Among the most critical issues that can affect hydraulic systems are cavitation and flashing. These phenomena can cause severe damage to system components if not addressed promptly. Both cavitation and flashing are insidious problems that can go unnoticed until significant damage has occurred, making early detection and prevention crucial for the health of hydraulic systems.
Understanding Cavitation
Definition and Mechanics
Cavitation is a phenomenon that occurs when vapor bubbles form in a liquid due to a significant pressure drop. This usually happens in hydraulic systems when the pressure falls below the liquid’s vapor pressure, causing localized boiling. These vapor bubbles then travel with the liquid flow and, when they encounter higher-pressure regions, they collapse or implode violently. This implosion generates shock waves and can cause severe damage to nearby surfaces and components.
The process begins when the pressure in a liquid drops below its vapor pressure, which is the pressure at which the liquid starts to vaporize. As the liquid vaporizes, small vapor bubbles form. When these bubbles move into regions of higher pressure, they rapidly collapse. This collapse releases a substantial amount of energy, creating shock waves that impact surrounding surfaces, leading to potential damage.
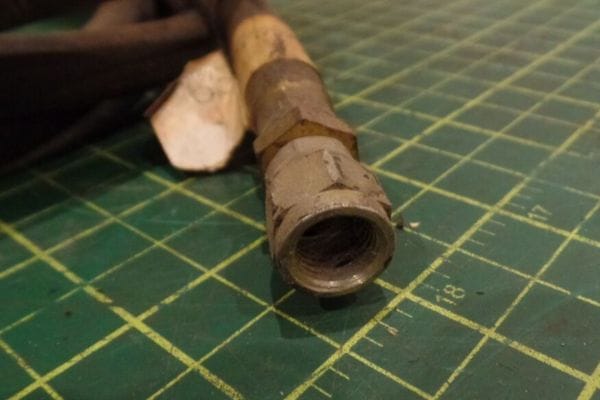
Causes of Cavitation
Low Pressure Zones: Cavitation typically occurs in areas where the pressure of the fluid is significantly lower than its vapor pressure. This often happens in hydraulic pumps, valves, and around propellers. For example, if a pump’s inlet pressure drops due to an obstruction or high flow rates, it can create a low-pressure zone conducive to cavitation.
High Fluid Velocities: High fluid velocities can lead to pressure drops within the system. As fluid speeds up, the pressure decreases according to Bernoulli’s principle. If the velocity is high enough, the pressure may fall below the vapor pressure of the liquid, resulting in cavitation. This is particularly common in narrow passages or poorly designed components where the flow is accelerated.
Symptoms of Cavitation
Noise and Vibration: One of the most noticeable signs of cavitation is the noise it generates, often described as a gravelly or rumbling sound. This noise results from the collapsing bubbles and shock waves. In addition to noise, cavitation can cause excessive vibration in the system, which can lead to further mechanical issues if not addressed promptly.
Performance Degradation: Cavitation can lead to a decrease in the efficiency of hydraulic systems. As the vapor bubbles collapse, they disrupt the flow of the liquid, reducing the overall performance of pumps, valves, and other components. This degradation can manifest as a drop in pressure, reduced flow rates, and erratic operation of hydraulic machinery.
Consequences of Cavitation
Erosion and Damage to Components: The collapse of vapor bubbles creates shock waves that can erode metal surfaces and other materials within the hydraulic system. This erosion can lead to pitting and wear on pumps, valves, and other critical components, resulting in costly repairs and replacements.
Reduced System Efficiency: As cavitation disrupts fluid flow and damages components, the overall efficiency of the hydraulic system declines. This inefficiency can lead to increased energy consumption, higher operational costs, and a shorter lifespan for the equipment. In severe cases, cavitation can cause system failures that lead to unscheduled downtime and significant financial losses.
Identifying Flashing in Hydraulic Systems
Definition and Mechanics
Flashing in hydraulic systems refers to the rapid vaporization of liquid as it passes through a region where the pressure drops significantly. This phenomenon occurs when a liquid’s pressure falls below its vapor pressure as it moves through a constriction or restriction in the system, causing a portion of the liquid to flash into vapor. The resulting vapor bubbles can disrupt normal fluid flow, leading to several operational problems.
