Using the correct hose for propane is critical because incompatible hoses, such as those designed for hydraulic fluids, may not be able to handle propane’s chemical properties or the pressures involved. The use of an inappropriate hose can result in material degradation, leaks, and an increased risk of fire or explosion, posing significant safety hazards. Thus, selecting a hose that meets the specific requirements for propane use is not just a matter of efficiency but a crucial safety consideration.
Understanding Hydraulic Hoses
A. Composition and Design of Hydraulic Hoses
Hydraulic hoses are constructed from a combination of materials, each chosen for its specific properties that enable the hose to function effectively under various conditions. The primary materials used in hydraulic hoses include:
Synthetic Rubber: This is the most common material used for the inner tube of hydraulic hoses. Synthetic rubber, such as nitrile or EPDM (ethylene propylene diene monomer), offers excellent flexibility and resistance to oils, making it ideal for carrying hydraulic fluids. The synthetic rubber layer is crucial because it must withstand constant contact with hydraulic oils, which can vary in composition and temperature.
Thermoplastics: In some cases, the inner tube or outer cover of hydraulic hoses may be made from thermoplastic materials like nylon or polyurethane. These materials provide superior resistance to abrasion and chemical degradation, making them suitable for environments where the hose may come into contact with harsh substances or where flexibility is a priority.
Reinforcement Layers: To enhance strength and pressure resistance, hydraulic hoses often include one or more layers of reinforcement. These layers can be made from braided or spiral-wound wire (usually steel) or textile materials. The reinforcement layer gives the hose its ability to handle high pressures without bursting, making it a critical component in ensuring the hose’s durability and safety.
Metal: In some cases, hydraulic hoses are designed with a metal braid or helix wire within the reinforcement layer, providing additional strength and the ability to maintain shape under high pressure or vacuum conditions.
B. Hydraulic Hose Applications
Hydraulic hoses are integral to the operation of a wide range of machinery and systems, serving as the conduits that transmit hydraulic power. Some of the most common applications include:
Industrial Machinery: In industries such as manufacturing, mining, and construction, hydraulic hoses are used to power equipment like excavators, bulldozers, cranes, and presses. These machines rely on hydraulic systems to perform heavy-duty tasks, and the hoses must be capable of handling high pressures and extreme temperatures.
Automotive Systems: Hydraulic hoses are also used in vehicles, particularly in the braking and power steering systems. These hoses must withstand high pressures and the constant flexing associated with vehicle operation, ensuring safe and reliable performance over the vehicle’s lifespan.
Agricultural Equipment: Tractors, harvesters, and other agricultural machinery use hydraulic systems for various functions, including lifting, steering, and powering attachments. Hydraulic hoses in these applications must be durable and resistant to the harsh environmental conditions often encountered in agriculture.
Propane: Characteristics and Handling Requirements
A. Chemical Properties of Propane
Propane is a hydrocarbon, specifically a three-carbon alkane, with the chemical formula C₃H₈. It is a colorless and odorless gas at room temperature, but for safety reasons, an odorant is usually added to detect leaks. Propane is highly flammable and is stored as a liquid under pressure in tanks and cylinders. When released from its container, propane expands and converts to gas, making it highly efficient for energy use.
Key chemical properties of propane include:
Flammability: Propane has a narrow flammable range in air, making it highly explosive under certain conditions. The gas can ignite at temperatures as low as -104°C (-155°F), which means it poses a significant fire hazard if not handled correctly.
Pressure Characteristics: Propane is stored under pressure as a liquid, and its vapor pressure increases with temperature. At 21°C (70°F), the vapor pressure of propane is approximately 110 psi, but it can exceed 200 psi at higher temperatures, necessitating hoses that can safely manage these pressures.
Temperature Characteristics: Propane remains in a liquid state under high pressure but rapidly vaporizes at atmospheric pressure, which is useful for fuel but also requires careful management to prevent hose degradation due to cold temperatures when the liquid expands.
