Compression brake line fittings play a significant role in the repair and maintenance of brake systems. These fittings are designed to connect brake lines securely, forming a seal that prevents brake fluid leakage under high pressure. However, despite their advantages, compression fittings come with certain drawbacks and risks, especially when used in high-pressure environments like public road vehicles. This article explores the advantages and disadvantages of compression brake line fittings in detail.
What Are Brake Line Compression Fittings?
Compression brake line fittings are components designed to connect and seal brake lines in hydraulic brake systems. These fittings create a secure connection by compressing a ferrule (a small metal ring) around the brake line, which helps form a tight seal to prevent brake fluid from leaking. They are commonly used for quick and temporary fixes or in low-pressure systems where other more permanent solutions might be less practical or too costly.
Definition and Overview
A compression brake line fitting is a mechanical device that connects two sections of brake tubing or joins a brake tube to a fitting, such as a union or adapter. It works by creating a seal through the compression of a ferrule when the nut is tightened, compressing it against the fitting body and the brake line itself. This action forms a leak-proof seal capable of withstanding a certain amount of hydraulic pressure. The effectiveness and longevity of this seal depend largely on the correct installation and the pressure levels within the system.
These fittings are often used in hydraulic systems because they are relatively easy to install and do not require specialized equipment like flaring tools or welding kits. They are particularly useful when a quick repair is needed, making them popular in situations such as off-road or temporary vehicle setups.
Components of a Compression Brake Line Fitting
A compression fitting typically consists of three main parts:
Fitting Body: This is the main component that connects to the brake line. The fitting body has a threaded opening on one end where the nut and ferrule are attached. It is designed to hold the brake line in place and to support the compression process when the nut is tightened.
Ferrule (Compression Ring): The ferrule is a small metal ring that sits between the fitting body and the nut. It is the key element that forms the seal. As the nut is tightened, it compresses the ferrule against the brake line and fitting body, creating a tight seal. Ferrules are usually made from soft metals like brass or copper, which allow them to deform slightly to fit snugly around the brake line.
Compression Nut: This part threads onto the fitting body and compresses the ferrule as it is tightened. The nut’s role is crucial as it drives the ferrule into place, ensuring that the brake line is securely sealed. Proper tightening of the compression nut is vital for preventing leaks; over-tightening or under-tightening can compromise the seal and lead to brake fluid leakage.
Together, these components work to form a leak-proof connection. The simplicity of this design is what makes compression fittings a popular choice for quick and efficient repairs.
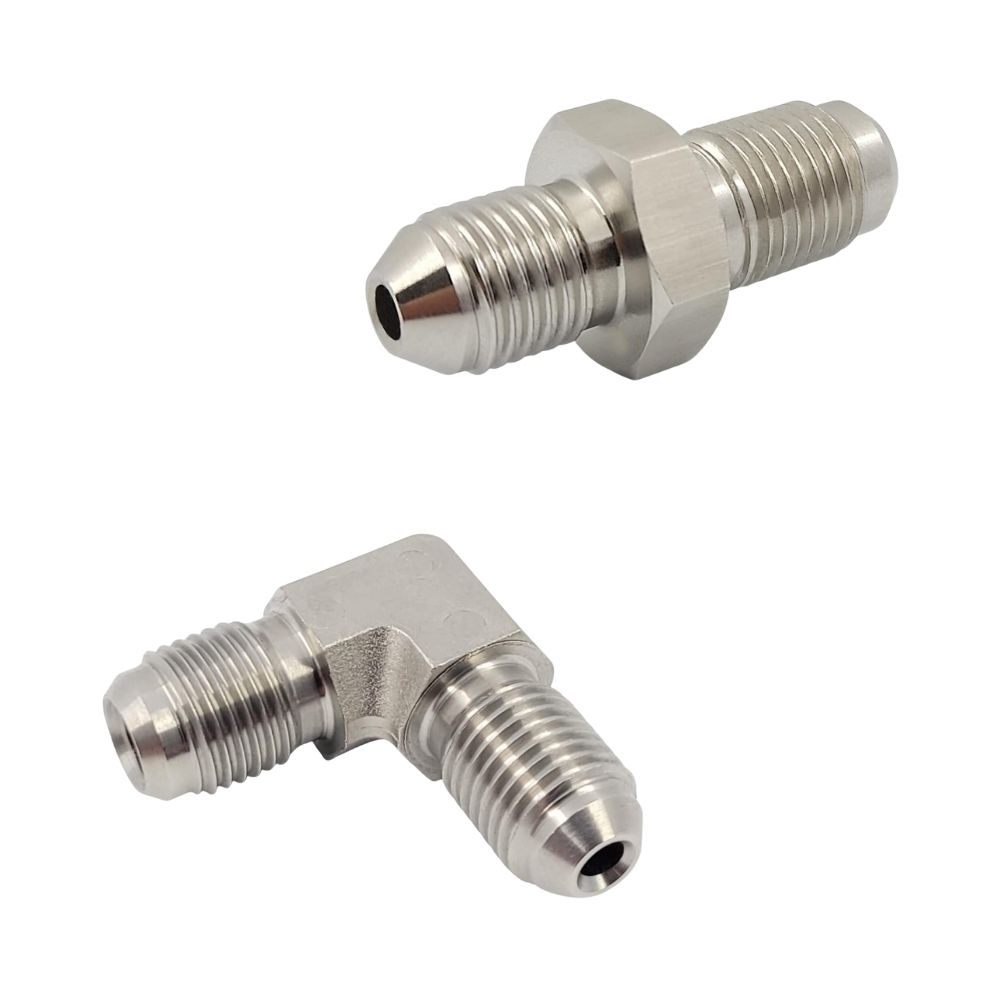
Common Uses