Flashing typically happens when liquid flows through a narrow passage or an area where the pressure is suddenly reduced. As the pressure drops, the liquid begins to vaporize, creating bubbles. Unlike cavitation, where vapor bubbles collapse violently, flashing involves the creation of vapor bubbles that continue to exist and interact with the fluid. These bubbles can reduce the overall efficiency of the system and cause damage to components over time.
Causes of Flashing
Restriction or Choke Points in the System: Flashing often occurs at points where the flow is restricted or choked, such as narrow pipes, valves, or orifices. When fluid encounters these restrictions, the velocity increases, and the pressure drops significantly. If the pressure drop is substantial enough, the liquid will start to vaporize, leading to flashing.
Sudden Pressure Drops: Rapid or abrupt changes in pressure, such as those caused by sudden valve openings or changes in system load, can also lead to flashing. When the pressure drops too quickly, the liquid’s vapor pressure is exceeded, resulting in vaporization. These sudden drops can be particularly problematic in systems with variable or unpredictable flow conditions.
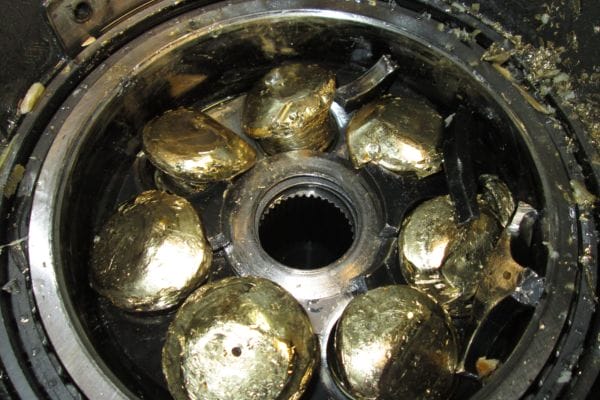
Symptoms of Flashing
Excessive Noise: Flashing can produce a distinct noise that is often described as a high-pitched hissing or bubbling sound. This noise results from the formation and movement of vapor bubbles within the fluid. The intensity and frequency of the noise can vary depending on the severity of the flashing and the system’s operating conditions.
Reduced Flow and Pressure Inconsistencies: Flashing can cause irregularities in flow and pressure throughout the hydraulic system. As vapor bubbles mix with the liquid, they disrupt the normal flow pattern, leading to fluctuations in pressure and reduced overall flow rates. This can manifest as inconsistent system performance and difficulties in maintaining stable operating conditions.
Consequences of Flashing
Erosion and Wear: The presence of vapor bubbles in the fluid can lead to erosion and wear on hydraulic components. As the bubbles move and interact with surfaces, they can cause abrasive damage and material degradation, particularly in areas where the fluid velocity is high. This erosion can affect the longevity and reliability of components such as pumps, valves, and pipes.
Decreased Performance and Reliability: Flashing can significantly impact the performance and reliability of hydraulic systems. The vapor bubbles disrupt the flow and pressure stability, leading to reduced efficiency and potential operational failures. Over time, the wear and damage caused by flashing can result in frequent maintenance needs, increased downtime, and higher operational costs.
Diagnosing Cavitation and Flashing
Diagnosing cavitation and flashing in hydraulic systems is critical to preventing damage and ensuring the system operates efficiently. Early detection allows for timely interventions, reducing the risk of costly repairs and downtime. This section explores the diagnostic tools and techniques used to identify these issues and how to analyze system data to recognize the signs of cavitation and flashing.
Diagnostic Tools and Techniques
Vibration Analysis
Vibration analysis is one of the most effective techniques for diagnosing cavitation and flashing. Cavitation, in particular, generates a distinct vibration signature due to the formation and collapse of vapor bubbles. This vibration is typically characterized by high-frequency noise that can be detected using vibration sensors attached to the system’s components, such as pumps and valves.
The process involves collecting vibration data over time and analyzing it to identify patterns or anomalies that indicate cavitation. For instance, sudden spikes in vibration amplitude, particularly in the high-frequency range, may suggest the presence of cavitation. Similarly, flashing can cause vibration due to the continuous presence of vapor bubbles within the fluid, which disrupts the flow and generates turbulence.