Understanding these properties is crucial for selecting hoses that can safely transport propane, as incorrect hose selection could lead to leaks, ruptures, or even explosions.
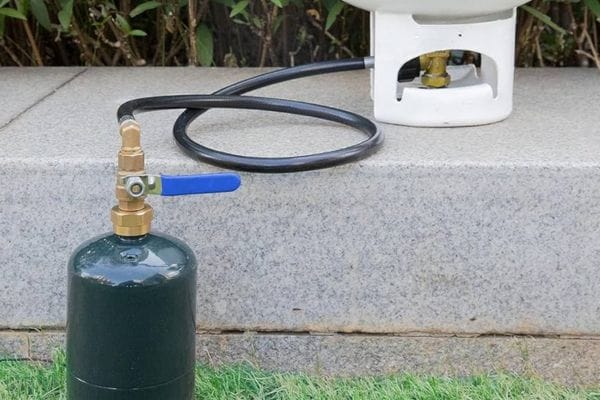
B. Common Uses of Propane
Propane is a versatile fuel widely used in various industries and applications. Some of the most common uses include:
Heating: Propane is commonly used for residential and commercial heating. It is also used in rural areas where natural gas pipelines are unavailable, providing an efficient and portable heating source.
Cooking: In both residential kitchens and outdoor grills, propane is a popular fuel due to its clean-burning properties and convenience. It is also used in commercial kitchens, food trucks, and remote cooking operations.
Industrial Applications: Propane is used as a fuel for forklifts, generators, and other industrial equipment, particularly in settings where clean-burning fuel is necessary to reduce emissions.
Agriculture: Farmers use propane for crop drying, heating greenhouses, and powering irrigation pumps. The portability and efficiency of propane make it an ideal energy source for agricultural operations.
Transportation: Propane is used as an alternative fuel in vehicles, especially in fleet operations. It offers a lower-carbon alternative to gasoline and diesel, making it a preferred choice for environmentally conscious companies.
Given its widespread use, ensuring that the hoses transporting propane are safe and reliable is essential. The potential hazards associated with propane leaks or ruptures make it imperative to use hoses designed specifically for this application.
C. Hose Requirements for Propane
Transporting propane safely requires hoses that meet specific criteria to handle the unique properties of this gas. The primary requirements include:
Material Compatibility: The hose material must be chemically compatible with propane to prevent degradation. Hoses made from materials like nitrile, neoprene, or other specialized compounds are typically used because they resist the chemical effects of propane and prevent permeation, which could lead to leaks.
Pressure Resistance: Hoses used for propane must withstand the pressures associated with liquid propane storage and transport. These hoses are designed to handle high vapor pressures and resist bursting under extreme conditions.
Temperature Tolerance: The hose must be able to function safely within the temperature range encountered in propane applications, including exposure to cold temperatures during the liquid-to-gas expansion process.
Common materials used for propane hoses include:
Nitrile: Known for its excellent resistance to oil, gas, and other chemicals, nitrile is a popular choice for propane hoses. It provides durability and flexibility, making it suitable for a range of temperatures and pressures.
Neoprene: This synthetic rubber is highly resistant to oil, heat, and weathering, making it another good option for propane hoses. Neoprene hoses offer a balance of flexibility and toughness, ideal for outdoor and industrial use.
Thermoplastic: Some propane hoses are made from thermoplastic materials, which offer excellent chemical resistance and can be lighter and more flexible than rubber alternatives. These hoses are often used in applications where ease of handling and installation are priorities.
Risks of Using Hydraulic Hoses for Propane
A. Chemical Incompatibility
Hydraulic hoses are typically designed to carry hydraulic fluids, such as oil or water-glycol mixtures, and are constructed using materials that are compatible with these substances. However, when exposed to propane, these materials may not hold up, leading to significant risks:
Material Degradation: Hydraulic hoses are often made from materials like synthetic rubber or thermoplastics, which may not be chemically compatible with propane. Propane can cause these materials to break down over time, leading to brittleness, cracking, or swelling of the hose. This degradation compromises the hose’s structural integrity and increases the likelihood of leaks.
