NPT thread specifications define the geometry, tolerances, and angle of the threads used in various types of pipe fittings. NPT threads are tapered, meaning the threads become tighter as the connection is made. This tapered design plays a key role in preventing leaks by creating a natural seal between the male and female threads.
Key Features of NPT Thread Specifications
Understanding the key features of NPT thread specifications is essential to ensure proper application, fitting, and sealing. These specifications are carefully designed to meet the needs of a wide range of plumbing, gas, hydraulic, and industrial systems. Here’s a breakdown of the critical aspects of NPT threads:
Tapered Design of NPT Threads
One of the defining characteristics of NPT threads is their tapered design. This means the diameter of the thread decreases along the length of the pipe fitting, creating a self-sealing connection. As the male and female parts are tightened, the threads compress against each other, forming a tight seal. This tapered design helps NPT threads provide a leak-proof connection, even in high-pressure systems. The tapering is what makes NPT fittings distinct from straight-threaded connections, ensuring that they form a reliable and secure bond without the need for additional sealing materials in low to moderate-pressure applications.
Thread Pitch: How it Affects Fit and Sealing
Thread pitch refers to the distance between each thread on the fitting. The pitch of NPT threads is standardized to ensure consistency and compatibility between different fittings. The coarse pitch of NPT threads is designed to create a tighter fit, which is essential for ensuring a good seal. A consistent thread pitch allows the fitting to engage properly, preventing gaps and leaks. In applications where precise sealing is critical, such as in gas or hydraulic systems, the correct thread pitch ensures that the fitting can withstand the pressure and maintain its seal under various conditions.
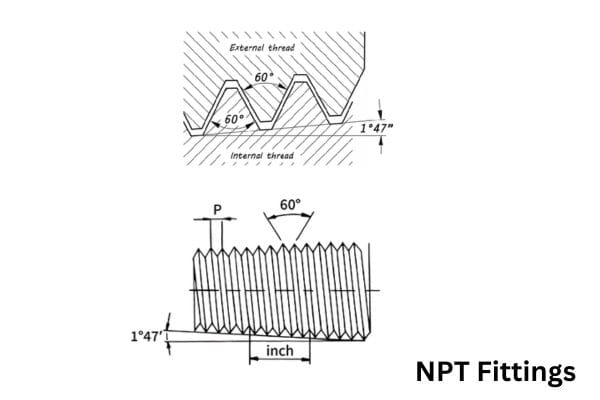
NPT Thread Angle: The 60-Degree Standard
The NPT thread angle is set at a precise 60 degrees, which is a critical factor in achieving the correct fit. This standardized angle ensures that the threads will engage uniformly and form a consistent, leak-resistant connection when the fitting is tightened. The 60-degree angle is designed to balance the pressure applied across the threads and allow for an even distribution of force when connecting fittings, preventing thread damage or slippage. This specific angle is one of the reasons NPT threads have become a universal standard in many industries, ensuring compatibility and consistency across different manufacturers.
NPT Thread Profile: Sharp vs. Rounded Threads
The NPT thread profile typically features sharp-edged threads, which are designed to grip tightly and create a secure seal when they are tightened. This sharp profile ensures that the threads engage securely and form a solid connection, especially when a sealing compound like PTFE tape is used. However, some fittings might also have a slightly rounded thread profile, which can help reduce the risk of cross-threading or damaging the fitting during installation. While the sharp profile is more common in standard NPT fittings, understanding the subtle differences in thread profiles can be important when selecting the right fitting for specific applications.
NPT Thread Geometry: What Sets It Apart
NPT thread geometry is a combination of the thread’s tapered shape, pitch, angle, and profile, which work together to form a highly effective sealing mechanism. The geometry of NPT threads allows them to engage tightly, even under pressure, without the need for additional sealing methods in many applications. This geometric design, along with the 60-degree angle, helps to distribute the force applied during tightening, ensuring the fitting remains secure and leak-free. NPT’s geometry is specifically designed to prevent slippage, reduce the risk of thread damage, and maintain the integrity of the system under a variety of pressures and conditions.
In summary, the key features of NPT thread specifications—tapered design, thread pitch, 60-degree angle, sharp or rounded thread profile, and thread geometry—work together to provide a reliable, durable, and effective sealing solution for a wide range of industrial and plumbing systems. Understanding these features is critical for selecting the right fittings and ensuring your systems are leak-proof and efficient.
NPT Thread Standards: An Overview
NPT (National Pipe Tapered) threads are one of the most widely used thread types in plumbing, gas, hydraulic, and industrial systems. Their design and specifications are governed by a set of standards that ensure consistent and reliable performance across various applications.
