This post aims to provide a comprehensive comparison between hydraulic tubes vs hoses, two essential components in fluid power systems. By exploring their differences, this post will help readers understand the unique properties of each, the applications they are best suited for, and the factors that influence the decision to use one over the other. Whether you are designing a new hydraulic system or maintaining an existing one, understanding the nuances between tubes and hoses is crucial for optimizing performance, minimizing downtime, and ensuring the longevity of your equipment.
Understanding Hydraulic Tubes
A. Definition and Basic Characteristics
Hydraulic tubes, also known as hydraulic piping or hydraulic lines, are rigid conduits specifically designed for the transport of hydraulic fluids within a hydraulic system. Unlike flexible hydraulic hoses, hydraulic tubes are characterized by their rigid and seamless structure, providing a stable and consistent pathway for fluid flow. The rigidity of these tubes ensures that they maintain their shape under high pressure and do not flex or bend easily, making them ideal for applications where precision and stability are paramount.
Physically, hydraulic tubes are typically cylindrical with a smooth, uniform outer surface and a consistent internal diameter. This uniformity is crucial for minimizing fluid friction and ensuring efficient fluid transmission. The seamless construction of hydraulic tubes, often achieved through extrusion or drawing processes, eliminates potential weak points, making them highly reliable for high-pressure applications. In contrast, welded hydraulic tubes are made by joining the edges of rolled metal sheets, which can introduce slight variations in wall thickness and may be more prone to failure under extreme conditions.
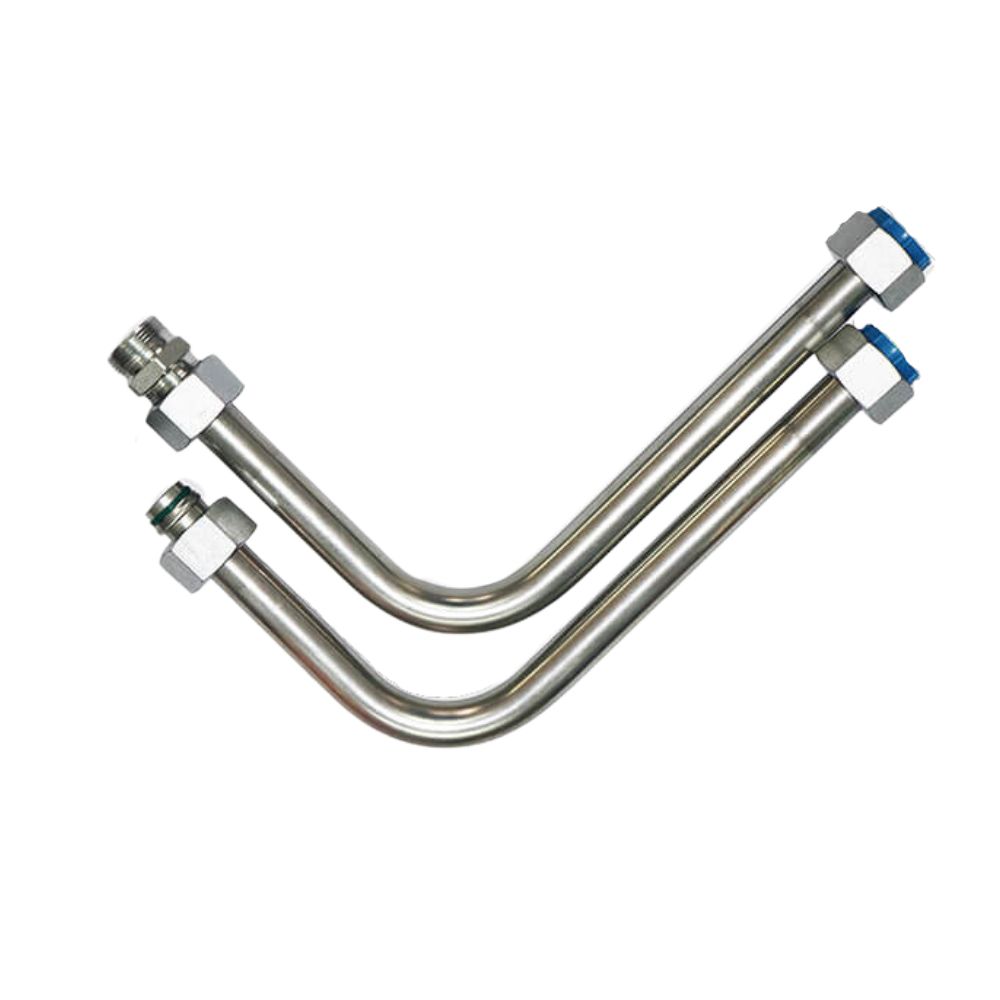
B. Materials
Hydraulic tubes are commonly made from metals that offer a balance of strength, durability, and corrosion resistance. The most prevalent materials include:
Carbon Steel: Widely used due to its high strength and cost-effectiveness, carbon steel is suitable for most standard hydraulic applications. It offers good machinability and can withstand significant pressure without deformation. However, it may require protective coatings or treatments to resist corrosion in certain environments.