By regularly monitoring vibration levels, operators can detect the early stages of cavitation and flashing and take corrective action before significant damage occurs.
Pressure and Temperature Monitoring
Pressure and temperature monitoring are essential for diagnosing both cavitation and flashing. These phenomena are directly related to changes in pressure and temperature within the hydraulic system, making it crucial to monitor these parameters closely.
Cavitation often occurs when the pressure in a certain part of the system drops below the vapor pressure of the fluid, causing vapor bubbles to form. By installing pressure sensors at key points in the system, such as pump inlets and outlets, operators can monitor pressure levels in real-time. A sudden drop in pressure below the fluid’s vapor pressure is a strong indicator of potential cavitation.
Temperature also plays a critical role, particularly in flashing. As the temperature of the fluid increases, its vapor pressure rises, making it more susceptible to flashing. Monitoring temperature changes in the fluid can help identify conditions that may lead to flashing, especially when the fluid passes through restricted areas where the pressure drops.
Analyzing System Data
Interpreting Performance Metrics
Analyzing system data is key to diagnosing cavitation and flashing accurately. Performance metrics such as flow rate, pressure, temperature, and vibration levels should be continuously monitored and analyzed to identify any deviations from normal operating conditions.
For cavitation, a drop in pump efficiency is a common sign. As cavitation progresses, the pump’s ability to move fluid effectively diminishes, leading to lower flow rates and reduced pressure. By comparing current performance metrics with baseline data (i.e., data collected when the system was known to be operating correctly), operators can identify when cavitation is occurring.
In the case of flashing, performance metrics such as flow consistency and pressure stability are important indicators. Flashing typically leads to fluctuations in flow rates and inconsistent pressure readings, as the presence of vapor bubbles disrupts the fluid flow. These fluctuations can be detected by analyzing trends in the data over time.
Identifying Anomalies and Trends
The key to diagnosing cavitation and flashing lies in identifying anomalies and trends in the system data. Anomalies are sudden, unexpected changes in the data, such as a sharp increase in vibration or a rapid pressure drop. These can indicate that cavitation or flashing is occurring.
Trends, on the other hand, are gradual changes in the data that develop over time. For example, a slow decline in pump efficiency or a gradual increase in system vibration levels may suggest that cavitation is starting to occur. Similarly, a trend of decreasing pressure stability could indicate that flashing is becoming an issue.
Data analysis software and tools can help automate the process of identifying these anomalies and trends. By setting thresholds for key metrics, the system can alert operators to potential issues before they lead to significant damage.
Preventive Measures and Solutions
Design Considerations
Proper System Design to Minimize Cavitation and Flashing
The foundation for preventing cavitation and flashing in hydraulic systems lies in thoughtful and strategic system design. When designing a hydraulic system, engineers must consider the flow dynamics and pressure profiles throughout the system.
To minimize cavitation, it’s crucial to avoid creating low-pressure zones where vapor bubbles can form. This can be achieved by ensuring that the fluid velocity is controlled and that the pressure remains above the liquid’s vapor pressure, even in the most demanding conditions. For example, designing pump inlets and other components with smooth transitions and avoiding sharp bends or abrupt changes in cross-sectional area can help maintain steady pressures and reduce the risk of cavitation.
For flashing, the design should focus on avoiding sudden pressure drops that could cause the liquid to vaporize. This involves carefully selecting the size and type of valves, orifices, and other flow-restricting components to ensure they are appropriate for the system’s operating conditions. Additionally, systems should be designed to handle peak flow rates and pressure variations without exceeding the vapor pressure of the fluid.
Choosing the Right Components and Materials
The selection of components and materials is critical in preventing cavitation and flashing. Components should be chosen based on their ability to withstand the operating conditions of the hydraulic system, including pressure, temperature, and flow rate.
For cavitation prevention, components like pumps and valves should be designed for smooth operation with minimal pressure drops. Materials used in these components should be resistant to the erosive effects of cavitation. Stainless steel, for example, is often preferred for its durability and resistance to pitting and erosion caused by cavitation.
In the case of flashing, materials that are resistant to wear and erosion caused by the continuous presence of vapor bubbles should be selected. Additionally, using components with design features that minimize pressure drops, such as streamlined valve bodies or special orifice designs, can help prevent flashing.
