Heat treatment of metal materials is a technology that changes the internal or surface structure of the material through the process of heating, holding, and cooling to improve its properties. Heat treatment process occupies an important position in mechanical manufacturing, especially in the processing of metal materials, which can improve the physical properties of the workpiece, mechanical properties, corrosion resistance, etc., and these improvements are usually achieved through changes in microstructure, which are difficult to detect with the naked eye.
Heat Treatment Overview
Definition and Basic Principles
Heat treatment is a process in which metal fittings are heated to a specific temperature, held at that temperature for a period, and then cooled at a controlled rate (either quickly or slowly). The primary objective of heat treatment is to alter the microstructure of the metal, which in turn enhances its mechanical properties such as hardness, strength, toughness, and ductility.
The core aim of heat treatment is to modify the metal’s microstructure at the atomic or crystalline level. This can involve processes like grain size alteration or phase transformation (such as austenite to martensite), which lead to significant improvements in the material’s physical properties. For example, by controlling the cooling rate, heat treatment can determine whether a material becomes hard, tough, or resistant to wear.
In most heat treatment processes, the changes are not visible to the naked eye, but they result in significant improvements in the material’s performance, making it more suitable for a wide range of industrial applications. Heat treatment is often employed to optimize metal alloys, making them more durable and reliable in demanding environments.
Characteristics of Heat Treatment Processes
Heat treatment differs from other manufacturing processes in several key ways. Unlike mechanical or chemical processing techniques, heat treatment does not change the external shape or overall chemical composition of the workpiece. Instead, it focuses on the internal microstructure and surface properties to improve performance. This is typically achieved by modifying the arrangement of the material’s atoms or crystals, which can significantly affect the metal’s strength, toughness, or resistance to fatigue.
The benefits of heat treatment are primarily realized through changes in the metal’s microstructure. For example, processes like grain coarsening or phase transformation can drastically improve mechanical properties such as hardness and tensile strength, while also enhancing material characteristics like resistance to corrosion and wear. These microstructural changes occur at the atomic level, often invisible to the naked eye, but they are crucial in determining the material’s performance.
Because heat treatment involves precise control over temperature and cooling rates, it can be tailored to achieve specific material properties, depending on the requirements of the application. Some heat treatments may result in a softer, more ductile material ideal for forming, while others may produce a hardened surface that is resistant to wear and tear.
In industrial applications, heat-treated components are commonly used in machinery, tools, automotive parts, and aerospace components, where high-performance materials are essential for functionality and safety. The ability to control and enhance these properties through heat treatment provides manufacturers with a valuable tool to produce components with superior performance characteristics.
Overall Heat Treatment
Overall heat treatment is a vital process in metallurgy that involves heating the entire workpiece to a specific temperature and then cooling it in a controlled manner. This method is designed to alter the internal microstructure of the metal, optimizing its mechanical properties such as hardness, strength, toughness, and ductility. Unlike surface treatments, overall heat treatment affects the entire mass of the material, making it suitable for components that require uniform performance throughout.
The heat treatment process is critical for improving the material’s behavior under stress, extending its lifespan, and ensuring it meets the specific performance standards required for its intended application.
Annealing
Process: Annealing involves heating the metal to a predetermined temperature, followed by a slow cooling process, typically in the furnace or air. The cooling rate is deliberately controlled to achieve the desired material properties.
Purpose: The primary goal of annealing is to relieve internal stresses that may have been induced during previous manufacturing steps (like forging or casting). Additionally, it softens the material, improves ductility, and enhances its machinability. By refining the grain structure, annealing also makes the material more uniform and stable, which is particularly beneficial for metals that will undergo further shaping or forming processes.
Applications: Annealing is widely used in industries where components need to be shaped or welded without compromising their material properties. It is commonly applied to steel, copper, aluminum, and other alloys to prepare them for further processing.