Compression brake line fittings are widely used in several scenarios:
Off-Road and Non-Public Vehicles: These fittings are commonly used in vehicles that do not operate on public roads, such as off-road vehicles, farm equipment, and lawn mowers. In these settings, brake systems typically experience lower pressure, making compression fittings an acceptable choice. Additionally, the ease of installation and replacement makes these fittings ideal for vehicles that frequently undergo modifications or repairs.
Temporary Repairs: In automotive repair and restoration, compression fittings are often used as a temporary solution to test the brake system’s functionality before permanent repairs are made. For instance, during vehicle restoration, mechanics might use compression fittings to check for leaks or pressure issues before replacing the brake lines with flared or welded connections. This allows for efficient troubleshooting and reduces the time needed to identify potential problems.
Hydraulic Systems: While not typically recommended for high-pressure automotive brake systems, compression fittings are used in other types of hydraulic systems where pressure levels are manageable. This includes applications in hydraulic machinery, HVAC systems, and low-pressure fluid systems where the simplicity and quick installation of compression fittings provide practical benefits.
DIY and Quick Fixes: For vehicle owners or hobbyists who need to perform quick fixes without access to specialized tools, compression fittings offer a practical solution. They are especially useful for individuals who might not have the skills or tools required for creating flared connections or welding lines. However, these fittings are only advisable in situations where safety is not compromised, as high-pressure applications in public road vehicles pose significant risks if the fittings fail.
How Compression Fittings Work
Basic Mechanism
The primary working principle of a compression fitting revolves around the interaction between three key components: the fitting body, the ferrule, and the compression nut. When the compression nut is tightened, it exerts force on the ferrule, which compresses it around the brake line. Here’s how this mechanism operates in detail:
Tightening the Nut: When the compression nut is turned clockwise onto the fitting body, it pulls the ferrule inward. This action creates pressure on the ferrule against the surface of the brake line.
Ferrule Compression: The ferrule, typically made of a softer metal like brass or copper, deforms slightly under this pressure. As it compresses, it conforms tightly around the brake line, filling any gaps and creating a seal that prevents brake fluid from leaking out. The integrity of this seal is crucial for maintaining the system’s hydraulic pressure.
Sealing Effect: The mechanical compression of the ferrule around the brake line creates a strong bond that withstands the pressures typically encountered in hydraulic brake systems. This seal remains effective as long as the fitting is properly tightened and the materials do not degrade over time.
Understanding this mechanism highlights the importance of proper installation, as a poorly tightened or installed fitting can lead to leaks and potentially dangerous brake system failures.
