulic components.
Corrosion Risk: The water content can lead to corrosion of metal components if not properly managed, necessitating the use of corrosion inhibitors.
Water-Oil Emulsions: Water-oil emulsions are mixtures of water and oil, with the water content varying depending on the required fire resistance level.
Benefits:
Fire Resistance: Like water-glycol solutions, these emulsions offer improved fire resistance compared to mineral oils.
Customizable: The ratio of water to oil can be adjusted to balance fire resistance with lubrication properties.
Limitations:
Corrosion Issues: Similar to water-glycol solutions, water-oil emulsions can lead to corrosion if proper maintenance and corrosion inhibitors are not used.
Reduced Lubrication: The lubrication properties of water-oil emulsions can be inferior to those of pure mineral oils.
Fire-Resistant Fluids
Fire-resistant fluids are essential in industries where there is a high risk of fire, such as steel mills, aerospace, and other high-temperature environments. These fluids are designed to resist ignition and burning, providing enhanced safety in critical applications.
Phosphate Esters: Phosphate esters are a type of fire-resistant fluid known for their excellent fire resistance properties.
Benefits:
Superior Fire Resistance: Phosphate esters are highly resistant to ignition and burning, making them suitable for extremely hazardous environments.
High Thermal Stability: They maintain performance at high temperatures, which is critical in industries like steel manufacturing.
Disadvantages:
Cost: Phosphate esters can be more expensive than mineral oils and other hydraulic fluids.
Handling Requirements: They require special handling and storage procedures to ensure safety and prevent degradation.
Organic Esters: Organic esters are another category of fire-resistant fluids, known for their lower flammability and environmental benefits.
Benefits:
Reduced Flammability: Organic esters have a lower risk of catching fire compared to mineral oils, making them suitable for various high-risk environments.
Environmental Benefits: They are often biodegradable and have a lower environmental impact compared to traditional mineral oils.
Disadvantages:
Higher Cost: Organic esters can be more costly than other types of hydraulic fluids.
Compatibility Issues: They may not be compatible with all materials used in hydraulic systems, necessitating careful selection of system components.
Key Properties of Hydraulic Fluids
Viscosity
Viscosity is a measure of a fluid’s resistance to flow, which plays a crucial role in hydraulic systems. It determines how easily the fluid can move through the system’s components.
Definition and Significance: Viscosity is defined as the internal friction within a fluid that resists flow. It is a key parameter in ensuring the hydraulic fluid performs optimally.
Impact on System Performance: Proper viscosity ensures that the fluid flows smoothly through the system, maintaining a consistent flow rate and pressure. Fluids with appropriate viscosity contribute to efficient energy use and system stability. If the viscosity is too high, it can lead to increased energy consumption and reduced efficiency. Conversely, too low viscosity may result in inadequate lubrication and potential system wear.
Compressibility
Compressibility refers to the extent to which a fluid’s volume decreases under pressure. It is essential for the proper operation of hydraulic systems, particularly in applications requiring precise control.
Importance in Hydraulic System Operation: Compressibility affects how the fluid responds to pressure changes. Fluids with low compressibility maintain more stable volume and pressure under varying conditions, which is critical for accurate control and system response.
Effects on System Response and Stability: A fluid with low compressibility ensures minimal changes in volume, providing stable and predictable performance. High compressibility can lead to system instability and delayed responses, impacting the overall effectiveness of hydraulic operations.
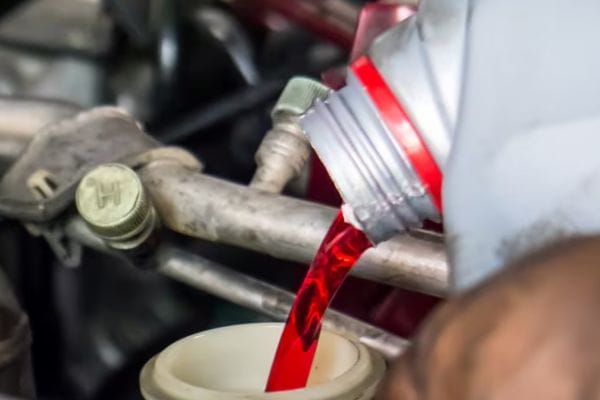
Lubricating Properties
Hydraulic fluids must possess adequate lubricating properties to ensure the longevity and efficient operation of system components.
Role in Reducing Wear and Tear: Proper lubrication minimizes friction between moving parts, reducing wear and extending the lifespan of components. Effective lubrication is essential for preventing premature component failure and maintaining system performance.
Impact on Component Lifespan: Well-lubricated components experience less friction and heat generation, which translates to longer service life and reduced maintenance requirements. This contributes to overall system reliability and cost-effectiveness.
Thermal Stability
Thermal stability is the ability of a hydraulic fluid to resist degradation and maintain performance at elevated temperatures.
