Kinks create obstructions within the hose, leading to significant pressure drops and restricted fluid flow. This disruption can cause the hydraulic system to work harder to maintain performance, resulting in increased energy consumption and accelerated wear on system components. Over time, the stress caused by kinks can weaken the hose material, leading to leaks, bursts, and potential system shutdowns. Moreover, kinks can compromise the safety of hydraulic systems. In critical applications, such as heavy machinery or industrial equipment, a sudden hose failure due to a kink can pose serious safety risks to operators and bystanders.
Understanding the Causes of Hydraulic Hose Kinks
Hydraulic hose kinks can significantly disrupt the performance of hydraulic systems, leading to inefficiencies, safety hazards, and potential system failures. To effectively prevent kinks, it is crucial to understand the underlying causes that contribute to their development.
Common Causes of Kinks
Improper Hose Installation:
One of the most prevalent causes of hydraulic hose kinks is improper installation. When hoses are installed with tight bends or incorrect routing, they are more likely to kink under pressure. Tight bends force the hose to operate outside its designed bend radius, leading to a collapse in the hose’s structure. Similarly, incorrect routing, such as routing hoses through confined spaces or sharp angles, increases the risk of kinks as the hose is forced to bend unnaturally.
Inappropriate Hose Selection:
Selecting the wrong hose for a specific application is another common cause of kinks. This includes choosing a hose of the wrong length or a hose that does not have the appropriate bend radius for the intended installation. For example, using a hose that is too short may require stretching or bending it beyond its capacity, leading to kinks. Conversely, a hose that is too long may sag or form loops that can kink under pressure. Additionally, not considering the hose’s minimum bend radius during selection can result in a hose that is prone to kinking when installed.
Environmental Factors:
Environmental factors such as temperature extremes and exposure to chemicals can also contribute to the formation of kinks in hydraulic hoses. High or low temperatures can affect the flexibility and elasticity of the hose material, making it more susceptible to kinking. For instance, hoses exposed to freezing temperatures may become stiff and brittle, increasing the likelihood of kinks when bent.
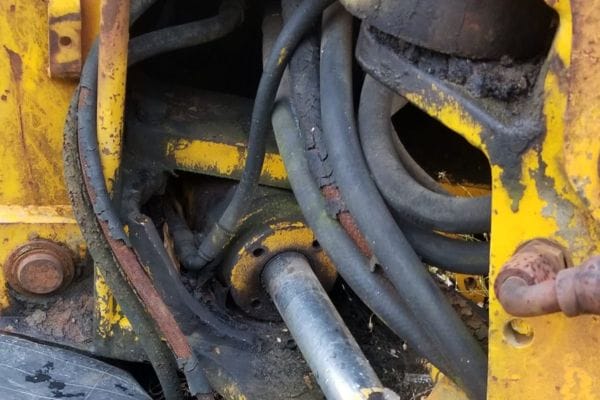
Lack of Regular Maintenance and Inspections:
Neglecting regular maintenance and inspections is another significant contributor to hydraulic hose kinks. Over time, hoses can develop wear and tear, become misaligned, or be subjected to external pressures that increase the risk of kinking.
Detailed Analysis of Each Cause
Improper Hose Installation:
When a hose is installed with tight bends or incorrect routing, it is forced to operate outside its designed parameters. Hydraulic hoses are engineered to function within specific bend radii; exceeding these limits causes the hose to collapse or kink.
Inappropriate Hose Selection:
Using a hose that is too short, too long, or has an inappropriate bend radius can force the hose into positions that are prone to kinking. A hose that is too short may need to be stretched, causing it to kink at its weakest points, while a hose that is too long may loop or droop, leading to kinks under pressure.
Environmental Factors:
Environmental conditions can have a significant impact on hose flexibility. For example, cold temperatures can make hoses brittle, increasing the likelihood of kinks when the hose is bent or moved. Similarly, chemical exposure can weaken the hose material, making it more susceptible to kinks over time.
Selecting the Right Hose to Prevent Kinks
Selecting the right hydraulic hose is crucial in preventing kinks, and ensuring the longevity and efficiency of the hydraulic system. The choice of hose material, construction, and size, along with understanding the latest innovations in hose design, can significantly reduce the risk of kinks.
