With the prolonged use of equipment, the hydraulic system may experience sluggish response, which not only reduces work efficiency but also may affect operational accuracy. The reasons for the slow response of the hydraulic system are multiple, usually involving hydraulic pumps, hydraulic oil, valves, cylinders, and other components of the performance problems. For these possible failures, taking appropriate measures to solve the problem, can effectively improve the response speed of the system to ensure the normal operation of the equipment.
Common Causes of Slow Hydraulic System Response
Hydraulic Pump Performance Decline
Overview of Hydraulic Pump Functions The hydraulic pump is the heart of any hydraulic system. Its primary function is to convert mechanical energy from a power source (such as an electric motor or engine) into hydraulic energy by pressurizing the fluid. This high-pressure fluid is then directed through the system to power actuators, valves, and other hydraulic components. The pump ensures a continuous flow of hydraulic fluid, enabling precise control over various mechanical movements. A well-functioning pump is essential for maintaining the overall efficiency and performance of the system.
Impact of Performance Decrease Over time, the performance of hydraulic pumps may deteriorate due to factors such as wear, internal leaks, or component degradation. When the pump starts to wear down, its ability to generate sufficient pressure and flow diminishes. This reduction in performance can lead to several problems, including:
Insufficient Flow: The pump may no longer provide the required flow of hydraulic fluid, causing delays in system response.
Pressure Fluctuations: Increased wear can cause internal gaps and leaks, leading to inconsistent pressure, which results in erratic or slow operation of actuators and valves.
System Inefficiency: A declining pump performance means the system may require more time to reach the desired pressure levels, slowing the overall responsiveness of the machinery.
Signs of Pump Issues several indicators may suggest the hydraulic pump is malfunctioning:
Noise: A common symptom of pump wear or damage is unusual noise, such as grinding, whining, or cavitation sounds, which indicate internal damage or low fluid levels.
Overheating: If the pump is struggling to maintain pressure, it may work harder than usual, leading to overheating.
Irregular Pressure Fluctuations: If the pump can’t maintain consistent pressure, the system may experience erratic movements or reduced responsiveness, making it harder to control machinery precisely.
Reduced Fluid Transfer Efficiency
Contamination of Hydraulic Fluid Hydraulic fluid is vital to the performance of the system, carrying both lubricating and cooling properties. Contaminants such as dirt, dust, water, or air can enter the system and degrade the fluid’s quality. Contaminated fluid can cause several issues:
Blockages: Dirt and debris can clog filters, valves, and other components, reducing fluid flow and system efficiency.
Corrosion and Wear: Water or air in the fluid can lead to internal corrosion, further deteriorating pump, valve, and cylinder components.
Loss of Lubrication: Contaminants can reduce the fluid’s ability to lubricate key components, resulting in increased wear and reduced system performance.
Viscosity Changes The viscosity of hydraulic fluid plays a critical role in the system’s ability to operate efficiently. Temperature variations and aging can alter the fluid’s viscosity, causing it to become either too thick or too thin. This can lead to:
Poor Lubrication: If the fluid is too thick, it may not flow easily enough to lubricate parts, increasing friction and wear on components.
Inefficient Fluid Transfer: If the fluid becomes too thin, it may not maintain adequate pressure or volume, causing sluggish system responses.
Fluid Leaks Leaks in the hydraulic system, whether in the pipes, seals, or fittings, can severely impact performance. Leaking fluid results in a loss of pressure and fluid volume, which can lead to:
Pressure Loss: A drop in fluid levels or pressure will slow down response times and may lead to complete system failure if left unaddressed.
Air Ingress: Leaks may allow air to enter the system, causing aeration of the fluid, which reduces the efficiency of the hydraulic system and leads to erratic or slow performance.