Ability to Withstand Temperature Variations: Fluids with high thermal stability can endure high operating temperatures without breaking down or losing their effectiveness. This is crucial for systems exposed to fluctuating or extreme temperatures.
Effects on Fluid Degradation and System Reliability: High thermal stability prevents fluid breakdown and degradation, ensuring consistent performance and protecting the hydraulic system from potential failures caused by overheating or thermal stress.
Chemical Stability
Chemical stability involves a fluid’s resistance to chemical changes such as oxidation and contamination, which can impact its performance and longevity.
Resistance to Oxidation and Contamination: A chemically stable fluid resists oxidation and other chemical reactions that can lead to the formation of harmful by-products. This stability helps maintain fluid integrity and system health.
Impact on Fluid Life and System Health: Chemically stable fluids have a longer service life and reduce the risk of clogging, corrosion, and other issues that can compromise system performance. Proper chemical stability is essential for maintaining overall fluid quality and system reliability.
Performance Characteristics
Pumpability
Pumpability measures how effectively a hydraulic fluid can be moved through the system by the pump. This characteristic is crucial for ensuring smooth operation and optimal energy consumption.
Definition and Importance: Pumpability refers to the ease with which a fluid is transported through the hydraulic system. It affects the efficiency of the pump and overall system performance.
Impact on System Operation: Fluids with poor pumpability can lead to increased friction and strain on the pump, causing potential wear and operational issues. Ensuring high pumpability helps maintain consistent flow, reduce energy consumption, and prevent damage to system components.
Anti-Wear Properties
Anti-wear properties are essential for protecting hydraulic system components from damage caused by friction and mechanical wear.
Mechanisms to Protect System Components: Hydraulic fluids often contain additives specifically designed to enhance anti-wear properties. These additives form a protective film on metal surfaces, reducing friction and wear.
Ensuring Longevity and Reliability: Effective anti-wear properties extend the lifespan of hydraulic components by minimizing damage and reducing the frequency of maintenance. This contributes to the overall reliability and efficiency of the hydraulic system.
Corrosion Resistance
Corrosion resistance is the ability of hydraulic fluid to protect metal surfaces from corrosive damage caused by chemical reactions.
Role in Protecting Metal Surfaces: Hydraulic fluids with good corrosion resistance prevent the formation of rust and other corrosive compounds that can damage metal components. This protection is crucial for maintaining system integrity and preventing leaks or component failures.
Extending Component Life: By protecting against corrosion, a fluid helps extend the lifespan of metal parts and ensures consistent performance over time. This reduces the need for frequent replacements and repairs, enhancing the overall cost-effectiveness of the system.
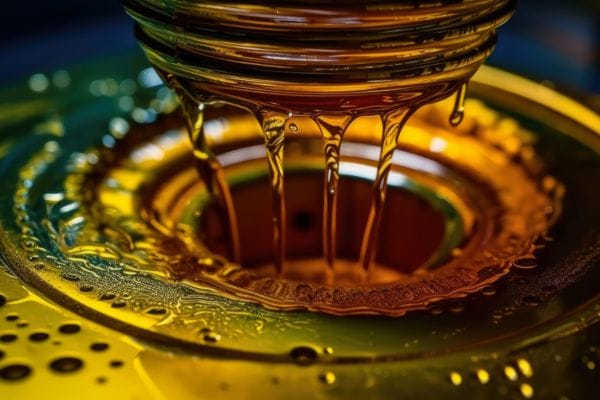
Foaming and Air Release
Foaming and air release characteristics impact the efficiency and safety of hydraulic systems.
Effects on System Efficiency: Foaming can lead to cavitation, where air bubbles collapse violently, causing damage to components and reducing performance. Effective hydraulic fluids should minimize foaming and facilitate rapid air release to maintain system efficiency.
Impact on Safety and Performance: Properly formulated fluids reduce the likelihood of cavitation and ensure that trapped air is quickly released, which helps maintain stable operation and prevents potential hazards associated with air bubbles in the system.
Selecting the Right Hydraulic Fluid
Application Considerations
Choosing the appropriate hydraulic fluid requires aligning its properties with the specific needs of the hydraulic system.
Operating Temperature: Select a fluid that remains stable and maintains performance across the expected temperature range of the system. Fluids with high thermal stability are essential for systems that operate under varying or extreme temperatures.
Pressure Requirements: Ensure the fluid can handle the maximum operating pressure of the system without degrading or causing issues. Fluids with suitable compressibility characteristics are crucial for maintaining system stability and performance under high pressure.
Fire or Environmental Hazards: For applications with high fire risks, such as in steel mills or aerospace, select fluids with high fire resistance. Consider environmental factors if the system operates in sensitive areas, opting for fluids that minimize ecological impact or contamination.
Environmental and Safety Factors
Selecting hydraulic fluids based on their environmental impact and safety features is crucial for responsible operation and compliance with regulations.
