Pressure hoses are designed to handle high-pressure environments, allowing them to convey fluids or gases at elevated pressures. They are commonly used in applications where maintaining a constant flow under pressure is essential, such as in hydraulic systems or high-pressure cleaning equipment. On the other hand, suction hoses are engineered to handle negative pressure or vacuum conditions. They are typically used for drawing in liquids or gases, such as in vacuum systems, or for transferring materials in agricultural settings.
Understanding Pressure and Suction Hoses
Definition and Purpose
Pressure Hoses: Pressure hoses are specifically designed to withstand and convey fluids or gases at high pressures. These hoses are built with reinforced layers to handle the stress exerted by the pressurized contents. Their primary function is to ensure that the fluid or gas is delivered efficiently and safely from one point to another, even under intense pressure. They are crucial in applications where high pressure is essential for operation, such as hydraulic systems, high-pressure cleaning, and various industrial processes.
Suction Hoses: Suction hoses, in contrast, are designed to operate under negative pressure or vacuum conditions. These hoses are built to handle the forces of suction without collapsing or deforming. Their primary role is to draw fluids or gases into a system, making them essential for applications such as vacuum systems, material transfer in agriculture, and industrial suction applications. Suction hoses must be flexible yet strong enough to maintain their shape and functionality under the influence of suction forces.
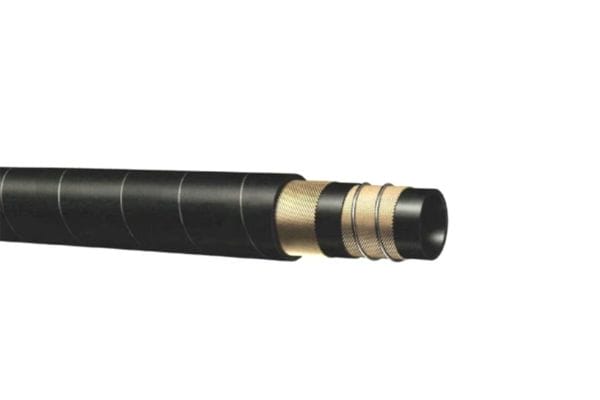
Basic Functionality
How Pressure Hoses Work: Pressure hoses are designed to operate effectively in environments where the internal pressure is significantly higher than the external pressure. They are constructed with multiple layers of reinforcement, including braided or spiral steel wires, to provide strength and prevent bursting. The inner lining of the hose is typically made from materials that can withstand high pressure, such as synthetic rubber or thermoplastic elastomers. When fluid or gas is pumped through the hose, the reinforced layers distribute the pressure evenly, allowing the hose to maintain its integrity and deliver the contents efficiently.
How Suction Hoses Work: Suction hoses function under conditions where the pressure inside the hose is lower than the atmospheric pressure outside. These hoses are constructed with flexible materials and often include a spiral reinforcement to prevent collapse under vacuum conditions. The hose’s design allows it to maintain its shape and resist deformation when suction forces are applied. The inner lining is typically made from materials that can handle the forces of suction and the type of fluid being conveyed. Suction hoses are essential for systems that need to draw in fluids or gases, ensuring smooth and efficient flow without compromising the hose’s structural integrity.
Feature | Pressure Hose | Suction Hose |
Main Role | Transports fluids/gases under high pressure safely and efficiently. | Draws in fluids/gases under negative pressure (vacuum). |
Reinforcement | Multi-layer steel wire (braided/spiral) to prevent bursting. | Spiral wire or plastic support to prevent collapse. |
Inner Lining | Rubber or thermoplastic for high-pressure resistance. | PVC or rubber for flexibility and suction stability. |
Function in Use | Resists internal pressure higher than outside environment. | Resists external pressure higher than inside vacuum. |
Construction and Design Differences
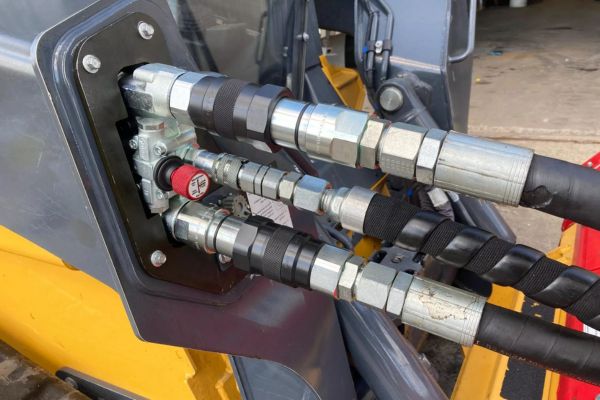
Reinforcement and Structure
Reinforcement Layers in Pressure Hoses: Pressure hoses require robust reinforcement to handle intense internal pressures. Common reinforcement methods include:
Braided Reinforcement: Braided layers, often made of steel wire or synthetic fibers, are woven around the hose’s core to provide strength and flexibility. Braiding helps distribute pressure evenly and prevents the hose from expanding or bursting under high pressure.