The Origin and Development of NPT Thread Standards
The NPT thread system originated in the United States during the late 19th and early 20th centuries. Prior to standardized threads, various pipe fittings used inconsistent thread designs, which led to leaks, system failures, and inefficiencies. To address this issue, the American National Standards Institute (ANSI) and the American Society of Mechanical Engineers (ASME) played pivotal roles in establishing uniform standards for pipe threads.
The first formal standard for NPT threads was developed by the American National Standards Institute (ANSI) in the 1930s. The goal was to create a standardized system for threaded connections that could be used in a variety of applications, ranging from water and gas pipelines to industrial machinery. The specifications focused on creating tapered threads that would create a self-sealing connection as the fitting was tightened, minimizing the need for external sealing materials.
ANSI and ASME Standards for NPT Threads
The ANSI and ASME are the two primary organizations responsible for defining the specifications and standards for NPT threads:
ANSI Standards: The American National Standards Institute (ANSI) provides the overarching framework for NPT thread standards. ANSI ensures that NPT threads are uniform in size, pitch, angle, and taper. The ANSI specification ensures that NPT threads can be used consistently across various applications and industries, promoting compatibility between manufacturers and systems.
ASME Standards: The American Society of Mechanical Engineers (ASME) also plays a critical role in NPT thread standards. ASME defines specific guidelines for the design, testing, and performance of NPT threaded connections. ASME’s guidelines ensure that NPT threads meet the necessary pressure ratings, tolerance levels, and sealing performance to be reliable in both low- and high-pressure systems.
Together, ANSI and ASME standards ensure that NPT threads are suitable for a wide range of uses, from residential plumbing to high-pressure industrial applications.
International Recognition of NPT Standards
While NPT threads were developed in the United States, they have gained international recognition and are widely used in many countries. However, not all countries follow the NPT standard, and some use their own national or international thread standards, such as BSPT (British Standard Pipe Tapered) threads or Metric threads.
Despite this, NPT threads are still the dominant choice in North America, Canada, and many global industries. In addition to their widespread use in plumbing systems and industrial applications, NPT threads are recognized for their ability to provide leak-proof seals under a variety of pressure conditions, making them critical for oil and gas, hydraulic, and chemical processing industries worldwide.
In many cases, NPT thread fittings are interchangeable with other pipe thread standards using adaptors, allowing international systems to integrate with U.S. pipe systems. However, compatibility issues can arise between NPT and other threads like BSPT, and careful attention is required when selecting fittings for international applications.
NPT Thread vs Other Thread Standards (BSPT, NPTF)
When working with threaded connections, it’s important to understand how NPT compares to other thread standards, such as BSPT (British Standard Pipe Tapered) and NPTF (National Pipe Tapered Fuel). Here’s a quick comparison:
NPT vs BSPT:
Thread Angle: NPT threads use a 60-degree thread angle, while BSPT threads use a 55-degree angle. This slight difference in angle makes NPT and BSPT threads incompatible, meaning they cannot be screwed together to form a proper seal.
Thread Geometry: NPT threads have a slightly rounded peak and valley, while BSPT threads have flatter peaks. This structural difference can prevent a tight seal if NPT and BSPT threads are mixed.
Applications: NPT is predominantly used in North America, whereas BSPT is used in the UK and countries with British-influenced standards, such as Australia and parts of Asia.
NPT vs NPTF:
Design: NPTF (National Pipe Tapered Fuel) threads are a specialized version of NPT designed for fuel systems and high-pressure applications. NPTF threads feature a metal-to-metal seal that does not require additional sealants. In contrast, NPT threads rely on sealants such as Teflon tape or pipe thread compound for sealing.
Usage: NPTF threads are used in situations that demand higher sealing performance, such as fuel lines, hydraulic systems, and gas pipelines. NPT threads are more common in general plumbing and low-pressure systems.
Compatibility: NPT and NPTF threads are often confused due to their similar appearance, but they are not interchangeable. The design differences in the sealing mechanism make them unsuitable for swapping.
NPT Fitting Sizes and Dimensions
Understanding the sizes and dimensions of NPT fittings is essential for ensuring compatibility, proper installation, and leak-proof connections. Since NPT threads are commonly used in a variety of applications, ranging from plumbing systems to hydraulic and industrial applications, knowing how to select the correct size and how to measure NPT threads is crucial.
