ISO 8434-3 is a key international standard that outlines the specifications and requirements for O-ring face seal connectors, primarily used in hydraulic systems. This standard, also known as SAE J453, focuses on ensuring the reliable and leakproof connection of tubes and hoses with diameters ranging from 6 mm to 38 mm. By detailing the design, material, and performance requirements, ISO 8434-3 aims to enhance the safety and efficiency of fluid power applications across various industries.
Understanding ISO 8434-3
Explanation of the Standard and Its History
ISO 8434-3 is part of a broader series of standards that define requirements for various types of hydraulic connectors. Established to promote safety and reliability in hydraulic systems, this standard specifically addresses O-ring face seal connectors. Its origins can be traced back to the need for standardized fittings in the growing fluid power industry, where variations in design and materials often led to compatibility issues and leakage problems.
The standard was developed by the International Organization for Standardization (ISO) and has evolved over the years to incorporate advances in materials science and engineering practices. By providing detailed specifications for connector dimensions, materials, and performance requirements, ISO 8434-3 ensures that O-ring face seal fittings can withstand the demanding conditions often encountered in hydraulic applications.
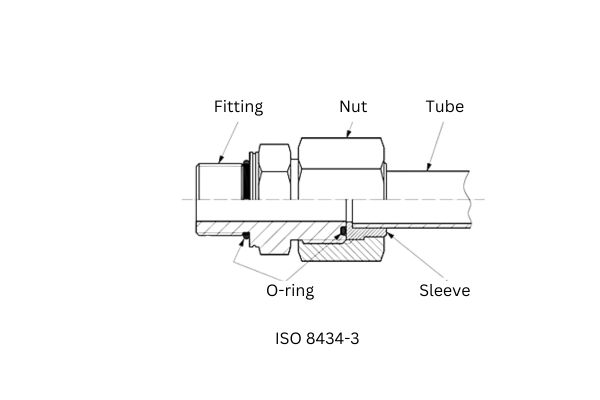
Comparison with Other Relevant Standards (e.g., SAE J453)
ISO 8434-3 is closely related to SAE J453, which outlines similar requirements for O-ring face seal connectors but is specific to the American context. While both standards aim to guide the design and performance of these connectors, there are subtle differences in measurement units and testing methods due to regional preferences.
For instance, ISO standards primarily use the metric system, while SAE standards favor imperial measurements. This distinction can affect manufacturing processes and compatibility in global supply chains. Understanding these differences is crucial for manufacturers and users who operate in international markets or who utilize equipment designed to comply with both standards.
Scope and Applications of ISO 8434-3 Threads
The scope of ISO 8434-3 encompasses the design and performance of O-ring face seal connectors made from stainless steel or carbon steel, applicable to tube outside diameters or hose inside diameters ranging from 6 mm to 38 mm. These connectors are suitable for a variety of fluid power applications where elastomeric seals are employed to prevent leakage.
ISO 8434-3 connectors are widely used across numerous industries, including automotive, aerospace, manufacturing, and construction. In hydraulic systems, they provide secure, leakproof connections that enhance system efficiency and safety. Applications range from heavy machinery and agricultural equipment to automotive hydraulic lines and industrial fluid transfer systems.
The versatility of O-ring face seal fittings makes them ideal for both high-pressure and low-pressure systems, and their design accommodates variations in assembly procedures. This adaptability allows engineers to select the most appropriate connector for their specific applications, further underscoring the importance of adhering to ISO 8434-3 standards.
Design and Dimensional Requirements
Detailed Specifications for O-Ring Face Seal Connectors
O-ring face seal connectors are critical components in hydraulic systems, and ISO 8434-3 provides comprehensive specifications to ensure their effective performance. These connectors are designed to provide a reliable, leakproof seal while allowing for easy assembly and disassembly. The design incorporates a flat face that serves as a sealing surface for the O-ring, creating a tight seal when the connector is tightened.
The standard outlines several key aspects of the connector design:
Sealing Geometry: The O-ring is seated in a precisely machined groove, ensuring consistent compression and contact with the flat face of the mating part. This geometry is crucial for maintaining the integrity of the seal under varying pressure and temperature conditions.
