A hydraulic hose spiral layer is a specialized layer of steel wire wound around the core of the hose. This spiral construction serves as a reinforcement to increase the hose’s pressure rating, flexibility, and resistance to wear and tear. Unlike braided hoses, which use interwoven wire strands, the spiral layer is wound in a continuous, helical pattern, providing superior strength and durability under extreme conditions.
The Basics of Hydraulic Hose Construction
Hydraulic hoses are essential components in any hydraulic system, designed to transfer fluid under high pressure. The construction of these hoses involves multiple layers that work together to ensure the hose can handle demanding conditions.
Components of a Hydraulic Hose
A typical hydraulic hose is made up of several components that ensure it functions effectively. These components include:
Inner Tube: The innermost layer that carries the hydraulic fluid. It’s designed to be resistant to the specific type of fluid being used (e.g., oil, water, or chemicals).
Reinforcement Layer: This is the critical layer that gives the hose strength and flexibility. It may consist of spiral-wound steel wire, braids, or textile yarn, depending on the hose type.
Outer Cover: The outermost layer protects the hose from external damage, such as abrasions, UV rays, weather exposure, and chemicals. It’s made from durable materials like rubber, PVC, or thermoplastic.
Materials Used in Hydraulic Hose Construction
The materials used in hydraulic hose construction are carefully chosen to match the operating conditions and the type of hydraulic fluid being transferred. Common materials include:
Rubber: Flexible and resistant to weather, ozone, and UV damage, rubber is often used in the outer cover and inner tube. It’s also available in different grades to resist various chemicals and temperatures.
PVC (Polyvinyl Chloride): Often used in industrial hoses, PVC is lightweight and resistant to corrosion but not as durable under extreme conditions compared to rubber.
Steel Wire: Used in reinforcement layers, steel wire can be wound in spirals or braided patterns to provide additional strength. Spiral steel wire layers offer higher pressure ratings and better flexibility under stress.
Nylon and Polyester: These materials are used in some types of reinforcement, offering strength while maintaining flexibility, often in lower-pressure hoses.
Teflon: For hoses that need to handle corrosive chemicals or extreme temperatures, Teflon offers excellent chemical resistance and can be used for inner tubes or covers.
The Role of Reinforcement Layers in Hose Performance
Reinforcement layers play a vital role in the overall performance of a hydraulic hose. These layers:
Increase Pressure Rating: Reinforcement layers, especially spiral or braided steel wires, allow the hose to withstand higher pressures without bursting or becoming deformed.
Improve Flexibility: While providing strength, reinforcement layers also contribute to the hose’s flexibility, allowing it to bend without kinking, which is crucial in tight or complex hydraulic systems.
Enhance Durability: The reinforcement helps protect the hose from external damage such as abrasion, cutting, and impacts, thus prolonging the hose’s lifespan in demanding environments.
Prevent Expansion: The reinforced layers prevent the hose from expanding under high pressure, ensuring the hydraulic system remains efficient and the fluid is transferred smoothly.
Hydraulic Hose Spiral Layer: What Makes It Different?
When it comes to hydraulic hose design, the spiral layer is often considered a superior choice for high-pressure applications. But what exactly sets it apart from other hose designs, like braided hoses?
Spiral vs. Braided Hose Design
While both spiral and braided hoses are commonly used in hydraulic systems, they have distinct design features and applications. The main differences include:
Design Pattern:
Spiral Hoses: These hoses are constructed by winding steel wire in a continuous spiral around the hose core. The wire winds at a consistent angle, creating multiple layers of reinforcement, which can be increased depending on the pressure rating required.
Braided Hoses: Braided hoses, on the other hand, consist of multiple layers of wire braided together, often using two or more layers. This braiding pattern creates a crisscross effect that provides strength and durability but usually offers less flexibility compared to spiral hoses.