Common NPT Thread Sizes for Pipe Fittings
NPT fittings are available in a range of sizes to accommodate various pipe diameters and system requirements. Some of the most common NPT thread sizes include:
1/8-inch NPT: Often used in small pipes and tubing, 1/8-inch NPT is common in low-pressure systems such as small hydraulic equipment and pneumatic systems.
1/4-inch NPT: This size is frequently found in plumbing systems, airlines, and automotive fuel lines, where smaller diameter fittings are required.
1/2-inch NPT: One of the most common sizes used in water plumbing, gas lines, and hydraulic fittings. It is ideal for medium-pressure systems.
3/4-inch NPT: Typically used for larger industrial plumbing systems, fuel lines, and high-pressure applications.
1-inch NPT and larger: These sizes are used in heavy-duty industrial and high-pressure systems, including hydraulic systems, oil pipelines, and larger fluid transfer systems. Sizes may go up to 4 inches or more, depending on the application.
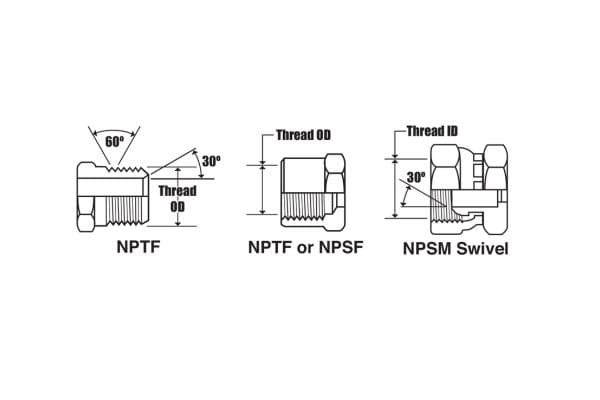
How to Measure NPT Threads and Fittings
Measuring NPT threads requires precision, as even small variations in size or pitch can lead to improper sealing and leaks. Here’s a step-by-step guide on how to measure NPT threads accurately:
Identify the Pipe Size: NPT fittings are typically labeled by their nominal size (e.g., 1/2-inch, 1-inch). This nominal size is the approximate inside diameter of the pipe the fitting will connect to, not the exact outside thread diameter.
Measure the Thread Pitch: The pitch of NPT threads is the distance between the peaks of the threads. To measure the pitch, use a thread pitch gauge. NPT threads generally have a coarse pitch, which ensures the connection remains strong and secure under pressure.
Measure the Thread Angle: Use a protractor or a thread angle gauge to verify the thread angle. NPT threads have a standardized 60-degree angle, which ensures they engage properly with each other to form a secure seal.
Measure the Outer Diameter of the Thread: To check the size of the NPT fitting, measure the outside diameter (OD) of the male threads. This measurement should match the specifications for the nominal size of the pipe fitting. For example, a 1/2-inch NPT fitting should have an outside diameter of about 0.840 inches.
Check the Tapered Length: NPT threads are tapered, meaning they get smaller as you move along the length of the fitting. Measure the taper by comparing the diameter at both ends of the fitting. This ensures the fitting will engage tightly when installed.
Standard NPT Thread Dimensions and Tolerances
The dimensions and tolerances for NPT threads are standardized to ensure consistent performance across various systems. The American National Standards Institute (ANSI) and the American Society of Mechanical Engineers (ASME) set the official specifications for NPT threads. These include:
Thread Pitch: NPT threads have a 1.814 threads per inch (TPI) for sizes up to 2 inches, with larger sizes having a reduced TPI. The coarse thread is designed to create a tight seal under pressure.
Thread Angle: NPT threads have a 60-degree thread angle, which ensures that the fitting can be tightened evenly and securely to form a leak-resistant seal.
Tapered Dimensions: NPT threads taper at a rate of 1 inch per foot (1° 47’ 30” per inch), meaning the male thread diameter decreases as the thread moves away from the fitting’s end. The tapered design helps ensure that the threads will engage tightly, preventing leaks.
Tolerance Levels: NPT threads must fall within the specific tolerances set by ANSI and ASME. These tolerances ensure that the threads fit together correctly without excessive gaps or tightness that could damage the threads or prevent proper sealing. For example, NPT threads are allowed a certain degree of variation in the thread’s peak and valley depth, as well as its diameter.
NPT Thread Sealing: Key to Leak Prevention
Sealing NPT threads is critical to ensuring leak-free connections in plumbing, hydraulic, and industrial systems. Although NPT threads are tapered and designed to provide a natural seal, they often require the use of sealants to ensure optimal performance, especially in high-pressure or complex applications.
Different Sealing Methods: PTFE Tape, Thread Sealants, and Compounds
There are several sealing methods available for NPT threads, each with its own set of advantages depending on the application. The most common sealing methods include PTFE tape, thread sealants, and pipe compounds.