Pressure Ratings: The connectors are designed to handle a range of pressures, ensuring safe operation in both low and high-pressure applications. Specific pressure ratings are determined based on the materials used and the connector dimensions.
Assembly Features: The connectors are engineered for ease of assembly, typically featuring threaded ends or welded sleeves that facilitate secure connections. This design reduces the risk of leakage caused by misalignment during installation.
Dimensions and Tolerances for Tubes and Hoses (6 mm to 38 mm)
ISO 8434-3 specifies exact dimensions and tolerances for O-ring face seal connectors, ensuring compatibility across various applications. The standard covers connectors suitable for tube outside diameters (OD) and hose inside diameters (ID) ranging from 6 mm to 38 mm.
Standard Dimensions: The dimensions of the connectors are defined in a series of tables within the standard. These tables detail the specific measurements for the O-ring grooves, sealing surfaces, and overall connector length. For example, the groove dimensions must be within specified tolerances to ensure proper O-ring seating and function.
Tolerances: Tolerances are critical to maintaining the performance of the connectors. ISO 8434-3 specifies allowable deviations in dimensions to ensure a proper fit. These tolerances account for variations in manufacturing processes and help to guarantee that connectors will function correctly in real-world applications.
Compatibility: By adhering to these dimensional specifications, manufacturers ensure that O-ring face seal connectors can be used interchangeably in various systems. This interoperability is essential for maintenance and repair operations, where components from different manufacturers may need to be combined.
Materials Used (Stainless Steel vs. Carbon Steel)
The choice of material for O-ring face seal connectors significantly impacts their performance and durability. ISO 8434-3 permits the use of both stainless steel and carbon steel, each offering unique advantages and considerations.
Stainless Steel:
Corrosion Resistance: Stainless steel connectors are highly resistant to corrosion, making them suitable for applications involving aggressive fluids or environments where moisture and corrosive agents are present.
Strength and Durability: They maintain structural integrity under high pressure and temperature conditions, ensuring long-term reliability in demanding applications.
Cost: While more expensive than carbon steel, the longevity and reduced maintenance needs of stainless steel connectors often justify the higher initial investment.
Carbon Steel:
Cost-Effectiveness: Carbon steel connectors are generally less expensive to produce, making them a cost-effective choice for applications where environmental conditions are not as harsh.
Strength: They offer good mechanical strength and performance but may require additional protective coatings or treatments to enhance their corrosion resistance.
Applications: Carbon steel connectors are typically used in less demanding environments where exposure to corrosive substances is minimal, ensuring adequate performance without the added cost of stainless steel.
Performance Characteristics
Pressure and Temperature Requirements
One of the primary considerations in the design of O-ring face seal connectors per ISO 8434-3 is their ability to withstand varying pressure and temperature conditions. The standard specifies a range of operational pressures, typically from vacuum conditions of 6.5 kPa (0.065 bar) to high working pressures, which can vary depending on the specific connector design and materials used.
Pressure Ratings: Each connector type comes with defined pressure ratings that indicate its maximum allowable working pressure (MAWP). These ratings are determined through rigorous testing and depend on factors such as the connector’s diameter, material, and the type of sealing element used. Users should always refer to the manufacturer’s specifications to ensure they are within safe operating limits.
Temperature Range: The temperature requirements are equally critical, as hydraulic systems often operate under extreme conditions. ISO 8434-3 connectors are designed to function effectively within specified temperature ranges, typically from -40°C to +100°C, with some connectors capable of operating at even higher temperatures depending on the materials employed. Users need to select connectors that match the specific temperature profiles of their applications to prevent seal degradation or failure.