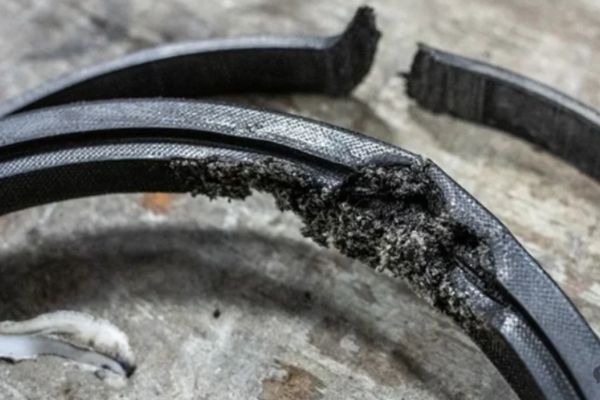
Mechanical Component Wear and Tear
Valve and Cylinder Issues Hydraulic valves and cylinders are crucial components for controlling fluid direction, pressure, and flow. Over time, these parts may wear out or malfunction, leading to issues such as:
Worn Valves: Valves that are worn or dirty may not operate as intended, resulting in inconsistent flow or pressure. This causes delays in system responses and leads to poor control of machinery movements.
Cylinder Malfunctions: Worn cylinders can suffer from internal leakage or damage to seals, which diminishes their ability to generate the required force or movement, ultimately slowing down the system.
Seal Degradation Hydraulic seals prevent fluid from leaking out of the system and maintain pressure within components. As seals age, they can degrade, become brittle, or lose their flexibility, leading to:
Internal Leaks: A degraded seal can allow fluid to escape from critical components, reducing pressure and flow, which in turn increases response time.
Pressure Loss: The compromised seals can also lead to a gradual loss of hydraulic pressure, slowing down the system’s ability to respond quickly to control inputs.
Control Element Failures
Valve Control Problems Hydraulic valves are used to regulate the flow of fluid within the system. Issues with valve controls, whether due to improper calibration, electrical faults, or mechanical failure, can lead to significant performance problems:
Improper Calibration: Valves that are not properly calibrated may either restrict or over-permit fluid flow, causing irregular pressure and delayed responses.
Electrical Faults: If valves are electronically controlled, any electrical malfunction—such as wiring issues or faulty solenoids—can disrupt the smooth operation of the system and lead to slow responses or erratic behavior.
Sensor Failures Modern hydraulic systems rely on sensors to monitor parameters such as pressure, flow, and temperature. Faulty sensors may provide incorrect data to the control system, leading to:
Incorrect Pressure Control: If a pressure sensor malfunctions, the system may not be able to accurately regulate pressure, causing delays or erratic movements.
Delayed Feedback: Slow or inaccurate sensor readings can result in delayed feedback to the control system, leading to lag or instability in the hydraulic response.
Solutions to Improve Hydraulic System Response
Maintain and Inspect Hydraulic Pumps
Regular Maintenance Schedule One of the most effective ways to ensure your hydraulic pump continues to perform optimally is by setting a regular maintenance schedule. Inspections should focus on identifying early signs of wear, leaks, or any irregularities in performance. This includes monitoring for unusual vibrations, sounds, or temperature fluctuations that may indicate an issue. Regular checks help identify problems before they escalate, preventing unexpected downtime and costly repairs.
Replace Worn Parts Hydraulic pumps are composed of several components that are subject to wear over time, such as seals, gears, and bearings. If these parts begin to degrade, the pump’s efficiency declines, leading to slow system responses. It’s essential to replace these components as soon as signs of wear are detected. Replacing worn parts promptly ensures that the pump can maintain its pressure and flow capacity, keeping the system responsive.
Pump Testing and Calibration Routine testing of hydraulic pumps is crucial to assess their performance and efficiency. A pump test can identify issues like reduced flow capacity or internal leaks that aren’t visible during physical inspections. Calibration should also be part of this process to ensure that the pump is delivering the correct pressure and flow rate to meet system requirements. If any discrepancies are found, recalibrating the pump or replacing faulty components may be necessary to restore optimal function.
Improve Fluid Quality and Condition
Regular Fluid Changes Hydraulic fluid can become contaminated over time due to external dirt, water, or internal wear from metal particles. Contaminated fluid reduces the efficiency of the hydraulic system, leading to slow or erratic responses. Regular fluid replacement is essential to maintain fluid integrity and avoid issues like clogged filters or wear on components. It’s also important to ensure that the right type of fluid is used, based on the system’s specific needs and environmental conditions.