Permeation Risks: Propane, being a smaller molecule than many hydraulic fluids, can permeate through the walls of a hydraulic hose more easily. This can lead to the gradual escape of gas, which not only reduces efficiency but also creates a hazardous environment where gas buildup could occur, posing risks of fire or explosion.
Chemical Reactions: In some cases, the chemical properties of propane can cause adverse reactions to the materials used in hydraulic hoses. For instance, certain rubber compounds might react with propane, leading to chemical breakdowns that further weaken the hose and increase the risk of failure during use.
These chemical incompatibilities underline why hydraulic hoses are unsuitable for propane transport, as the consequences of using incompatible materials can be both dangerous and costly.
B. Temperature and Pressure Concerns
Hydraulic hoses are engineered to operate within specific temperature and pressure ranges, typically those associated with hydraulic systems. However, propane presents unique challenges that can exceed these operational limits:
Temperature Extremes: Hydraulic hoses are designed to handle the temperatures associated with hydraulic fluids, which typically do not fluctuate as widely as those encountered with propane. Propane, particularly in its liquid form, can reach extremely low temperatures when it vaporizes, potentially causing hydraulic hoses to become brittle and crack. Conversely, if the temperature increases, the pressure inside the propane hose rises significantly, which may exceed the hose’s designed pressure rating.
Pressure Variability: The pressure within a propane system can vary widely depending on the temperature and the phase (liquid or gas) of the propane. Hydraulic hoses might not be capable of withstanding the higher pressures required to contain propane safely, especially under conditions where the temperature causes the vapor pressure to rise dramatically. Hydraulic hoses that are not rated for these pressures can fail, leading to leaks or catastrophic hose ruptures.
Comparison of Operational Limits: Hydraulic hoses are typically rated for specific pressures and temperatures relevant to their intended use. These ratings are generally lower than what is required for safe propane transport. For example, a hydraulic hose rated for 3,000 psi and temperatures between -40°C to 100°C might not be suitable for propane, which could exert higher pressures and expose the hose to lower or higher temperatures depending on the environmental conditions.

C. Safety Hazards
The use of hydraulic hoses for propane, despite the aforementioned incompatibilities, can lead to severe safety hazards that pose risks to both people and property:
Fire and Explosion Risks: Propane is a highly flammable gas, and any leaks from a hydraulic hose not designed for propane can create a dangerous environment. A small spark or flame near a leaking hose could ignite the propane, leading to a fire or explosion. The confined spaces where propane is often used or stored can exacerbate these risks, leading to potentially catastrophic outcomes.
Environmental Hazards: In addition to immediate safety risks, propane leaks due to hydraulic hose failure can result in environmental damage. Propane can displace oxygen in confined spaces, posing asphyxiation risks, and when released into the atmosphere, it contributes to air pollution and greenhouse gas emissions.
Alternatives to Hydraulic Hoses for Propane
A. Recommended Hose Materials for Propane
When selecting hoses for propane, it’s essential to choose materials specifically designed to handle the unique characteristics of propane. The following materials are commonly recommended due to their chemical compatibility, durability, and safety in propane applications:
Nitrile Rubber (NBR): Nitrile is a synthetic rubber that offers excellent resistance to oils, fuels, and other chemicals, making it ideal for propane. It has good flexibility and can withstand the pressures and temperatures associated with propane use. Nitrile hoses are commonly used in propane applications because they provide a reliable seal, preventing leaks and ensuring safety.
Thermoplastic: Thermoplastic hoses are another excellent choice for propane, especially in applications where lightweight and flexibility are priorities. These hoses are made from materials such as nylon or polyurethane, which offer high chemical resistance and can handle a wide range of temperatures. Thermoplastic hoses are also known for their smooth internal surfaces, which reduce the risk of blockages and ensure a consistent flow of propane.