Stainless Steel: Known for its excellent corrosion resistance, stainless steel hydraulic tubes are ideal for applications where the hydraulic system is exposed to moisture, chemicals, or extreme temperatures. Stainless steel is slightly more expensive than carbon steel but offers superior longevity and minimal maintenance requirements.
Alloy Steel: Alloy steel tubes, which incorporate elements like chromium, nickel, or molybdenum, provide enhanced strength, toughness, and resistance to wear. These tubes are often used in high-stress environments where standard materials may not suffice.
Copper and Brass: Though less common in modern hydraulic systems, copper and brass tubes are used in certain specialized applications due to their excellent thermal conductivity and corrosion resistance.
C. Construction
The manufacturing process of hydraulic tubes can vary depending on the desired specifications and the application. The two primary methods are:
Seamless Construction: Seamless hydraulic tubes are manufactured by extruding a solid billet of metal through a die to create a tube without any welds. This process results in a uniform wall thickness and eliminates the risk of weak points along the length of the tube. Seamless tubes are preferred for high-pressure applications and are considered more reliable.
Welded Construction: Welded hydraulic tubes are made by rolling a flat sheet of metal into a cylindrical shape and then welding the edges together. While this method is more cost-effective and suitable for lower-pressure applications, it may introduce minor inconsistencies in wall thickness and potential weak points at the weld seam.
D. Advantages of Hydraulic Tubes
Hydraulic tubes offer several advantages that make them the preferred choice for many industrial applications:
Durability: The rigid construction of hydraulic tubes ensures they can withstand significant mechanical stress without deforming. This durability is especially important in high-pressure systems where even slight deformations can lead to leaks or system failures.
High-Pressure Handling: Hydraulic tubes are designed to operate under extremely high pressures, making them suitable for demanding applications in heavy machinery, aerospace, and industrial settings. The seamless construction of these tubes further enhances their ability to handle pressure without compromising structural integrity.
Low Expansion: Unlike flexible hoses, hydraulic tubes exhibit minimal expansion when subjected to pressure. This characteristic ensures that the fluid flow remains consistent, which is crucial for precise control and operation of hydraulic systems.
Corrosion Resistance: When made from materials like stainless steel or coated carbon steel, hydraulic tubes offer excellent resistance to corrosion, ensuring a long service life even in harsh environments.
Minimal Maintenance: Due to their rigid construction and resistance to wear, hydraulic tubes require less frequent maintenance compared to hoses, reducing downtime and maintenance costs.
E. Common Applications
Hydraulic tubes are commonly found in various applications where their unique characteristics offer distinct advantages:
Heavy Machinery: In construction equipment, such as excavators and bulldozers, hydraulic tubes are used to transmit high-pressure fluid to hydraulic cylinders and motors. Their rigidity ensures precise control of the machinery’s movements.
Industrial Settings: In manufacturing plants, hydraulic tubes are used in hydraulic presses, injection molding machines, and other equipment that requires high-pressure fluid transmission. Their durability and resistance to wear make them ideal for these demanding environments.
Understanding Hydraulic Hoses
A. Definition and Basic Characteristics
Hydraulic hoses are flexible, reinforced tubes designed to transport hydraulic fluid within a hydraulic system. Unlike rigid hydraulic tubes, hoses are engineered to accommodate movement and vibrations within machinery, making them essential for applications where flexibility is required. Hydraulic hoses consist of several layers, typically including an inner tube to carry the fluid, one or more layers of reinforcement to withstand pressure, and an outer cover to protect against environmental factors such as abrasion, chemicals, and weathering.
The primary characteristic of hydraulic hoses is their flexibility, which allows them to bend and move with the components of the machinery they serve. This flexibility is crucial in systems where the components are in motion, as it prevents the hose from cracking or breaking under repeated stress. Additionally, hydraulic hoses are designed to absorb shocks and vibrations, further protecting the hydraulic system and ensuring smooth operation.
