Industrial hose assemblies play a critical role in ensuring efficient fluid transfer across multiple industries, from manufacturing and agriculture to oil & gas, chemical processing, and construction. They are essential for maintaining operational safety, boosting productivity, and reducing downtime. These versatile components are designed to handle a wide range of fluids—including air, water, oil, chemicals, and more—under various pressure and temperature conditions.
What are Industrial Hose Assemblies?
Definition
An industrial hose assembly is a comprehensive system designed to facilitate the transfer of a wide range of fluids, gases, and other materials between locations in industrial operations. Unlike standard hoses, industrial hose assemblies are built with specific components that ensure they can handle the demanding conditions of different industrial environments.
The core structure of an industrial hose assembly includes:
Flexible Hose: The main conduit that carries the fluid. These hoses are designed to be versatile and can be made from various materials like rubber, PVC, polyurethane, or Teflon, depending on the application’s requirements for flexibility, chemical resistance, and durability.
Reinforcement Layers: These layers provide the hose with additional strength, enabling it to withstand high pressures and harsh working conditions. Reinforcement can come in the form of braided steel wires, textile layers, or spiral wraps, all of which enhance the assembly’s pressure tolerance and flexibility.
End Fittings: These fittings allow for secure connections to machinery, tanks, pumps, or other equipment. They come in various forms, including cam-and-groove couplings, flanges, or quick disconnects, and are typically made of materials like stainless steel, brass, or composite materials.
Clamps and Sleeves: Additional accessories like clamps and sleeves help maintain the integrity of the connection and protect the hose from external damage.
The integration of these components ensures the hose assembly can endure extreme pressure variations, high temperatures, abrasive materials, and chemical exposure, making it suitable for demanding industrial applications.
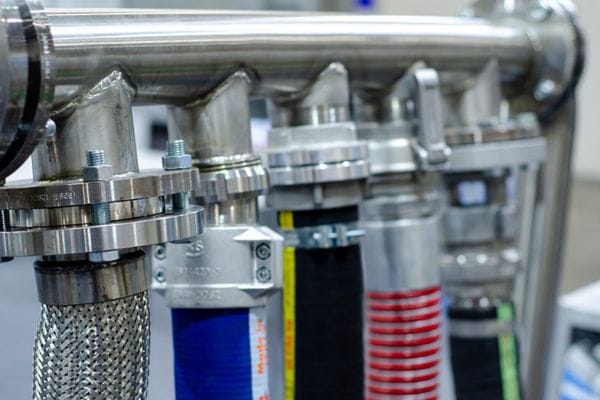
Uses
Industrial hose assemblies are employed in a diverse range of industries due to their ability to adapt to specific needs. Some key applications include:
Manufacturing: In the manufacturing sector, hose assemblies are used to transport coolants, hydraulic fluids, and lubricants that support machinery operations. They play a vital role in the automation of systems, ensuring the seamless movement of fluids required for processes like welding, molding, and cutting.
Chemical Processing: Chemical industries rely on industrial hose assemblies to handle corrosive fluids, acids, and other aggressive chemicals. The hose material and fittings are carefully chosen to ensure chemical compatibility, minimizing the risk of leaks, contamination, or hose degradation.
Oil & Gas: This industry heavily depends on hose assemblies for drilling, extraction, and refining processes. Hoses in this sector are often designed to transfer high-pressure fluids such as crude oil, natural gas, drilling mud, and other petrochemicals. The assemblies must endure high pressures, rugged conditions, and potentially explosive environments.
Food & Beverage: In the food and beverage sector, sanitary hose assemblies are used for transferring consumable products like juices, milk, beer, and oils. These assemblies are made from food-grade materials that ensure hygiene, prevent contamination, and maintain the quality of the products being transported.
Agriculture: Agricultural operations utilize industrial hose assemblies for various purposes, including irrigation, pesticide spraying, and nutrient application. The assemblies help efficiently distribute water and chemicals over large areas, supporting crop growth and protection.
Construction and Mining: In these sectors, hose assemblies are indispensable for conveying air, water, cement, slurry, and other materials essential for drilling, tunneling, and construction operations. Due to harsh working conditions, these hoses need to be extremely rugged, abrasion-resistant, and able to handle fluctuating pressures.
Importance
Industrial hose assemblies are vital components in ensuring operational efficiency, safety, and reliability. Their importance extends beyond simply transporting fluids; they are critical to maintaining smooth operations across a range of industries. Here’s why:
Safe Handling of Hazardous Materials: Many industries deal with hazardous materials that can pose risks to workers and the environment if not managed properly. Well-designed hose assemblies prevent leaks and spills, ensuring a safe working environment and compliance with environmental regulations.