Spiral Reinforcement: Spiral-wound reinforcement, typically made from steel wire, is used for hoses that experience very high pressures. This design offers superior strength and resistance to deformation, ensuring that the hose maintains its shape and functionality under extreme pressure.
Structure of Suction Hoses: Suction hoses are designed to resist collapse under vacuum conditions. Common structural features include:
Spiral Reinforcement: Many suction hoses incorporate a spiral wire or plastic reinforcement embedded in the hose wall. This spiral structure helps the hose maintain its shape and prevents it from collapsing or kinking when subjected to suction forces.
Flexible Construction: The flexibility of suction hoses is crucial for their performance. The hose’s design often includes a combination of flexible materials and reinforcement to ensure it can handle varying suction conditions without losing integrity.
Hose Type | Reinforcement Method | Function |
Pressure Hose | Braided Wire/Fiber – woven layers | Adds strength & flexibility, prevents bursting under load. |
Spiral Steel Wire – continuous spiral | Handles very high pressure, resists deformation. | |
Suction Hose | Spiral Wire/Plastic Support | Prevents collapse or kinking under vacuum. |
Flexible Construction + Reinforcement | Maintains shape, allows bending during suction operation. |
Differences in Lining for Pressure and Suction Hoses
Pressure Hoses: The inner lining of pressure hoses is typically made from materials that can withstand high pressures and resist abrasion. Rubber linings, such as nitrile or EPDM, are common for their durability and resistance to the chemicals and temperatures associated with high-pressure applications.
Suction Hoses: The inner lining of suction hoses is designed to handle negative pressure and resist abrasion from the conveyed materials. PVC or rubber linings are often used, with a focus on flexibility and resistance to wear and tear. The lining needs to be robust enough to handle the stress of suction without compromising performance.
Outer Covering:
Pressure Hoses: The outer covering of pressure hoses is designed to protect against external damage, such as abrasion, UV exposure, and chemicals. Common materials include rubber or thermoplastic compounds that offer excellent durability and resistance to environmental factors. The outer cover also provides additional strength and flexibility.
Suction Hoses: The outer covering of suction hoses is typically designed to resist wear and tear from environmental conditions, such as abrasions and UV exposure. It may also be made from flexible materials like PVC or rubber, with additional reinforcement to protect against external damage while maintaining the hose’s ability to perform under suction conditions.
Feature | Pressure Hose | Suction Hose |
Inner Lining | Rubber (NBR, EPDM) or Thermoplastic → Withstands high pressure, resists chemicals & abrasion. | PVC or Rubber → Flexible, resists wear, holds shape under vacuum. |
Outer Covering | Rubber/Thermoplastic → Protects from abrasion, UV, chemicals; adds durability & strength. | PVC/Rubber → Protects from abrasion & UV; reinforced for flexibility under suction. |
Performance Characteristics
Pressure Ratings
Pressure hoses are designed to handle different levels of pressure depending on their construction and application. Maximum pressure ratings vary widely, with some common benchmarks:
Low-Pressure Hoses: Typically handle pressures up to 3000 psi. These are often used in lighter-duty hydraulic systems and applications where extreme pressure is not required.
Medium-Pressure Hoses: Generally rated for pressures ranging from 3000 to 6000 psi. These hoses are used in more demanding hydraulic systems and industrial applications.
High-Pressure Hoses: Designed for pressures above 6000 psi, with some hoses rated for up to 10,000 psi or more. These are used in extreme environments, such as high-pressure cleaning and certain hydraulic systems.
Suction hoses are designed to operate under negative pressure conditions, but they have limitations in terms of how much vacuum they can handle. Key considerations include:
Maximum Vacuum Rating: Suction hoses can typically handle vacuums up to 29.9 inches of mercury (Hg), which is close to a full vacuum. Beyond this, the risk of collapse or deformation increases.
Limitations: Excessive suction pressure can cause the hose to collapse if it lacks adequate reinforcement. The hose must be chosen based on the specific vacuum conditions of the application to avoid operational issues.