Biodegradability: Opt for biodegradable fluids if there is a risk of spillage or leakage into the environment. Biodegradable fluids break down more quickly and reduce long-term environmental damage.
Toxicity: Consider the toxicity of the hydraulic fluid, especially if the system is used in environments where human exposure is possible. Non-toxic fluids are safer and more environmentally friendly, reducing health risks.
Flammability: Choose fluids with appropriate flammability characteristics based on the system’s operating environment. For high-risk areas, select fluids with lower flammability to enhance safety and reduce fire hazards.
Manufacturer Recommendations
Following manufacturer recommendations is essential for ensuring the hydraulic system operates efficiently and reliably.
Adherence to Recommended Fluids: Manufacturers often provide specific fluid recommendations based on system design and component materials. Using the recommended fluid helps maintain optimal performance and avoid issues related to incompatibility or degradation.
Maintenance Practices: Along with selecting the right fluid, adhering to recommended maintenance practices is crucial. This includes regular monitoring of fluid condition, timely replacement, and proper handling procedures. Following these guidelines helps extend the system’s lifespan and ensures ongoing reliability and efficiency.
Maintenance and Management
Monitoring Fluid Quality
Regular monitoring of hydraulic fluid quality is essential for maintaining optimal system performance and preventing issues.
Methods for Assessing Fluid Condition: Regular assessments include visual inspections, where operators check for changes in color, clarity, or the presence of contaminants. Analytical tests, such as viscosity measurements, particle counts, and chemical analyses, provide detailed insights into fluid conditions.
Benefits of Monitoring: Early detection of issues like degradation, contamination, or reduced performance allows for timely interventions. Consistent monitoring helps maintain system efficiency, extend component lifespan, and prevent costly breakdowns.
Fluid Replacement and Disposal
Proper fluid replacement and disposal practices are critical for system maintenance and environmental protection.
Fluid Replacement Guidelines: Replace hydraulic fluids based on manufacturer recommendations or when analysis indicates significant degradation. Follow recommended intervals or triggers such as changes in fluid properties or system performance issues.
Best Practices for Disposal: Ensure proper disposal of used hydraulic fluids according to local regulations and environmental guidelines. Many regions have specific requirements for the handling and disposal of hazardous materials to minimize environmental impact. Employ recycling or waste management services that comply with these regulations.
Handling Contamination
Contamination can severely impact hydraulic system performance and longevity, so effective management strategies are crucial.
Prevention Through Filtration: Implement proper filtration systems to remove contaminants such as particles, water, and debris from the hydraulic fluid. Regularly replace filters and ensure they are appropriately sized for the system.
Handling Contamination Incidents: Develop and follow protocols for responding to contamination events. This includes immediate isolation of affected areas, system cleaning, and fluid replacement. Addressing contamination quickly helps prevent damage and ensures continued system reliability.
Regular System Checks: Conduct routine inspections and maintenance to identify potential sources of contamination. Regular checks help maintain fluid quality and system performance, reducing the risk of operational issues.
Conclusion
Performance characteristics such as pumpability, anti-wear properties, corrosion resistance, and foaming and air release further influence system effectiveness and longevity. Making informed decisions based on these factors, as well as adhering to best practices for fluid maintenance and management, ensures that your hydraulic systems operate reliably and efficiently. Regular monitoring, proper fluid replacement, and effective contamination handling are essential to maintain fluid quality and system performance.
FAQ
What are the main types of hydraulic fluids?
The main types of hydraulic fluids include mineral oils, water-based fluids (such as water-glycol solutions and water-oil emulsions), and fire-resistant fluids (like phosphate esters and organic esters). Each type has specific applications and properties suited to different operational needs.
How does viscosity affect hydraulic fluid performance?
Viscosity measures a fluid’s resistance to flow. It affects how easily the fluid moves through the system and maintains pressure. Proper viscosity ensures smooth operation, energy efficiency, and stable system performance.
Why is thermal stability important for hydraulic fluids?
Thermal stability indicates a fluid’s ability to withstand high temperatures without degrading. It is crucial for maintaining consistent performance and preventing fluid breakdown, which can lead to system failure and reduced reliability.
How can I monitor the quality of hydraulic fluid?
You can monitor hydraulic fluid quality through visual inspections for changes in color or clarity and analytical tests that measure properties like viscosity and contamination levels. Regular checks help detect issues early and maintain system performance.
What should I consider when selecting hydraulic fluid for my system?
Consider factors such as the operating temperature and pressure of your system, fire or environmental hazards, and the fluid’s compatibility with system components. It’s also important to follow manufacturer recommendations for optimal performance.
How should I handle the disposal of used hydraulic fluids?
Dispose of used hydraulic fluids according to local regulations and environmental guidelines. Many areas have specific rules for the disposal of hazardous materials.