Consistent Flow Rates: In any process that involves fluid transfer, maintaining consistent flow rates is essential for optimal performance. Industrial hose assemblies, when chosen and installed correctly, ensure that fluids are delivered consistently, preventing downtime and production losses.
Reduced Maintenance Costs: High-quality hose assemblies built from durable materials are more resistant to wear and tear, extending their lifespan and reducing the need for frequent repairs or replacements. This reliability minimizes maintenance costs and ensures more efficient use of resources.
Adaptability to Different Conditions: Industrial hose assemblies can be customized for specific conditions, such as high pressure, extreme temperatures, chemical exposure, or abrasive materials. This adaptability makes them indispensable in applications where conditions can vary widely.
Main Components of Industrial Hose Assemblies
Hose Tube
The hose tube is the innermost layer of the industrial hose assemblies, responsible for carrying the fluids or gases safely from one point to another. Its material composition significantly influences the assembly’s performance, durability, and resistance to various chemicals, temperatures, and pressures.
Material Types:
Rubber (e.g., EPDM, nitrile, butyl): Rubber is commonly used for its flexibility, elasticity, and resistance to abrasion, oils, and chemicals. EPDM is suited for handling water, air, and certain chemicals, while nitrile is ideal for transporting petroleum-based fluids. Butyl is often used for gas and water applications.
PVC (Polyvinyl Chloride): PVC is widely used due to its affordability, lightweight nature, and good resistance to chemicals and weathering. It’s commonly used in low to medium-pressure applications like irrigation, chemical transfer, and food processing.
Teflon (PTFE): Teflon hoses offer exceptional chemical resistance, making them suitable for transporting highly corrosive fluids. They have excellent temperature resistance and are often used in chemical, pharmaceutical, and food processing applications.
Polyurethane (PU): Known for its high abrasion resistance and flexibility, polyurethane hoses are used for conveying abrasive materials, such as sand, gravel, and other bulk solids, making them common in material handling and mining industries.
Properties:
Chemical Resistance: Ensures that the tube material can withstand the transported fluids without degradation or corrosion.
Flexibility: A flexible tube enables easier installation, handling, and routing in confined spaces.
Durability: The tube material should endure wear and tear, reducing the risk of rupture or leaks during operation.
Applications:
Rubber hoses: Used in oil & gas, water handling, and chemical processing.
PVC hoses: Common in agriculture, food processing, and light chemical transfer.
Teflon hoses: Suitable for corrosive chemical transfer, high-temperature applications, and pharmaceutical processes.
Polyurethane hoses: Used in material handling, mining, and bulk transportation of abrasive materials.
Reinforcement Layers
Reinforcement layers provide strength to the hose assembly, enabling it to withstand internal pressure, maintain structural integrity, and enhance the hose’s flexibility and resistance to kinking.
Purpose:
The main role of reinforcement is to strengthen the hose and allow it to handle higher pressures without bursting or deforming. It also helps maintain the hose’s shape, ensuring consistent flow and performance.
Types of Reinforcements:
Textile Layers (Fabric/Braided): These reinforcements are typically made from synthetic fibers (e.g., polyester, nylon) and are used in applications where moderate pressure resistance is needed. Textile-reinforced hoses are lightweight, flexible, and ideal for water and air handling.
Steel Wire Braid/Spiral: Steel wire braid or spiral reinforcement provides high-pressure resistance, making hoses suitable for hydraulic systems and other applications that demand high strength. Braided hoses offer more flexibility, while spiral hoses are more robust, handling higher pressures.
Composite Layers: Composed of multiple materials, such as metal, fabric, and plastic film, composite reinforcements offer a balance of flexibility, chemical resistance, and pressure tolerance. They are used in chemical transfer and petroleum handling applications.
Performance Factors:
Pressure Tolerance: Reinforcement layers directly impact the hose’s pressure rating, determining how much pressure it can withstand.
Flexibility vs. Rigidity: The type and number of reinforcement layers influence the hose’s flexibility. For instance, single-layer braided reinforcement offers more flexibility than multi-layer spirals, which provide more rigidity and higher pressure resistance.
Outer Cover
The outer cover of the hose assembly serves as the protective layer, shielding the inner tube and reinforcement from environmental hazards, mechanical abrasion, and chemical exposure.
Functions:
The outer cover protects against abrasion, chemicals, oils, weathering, and other external factors that could compromise the hose’s integrity. It acts as a first line of defense against potential damage, extending the hose’s lifespan.