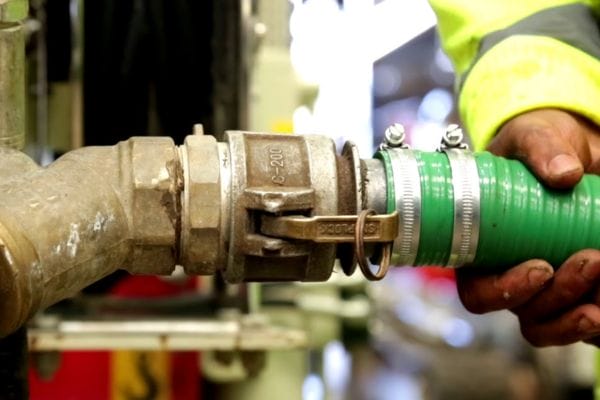
Temperature Tolerance
Temperature Ranges for Pressure Hoses: Pressure hoses must be able to withstand a range of temperatures depending on their intended use. Common temperature tolerances include:
Low-Temperature Tolerance: Some pressure hoses can operate effectively at temperatures as low as -40°F (-40°C), making them suitable for cold weather applications.
High-Temperature Tolerance: Many pressure hoses can handle temperatures up to 250°F (121°C) or higher. Specially designed hoses can withstand even more extreme temperatures, reaching up to 400°F (204°C) or more, depending on the material and construction.
Temperature Tolerance of Suction Hoses: Suction hoses also need to manage varying temperatures, although their tolerance may differ from pressure hoses:
Low-Temperature Tolerance: Suction hoses are generally effective at temperatures as low as -20°F (-29°C) to -40°F (-40°C), depending on the material.
High-Temperature Tolerance: Suction hoses usually handle temperatures up to 150°F (66°C) to 200°F (93°C). Higher temperatures may require specialized hoses with specific materials and construction to maintain performance and flexibility.
Flexibility and Bend Radius
Flexibility and Bend Radius Requirements for Pressure Hoses:
Pressure hoses need to be flexible enough to accommodate various installation scenarios while maintaining their performance under pressure. Key considerations include:
Flexibility: Pressure hoses are designed with flexibility in mind, allowing them to be routed around obstacles and through tight spaces without kinking or collapsing. The degree of flexibility depends on the hose material and reinforcement.
Bend Radius: Each pressure hose has a minimum bend radius, which is the tightest curve the hose can make without damaging its structure. A typical minimum bend radius ranges from 2 to 4 times the hose diameter. Exceeding this bend radius can lead to reduced flow, increased wear, or hose failure.
Flexibility Considerations for Suction Hoses:
Suction hoses must also be flexible to ensure smooth operation in various applications. Key factors include:
Flexibility: Suction hoses are generally more flexible than pressure hoses to facilitate ease of use and installation. This flexibility helps them conform to different layouts and routing paths.
Bend Radius: Suction hoses often have a larger minimum bend radius compared to pressure hoses, which helps prevent kinking under suction conditions. A typical minimum bend radius is about 1.5 to 3 times the hose diameter. A proper bend radius is essential to avoid collapse and ensure efficient suction performance.
Applications and Industry Uses
Pressure Hose Applications
Common Industries Using Pressure Hoses: Pressure hoses are integral to many industries where high pressure is necessary for operational efficiency. Key industries include:
Automotive Industry: Pressure hoses are used in various automotive applications, such as hydraulic systems for brakes and steering, as well as in high-pressure fuel lines. These hoses ensure the safe and efficient transfer of fluids under high pressure.
Construction Industry: In construction, pressure hoses are essential for hydraulic machinery, including excavators, bulldozers, and cranes. They are used to transfer hydraulic fluids that power these machines, providing the necessary force for heavy lifting and other tasks.
Manufacturing and Industrial Processes: Pressure hoses are utilized in manufacturing processes that require high-pressure fluid transfer, such as in the operation of hydraulic presses, pumps, and machinery. They also play a role in high-pressure cleaning systems used in industrial settings.
Specific Use Cases and Examples:
Application | Function of Pressure Hose |
Automotive Braking System | Transfers brake fluid from master cylinder to calipers → Ensures effective braking. |
Hydraulic Excavator | Delivers hydraulic fluid to arm & bucket components → Enables movement & heavy operation. |
Pressure Washer | Carries high-pressure water → Cleans dirt, grime, and stains quickly. |
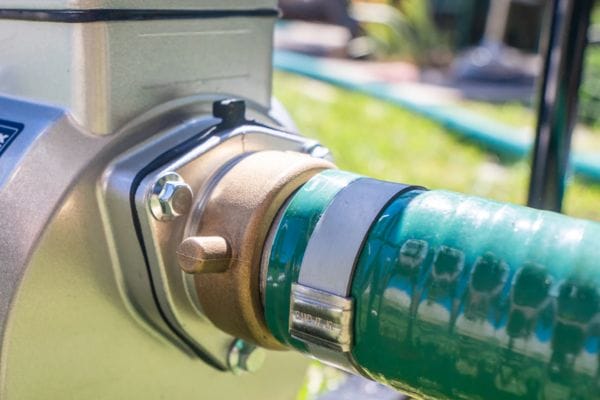
Suction Hose Applications
Industries Relying on Suction Hoses: Suction hoses are crucial in industries where drawing in materials or fluids is required. Key industries include:
Agriculture: Suction hoses are widely used in agriculture for irrigation systems, fertilizer applications, and the transfer of liquids and granular materials. They help in drawing water from sources and delivering it to fields and crops.