Choosing the Appropriate Hose Type
The material and construction of a hydraulic hose play a pivotal role in its performance and resistance to kinking. Selecting the right hose type involves understanding the specific demands of your application and matching them with the appropriate hose characteristics.
Material and Construction:
Hydraulic hoses are constructed from various materials, including rubber, thermoplastic, and reinforced synthetic materials. Each material has unique properties that influence the hose’s flexibility, durability, and resistance to environmental factors. For instance, rubber hoses are known for their flexibility and resistance to abrasion, while thermoplastic hoses offer lightweight construction and resistance to chemicals.
The construction of the hose, including the number of reinforcement layers, also affects its ability to withstand internal pressure and external bending forces. A hose with more reinforcement layers may offer higher pressure ratings but could be less flexible, making it more prone to kinking if not properly selected for the application.
Flexibility, Pressure Rating, and Compatibility:
- Flexibility: The flexibility of the hose is a critical factor in preventing kinks. A highly flexible hose can bend easily without collapsing or forming sharp angles, reducing the likelihood of kinks during operation. However, flexibility should not compromise the hose’s strength and durability.
- Pressure Rating: The hose must be able to withstand the system’s operating pressure. Using a hose with a pressure rating lower than required can lead to expansion and deformation, increasing the risk of kinks. Conversely, a hose with a significantly higher pressure rating may be too stiff, making it difficult to install without kinking.
- Compatibility with Hydraulic Fluid: The hose material must be compatible with the hydraulic fluid used in the system. Incompatible materials can degrade over time, leading to a loss of flexibility and an increased risk of kinks.
Hose Material | Key Features | Best For | Considerations |
Rubber Hose | – Flexible | General-purpose hydraulic systems | May be heavier than other types |
– Abrasion-resistant | |||
– Good temperature range | |||
Thermoplastic Hose | – Lightweight | Mobile equipment, chemical exposure areas | Less flexible in cold temperatures |
– Chemical-resistant | |||
– Non-conductive | |||
Reinforced Synthetic Hose | – High pressure rating | Heavy-duty machinery, industrial environments | May have a larger bend radius |
– Durable under stress | |||
PTFE (Teflon) Hose | – Excellent chemical resistance | High-temp or aggressive fluid applications | Not as flexible; needs special fittings |
– High temperature tolerance |
Importance of Proper Hose Sizing
Proper hose sizing is essential in preventing kinks and ensuring the efficient operation of the hydraulic system. Incorrect hose length or diameter can lead to issues such as sagging, stretching, or excessive bending, all of which contribute to kinking.
Measuring and Selecting the Correct Hose Length and Diameter:
- Length: The hose length should be carefully measured to match the routing requirements of the system. A hose that is too short may need to be stretched, leading to tension and potential kinks. Conversely, a hose that is too long may form loops or sags, which are prone to kinking under pressure.
- Diameter: The internal diameter of the hose must be sufficient to allow the required flow rate without causing excessive pressure drops. A hose with too small a diameter may restrict flow, increasing the internal pressure and the likelihood of kinking. Conversely, a hose with too large a diameter may be too rigid, making it difficult to install without bending sharply.
The Role of the Hose’s Minimum Bend Radius:
The minimum bend radius is the smallest radius at which a hose can be bent without kinking. It is a critical factor in hose selection, particularly in applications with tight routing or limited space. Exceeding the minimum bend radius causes the hose to collapse or kink, compromising the hydraulic system’s performance.
When selecting a hose, it is essential to choose one with a minimum bend radius that accommodates the specific routing requirements of your system. This ensures that the hose can be installed without being forced into tight bends that could lead to kinks.
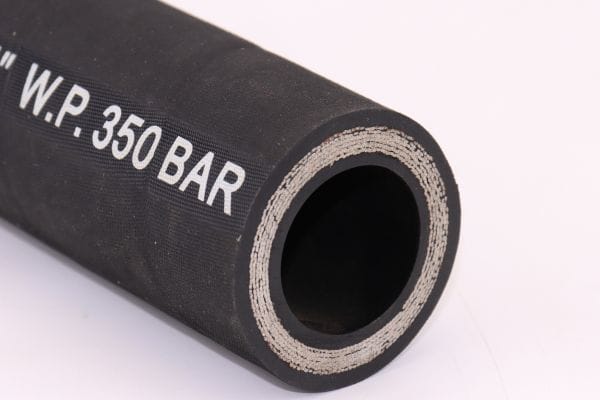
Best Practices for Hydraulic Hose Installation
Proper Hose Routing Techniques
One of the most important aspects of hydraulic hose installation is proper routing. Incorrect routing can lead to tight bends, sharp angles, and increased tension on the hose, all of which can result in kinks and premature hose failure.