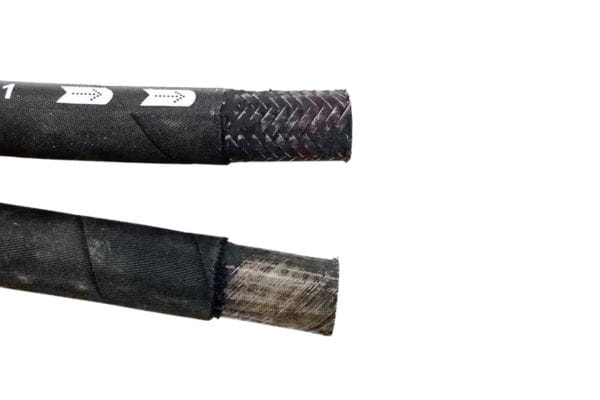
B. Materials and Construction
Hydraulic hoses are made from a variety of materials, each selected for specific performance characteristics depending on the application. The most common materials used in hydraulic hoses include:
Rubber: The most widely used material for hydraulic hoses, rubber offers excellent flexibility, durability, and resistance to abrasion and weathering. Synthetic rubber compounds, such as nitrile, are often used for the inner tube to provide compatibility with various hydraulic fluids, while the outer cover is typically made from a tougher rubber compound to protect against external damage.
Thermoplastics: Thermoplastic hoses are lightweight and offer superior chemical resistance compared to rubber hoses. They are often used in applications where the hydraulic fluid contains aggressive chemicals or where the operating environment is harsh. Thermoplastic hoses are also known for their resistance to UV radiation and are suitable for outdoor use.
PTFE (Teflon): PTFE hoses are used in applications requiring high-temperature resistance, chemical compatibility, and low friction. These hoses are ideal for environments where extreme conditions are present, such as aerospace and chemical processing industries. PTFE hoses are also used when the hydraulic fluid needs to be transported with minimal contamination.
Reinforcement Layers: The reinforcement layer of a hydraulic hose is critical for its ability to withstand high pressures. This layer can be made from materials such as braided or spiraled steel wire, textile fibers, or even high-strength aramid fibers (e.g., Kevlar). The number and type of reinforcement layers depend on the pressure rating and intended use of the hose. Braided steel wire provides flexibility and moderate pressure resistance, while spiral wire reinforcement offers greater pressure resistance but less flexibility.
Outer Cover: The outer cover of a hydraulic hose is designed to protect the hose from environmental factors such as abrasion, chemicals, and extreme temperatures. It can be made from a variety of materials, including synthetic rubber, thermoplastics, and other specialized compounds.
C. Construction
The construction of hydraulic hoses typically involves several layers:
Inner Tube: The inner tube is the innermost layer of the hose, designed to carry the hydraulic fluid. It must be compatible with the specific fluid being used and resistant to any chemical reactions.
Reinforcement Layer: The reinforcement layer(s) provide the hose with its strength and ability to withstand internal pressure. Depending on the hose’s design, it may have one or multiple layers of reinforcement, such as braided steel wire or textile fibers.
Outer Cover: The outer cover is the protective layer that shields the reinforcement and inner tube from external damage. This layer is crucial for extending the life of the hose, particularly in demanding environments.
D. Advantages of Hydraulic Hoses
Hydraulic hoses offer several advantages, making them the preferred choice in many dynamic and flexible hydraulic systems:
Flexibility: The primary advantage of hydraulic hoses is their flexibility, which allows them to be routed through tight spaces and around obstacles. This flexibility is essential in applications where the hose needs to move or flex with the equipment, such as in mobile machinery or articulated arms.
Ease of Installation: Hydraulic hoses are relatively easy to install compared to rigid tubes. They can be cut to length on-site, and their flexibility allows for easy routing without the need for precise measurements or complex fittings. This ease of installation reduces downtime and labor costs.
Vibration Dampening: Hydraulic hoses can absorb shocks and vibrations that would otherwise be transmitted through the hydraulic system. This dampening effect helps protect sensitive components from damage and reduces noise levels in the system.
E. Common Applications
Hydraulic hoses are used in a wide variety of applications where flexibility and movement are required. Some common applications include:
Mobile Equipment: Hydraulic hoses are extensively used in mobile machinery such as excavators, loaders, and cranes. Their flexibility allows them to accommodate the constant movement and articulation of the equipment, ensuring a reliable flow of hydraulic fluid to various components.