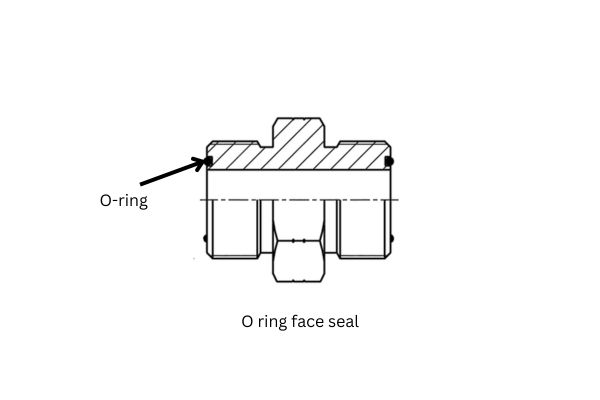
Leakproof Capabilities and Flow Characteristics
Leakage prevention is one of the standout features of O-ring face seal connectors. The design allows for a robust sealing mechanism that minimizes the risk of fluid leakage, which is crucial in maintaining system efficiency and safety.
Sealing Mechanism: The O-ring, when compressed against the flat face of the connector, creates a seal that is less susceptible to leakage compared to other types of fittings. The geometry of the connector promotes even distribution of sealing pressure, which enhances its leakproof capabilities.
Flow Characteristics: In addition to preventing leaks, ISO 8434-3 connectors are designed to maintain optimal flow characteristics. Their smooth internal surfaces reduce turbulence and pressure drops, ensuring efficient fluid transfer. This characteristic is particularly important in hydraulic applications where maintaining flow rates is critical for system performance.
Testing for Leakage: Manufacturers typically perform rigorous testing, including pressure testing and leak detection, to ensure that connectors meet the specified leakproof criteria. These tests simulate real-world conditions to validate that the connectors can maintain their integrity over time.
Factors Influencing Performance in Real-World Applications
While ISO 8434-3 connectors are designed with high performance in mind, several external factors can influence their effectiveness in real-world applications.
Installation Practices: Proper installation is crucial for the performance of O-ring face seal connectors. Misalignment, over-tightening, or under-tightening can compromise the integrity of the seal, leading to leaks or premature failure. Following the manufacturer’s installation guidelines is essential for ensuring optimal performance.
Material Compatibility: The choice of materials used in conjunction with O-ring face seal connectors can significantly impact their performance. For example, using incompatible fluids or extreme temperatures can lead to chemical degradation of the O-ring material, resulting in leaks. Therefore, it’s essential to select materials that are compatible with the fluids being conveyed.
Environmental Conditions: External environmental factors, such as exposure to chemicals, moisture, and temperature fluctuations, can also affect the performance of the connectors. Regular maintenance and inspection are recommended to identify potential issues early and ensure long-term reliability.
System Design: The overall design of the hydraulic system, including the routing of hoses and tubes, can influence the performance of O-ring face seal connectors. Systems that minimize sharp bends, excessive vibrations, and thermal expansion can help maintain connector integrity.
Applications and Usage
ISO 8434-3 O-ring face seal connectors find applications across a wide range of industries, including:
Automotive: In vehicles, these connectors are used in hydraulic systems for brakes, steering, and suspension, ensuring reliable performance under varying pressures and temperatures.
Industrial Machinery: Many manufacturing and construction machines utilize ISO 8434-3 connectors to maintain efficient hydraulic operations, such as in excavators and forklifts.
Aerospace: The aerospace industry employs these connectors for fluid systems that require lightweight and leakproof solutions, ensuring safety and performance in flight.
Marine: In marine applications, the connectors are crucial for hydraulic steering systems and other fluid power applications exposed to harsh environments.
These connectors are particularly valuable in scenarios where leak prevention is critical, as even small leaks can lead to significant operational issues or environmental concerns.
Benefits of Using O-Ring Face Seal Fittings in Fluid Power Systems
Utilizing ISO 8434-3 O-ring face seal fittings in fluid power systems offers several benefits:
Leak Resistance: The design minimizes leakage, which is essential for maintaining system efficiency and reducing maintenance costs.
Versatility: These connectors accommodate both metric and inch tubing, making them adaptable for various applications and industries.
Ease of Installation: The user-friendly design facilitates quick and easy installation and disassembly, reducing downtime during maintenance or repairs.
Robust Performance: Built to withstand high pressures and temperatures, O-ring face seal connectors offer reliable performance in demanding environments.