Guidelines for Routing Hoses:
- Avoid Tight Bends and Sharp Angles: When routing hydraulic hoses, it’s essential to avoid tight bends and sharp angles that can stress the hose and lead to kinking. Instead, aim for smooth, gradual curves that follow the natural bend radius of the hose. Tight bends can cause the hose to collapse or kink, obstructing fluid flow and reducing the hose’s lifespan.
- Plan the Hose Path: Before installing the hose, plan the routing path carefully. Consider the movement of connected components and the potential for hose movement or flexing during operation. Ensure that the hose is not routed near sharp edges, abrasive surfaces, or high-heat areas that could damage the hose over time.
- Consider the Hose Length: Use a hose of appropriate length to avoid excessive slack, which can lead to sagging and kinking. However, ensure the hose is not too short, as stretching the hose to fit can cause unnecessary tension and potential kinks.
The Importance of Using Clamps and Brackets:
- Securing Hoses in Place: Properly securing hoses with clamps and brackets is crucial to preventing unwanted movement, which can lead to kinks. Clamps and brackets help to maintain the hose’s position, reducing the risk of excessive bending or flexing during operation.
- Selecting the Right Clamps and Brackets: Choose clamps and brackets that match the hose’s diameter and are made from materials compatible with the hose. Ensure that they are installed at regular intervals along the hose’s length to provide adequate support without crushing or damaging the hose.
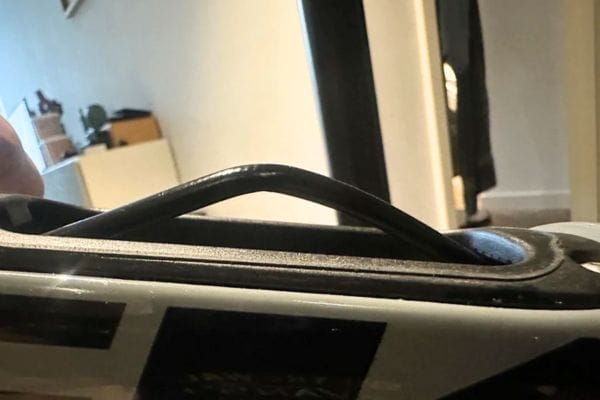
Maintaining Adequate Bend Radius
The minimum bend radius of a hydraulic hose is the smallest radius at which the hose can be bent without causing kinks or damage. Adhering to this bend radius is crucial to preventing kinks and ensuring the hose’s integrity.
Explanation of the Minimum Bend Radius:
The minimum bend radius is determined by the hose’s construction and material properties. Bending the hose beyond this radius causes the internal layers to collapse or weaken, leading to kinks and reduced flow capacity. Exceeding the bend radius also increases stress on the hose reinforcement, which can lead to premature failure.
Tips for Ensuring Proper Bend Radius:
- Measure Before Installation: Before installing the hose, measure the required bend radius along the planned routing path. Ensure that the hose’s bend radius does not exceed the manufacturer’s specified minimum bend radius. If necessary, adjust the routing path to accommodate a more gradual curve.
- Use Bend Restrictors: Bend restrictors are accessories that help maintain the hose’s bend radius by preventing it from bending too sharply at critical points. These can be particularly useful at hose ends where connections to fittings often result in tight bends.
- Avoid Unsupported Bends: Ensure that bends are supported by clamps or brackets to maintain the correct radius and prevent the hose from sagging or flexing excessively.
Avoiding Common Installation Mistakes
Even with the best intentions, common installation mistakes can lead to hydraulic hose kinks and system failures. Recognizing and avoiding these errors is key to a successful installation.
Common Errors During Hose Installation:
- Over-Tightening Fittings: Over-tightening fittings can stress the hose at the connection point, leading to kinks. This mistake often occurs when attempting to ensure a secure connection, but it can cause more harm than good.
