Among the different types of weld fittings, socket weld, and butt weld fittings are two of the most commonly used. Each fitting type has its unique characteristics, advantages, and drawbacks, making it essential to choose the right one for specific applications. The selection of weld fittings impacts not only the strength and longevity of the piping system but also its overall cost, ease of maintenance, and safety.
Understanding Weld Fittings
A. What Are Weld Fittings?
Weld fittings are specialized components used in piping systems to join sections of pipe together, create directional changes, or connect pipes to other equipment such as valves, pumps, or vessels. These fittings are crucial in ensuring that a piping system maintains its structural integrity and can handle the flow of fluids or gases under various conditions, including high pressure and temperature.
The primary purpose of weld fittings is to provide a secure, leak-proof connection that can withstand the mechanical stresses, thermal expansion, and corrosive environments typically encountered in industrial applications. Unlike mechanical fittings, which rely on threads or clamps to secure pipes, weld fittings use the welding process to create a permanent bond between pipes. This bond is typically stronger than the base material of the pipe itself, making weld fittings ideal for applications where safety, durability, and reliability are paramount.
Weld fittings are widely used across a variety of industries, including oil and gas, chemical processing, power generation, water treatment, and pharmaceuticals. In these sectors, piping systems are often subjected to harsh conditions, making the strength and reliability of the weld fittings critical. For example, in the oil and gas industry, weld fittings are essential in pipelines that transport crude oil and natural gas across long distances, often through challenging environments. Similarly, in chemical processing plants, weld fittings are used to ensure that hazardous materials are safely contained and transported without leaks.
B. Types of Weld Fittings
There are several types of weld fittings, each designed for specific applications and pipe sizes. The most common types include socket weld fittings and butt weld fittings, both of which are integral to the construction and maintenance of industrial piping systems.
Socket Weld Fittings:
Description: Socket weld fittings involve inserting the pipe into a recessed area, or socket, of the fitting. The pipe is then welded around the outer circumference, creating a fillet weld. This type of fitting is typically used for small-diameter pipes, usually under 2 inches, where the flow of the fluid is not significantly impeded by the internal protrusion of the pipe.
Applications: Socket weld fittings are commonly used in systems where leak-tightness is essential, such as in steam or gas lines. They are also preferred in high-pressure systems where the strength of the joint is critical.
Butt Weld Fittings:
Description: Butt weld fittings are used to connect pipes that are aligned end-to-end. The edges of the pipes are beveled before welding to create a strong, seamless joint that offers a smooth flow path with minimal turbulence. This type of fitting is suitable for larger-diameter pipes and systems where maintaining a smooth interior surface is important.
Applications: Butt weld fittings are widely used in industries where high-pressure and high-temperature conditions are prevalent, such as in power plants and petrochemical facilities. They are also favored in systems requiring frequent inspection or those that transport corrosive substances, as the continuous joint reduces the risk of leaks and corrosion.
Socket Weld Fittings
A. What Are Socket Weld Fittings?
Socket weld fittings are a type of pipe fitting used to join sections of pipe by inserting one pipe into the socket end of a fitting, such as an elbow, tee, or coupling, and then applying a weld around the circumference of the joint. This method is commonly used in small-diameter piping systems, typically for pipes with diameters of 2 inches or less. The socket weld process results in a fillet weld, which provides a strong and reliable joint that is capable of withstanding moderate to high pressure.
Construction and Design Features:
Socket weld fittings are designed with a socket or recess at one end into which the pipe is inserted. The socket provides a snug fit, which ensures proper alignment and positioning of the pipe before welding. This design feature makes socket weld fittings particularly suitable for applications where precision and leak-tightness are critical.
The construction of socket weld fittings includes a flat face on the socket end, which comes into contact with the pipe’s end. This ensures that the pipe is seated correctly within the fitting, reducing the likelihood of misalignment during welding. The pipe is typically inserted until it bottoms out in the socket, then slightly withdrawn to provide an expansion gap. This gap allows for thermal expansion of the pipe during welding, reducing stress on the joint and ensuring a more secure connection.
Socket weld fittings are commonly made from materials such as stainless steel, carbon steel, and various alloys, depending on the application and the properties required, such as corrosion resistance, strength, or temperature tolerance.
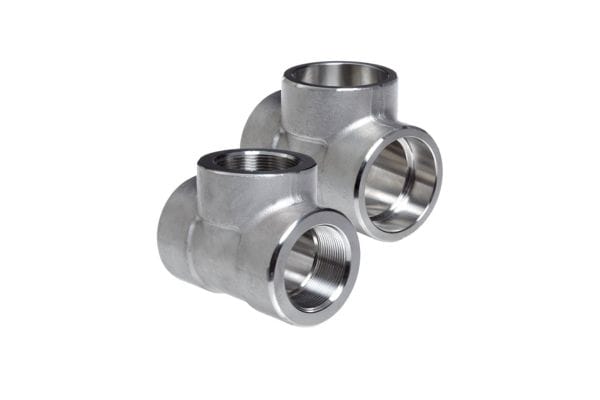
B. Installation Process
Preparation:
Begin by selecting the appropriate socket weld fitting for your application, ensuring it is compatible with the pipe material and size.