Installation and Maintenance
Best Practices for Installing ISO 8434-3 Connectors
Installing ISO 8434-3 O-ring face seal connectors requires careful attention to detail to ensure optimal performance. Here are some best practices:
Clean Surfaces: Before installation, thoroughly clean the mating surfaces of both the connector and the port. Remove any debris, dirt, or old seal material to prevent contamination that could lead to leaks.
Check O-Ring Condition: Inspect the O-ring for any signs of wear, cracks, or deformation. Use only new, compatible O-rings that meet the specified material requirements for the application, ensuring a tight seal.
Proper Alignment: Align the connector accurately with the port before tightening. Misalignment can lead to uneven pressure on the O-ring, resulting in seal failure. Use guide pins or other alignment tools if necessary.
Torque Specifications: Follow the manufacturer’s torque specifications during installation. Over-tightening can damage the O-ring or connector, while under-tightening can lead to leaks. Use a calibrated torque wrench to achieve the correct torque.
Test After Installation: Once installed, conduct a pressure test to check for leaks. Monitor the system closely during initial operation to ensure that the connections are secure.
Common Installation Mistakes and How to Avoid Them
Several common mistakes can compromise the effectiveness of ISO 8434-3 connectors. Here’s how to avoid them:
Ignoring Manufacturer Guidelines: Failing to adhere to the manufacturer’s installation guidelines can lead to improper sealing. Always consult the technical documentation specific to the connector being used.
Using Incorrect Tools: Using inappropriate tools for installation can result in damage to the connector or the O-ring. Ensure that the right tools, such as torque wrenches and alignment fixtures, are used.
Neglecting Environmental Factors: Ignoring the operating environment can lead to premature failure. Be aware of temperature and pressure variations and select connectors that are suitable for the specific conditions.
Reusing Old O-rings: Reusing O-rings from previous installations can compromise sealing effectiveness. Always use new O-rings to ensure reliable performance.
Maintenance Tips to Ensure Longevity and Reliability
Regular maintenance is essential to ensure the longevity and reliability of ISO 8434-3 connectors:
Routine Inspections: Periodically inspect connectors for signs of wear, corrosion, or damage. Look for any fluid leaks around the connection points, which may indicate a failing seal.
Cleaning: Keep the connectors clean and free of debris. Accumulation of dirt or contaminants can lead to corrosion and failure of the sealing surface.
Monitor Operating Conditions: Regularly monitor the operating pressure and temperature of the system. Ensure that they remain within the specifications defined by ISO 8434-3 to avoid stressing the connectors.
Replace Worn Components: At the first sign of wear or degradation, replace O-rings and connectors. Proactive replacement can prevent unexpected failures and costly downtime.
Conclusion
In this guide, we explored the critical aspects of ISO 8434-3 O-ring face seal connectors, including their specifications, performance characteristics, applications, and best practices for installation and maintenance. We emphasized the importance of understanding the standard to ensure reliable, leakproof connections in various hydraulic systems, from automotive to industrial machinery. Adhering to ISO 8434-3 standards is not just a matter of compliance; it significantly enhances system efficiency, safety, and longevity.
FAQ
What is ISO 8434-3?
ISO 8434-3 is a standard that specifies the requirements for O-ring face seal connectors used in hydraulic systems, ensuring leakproof connections.
What sizes do ISO 8434-3 connectors come in?
These connectors are designed for tube outside diameters and hose inside diameters ranging from 6 mm to 38 mm.
What materials are used for ISO 8434-3 connectors?
Connectors are typically made from stainless steel or carbon steel, chosen based on the application’s pressure and temperature requirements.
How do I install ISO 8434-3 connectors properly?
Ensure clean surfaces, check O-ring condition, align the connectors, follow torque specifications, and conduct a pressure test after installation.
What are the advantages of using O-ring face seal fittings?
Benefits include leak resistance, versatility for metric and inch tubing, ease of installation, and robust performance under varying conditions.
Where are ISO 8434-3 connectors commonly used?
These connectors are widely used in industries such as automotive, industrial machinery, aerospace, and marine applications.