Flexible Connections: In hydraulic systems where components must be connected but are not aligned, hydraulic hoses provide the necessary flexibility to bridge the gap. This is common in systems where the components move relative to each other, such as in hydraulic presses or robotic arms.
Systems with Frequent Movement: Hydraulic hoses are ideal for applications where the system is in constant motion or where the hose must bend repeatedly during operation. Examples include conveyor systems, automated machinery, and lifting equipment.
Temporary or Portable Systems: Hydraulic hoses are often used in temporary setups or portable hydraulic systems because they can be quickly and easily connected and disconnected. This makes them ideal for applications like emergency hydraulic repair systems or portable hydraulic testing rigs.
Key Differences Between Hydraulic Tubes and Hoses
A. Flexibility
Flexibility is one of the most significant differences between hydraulic tubes and hoses, and it plays a critical role in determining their usage in various hydraulic systems.
Hydraulic Tubes: Hydraulic tubes are rigid and inflexible, designed to maintain their shape under pressure. This rigidity makes them suitable for applications where stability and precise fluid transmission are crucial. However, the lack of flexibility means that hydraulic tubes require precise alignment during installation. They are best suited for static systems where components are fixed, and there is no need for movement or bending.
Hydraulic Hoses: In contrast, hydraulic hoses are highly flexible and capable of bending and maneuvering around obstacles within a system. This flexibility allows hoses to be routed through tight spaces and to accommodate the movement of machinery parts. Hydraulic hoses are ideal for dynamic systems where components are in motion or where frequent adjustments are necessary. The ability of hoses to flex and bend without compromising their integrity makes them indispensable in mobile equipment, articulated machinery, and other applications requiring frequent movement.
Impact on Usage: The flexibility of hoses allows for greater versatility in system design, particularly in environments where space constraints or complex layouts are present. In contrast, the rigidity of tubes provides a stable and secure pathway for fluid transmission, making them ideal for high-precision applications where movement is minimal. In deciding between tubes and hoses, engineers must consider the specific movement and layout requirements of the system to ensure optimal performance and reliability.
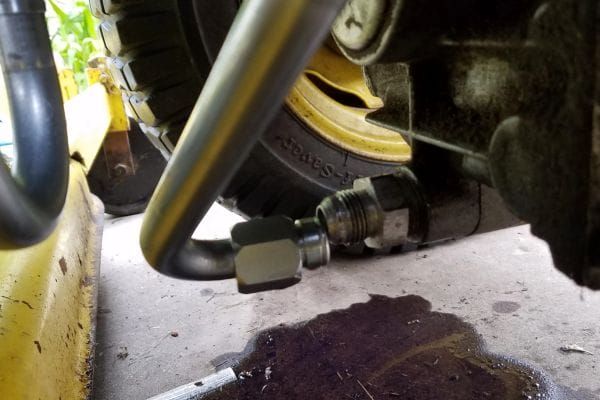
B. Pressure Handling
Pressure handling capability is another critical factor that distinguishes hydraulic tubes from hoses.
Hydraulic Tubes: Hydraulic tubes generally have a higher pressure rating than hoses, thanks to their rigid construction and thicker walls. The seamless nature of many tubes further enhances their ability to withstand high pressures without deforming or bursting. This makes hydraulic tubes the preferred choice for applications involving extremely high pressures, such as industrial machinery, aerospace, and high-pressure hydraulic systems. Tubes are less likely to experience pressure-related failures, which contributes to their reliability in demanding environments.
Hydraulic Hoses: While hydraulic hoses are designed to handle substantial pressures, they typically have lower pressure ratings compared to tubes. Hoses rely on multiple layers of reinforcement, such as braided steel wire or textile fibers, to provide the necessary strength to withstand pressure. However, the flexibility that makes hoses so versatile also means that they can expand slightly under pressure, which can lead to pressure drops and potential system inefficiencies. The pressure rating of a hose is also more variable, depending on factors like the number of reinforcement layers, the material of the inner tube, and the construction of the hose.
Impact on Usage: When selecting between tubes and hoses, pressure requirements are a key consideration. In systems where maintaining high pressure is critical, and where any expansion or flexing could lead to performance issues, hydraulic tubes are typically the better choice. In contrast, hydraulic hoses may be suitable for lower-pressure systems or where flexibility is a more critical factor than pressure integrity.