Material Options:
Nitrile: Known for its oil and chemical resistance, nitrile is commonly used in fuel transfer hoses.
Neoprene: Offers good weather resistance, making it suitable for outdoor use in various industrial applications.
Polyurethane: Known for its superior abrasion resistance, polyurethane is used in hoses for material handling, construction, and mining applications.
Resistance Properties:
Abrasion Resistance: The cover material should withstand wear caused by dragging or contact with rough surfaces.
Weather Resistance: UV rays, ozone, and moisture should not degrade the outer cover.
Chemical Resistance: The cover should resist chemical splashes or exposure to prevent degradation.
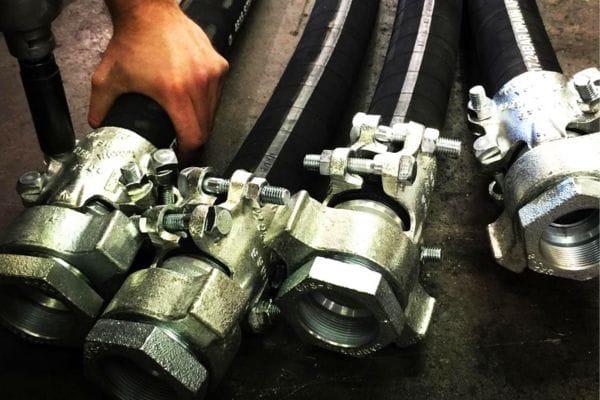
End Fittings
End fittings are components that connect the hose to other equipment, such as pumps, tanks, or valves. They are critical for ensuring a secure and leak-free connection.
Purpose:
Fittings allow hoses to be connected to machinery, tanks, valves, and other equipment. They ensure a tight seal, preventing leaks and ensuring safe fluid transfer.
Types:
Cam-and-Groove Couplings: Quick-connect fittings that allow for easy attachment and detachment, commonly used in industries like petroleum and chemical handling.
Flange Connections: Provide a strong, leak-proof seal and are often used in high-pressure applications such as oil & gas.
Quick-Release Couplings: Designed for rapid connection and disconnection, ideal for applications requiring frequent hose changes.
Threaded Fittings: Common in general industrial and hydraulic applications where a secure, threaded connection is needed.
Material Considerations:
Stainless Steel: Offers high corrosion resistance and is suitable for food, pharmaceutical, and chemical applications.
Brass: Ideal for low to medium-pressure applications, particularly in water and air systems.
Plastic (e.g., PVC, Nylon): Used in low-pressure applications, offering lightweight and corrosion resistance.
Clamps and Sleeves
Clamps and sleeves are additional accessories that ensure the hose assembly remains secure and functions effectively without leaks or disconnects.
Function:
Clamps and sleeves provide extra security to the connection points, preventing leaks, hose slippage, or disconnection under pressure. They help maintain a consistent seal, ensuring the hose assembly operates safely.
Types and Selection:
Worm Gear Clamps: Common for low to medium-pressure applications, providing a secure fit around the hose.
T-Bolt Clamps: Offer high strength and are used in high-pressure applications where robust security is needed.
Sleeve Clamps: Used for applications requiring extra protection or reinforcement at the hose ends, preventing excessive bending or wear.
Selection Criteria:
Clamps and sleeves are selected based on hose size, pressure rating, and application needs. For instance, high-pressure applications require heavy-duty clamps like T-bolt or double-bolt clamps to maintain a secure seal.
Factors to Consider When Choosing Components
When selecting components for industrial hose assemblies, it’s critical to consider several key factors that directly influence the performance, safety, and longevity of the assembly. Each of these factors should align with the specific application requirements to ensure efficiency and reliability.
Chemical Compatibility
Importance:
One of the primary considerations when choosing hose components is the compatibility of materials with the fluids being transferred. Industrial hose assemblies often handle a wide range of chemicals, oils, acids, and other substances that can degrade or damage the hose tube, reinforcement, or fittings if they are not chemically compatible.
Selecting Compatible Materials:
Hose Tube: For handling corrosive chemicals, materials like Teflon (PTFE) or EPDM are often used due to their broad chemical resistance. For petroleum-based fluids, nitrile is generally preferred. Similarly, PVC can handle many general chemicals but may not be suitable for highly concentrated acids or solvents.
End Fittings: The fittings must also be made from materials that resist corrosion and chemical reactions with the fluids. Stainless steel is widely used in chemical applications for its corrosion resistance, while brass may be suitable for less aggressive fluids.
Failure Risks: If incompatible materials are chosen, the hose can degrade prematurely, leading to leaks, contamination, or even failure of the assembly. This can pose safety risks, result in environmental hazards, and cause costly downtime.