Inspect the pipe ends and fitting socket for cleanliness. Remove any dirt, grease, or other contaminants that could interfere with the welding process.
Measure and mark the pipe to ensure it is inserted to the correct depth in the socket.
Cutting and Deburring:
Cut the pipe to the desired length using a pipe cutter or saw. Ensure the cut is square to provide a proper fit within the socket.
Deburr the cut edges of the pipe to remove any sharp edges or burrs that could cause misalignment or disrupt the welding process.
Insertion:
Insert the pipe into the socket of the fitting until it bottoms out. Then, withdraw the pipe slightly to create a small expansion gap (typically around 1/16 inch). This gap allows for thermal expansion during welding.
Alignment:
Ensure the pipe and fitting are properly aligned before welding. Misalignment can cause weak joints and may lead to failure under pressure.
Tack Welding:
Perform tack welds at multiple points around the joint to hold the pipe and fitting in place. Tack welding helps maintain alignment during the final welding process.
Final Welding:
Complete the weld around the circumference of the joint. Use a fillet weld technique, applying consistent heat and filler material to ensure a strong, uniform weld.
Allow the weld to cool slowly to avoid thermal shock, which can lead to cracking.
C. Advantages of Socket Weld Fittings
Simplicity and Ease of Installation: One of the most significant advantages of socket weld fittings is their simplicity and ease of installation. The socket design allows for quick and accurate alignment of the pipe and fitting, reducing the need for complex jigs or fixtures. This ease of installation makes socket weld fittings ideal for small-bore piping systems, where precise alignment is critical but space may be limited.
Reduced Risk of Leakage in Small-Bore Pipes: Socket weld fittings are particularly well-suited for small-bore piping systems, where the risk of leakage is a primary concern. The fillet weld applied around the joint creates a strong, leak-tight seal that can withstand moderate to high pressures. Additionally, because the pipe is inserted into the socket before welding, there is less likelihood of misalignment or gaps that could lead to leaks.
Strength and Reliability: The fillet weld used in socket weld fittings provides a robust and reliable joint that can handle moderate pressures and vibrations. This makes socket weld fittings a popular choice for applications such as steam systems, chemical lines, and gas pipelines, where the integrity of the piping system is crucial.
D. Disadvantages of Socket Weld Fittings
Limitations in Larger Diameter and High-Pressure Applications: While socket weld fittings are ideal for small-bore piping systems, they are not well-suited for larger diameter pipes or high-pressure applications. The design of the socket weld creates a small protrusion inside the pipe, which can cause turbulence and reduce the flow rate in larger pipes. Additionally, the fillet weld may not be strong enough to withstand the stresses and pressures encountered in larger or high-pressure systems.
Potential for Stress Concentration and Corrosion: The design of socket weld fittings can lead to stress concentration at the joint, particularly if the expansion gap is not properly maintained during installation. Over time, this stress concentration can lead to cracking or failure of the joint. Additionally, the small gap between the pipe and the socket can trap moisture, chemicals, or debris, leading to crevice corrosion. This type of corrosion can be difficult to detect and may compromise the integrity of the piping system.
Butt Weld Fittings
A. What Are Butt Weld Fittings?
Butt weld fittings are a type of pipe fitting that joins two sections of pipe end-to-end through a welding process. These fittings are designed to create a strong, seamless joint that can withstand high pressures, temperatures, and corrosive environments. Unlike socket weld fittings, which involve inserting one pipe into a socket, butt weld fittings require the pipes to be aligned directly against each other, with their ends prepared for welding by beveling.
Construction and Design Features:
Butt weld fittings are constructed to provide a continuous metal structure that is as strong as or stronger than the pipes being connected. The process typically involves beveling the ends of the pipes or fittings to create a V-shaped groove, which allows for deeper penetration of the weld material. This deep penetration ensures a robust and durable joint that can handle high-stress conditions.
The design of butt weld fittings includes various shapes and sizes to accommodate different piping system requirements. Common types of butt weld fittings include elbows (for changing the direction of the pipe), tees (for branching the flow), reducers (for changing pipe diameter), and caps (for sealing the end of a pipe). These fittings are typically made from materials such as carbon steel, stainless steel, alloy steel, and other specialized materials, depending on the application’s requirements.
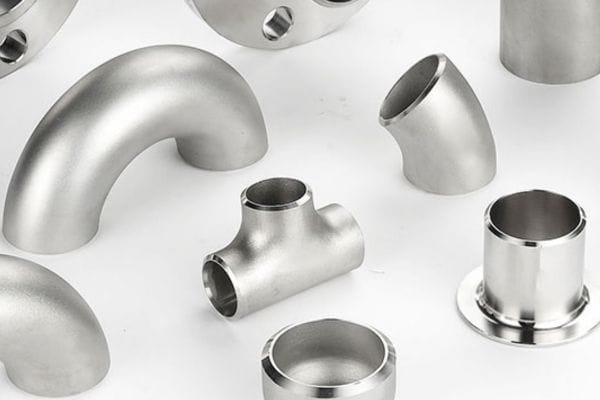
B. Installation Process
Preparation:
Select the appropriate butt weld fitting for your application, ensuring compatibility with the pipe material and size.