Pressure Handling:
Spiral Hoses: Designed to handle much higher pressures, spiral hoses are perfect for extreme hydraulic applications where there are sudden pressure spikes or high operating pressures. They are less likely to fail under intense conditions.
Braided Hoses: Typically used for moderate pressure applications, braided hoses perform well in environments where pressure levels are not as extreme, but they are not as resistant to high-pressure surges.
Flexibility:
Spiral Hoses: While spiral hoses offer superior pressure resistance, they can be less flexible than braided hoses due to their structure. However, newer designs incorporate advanced spirals that enhance flexibility while maintaining strength.
Braided Hoses: Known for their flexibility, braided hoses are easier to handle and route through tight spaces, but they may not provide the same pressure protection as spiral hoses.
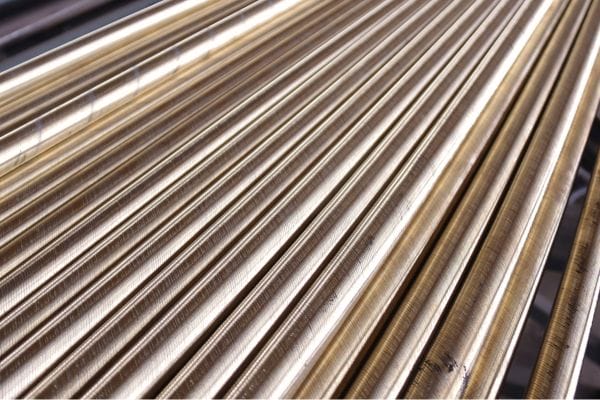
How the Spiral Layer Enhances Strength and Flexibility
The spiral layer in hydraulic hoses is engineered to provide a perfect balance of strength and flexibility. Here’s how:
Enhanced Strength: The helical nature of the spiral layer creates a tight, continuous reinforcement that prevents the hose from expanding under pressure. This layer absorbs the force exerted by the hydraulic fluid, preventing hose rupture, expansion, or collapse. Multiple layers of spiral wire increase the hose’s strength, making it capable of withstanding high pressure and heavy-duty use.
Increased Flexibility: While strength is crucial, flexibility is equally important in hydraulic hoses. The spiral construction allows the hose to remain flexible and bend without kinking or restricting fluid flow. This is particularly valuable in dynamic applications where the hose needs to move or bend regularly. Spiral hoses are designed to bend with ease, while still providing superior resistance to pressure.
Resistant to Twisting and Curling: Unlike braided hoses, spiral hoses are less likely to twist or curl when subjected to movement or bending. This means they are more reliable in environments where the hose must handle dynamic motions, such as machinery or industrial equipment.
The Role of Spiral Steel Wire in Reinforcement
The spiral steel wire used in hydraulic hoses plays a key role in providing the strength and pressure resistance that makes these hoses ideal for high-demand environments. Here’s how it works:
High Tensile Strength: The steel wire used in the spiral reinforcement has high tensile strength, meaning it can handle the internal pressure exerted by the hydraulic fluid without breaking or distorting. This is essential for applications where the hose is subjected to high-pressure surges or constant high-pressure flow.
Resistance to Abrasive Forces: Spiral steel wire also helps the hose resist external damage from abrasion. Whether it’s wear caused by movement, exposure to sharp objects, or rubbing against other surfaces, the spiral steel wire provides a protective shield, enhancing the hose’s durability and life cycle.
Pressure Distribution: The steel wire in the spiral layer evenly distributes internal pressure along the length of the hose, reducing the risk of localized pressure buildup. This pressure distribution ensures that the hose can handle stress evenly, preventing weak spots that could lead to failure.
Prevents Expansion: When exposed to high internal pressure, hoses without proper reinforcement can expand, which can compromise performance. The spiral steel wire prevents the hose from stretching or bulging, ensuring that the fluid flow remains uninterrupted and the hose maintains its structural integrity.