Marine Industry: In marine applications, suction hoses are used for bilge pumping and transferring fuel or other liquids on boats and ships. They are essential for maintaining the vessel’s operational efficiency and safety.
Construction and Waste Management: Suction hoses are used in construction for vacuuming up debris, dust, and materials. In waste management, they are employed for transferring sewage and other waste materials in vacuum trucks.
Specific Use Cases and Examples:
Application | Function of Suction Hose |
Irrigation System | Draws water from wells/reservoirs → Supplies water efficiently to crops & fields. |
Bilge Pump | Removes water from ship bilge → Prevents flooding, keeps vessel stable. |
Vacuum Truck | Collects sewage, sludge, or waste → Ensures safe transport & disposal in waste management. |
Selection Criteria and Buying Guide
✔ Pressure Ratings
Pressure hose → Must match/exceed system’s maximum pressure.
Suction hose → Must withstand maximum vacuum without collapsing.
✔ Material
Pressure hose → Rubber / Thermoplastics / Reinforced composites → durable & chemical-resistant.
Suction hose → PVC / Rubber / Reinforced types → flexible & collapse-resistant.
✔ Temperature Tolerance
Pressure hose → Broader range (e.g., -40°C to +250°C).
Suction hose → Narrower range (e.g., -20°C to +93°C).
✔ Flexibility & Bend Radius
Pressure hose → Needs tighter bend radius, avoid kinking.
Suction hose → More pliable, larger bend radius to prevent collapse.
How to Match Hoses with Specific Applications
Identify the Application Requirements:
Pressure Applications: For hydraulic systems, high-pressure cleaning, or other high-pressure tasks, select hoses with high pressure ratings and durable materials. Consider factors such as fluid type, pressure conditions, and environmental exposure.
Suction Applications: For applications involving the drawing of fluids or materials, such as in agriculture or waste management, choose hoses designed to handle vacuum conditions with appropriate reinforcement to prevent collapse.
Consider the Environment:
Exposure to Chemicals and Abrasion: If the hose will be exposed to harsh chemicals or abrasive materials, select hoses with chemical-resistant linings and durable outer coverings to ensure longevity and performance.
Temperature Extremes: Match the hose’s temperature tolerance with the environmental conditions it will face. For extreme temperatures, ensure the hose is rated for those conditions to prevent failure.
Check for Compatibility:
Couplings and Fittings: Ensure that the hose is compatible with the couplings and fittings used in your system. Mismatched components can lead to leaks or failures.
Application-Specific Features: Some applications may require specialized hoses with additional features such as fire resistance, UV protection, or food-grade compliance. Choose hoses that meet these specific needs.
Conclusion
For best results, consulting with an industry expert or hose supplier can provide valuable insights tailored to your specific needs. Topa experts can help you navigate the complexities of hose selection, ensuring that you choose the product that best suits the needs of your application. With our knowledge, you can make informed decisions and get the best performance from your hose system.
FAQ
What is the main difference between pressure and suction hoses?
Pressure hoses are designed to handle high-pressure environments and deliver fluids under pressure, while suction hoses are built to operate under negative pressure or vacuum conditions to draw fluids in.
What materials are commonly used in pressure hoses?
Pressure hoses are typically made from materials like rubber, thermoplastics, and reinforced composites to withstand high pressure and provide durability.
Can suction hoses be used for high-pressure applications?
No, suction hoses are not designed for high-pressure applications. They are meant for drawing fluids under vacuum and have limitations regarding pressure handling.
How do I determine the right hose for my application?
Consider factors such as the required pressure rating, material compatibility, temperature tolerance, and flexibility needs.
What should I do if I’m unsure about which hose to choose?
Consult with hose suppliers or industry experts. They can provide guidance based on your application’s specific needs and help you select the most appropriate hose.
How often should hoses be inspected or replaced?
Hoses should be regularly inspected for signs of wear, damage, or degradation. The frequency of inspection depends on usage and environmental conditions, but it’s generally a good practice to check them periodically and replace them as needed to prevent failures.