- Incorrect Hose Length: Using a hose that is too short or too long can lead to excessive stretching or sagging, both of which increase the risk of kinks. Ensuring the correct hose length is critical for proper installation.
- Neglecting Environmental Factors: Failing to account for environmental factors such as temperature, chemical exposure, and abrasion can result in hose degradation and kinking over time.
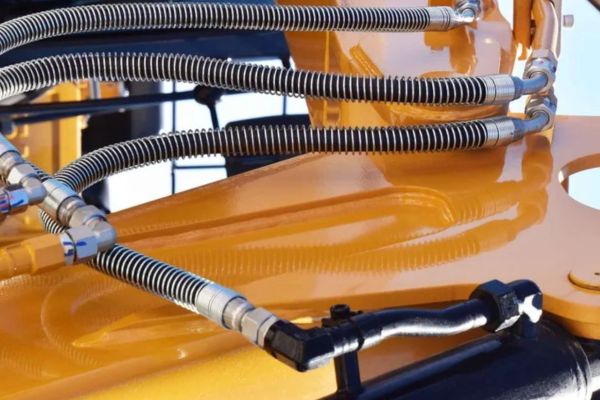
Enhancing Hose Longevity with Smart Design & Protective Accessories
Kink-Resistant Hose Design
Modern hydraulic hose technology has significantly evolved to combat one of the most common failure points—kinks. Today’s kink-resistant hoses are specifically engineered to maintain shape and flexibility, even in confined or high-stress environments.
Key advancements include:
- Spiral or braided reinforcement layers, which provide the strength to endure high pressures while allowing smooth bending.
- Use of flexible, high-performance materials, such as thermoplastic elastomers, which improve maneuverability in tight spaces without sacrificing durability.
- Abrasion-resistant outer covers, designed to shield against external wear, a common precursor to kinking or cracking.
- These features lead to reduced maintenance needs, fewer hose replacements, and more stable fluid flow, minimizing system disruptions and downtime.
Protective Accessories
While hose design lays the foundation, protective accessories add a vital layer of defense—especially in demanding environments or mobile applications.
Common accessories include:
- Hose Sleeves: Fabric or polymer-based sleeves that guard against abrasion, UV exposure, and chemical contact. They also offer minor kink resistance in high-flex areas.
- Spring Guards: Metal coils wrapped around the hose exterior to prevent collapse when the hose is bent. Ideal for equipment with frequent directional movement.
- Bend Restrictors: Molded collars installed near hose ends or fittings to prevent tight bends and maintain safe curvature, reducing localized stress and extending service life.
Combined Benefits for System Efficiency
- When used together, kink-resistant hoses and protective accessories:
- Maintain optimal bend radius and flexibility.
- Prevent premature wear caused by external hazards or mechanical stress.
- Contribute to overall system reliability, safety, and cost-efficiency.
Troubleshooting and Correcting Kinked Hoses
Kinked hydraulic hoses can compromise the efficiency and safety of your hydraulic system. Identifying and addressing kinks promptly is essential to maintaining optimal system performance. This section outlines the steps to identify and assess kinked hoses, determine whether to repair or replace them and offer quick fixes for minor kinks.
Identifying and Assessing Kinked Hoses
Identifying a kinked hose is the first step in troubleshooting. Kinks can range from minor deformations to severe collapses that significantly restrict fluid flow.
Steps to Determine the Severity of a Kink:
- Visual Inspection: Start with a visual inspection of the hose. Look for visible signs of deformation, such as flattened sections, sharp bends, or creases in the hose material. A kink will often appear as a pronounced, abrupt bend that disrupts the hose’s natural curve.
- Check for Performance Issues: A kinked hose can cause performance issues in the hydraulic system, such as reduced flow rate, pressure drops, or erratic system behavior. If you notice any of these symptoms, inspect the hose for potential kinks.
- Feel for Stiffness: Run your hand along the hose to feel for areas that are stiffer than the rest of the hose. A kinked section may feel harder and less flexible due to the deformation of the hose material.
When to Repair Versus Replace a Kinked Hose:
- Minor Kinks: If the kink is minor and does not appear to have caused significant damage to the hose, it may be possible to repair or straighten it out. However, even minor kinks can weaken the hose over time, so careful consideration is required.