D. Installation and Maintenance
Hydraulic Tubes: Installing hydraulic tubes can be a more complex and time-consuming process compared to hoses. Due to their rigidity, tubes require precise alignment and accurate measurements during installation. They often need specialized fittings and tools to ensure secure connections, and any misalignment can lead to leaks or system failures. Additionally, the rigid nature of tubes makes them less adaptable to changes in system layout, meaning that modifications or repairs can be challenging.
Maintenance for hydraulic tubes is generally minimal, as their rigid construction makes them less prone to wear and damage. However, if a tube does fail, it often requires full replacement rather than a simple repair, which can be costly and time-consuming.
Hydraulic Hoses: Hydraulic hoses are easier to install due to their flexibility. They can be cut to the required length on-site, routed through tight spaces, and connected using standard fittings. This ease of installation reduces labor costs and downtime. However, hoses require more frequent maintenance than tubes. The flexible materials used in hoses are more susceptible to wear, abrasion, and damage from environmental factors, which means that hoses may need to be inspected and replaced more often.
Maintenance tasks for hoses include checking for leaks, ensuring that the hose is not kinked or twisted, and replacing worn or damaged sections. The ease of installation and repair makes hoses a more convenient option for systems where frequent adjustments or maintenance are expected.
Impact on Usage: The choice between tubes and hoses can significantly impact the installation and maintenance costs of a hydraulic system. In systems where long-term reliability and minimal maintenance are priorities, hydraulic tubes may be the better choice despite the more complex installation process.
F. Environmental and Operating Conditions
The environmental and operating conditions of a hydraulic system are crucial factors that influence whether tubes or hoses are more suitable for the application.
Temperature: Hydraulic tubes, particularly those made from metals like steel or stainless steel, can withstand a wider range of temperatures compared to hoses. This makes tubes ideal for environments where extreme heat or cold is present, such as in industrial furnaces or outdoor applications in harsh climates. Hoses, depending on their material composition, can also handle a broad range of temperatures, but they may be more prone to degradation at the extremes. For example, rubber hoses can become brittle in cold temperatures or may soften and lose strength in high heat.
Chemical Exposure: Hydraulic tubes, especially those made from stainless steel or with specialized coatings, offer excellent resistance to chemical exposure. This makes them suitable for use in environments where the hydraulic fluid or surrounding atmosphere contains corrosive chemicals. Hoses, particularly those made from materials like PTFE, can also provide good chemical resistance, but the outer cover and reinforcement layers must be carefully selected to ensure compatibility with the chemicals involved.
Abrasive Environments: In environments where abrasion is a concern, such as in mining or construction, the outer cover of a hydraulic hose is at risk of damage. While hoses can be designed with abrasion-resistant covers, they are generally more vulnerable to wear than tubes. Hydraulic tubes, with their solid metal construction, are inherently more resistant to abrasion and are better suited for harsh, abrasive environments.
Conclusion
In conclusion, the key differences between hydraulic tubes and hoses revolve around flexibility, pressure handling, installation, maintenance, and environmental suitability. Tubes offer rigidity, high-pressure capabilities, and durability, making them ideal for stationary systems with precise requirements. In contrast, hoses provide flexibility, ease of installation, and adaptability, suiting dynamic environments where movement is frequent. When deciding between the two, consider your system’s specific needs, including pressure, space, and maintenance requirements.
FAQ
What is the main difference between hydraulic tubes and hoses?
Hydraulic tubes are rigid and inflexible, ideal for high-pressure, stationary applications, while hydraulic hoses are flexible, making them suitable for dynamic systems where movement and flexibility are required.
When should I use a hydraulic tube instead of a hose?
Use a hydraulic tube when your application requires high pressure handling, durability, and minimal movement, such as in industrial machinery or high-precision systems.
Are hydraulic hoses more prone to wear and tear than tubes?
Yes, hydraulic hoses are more prone to wear and tear due to their flexible nature and exposure to environmental factors, requiring more frequent maintenance and replacement.
How does temperature affect the choice between hydraulic tubes and hoses?
Hydraulic tubes, particularly metal ones, can withstand a wider range of temperatures compared to hoses, making them better suited for extreme temperature environments.
What factors should I consider when selecting between a hydraulic tube and a hose?
Consider application-specific needs, pressure and flow requirements, space and flexibility constraints, and maintenance and accessibility when choosing between a tube and a hose.
Can hydraulic hoses be used in high-pressure applications?
Yes, hydraulic hoses can be used in high-pressure applications, but they generally have lower pressure ratings than tubes. The appropriate hose should be selected based on its pressure rating and reinforcement layers.