How Hydraulic Hose Spiral Layers Handle High Pressure
Hydraulic hoses are often subjected to extreme pressures, and the ability to safely handle these pressures is crucial for the functionality and safety of hydraulic systems. Spiral layers, in particular, are designed to provide robust protection against high-pressure fluctuations.
Pressure-Rated Hoses: Why It Matters
A pressure-rated hose is a hose that is designed and tested to handle a specific pressure range without failing. This rating is a critical specification for any hydraulic system, as it directly impacts the system’s performance, safety, and durability.
Safety First: Pressure-rated hoses ensure that the hydraulic system operates within safe pressure limits, preventing hose rupture or leaks. The pressure rating of a hose indicates the maximum pressure it can safely handle before failure, providing peace of mind to operators and maintenance teams.
Industry Standards: Most hydraulic systems are governed by industry standards that specify the required pressure ratings for various components. These ratings are often determined based on factors like the system’s fluid type, operating temperature, and intended application. Spiral-wound hoses, with their superior reinforcement, can often achieve higher pressure ratings than braided hoses.
Consistent Fluid Flow: Pressure-rated hoses maintain consistent fluid flow without loss of pressure, ensuring that hydraulic components like pumps, cylinders, and valves operate efficiently. This is essential for systems that require precision and reliability, such as in manufacturing or heavy machinery operations.
The Importance of Spiral Layers in Managing High-Pressure Fluctuations
Hydraulic systems can experience pressure fluctuations due to factors such as system startup, changes in load, or unexpected resistance within the system. Spiral layers play a crucial role in managing these pressure fluctuations, which can otherwise lead to hose failure if not properly controlled.
Pressure Distribution: The spiral reinforcement in hydraulic hoses evenly distributes the internal pressure across the hose, preventing localized pressure spikes that could damage the hose. This even distribution allows the hose to better withstand surges or drops in pressure, which is common in dynamic hydraulic systems.
Resilience Under Stress: When a system undergoes pressure fluctuations, spiral layers allow the hose to maintain its structural integrity. The continuous spiral wire reinforcement absorbs these fluctuations, ensuring that the hose doesn’t expand, weaken, or burst. This ability to manage fluctuating pressures makes spiral-wound hoses ideal for high-demand environments where the pressure is not always consistent.
Prevention of Kinking or Buckling: During sudden pressure increases, hoses without sufficient reinforcement may kink or buckle, compromising the system’s fluid flow. The spiral layers in these hoses allow for greater flexibility and resilience, ensuring the hose retains its shape and pressure resistance, even under intense conditions.
Burst Pressure and How Spiral Layers Help Prevent Failure
Burst pressure is the pressure at which a hose will fail or rupture. Understanding burst pressure is essential for selecting the right hose for an application, as hoses that fail under high pressure can lead to dangerous leaks, system shutdowns, and expensive repairs.
Burst Pressure and Hose Integrity: The burst pressure rating indicates the maximum pressure that a hydraulic hose can withstand before it bursts. Spiral-wound hoses are designed to handle higher burst pressures due to their strong, continuous reinforcement layers. These layers of steel wire help prevent the hose from expanding beyond its capacity, even in high-pressure scenarios.
How Spiral Layers Prevent Burst Failure: Spiral layers provide multi-layer protection that enhances the hose’s ability to withstand high-pressure surges. Each additional spiral layer offers added strength, distributing the pressure more effectively and preventing failure at weak points. Spiral layers also prevent the hose from becoming distorted under pressure, ensuring that the hose does not burst, crack, or rupture when subjected to extreme forces.
Enhanced Burst Pressure Safety: Spiral-wound hoses are often rated for burst pressures several times higher than their working pressures. This margin of safety is crucial for systems that deal with unpredictable or intermittent high-pressure conditions, such as hydraulic presses, construction equipment, or oil rigs.
Customization and Specifications of Hydraulic Hose Spiral Layers
Choosing the right hydraulic hose is crucial for the efficiency and safety of your hydraulic system. With hydraulic hose spiral layers, there are many customization options available that allow you to tailor the hose’s specifications to meet the demands of your specific application.