Inspect the pipe ends and the fitting for cleanliness. Remove any dirt, grease, or contaminants that could interfere with the welding process.
Bevel the pipe ends if they are not pre-beveled. The beveling process creates a V-shaped groove that allows for proper weld penetration.
Alignment:
Align the pipes or fittings end-to-end, ensuring that the bevels match up perfectly. Misalignment can lead to weak joints and potential failure under pressure.
Use alignment tools such as clamps or jigs to hold the pipes and fittings in place during welding. Precision in alignment is crucial for a strong weld.
Tack Welding:
Perform tack welds at several points around the joint to hold the pipes and fittings in place. Tack welds are temporary welds that prevent movement during the final welding process.
Final Welding:
Complete the weld by filling the V-groove with welding material. This process typically involves multiple passes with the welding torch to ensure full penetration and strength.
Use appropriate welding techniques, such as TIG (Tungsten Inert Gas), MIG (Metal Inert Gas), or stick welding, depending on the material and application requirements.
Allow the weld to cool gradually to prevent thermal shock, which can lead to cracking.
Inspection and Testing:
After welding, inspect the joint visually and, if necessary, use non-destructive testing methods such as radiography, ultrasonic testing, or dye penetrant inspection to ensure the weld’s integrity.
Perform pressure testing on the system to confirm that the joint can withstand the operational conditions without leaking.
C. Advantages of Butt Weld Fittings
Superior Strength and Durability: One of the primary advantages of butt weld fittings is their superior strength and durability. The full penetration weld created during installation provides a joint that is as strong as the pipe itself, if not stronger. This makes butt weld fittings ideal for high-pressure and high-temperature applications where joint integrity is critical. The continuous, homogeneous weld ensures that the joint can withstand significant mechanical stress, thermal expansion, and contraction, as well as the corrosive effects of harsh chemicals or fluids.
Seamless and Smooth Interior, Reducing Friction and Turbulence: Butt weld fittings create a seamless interior surface within the piping system, which is particularly beneficial for fluid dynamics. The absence of internal ridges or gaps reduces friction and turbulence, allowing for a smoother flow of liquids or gases. This characteristic is especially important in industries where maintaining efficient flow rates and minimizing pressure drops are crucial, such as in chemical processing or oil and gas transportation. Additionally, the smooth interior reduces the risk of buildup or blockage, contributing to the system’s long-term reliability.
D. Disadvantages of Butt Weld Fittings
Higher Cost and Complexity of Installation: One of the main disadvantages of butt weld fittings is the higher cost associated with their installation. The process requires skilled labor, specialized tools, and precision alignment, all of which contribute to increased labor costs. Additionally, the welding process for butt weld fittings is more time-consuming than for other types of fittings, such as socket welds or threaded fittings. The need for beveling, alignment, and multiple welding passes adds to the overall complexity and cost of installation.
Need for Precise Alignment and Skilled Labor: Installing butt weld fittings requires a high degree of precision in alignment and welding. Any misalignment or poor welding technique can compromise the strength of the joint, leading to potential failures. As a result, the installation of butt weld fittings must be carried out by skilled welders who are trained to meet industry standards. This requirement for skilled labor can limit the use of butt weld fittings in situations where such expertise is not readily available.
Conclusion
When deciding between socket weld and butt weld fittings, it is crucial to carefully evaluate your specific project requirements, including the size of the piping system, operating pressures, temperatures, and budget constraints. Each fitting type has its own set of advantages and limitations, and the best choice depends on the unique demands of your application. By understanding these differences, you can make an informed decision that ensures the long-term performance and reliability of your piping system.
FAQ
What is the main difference between socket weld and butt weld fittings?
Socket weld fittings involve inserting a pipe into a socket before welding, while butt weld fittings join pipes end-to-end with a full penetration weld.
Which type of fitting is better for high-pressure applications?
Butt weld fittings are generally better suited for high-pressure applications due to their superior strength and seamless joint.
Are socket weld fittings suitable for large-diameter pipes?
No, socket weld fittings are typically used for small-diameter pipes (usually under 2 inches) and are not ideal for large-diameter applications.
Do butt weld fittings require special tools for installation?
Yes, butt weld fittings require tools for pipe beveling, precise alignment, and advanced welding techniques, often necessitating skilled labor.
Which fitting type is easier to install?
Socket weld fittings are easier and quicker to install, making them a cost-effective option for small-bore piping systems.
Can I inspect socket and butt weld fittings easily?
Socket weld fittings are generally easier to inspect visually, while butt weld fittings may require non-destructive testing methods like radiography for thorough inspection.