Neoprene: Neoprene is a versatile synthetic rubber that resists oil, heat, and weathering, making it suitable for outdoor propane applications. Neoprene hoses maintain flexibility in a wide temperature range and provide good protection against environmental factors such as UV radiation and ozone, which can degrade other materials.
Stainless Steel Braided Hoses: For high-pressure applications or where additional durability is required, stainless steel braided hoses are often used. These hoses have an inner layer made from a material compatible with propane, such as nitrile or PTFE, and an outer layer of stainless steel braid. The stainless steel provides added strength, protects against external damage, and increases the hose’s pressure rating.
B. Selecting the Right Hose
Choosing the correct hose for propane applications involves careful consideration of several factors. The following step-by-step guide will help you make an informed decision:
Identify the Application:
Determine the specific use of the propane hose, whether it’s for residential heating, industrial machinery, or transportation. The application will influence the hose’s material and design requirements.
Consider Hose Material:
Based on the chemical properties of propane, select a hose material that is compatible, such as nitrile, thermoplastic, or neoprene. Ensure the material can handle the expected exposure to propane without degradation.
Determine Pressure Rating:
Assess the pressure conditions the hose will be subjected to. Propane can be stored under high pressure, especially in liquid form. Choose a hose with a pressure rating that exceeds the maximum expected operating pressure to ensure safety.
Evaluate Temperature Range:
Consider the temperature extremes the hose will encounter. Propane hoses must maintain flexibility and integrity in cold conditions (as low as -40°C) and withstand higher temperatures (up to 70°C or more) without failure. Select a hose rated for the full range of temperatures expected in your application.
Check Hose Size:
Choose the correct hose diameter based on the flow rate requirements of your application. A hose that is too small can create pressure build-up, while a hose that is too large may be difficult to handle. Ensure the size is appropriate for the intended use.
Verify Compliance with Standards:
Ensure that the hose meets relevant industry standards and certifications for propane use, such as those from Underwriters Laboratories (UL), the American Society for Testing and Materials (ASTM), or the Canadian Standards Association (CSA). Compliance with these standards ensures that the hose has been tested and approved for safety and performance.
Assess Environmental Factors:
Consider the environmental conditions in which the hose will be used, such as exposure to sunlight, chemicals, or physical abrasion. Choose a hose with an outer layer that can resist these factors, such as neoprene for outdoor use or stainless steel braiding for added protection.
Conclusion
Given the substantial risks and potential hazards, it is strongly recommended that only hoses specifically designed and certified for propane use be employed in any propane application. These hoses are made from materials that are chemically compatible with propane and are engineered to handle the unique pressures and temperatures associated with this gas. Prioritizing safety and regulatory compliance in hose selection is crucial to preventing accidents and ensuring the safe and efficient use of propane.
FAQ
Can hydraulic hoses be used for propane?
No, hydraulic hoses are not suitable for propane due to chemical incompatibility and the risk of material degradation, leaks, and safety hazards.
What materials are recommended for propane hoses?
Nitrile rubber, thermoplastic, and neoprene are commonly recommended materials for propane hoses due to their chemical resistance and durability.
Why is it dangerous to use hydraulic hoses for propane?
Hydraulic hoses can degrade when exposed to propane, leading to leaks, fires, or explosions, which pose significant safety risks.
What should I consider when selecting a propane hose?
Consider factors such as hose material compatibility, pressure rating, temperature range, and compliance with industry standards when selecting a propane hose.
What temperature range should a propane hose handle?
A propane hose should handle temperatures from as low as -40°C to as high as 70°C or more, depending on the application.
Where can I get advice on choosing the right propane hose?
You can consult with hose manufacturers or industry experts for professional advice on selecting the appropriate hose for propane applications.