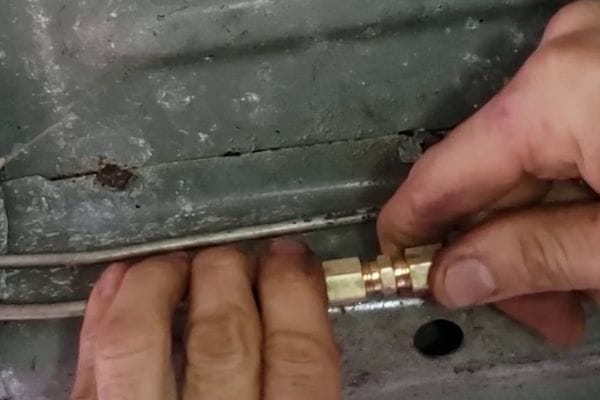
Installation Process
Installing compression fittings in brake lines involves several straightforward steps. Here’s a step-by-step overview of the installation process, including the common tools needed:
Gather Tools and Materials: Before starting, collect the necessary tools:
Compression fittings
Brake line (appropriate material and size)
Wrench (preferably a torque wrench for precise tightening)
Tubing cutter (to ensure clean cuts)
Deburring tool (to smooth out any rough edges)
Cut the Brake Line: Using a tubing cutter cut the brake line to the desired length. Ensure the cut is straight and clean to facilitate a better seal.
Deburr the Edges: After cutting, use a deburring tool to remove any sharp edges or burrs from the cut end of the brake line. This step is crucial for preventing damage to the ferrule and ensuring a proper seal.
Prepare the Compression Fitting: Slide the compression nut and then the ferrule onto the brake line. Ensure that the ferrule is positioned correctly on the line before connecting it to the fitting body.
Connect to the Fitting Body: Insert the brake line into the fitting body, ensuring it reaches the bottom of the fitting. This is important for a complete seal.
Tighten the Nut: Using a wrench, tighten the compression nut onto the fitting body. It’s essential to apply even pressure and avoid over-tightening, as this can damage the ferrule or the brake line itself.
Check for Leaks: After installation, it’s vital to test the system for leaks. Pressurize the brake system and visually inspect the connection for any signs of fluid escaping.
Final Adjustments: If any leaks are detected, slightly tighten the nut again to ensure a proper seal. Always refer to manufacturer specifications for recommended torque settings.
Advantages of Installation
Compression fittings have gained popularity for several reasons:
Ease of Installation: One of the most significant advantages of compression fittings is their straightforward installation process. Unlike flared fittings, which require specialized tools and techniques, compression fittings can be installed with basic hand tools. This accessibility makes them ideal for DIY enthusiasts and mechanics alike.
Time Efficiency: The installation process for compression fittings is generally quicker, allowing for faster repairs and less downtime for vehicles. This is especially valuable in situations where timely repairs are critical, such as in off-road vehicles or emergency services.
Cost-Effectiveness: Compression fittings are typically more affordable than other connection methods, such as flared or welded fittings. This cost advantage makes them an attractive option for temporary repairs and budget-conscious repairs.
Versatility: Compression fittings can be used with various materials, including copper, steel, and copper-nickel brake lines. This versatility allows them to be applied in different situations and environments, accommodating various vehicle types and brake systems.
Disadvantages and Risks Associated with Compression Brake Line Fittings
Prone to Leaks Under High Pressure
One of the primary concerns with compression fittings is their reliability in high-pressure brake systems. Unlike flare fittings, which are designed to handle high hydraulic pressures more effectively, compression fittings can be less robust. The nature of their design—where the seal relies on the compression of a softer material (the ferrule)—means that they may not withstand extreme pressures over time.
When brake fluid is subjected to high pressure, such as during emergency braking scenarios, compression fittings can become susceptible to leaks. This is especially true if the fitting is not tightened properly or if it has been subjected to thermal expansion and contraction, which can loosen the connection. The risk of brake fluid leaks is particularly dangerous, as even a small loss of fluid can compromise the entire braking system, leading to reduced braking efficiency or complete brake failure.
In scenarios where vehicles operate under high stress—such as racing or heavy-duty applications—using compression fittings can pose significant safety risks. They are generally more suited for low-pressure systems or temporary fixes rather than permanent solutions in critical brake applications.
Legality Issues
Another critical factor to consider is the legal implications surrounding the use of compression fittings in certain vehicles, particularly those that operate on public roads. Many jurisdictions have strict regulations governing the types of fittings that can be used in brake systems, primarily to ensure the highest safety standards.
In numerous regions, the use of compression fittings in passenger vehicles is either discouraged or outright prohibited. This is due to concerns about their reliability and potential failure under high-stress conditions. Vehicle manufacturers often specify the types of connections to be used in their braking systems, and compression fittings may not meet the required safety standards.