Filtration Systems Investing in high-quality filtration systems can significantly improve fluid quality and extend the life of the hydraulic components. Filters trap contaminants like dirt, metal shavings, and water from entering the system, preventing damage to critical components such as pumps and valves. Regularly changing filters and monitoring their performance helps keep the fluid clean and ensures smooth operation.
Monitor Viscosity The viscosity of hydraulic fluid plays a crucial role in ensuring proper flow and lubrication within the system. If the fluid’s viscosity is too high or too low for the operating temperature, it can lead to sluggish or uneven system performance. Regularly checking and adjusting the fluid viscosity to suit the operating conditions—such as changes in ambient temperature—helps maintain smooth and efficient operation.
Replace or Repair Worn Mechanical Components
Valve Overhaul Hydraulic valves regulate the flow and pressure of the fluid within the system, and if they become worn or malfunction, they can cause uneven or slow response times. Overhauling valves by disassembling, cleaning, and replacing worn components ensures they operate correctly. Regular valve servicing is critical to maintaining precise flow control and preventing issues like leakage or misalignment, which can lead to system inefficiency.
Cylinder Maintenance Cylinders are key components in hydraulic systems, responsible for converting hydraulic energy into mechanical motion. Over time, cylinders can develop leaks, suffer from seal degradation, or experience misalignment. Regular inspection and maintenance of cylinders, including checking for damage, wear, and ensuring proper alignment, can prevent delays in movement and ensure that the system responds smoothly.
Seal Replacement Seals are essential for maintaining pressure within a hydraulic system. When seals wear out, they can cause internal leakage, which directly impacts system pressure and flow, leading to slow or inconsistent responses. Replacing worn seals before they fail can prevent performance degradation and help maintain the hydraulic system’s efficiency.
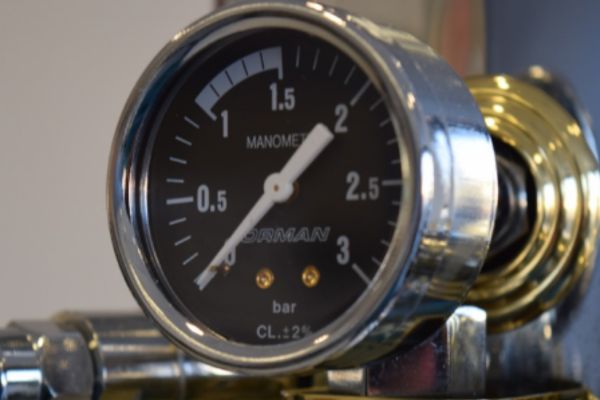
Address Control System Failures
Valve Control Calibration If the valves in a hydraulic system are not properly calibrated, the system may experience problems with regulating flow and pressure, leading to slow or erratic responses. Ensuring that all control valves are correctly calibrated to the system’s specifications is crucial. Regular recalibration can help adjust for any changes in the system’s performance due to wear or environmental factors, ensuring accurate flow control.
Sensor Maintenance Hydraulic systems rely on sensors to provide real-time data on parameters like pressure, temperature, and flow. If sensors become faulty or lose calibration, they may provide inaccurate readings that can affect system performance. Regular maintenance, including testing and recalibration of sensors, is essential to ensure that the system operates within the correct parameters. Accurate sensor data enables better control and faster response times.
Control System Upgrades Over time, older hydraulic control systems may become outdated or insufficient for modern operational needs. Upgrading to more advanced control systems can provide benefits like improved accuracy, better responsiveness, and increased reliability. Implementing digital or electronic control systems, such as proportional or servo valves, can enhance performance and ensure the hydraulic system responds quickly and accurately to commands. Upgrading may also reduce the frequency of manual interventions, improving overall system efficiency.