- Severe Kinks: If the kink is severe, causing a sharp bend or visible damage to the hose material, it is usually safer to replace the hose. Severe kinks can lead to a permanent loss of hose integrity, increasing the risk of leaks, bursts, or complete hose failure.
- Age and Condition of the Hose: Consider the age and overall condition of the hose when deciding whether to repair or replace it. Older hoses or those that have been exposed to harsh environmental conditions may be more prone to future kinks and failures, making replacement the better option.
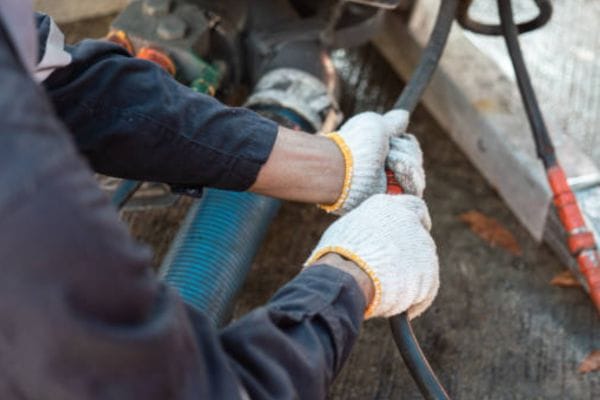
Quick Fixes for Minor Kinks
For minor kinks, several techniques can be used to straighten the hose and restore its functionality. These methods are suitable for temporary fixes or for situations where immediate replacement is not feasible.
Techniques to Straighten Out Minor Kinks:
- Manual Straightening: Gently straighten the kinked section by hand. Start at the kink and work your way outwards, applying gradual pressure to the hose to smooth out the bend. Be careful not to force the hose, as this can cause further damage.
- Warm Water Soak: Soak the kinked hose in warm water for several minutes. The heat will make the hose material more pliable, making it easier to straighten. After soaking, gently bend the hose in the opposite direction of the kink to restore its shape.
- Use of Hose Springs or Bend Restrictors: If the kink occurs near the end of the hose or in a high-stress area, consider adding a hose spring or bend restrictor. These accessories help support the hose and prevent further kinking by maintaining the correct bend radius.
- Temporary Re-routing: If the kink is caused by improper routing, consider temporarily re-routing the hose to reduce stress on the kinked section. This may involve loosening clamps or brackets and adjusting the hose’s position to avoid tight bends.
Conclusion
Taking a proactive approach to hose maintenance and installation is crucial in preventing kinks and ensuring the smooth operation of your hydraulic system. Rather than waiting for problems to arise, regular inspections and preventive measures can help identify potential issues early, allowing you to address them before they escalate into costly repairs or system failures. By implementing the strategies discussed in this guide, you can significantly reduce the risk of kinks and enhance the overall reliability of your hydraulic system.
Don’t let hose kinks compromise your performance or safety. At Topa, we specialize in high-quality, kink-resistant hydraulic hoses engineered for durability, flexibility, and extreme environments. Whether you’re in construction, agriculture, mining, or manufacturing, our hoses are built to handle your toughest challenges.
FAQ
What causes hydraulic hoses to kink?
Hydraulic hoses can kink due to improper installation, tight bends, incorrect hose selection, and lack of regular maintenance.
How can I prevent hydraulic hose kinks during installation?
To prevent kinks, ensure proper routing with smooth curves, maintain the hose’s minimum bend radius, and use clamps or brackets to secure the hose in place.
What is the minimum bend radius, and why is it important?
The minimum bend radius is the smallest radius a hose can bend without kinking. Maintaining this radius is crucial to prevent hose collapse and ensure proper fluid flow.
Should I repair or replace a kinked hose?
Minor kinks may be repaired, but severe kinks or those affecting hose integrity typically require hose replacement to ensure safety and performance.
What accessories can help prevent hose kinks?
Hose sleeves, springs, and bend restrictors can help maintain the hose’s shape and prevent kinking, especially in high-stress areas.
How often should I inspect hydraulic hoses for kinks?
Regular inspections should be conducted as part of your routine maintenance schedule to catch and address potential kinks early.