Operational Adjustments
Maintaining Optimal Operating Conditions
Once the system is designed and built, maintaining optimal operating conditions is key to preventing both cavitation and flashing. Operators must ensure that the system operates within the specified pressure and flow rate ranges to avoid conditions that could lead to these issues.
Regularly monitoring fluid levels, pressures, and temperatures is essential. Operators should be vigilant about keeping the pressure in the system above the vapor pressure of the fluid, particularly at pump inlets and other critical points. Adjustments may need to be made to pump speeds, valve positions, or other settings to maintain the correct operating conditions.
Temperature control is also important because fluid temperature directly affects vapor pressure. Keeping the fluid temperature within the recommended range can help prevent both cavitation and flashing. If necessary, cooling systems or heat exchangers can be used to maintain the fluid temperature within safe limits.
Regular Monitoring and Maintenance Practices
Proactive monitoring and maintenance are essential to catch early signs of cavitation and flashing before they cause significant damage. Regular inspections should be conducted to check for unusual noises, vibrations, or pressure fluctuations, which could indicate cavitation or flashing.
Using diagnostic tools such as vibration analysis, pressure sensors, and flow meters can help detect early signs of trouble. For example, installing pressure gauges at critical points in the system can help monitor pressure drops that could lead to cavitation or flashing. If any anomalies are detected, immediate action should be taken to correct the issue.
Preventive maintenance, including regular cleaning and servicing of components, helps ensure that the system remains in optimal condition. Replacing worn parts, such as pump seals or valve seats, before they fail can prevent conditions that might lead to cavitation or flashing.
Upgrades and Modifications
Installing Anti-Cavitation Devices
For systems that are particularly prone to cavitation, installing anti-cavitation devices can be an effective solution. These devices are designed to manage the pressure conditions within the system to prevent the formation of vapor bubbles. One common type of anti-cavitation device is the inducer, which is installed at the pump inlet. Inducers help increase the pressure of the fluid before it enters the pump, reducing the likelihood of cavitation.
Another approach is to use cavitation-resistant pumps that are designed to handle low-pressure conditions without allowing cavitation to occur. These pumps often feature specialized impellers and volutes that effectively manage fluid flow, reducing the chances of pressure drops leading to cavitation.
System Modifications to Prevent Flashing
To prevent flashing, system modifications may be necessary, especially in cases where flashing has been identified as a recurring problem. One effective modification is to redesign or replace flow-restricting components such as valves and orifices with versions that create less pressure drop. For instance, replacing a standard orifice plate with a multi-hole orifice plate can distribute the pressure drop more evenly, reducing the risk of flashing.
Another modification might involve installing pressure-sustaining valves or back-pressure regulators that maintain a minimum pressure in the system, preventing the pressure from dropping to levels that would cause flashing. These devices can be handy in systems with variable flow rates or where pressure fluctuations are common.
Conclusion
Regular maintenance, combined with advanced monitoring technologies, ensures that systems operate within safe parameters, preventing cavitation and flashing from developing into serious issues. By prioritizing these practices, operators can ensure the long-term performance and reliability of their hydraulic fitting systems, minimizing downtime and maximizing efficiency in their operations.
FAQ
What is cavitation in hydraulic systems?
Cavitation occurs when vapor bubbles form in a fluid due to low pressure and then collapse, damaging system components.
What causes flashing in hydraulic systems?
Flashing happens when a liquid rapidly vaporizes due to sudden pressure drops, often caused by restrictions or choke points in the system.
How can I identify cavitation in my hydraulic system?
Symptoms include unusual noise, vibrations, and decreased performance. Vibration analysis and pressure monitoring are key diagnostic tools.
What are the signs of flashing in a hydraulic system?
Excessive noise, reduced flow, and pressure inconsistencies are common indicators. Monitoring system pressure and flow can help detect flashing.
How can I prevent cavitation and flashing?
Proper system design, choosing the right components, maintaining optimal operating conditions, and regular monitoring can help prevent these issues.
What should I do if I detect cavitation or flashing?
Addressing the root causes, such as adjusting operating conditions or upgrading components, and conducting regular maintenance can help mitigate these problems.