PTFE Tape (Teflon Tape): PTFE (Polytetrafluoroethylene) tape, commonly known as Teflon tape, is a popular sealing method for NPT threads. It’s a flexible, thin tape that is wrapped around the male threads of the fitting before installation. PTFE tape works by filling the tiny gaps between threads and creating a barrier that prevents leaks.
Advantages: PTFE tape is easy to apply, cost-effective, and works well in low to medium pressure systems.
Limitations: While it provides a reliable seal in most cases, PTFE tape may not be suitable for very high-pressure or high-temperature applications. Additionally, over-wrapping or incorrect application can cause sealing issues.
Thread Sealants (Liquid Thread Sealants): Thread sealants are paste-like compounds that are applied directly to the male threads of a fitting. These sealants create a thicker barrier between the threads than PTFE tape, providing a more durable and long-lasting seal.
Advantages: Thread sealants offer stronger seals, making them ideal for high-pressure applications or high-temperature environments. They also help prevent galling (thread damage) and are available in various formulations to resist chemicals, oils, and other harsh substances.
Limitations: Thread sealants can be messier to apply compared to PTFE tape, and excess sealant can leak out during installation, potentially causing contamination.
Pipe Compounds: Pipe compounds are specialized liquid or paste products used to seal NPT threads. These compounds are often more viscous than regular thread sealants and are designed for specific applications, such as fuel lines or gas systems.
Advantages: Pipe compounds provide an extra layer of protection against leaks and are specially formulated for specific use cases. They’re often more resistant to vibration and thermal expansion than PTFE tape.
Limitations: Pipe compounds can be more expensive than other sealing methods and require careful application to ensure a consistent, even layer.
How Sealants Enhance the Performance of NPT Threads
Sealants are crucial for enhancing the performance and longevity of NPT thread connections. Here’s how they improve the sealing and overall effectiveness of NPT threads:
Fill in Microscopic Gaps: Sealants help to fill the tiny gaps that naturally exist between the threads of NPT fittings. Without sealants, these gaps could lead to slow leaks over time, especially in high-pressure or chemically aggressive environments. The sealant provides a continuous barrier, preventing leakage.
Improve Pressure Resistance: In high-pressure systems, the force exerted on the threads can cause small leaks if the seal is not properly maintained. Sealants enhance the pressure resistance of NPT threads by filling any imperfections and ensuring a stronger seal, which is essential for maintaining system integrity under stress.
Reduce the Risk of Thread Damage: When fittings are tightened without sealant, the threads can experience friction and wear, leading to galling or thread damage. Using sealants, such as thread compounds, can reduce friction, ensuring smoother engagement and protecting the threads from damage over time.
Enhance Chemical and Temperature Resistance: Some sealants are specially formulated to withstand high temperatures, chemicals, or corrosive substances. This makes them ideal for use in applications such as fuel systems, hydraulic lines, and chemical processing, where conventional sealing methods like PTFE tape may not be sufficient.
Conclusion
Careful attention to thread tolerances, sealant application and installation methods will ensure optimum performance of NPT threads and minimize the need for maintenance and repair. If you are in need of NPT hydraulic fitting, please feel free to contact Topa and we can select the best quality hydraulic products for you!
FAQ
Do NPT threads require sealants?
Yes, NPT threads often require sealants like PTFE tape or thread sealants to fill the small gaps between the threads and create a leak-free seal, especially in high-pressure or chemical applications.
What is the purpose of the tapered design in NPT threads?
The tapered design of NPT threads helps to create a self-sealing connection as the male and female threads compress together, forming a tight seal that reduces the risk of leaks.
Can I use PTFE tape on NPTF threads?
Yes, you can use PTFE tape on NPTF threads, though NPTF fittings generally don’t require sealing compounds due to their metal-to-metal seal. Sealants may still be used for extra protection in some high-pressure applications.
What are the most common mistakes when sealing NPT threads?
Common mistakes include over-wrapping PTFE tape, under-tightening fittings, using the wrong sealant, and failing to clean the threads before sealing. These can lead to leaks or improper sealing.
What is the difference between NPT and BSPT threads?
The main difference is the thread angle: NPT has a 60-degree angle, while BSPT has a 55-degree angle. This makes NPT and BSPT threads incompatible with each other.
When should I use thread sealants for NPT threads?
You should use thread sealants when working with high-pressure systems, fuel lines, or chemical pipes, or when the sealing needs to be enhanced beyond the natural taper of the NPT threads.