Temperature Range
Effect on Hose Performance:
Temperature plays a critical role in determining the durability and performance of the hose assembly. Hoses exposed to extreme temperatures—either high or low—must be made of materials that can withstand these conditions without degrading.
High Temperatures: Exposure to high temperatures can lead to the softening or melting of the hose material, weakening the structure and reducing pressure resistance. For high-temperature applications, materials like Teflon, silicone, or Viton are often used due to their heat resistance.
Low Temperatures: Cold temperatures can cause some materials to become brittle and prone to cracking. Materials like EPDM and neoprene maintain flexibility and integrity in colder environments, making them ideal for applications in freezing conditions.
Need for Temperature-Resistant Materials:
The selected hose must have a temperature range that exceeds the expected temperature of the fluids or the ambient conditions. For instance, in the chemical industry, where hot acids are transported, a high-temperature-resistant material like PTFE is essential to maintain safety and performance.
Pressure Rating
Influence on Reinforcement and Structure:
Pressure ratings are among the most important criteria for choosing the right hose and reinforcement type. The pressure of the fluid being transferred, along with the potential for sudden pressure spikes, determines the level and type of reinforcement required.
Low to Medium Pressure: Hoses with textile reinforcement are often suitable for low to medium pressure applications, such as water transfer or general chemical handling. These hoses offer good flexibility while still handling moderate pressures.
High Pressure: For high-pressure applications, such as hydraulics or high-pressure water blasting, hoses must have steel wire braid or spiral reinforcement to withstand the stress. Multiple layers of spiral steel reinforcement provide the necessary strength to handle pressures up to several thousand PSI.
Pressure Fluctuations: In applications with sudden pressure changes, the hose should have additional safety margins in its pressure rating to prevent bursting or hose failure.
Flexibility vs. Rigidity
Flexible Hoses:
Pros:
Flexible hoses are easier to route, install, and handle in tight or confined spaces. They offer better maneuverability, making them ideal for applications that require frequent hose movement or where hoses need to adapt to changes in alignment.
They also reduce the risk of hose kinking, which can obstruct fluid flow and compromise performance.
Cons:
Flexible hoses generally have a lower pressure rating compared to rigid hoses. They may also wear more quickly in abrasive environments because of their ability to bend and move, increasing surface wear.
Applications:
Flexible hoses are commonly used in chemical transfer, food and beverage processing, and hydraulic systems where hose movement or adjustments are frequent.
Rigid Hoses:
Pros:
Rigid hoses offer greater strength and durability, making them suitable for high-pressure applications. Their robust design ensures consistent flow rates and minimal risk of kinking.
Cons:
Rigid hoses can be challenging to install and route, particularly in spaces with limited access. They require more precise alignment and may not adapt well to changes in positioning.
Applications:
These hoses are often used in high-pressure hydraulic systems, fixed installations in manufacturing plants, and other settings where steady, straight fluid transfer is required.
Conclusion
Now is a good time to evaluate your current hose assemblies. Are they meeting your operational needs effectively? Are there signs of wear, leaks, or performance issues? Upgrading components tailored to your specific requirements can improve performance, enhance safety, and reduce downtime. Consider consulting with a hose assembly expert to ensure optimal selection and installation, resulting in longer-lasting, more reliable assemblies.
FAQ
What are industrial hose assemblies?
Industrial hose assemblies are a complete system made up of a flexible hose, reinforcement layers, end fittings, and other accessories, designed to transport fluids, gases, or other materials in industrial settings.
How do I choose the right hose material?
Select hose material based on chemical compatibility, temperature range, and the specific fluid being transferred. Materials like rubber, PVC, or Teflon are commonly used, each suited to different fluids and conditions.
What are the main types of hose reinforcements?
The main reinforcement types include textile layers, steel wire braid/spiral, and composite layers. The choice depends on the pressure requirements and application needs.
Why is chemical compatibility important in hose assemblies?
Using incompatible materials can lead to hose degradation, leaks, or failure, which can pose safety risks and damage equipment. Always ensure that the hose materials are suited for the specific fluids being transported.
How often should industrial hoses be inspected?
Regular inspection is recommended, ideally every 3-6 months or as needed, to check for signs of wear, leaks, or damage. Proper maintenance can extend the hose’s lifespan and ensure safety.
When should I replace my industrial hose assembly?
Replace the hose assembly if you notice leaks, cracks, corrosion, or decreased performance. Regular wear and tear, especially in high-pressure or chemical applications, often indicates the need for replacement.