Understanding Hydraulic Hose Specifications
Hydraulic hose specifications are essential for determining whether a particular hose will meet the needs of your system. These specifications help identify the hose’s performance characteristics, pressure handling capacity, and material compatibility with the fluid being transferred. Here’s a breakdown of the key specifications you should consider when selecting a hydraulic hose:
Pressure Rating: The pressure rating of a hose indicates the maximum working pressure (MWP) the hose can safely handle during operation. It’s crucial to select a hose with a pressure rating that matches or exceeds the pressure requirements of your hydraulic system.
Burst Pressure: The burst pressure is the maximum pressure at which the hose will fail. Choosing a hose with a burst pressure well above your system’s operating pressure provides an extra margin of safety.
Temperature Range: Hydraulic systems operate in varying temperature conditions, so it’s important to select hoses that can handle both high and low temperatures. Spiral-layer hoses are often designed to withstand extreme temperatures, whether in freezing conditions or high-heat environments.
Chemical Compatibility: The hose material must be compatible with the hydraulic fluid in your system. Whether it’s oil, water, or other chemicals, choosing the right hose material prevents degradation, leaks, and system failure.
Flexibility and Bend Radius: Depending on your system’s layout, you may need hoses that can bend easily without restricting fluid flow. Spiral hoses offer a good balance of flexibility and pressure resistance, but it’s important to check the hose’s bend radius to ensure it suits your needs.
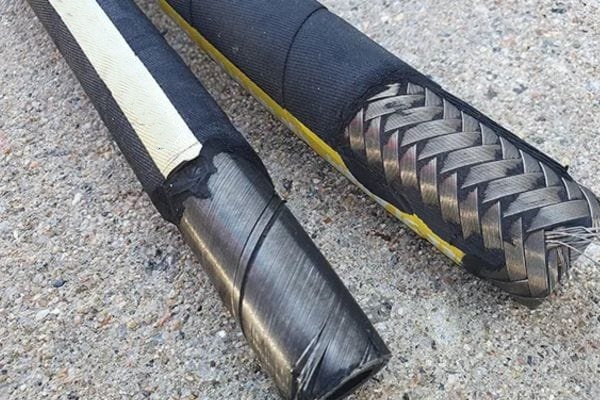
Customizing Spiral Layer Hoses for Specific Applications
One of the main advantages of spiral layer hoses is their customizability. These hoses can be tailored to meet the specific needs of various industries and applications, ensuring optimal performance and safety.
Application-Specific Pressure and Size: Hydraulic systems vary greatly in terms of pressure and flow rate. Spiral layer hoses can be customized to meet specific pressure requirements, from standard industrial applications to extreme high-pressure conditions, such as those found in the oil and gas industry. Customizing the hose’s diameter and length also ensures it fits perfectly within the constraints of your system.
Material Choices for Unique Environments: Depending on the environment in which the hose will operate, customization may include selecting specific materials for the inner tube, reinforcement layer, and outer cover. For example, for systems exposed to high temperatures, a heat-resistant outer cover can be used, while corrosive environments might require hoses with a Teflon or stainless steel inner tube.
Flexible Reinforcement: The spiral reinforcement can be customized for applications requiring more flexibility or more robust strength. If you need a hose that can flex around tight corners, choosing a hose with an optimized spiral layer for flexibility is essential. On the other hand, more demanding applications requiring higher pressure ratings can benefit from adding additional spiral layers for extra strength and durability.
Abrasion Resistance and Outer Cover Customization: Spiral hoses can be customized with specific outer covers designed for wear protection. Options include covers made from materials such as polyurethane, rubber, or PVC, each offering different levels of abrasion resistance. If the hose will be exposed to frequent friction or physical stress, adding an abrasion-resistant cover is essential for preventing damage.