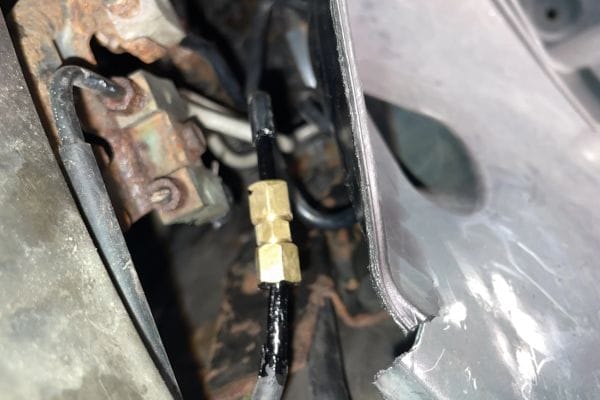
Tendency to Fail Over Time
Compression fittings are not immune to wear and tear. Over time, several factors can lead to their failure, posing significant safety risks:
Vibration: Vehicles experience constant vibrations during operation, which can gradually loosen compression fittings. This is particularly concerning in high-performance or off-road vehicles, where vibrations can be more pronounced. As the fittings loosen, the seal can become compromised, leading to potential leaks.
Improper Installation: If compression fittings are not installed correctly, they are at a higher risk of failure. Over-tightening can damage the ferrule, while under-tightening may not create a secure seal. Additionally, if the brake line is not cut properly or deburred adequately, it can lead to leaks at the connection point.
Material Fatigue: The materials used in compression fittings can degrade over time. Factors like corrosion, exposure to harsh chemicals, or prolonged high temperatures can weaken the ferrule or the brake line itself. Once the integrity of these components is compromised, the likelihood of failure increases significantly.
Regular inspections and maintenance are essential to identify early signs of wear and prevent catastrophic failures. However, as discussed in the following section, maintaining and inspecting these fittings presents its challenges.
Inspection and Maintenance Challenges
Maintaining and inspecting compression brake line fittings can be challenging, which can lead to safety hazards if not addressed properly. Here are some key issues:
Accessibility: In many vehicles, brake line fittings are located in hard-to-reach areas. This makes it difficult for mechanics or vehicle owners to perform thorough inspections regularly. If fittings are not easily accessible, they may be overlooked during routine maintenance checks, increasing the risk of undetected leaks or failures.
Difficulty in Identifying Issues: Unlike some other fittings, where leaks are visually apparent, compression fittings can sometimes leak internally. This means that brake fluid may not escape outside the fitting, making it hard to detect a problem until significant damage has occurred. Without visible signs of failure, proactive maintenance may be neglected.
Alternative Solutions to Compression Brake Line Fittings
Flare Fittings
Flare fittings are a widely used alternative to compression fittings, particularly in high-pressure brake systems. They are designed to create a secure, leak-proof seal by flaring the end of the brake line tubing. The flared end of the tube is inserted into a fitting, and a nut is tightened to compress the flare against the fitting body, forming a strong and durable connection.
Benefits of Flare Fittings:
Higher Pressure Tolerance: Flare fittings are specifically designed to handle the high pressures commonly encountered in hydraulic brake systems. The flaring process creates a robust mechanical bond that minimizes the risk of leaks under high pressure, making it ideal for vehicles operating on public roads or in heavy-duty applications.
Durability: The flared connection is mechanically strong and resistant to vibrations, a common cause of failure in compression fittings. This makes flare fittings particularly suitable for long-term applications where reliability is crucial.
Compatibility: Flare fittings are compatible with various brake line materials, including steel, copper, and copper-nickel. This versatility allows for a wide range of applications in different vehicle types and environments.
When to Use Flare Fittings: Flare fittings are the preferred choice for permanent installations in vehicles that operate at high pressures, such as passenger cars, trucks, and commercial vehicles. They are also recommended when complying with safety regulations for road vehicles. However, installing flare fittings requires specific tools like a flaring tool kit and some technical expertise, which may not be as convenient for quick or temporary fixes.
Welding Brake Lines
Welding brake lines is a highly durable solution, often used in professional repair settings where a permanent fix is required. In this method, sections of the brake line are welded together, forming a continuous and seamless connection that eliminates the risk of leaks.