Prevention Strategies for Long-term System Stability
Implement a Preventative Maintenance Plan
Scheduled Inspections A comprehensive preventative maintenance plan is essential for maintaining the long-term health and performance of hydraulic systems. The first step in this plan should be to create a detailed schedule for inspecting all system components, including pumps, valves, cylinders, and seals. Inspections should be done at regular intervals—whether monthly, quarterly, or annually—depending on the frequency of system use. During these inspections, key aspects such as fluid quality, pressure levels, component wear, and system leaks should be assessed. The goal is to identify early signs of wear or degradation before they lead to costly repairs or system downtime.
Condition Monitoring Advanced condition monitoring is a valuable tool for maintaining hydraulic system stability. By using sensors and real-time data logging systems, operators can continuously monitor key parameters such as pressure, temperature, flow rate, and fluid contamination levels. This allows for early detection of potential issues that might not be visible through manual inspections. For example, subtle changes in pressure or temperature may indicate wear or impending failure of a component. With condition monitoring, maintenance teams can predict and address issues proactively, minimizing the risk of unexpected failures and ensuring smooth system operation over the long term.
Training and Skill Development for Operators
Proper Operation Techniques Proper training for hydraulic system operators is critical to preventing premature system wear and ensuring long-term stability. Operators should be taught the correct handling and operational procedures, such as avoiding overloading the system, using the correct fluid type, and adhering to the recommended operational parameters (e.g., pressure, temperature, and flow). Educating operators about the impact of improper usage, such as overpressurization or incorrect valve manipulation, can prevent unnecessary strain on the system. By following best practices, operators can help maintain system efficiency and prevent costly damage to hydraulic components.
Troubleshooting Skills Equipping operators with basic troubleshooting skills is a proactive strategy for minimizing downtime and preventing the escalation of minor issues into major problems. Operators should be trained to identify common signs of system malfunction, such as unusual noises, fluctuating pressure readings, or slow response times. With these skills, operators can quickly diagnose issues and take immediate corrective actions, such as adjusting flow rates or shutting down the system before further damage occurs. This not only ensures quick resolution of minor issues but also helps operators develop a deeper understanding of the hydraulic system, which is essential for optimizing long-term performance.
Conclusion
By implementing regular maintenance schedules, improving fluid quality, replacing worn mechanical components, and addressing control system failures, operators can significantly enhance hydraulic system performance. Additionally, the adoption of preventative maintenance plans and the use of real-time condition monitoring can help detect issues early, preventing costly breakdowns and extending the lifespan of the equipment.
FAQ
What causes slow response in a hydraulic system?
Slow response in hydraulic systems can be caused by issues such as pump performance decline, contaminated or aging hydraulic fluid, worn-out mechanical components (e.g., valves or cylinders), or control system failures (e.g., faulty sensors or miscalibrated valves).
How often should I inspect my hydraulic system?
Regular inspections are crucial for maintaining system performance. A typical schedule might involve monthly or quarterly checks, depending on usage. Inspections should focus on key components like the pump, fluid quality, seals, and valves.
What maintenance can prevent hydraulic system issues?
Preventative maintenance includes routine checks, replacing worn parts (e.g., seals, bearings), changing hydraulic fluid regularly, and ensuring proper calibration of valves and sensors. Condition monitoring with sensors can also help detect early signs of failure.
How can I improve fluid quality in my hydraulic system?
To maintain fluid quality, replace hydraulic fluid at regular intervals, install high-quality filtration systems to prevent contamination, and monitor fluid viscosity to ensure it remains suitable for the system’s operating temperature.
What should I do if my hydraulic system is making unusual noises or overheating?
Unusual noises or overheating often indicate issues like pump wear, internal leaks, or insufficient fluid flow. It’s essential to inspect the pump, check for fluid leaks, and test the system’s pressure and flow rate to identify the root cause.
Why is operator training important for hydraulic system performance?
Proper operator training ensures that users handle the system correctly, avoiding overloading, improper usage, or mistakes that could damage components. It also equips operators with basic troubleshooting skills to quickly address minor issues, reducing downtime.