Anti-Static and Fire Resistance: For applications where flammable materials are present, such as in oil and gas operations, customizing a spiral-layer hose to include anti-static properties or fire-resistant materials is a must. Special additives in the hose construction can prevent static buildup and offer better protection against flames or sparks.
How to Choose the Right Hose for Your Hydraulic System
Selecting the right hydraulic hose with spiral layers for your system involves evaluating several factors to ensure it will perform optimally and provide long-lasting service. Here’s a step-by-step guide to help you make an informed decision:
Assess Pressure and Flow Requirements: Start by determining the pressure requirements of your hydraulic system. Choose a hose with a pressure rating that meets or exceeds your system’s operating pressure, and ensure it has the appropriate burst pressure. Don’t forget to assess flow rate to ensure the hose can handle the volume of hydraulic fluid required.
Consider Temperature Extremes: If your hydraulic system operates in high-heat or sub-zero environments, choose a hose that can withstand those temperatures without compromising performance. Spiral-layer hoses are often more temperature-resistant than braided hoses, making them ideal for extreme conditions.
Select the Right Material for FluidCompatibility: Consider the type of hydraulic fluid used in your system. Oils, water, and chemicals each require specific materials for the hose’s inner tube to avoid degradation. Spiral layer hoses offer excellent compatibility with a wide range of fluids, but it’s important to choose the correct material for the job.
Evaluate Flexibility and Bend Radius: Depending on the layout of your hydraulic system, flexibility may be crucial. Spiral-layer hoses tend to offer better flexibility than braided hoses, but it’s important to check the bend radius to ensure that the hose can handle tight corners or bends without restricting fluid flow or causing damage.
Consider Abrasion Resistance and Environmental Protection: Think about the environment in which the hose will operate. Will it be exposed to external damage such as abrasion, UV rays, or chemicals? Spiral hoses can be customized with a tough outer cover to resist such external factors, providing longer hose life and reliability in harsh environments.
Conclusion
Spiral-layer hoses are highly versatile, suitable for a wide range of industries, and contribute significantly to reducing operational costs while improving system safety and performance. The right investment in high-quality spiral-layer hoses will enhance the overall reliability of your hydraulic system, reduce the frequency of repairs and replacements, and ensure smooth and uninterrupted operations in demanding environments.
FAQ
What is a hydraulic hose spiral layer?
A hydraulic hose spiral layer is a reinforcement layer made from spiral-wound steel wire, designed to enhance the strength, pressure resistance, and flexibility of the hose. It helps the hose withstand high-pressure environments and external damage, ensuring durability and performance.
Why do I need a spiral layer in my hydraulic hose?
The spiral layer provides superior strength and pressure resistance, making it ideal for high-pressure hydraulic systems. It also increases the hose’s flexibility, protects against abrasion, and reduces the risk of hose failure under extreme conditions.
What industries use hydraulic hoses with spiral layers?
Hydraulic hoses with spiral layers are commonly used in industries such as construction, agriculture, mining, oil and gas, and manufacturing, where high-pressure systems are necessary, and durability is crucial.
How do spiral-layer hoses differ from braided hoses?
Spiral-layer hoses have continuous spiral steel wire reinforcement, providing higher pressure resistance and durability. In contrast, braided hoses use interwoven wire strands, offering flexibility but typically handling lower pressure and being more prone to damage under harsh conditions.
Can spiral-layer hoses be customized for my application?
Yes, spiral-layer hoses can be customized in terms of pressure ratings, hose length, material types, and outer covers to suit the specific needs of your hydraulic system, whether it requires heat resistance, chemical compatibility, or abrasion protection.
How do I maintain hydraulic hoses with spiral layers?
Regular inspections for wear, abrasions, or leaks are essential. Make sure to avoid kinking, excessive bending, or exposure to harsh chemicals. Proper storage and handling will extend the lifespan of your spiral-layer hose ensuring optimal performance over time.