Benefits of Welding Brake Lines:
Seamless Connection: Welding provides a leak-proof, seamless connection that is not susceptible to loosening due to vibration or pressure changes, unlike fittings that rely on mechanical seals.
Longevity: Welded brake lines have an extended lifespan, making them ideal for high-performance vehicles and those exposed to extreme conditions, such as race cars and heavy-duty trucks.
Custom Fabrication: Professional welding allows for custom brake line fabrication, ensuring that the brake system is tailored to the vehicle’s specific requirements and conditions.
When to Use Welding: Welding is suitable for situations where the brake system needs to be highly reliable and maintenance-free for extended periods. It is commonly used in professional settings, such as automotive workshops, where trained technicians have access to the necessary equipment and expertise. However, welding brake lines is not practical for DIY enthusiasts or temporary repairs, as it requires specialized tools and skills.
Quick-Connect Fittings
Quick-connect fittings represent a newer technology designed to simplify brake line connections while providing reliability. These fittings are engineered to “snap” into place, creating a secure seal without the need for extensive tools or tightening processes. They are increasingly used in modern brake systems, especially in situations where rapid assembly or disassembly is advantageous.
Benefits of Quick-Connect Fittings:
Ease of Use: Quick-connect fittings are designed for fast and straightforward installation, reducing the time and effort required for brake line repairs. They are ideal for both professional mechanics and experienced DIY enthusiasts.
No Need for Specialized Tools: Unlike flare fittings or welding, quick-connect fittings do not require specialized tools, making them more accessible for general use.
Reliable Seal: Modern quick-connect fittings are engineered to provide a secure seal, minimizing the risk of leaks and offering a reliable connection similar to that of traditional flaring methods.
When to Use Quick-Connect Fittings: These fittings are a suitable option when ease of use and speed are critical, such as in emergency repairs or routine maintenance that requires frequent disassembly. While quick-connect fittings are designed to handle a wide range of pressures, they may not be as robust as flared or welded connections in extreme conditions, making them best for standard applications.
Comparative Chart | ||||
Feature | Compression Fittings | Flare Fittings | Welding Brake Lines | Quick-Connect Fittings |
Pressure Tolerance | Moderate (Prone to leaks) | High (Excellent seal) | Very High (Seamless connection) | Moderate to High (Depends on design) |
Installation Complexity | Low (Simple tools required) | Moderate (Flaring tool needed) | High (Welding equipment needed) | Low(No specialized tools) |
Durability | Medium(Prone to vibration issues) | High (Resistant to vibration) | Very High (Permanent solution) | High (Designed for quick assembly) |
Conclusion
For those considering the use of compression fittings, it’s essential to evaluate their application carefully. They may be appropriate for low-pressure systems or temporary repairs, but in high-stress scenarios or regulated environments, opting for flare fittings or welding is recommended to ensure safety and reliability. If you found this information useful, please share the post with others who might benefit from it. Always consult professionals for brake line repairs to ensure the highest safety standards are met.
FAQ
What are compression brake line fittings used for?
Compression brake line fittings are used to connect brake lines in hydraulic systems. They create a seal by compressing a ferrule around the brake line, allowing for fluid to flow without leaks. They are often used for temporary fixes or in low-pressure systems.
Are compression brake line fittings safe for high-pressure systems?
No, compression fittings are not recommended for high-pressure systems, such as those found in most vehicle brake lines. They are prone to leaks under extreme pressure and may not meet the safety standards required for vehicles on public roads.
Can I use compression fittings for brake lines in my car?
Compression fittings are generally not suitable for use in passenger vehicles that operate on public roads. Many jurisdictions prohibit their use due to the risk of leaks and potential brake failure. It’s important to check local regulations and safety standards.
What are the alternatives to compression brake line fittings?
Alternatives include flare fittings, which provide a more durable and high-pressure tolerant connection, welding for a permanent and seamless connection, and quick-connect fittings for easy installation without compromising safety.
Are compression fittings easy to install?
Yes, one of the benefits of compression fittings is their ease of installation. They require only basic tools and are suitable for quick or temporary fixes, making them a popular option for DIY repairs and off-road vehicles.
What are the risks of using compression brake line fittings?
The risks include potential leaks under high pressure, failure over time due to vibrations or improper installation, and legal restrictions in certain areas. Regular inspection and maintenance are required to minimize these risks.