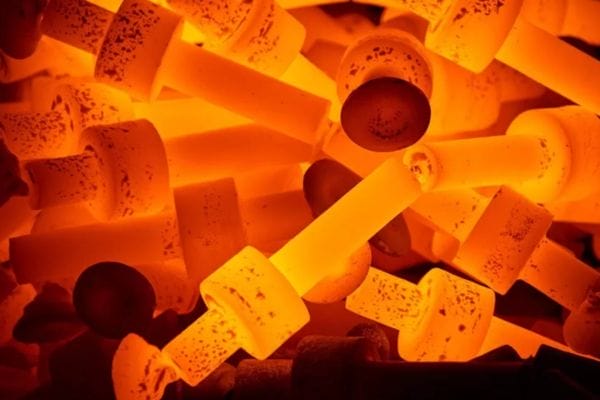
Normalizing
Process: Normalizing involves heating the metal to a temperature slightly above its critical temperature (the point at which the material’s crystal structure transforms), and then allowing it to cool in still air. The cooling is done at a controlled rate to avoid rapid temperature changes.
Purpose: The main goal of normalizing is to refine the metal’s grain structure and enhance its mechanical properties. This process promotes a uniform, fine-grained microstructure, which enhances strength and toughness. It also improves the material’s hardness and wear resistance, especially in carbon steels.
Applications: Normalizing is commonly used in steel production, particularly for medium and high-carbon steels. It is also beneficial for improving the consistency of large components or materials that are not suitable for quenching.
Quenching
Process: Quenching involves rapidly cooling a heated metal, typically by immersion in water, oil, or other quenching media. The metal is heated to a high temperature, usually above the critical temperature, and then suddenly cooled to “trap” the material in a hardened state.
Purpose: The primary purpose of quenching is to harden the material by increasing its strength and wear resistance. Rapid cooling prevents the metal’s microstructure from returning to a softer phase, such as ferrite, resulting in a more robust, hardened state (e.g., martensite in steel).
Caveats: While quenching significantly increases hardness, it also makes the material more brittle due to the stresses created by rapid cooling. As a result, quenching is often followed by tempering to restore some of the lost toughness and reduce brittleness.
Applications: Quenching is widely used in manufacturing tools, cutting tools, gears, and high-strength machine components that require superior hardness and wear resistance. It is particularly essential in the production of high-carbon steels and alloy steels.
Tempering
Process: After quenching, the metal often needs to be tempered to reduce brittleness and increase toughness. Tempering involves reheating the quenched material to a lower temperature (usually between 150°C and 650°C, depending on the desired properties), then cooling it at a controlled rate. This reduces internal stresses caused by the rapid quenching process.
Purpose: The goal of tempering is to strike a balance between hardness and toughness. While quenching makes the material very hard, it also makes it brittle. Tempering reduces this brittleness by promoting a more stable microstructure, which enhances toughness and ductility without significantly reducing the hardness achieved during quenching.
Applications: Tempering is used extensively in the production of steel tools, structural components, and springs where a combination of hardness, toughness, and flexibility is needed. It is often the final step in the heat treatment process for carbon and alloy steels, ensuring the material is suitable for heavy-duty applications.
Surface Heat Treatments
Surface heat treatment focuses on altering the properties of a metal’s surface layer while leaving its internal microstructure largely unchanged. This targeted modification of the surface is critical for improving the performance characteristics of materials, particularly in components that experience high levels of wear, friction, or stress. By enhancing the surface hardness, wear resistance, and fatigue strength, surface heat treatment ensures that the material can perform better in demanding applications, all while maintaining the desirable properties of the bulk material, such as toughness and ductility.
Surface heat treatments are typically employed when the functional requirements demand improved surface performance, but without altering the underlying core properties of the metal. These processes are highly effective in extending the lifespan of components subjected to harsh working conditions, such as gears, shafts, and engine parts.
Carburizing
Process: Carburizing is a surface hardening process in which carbon is diffused into the surface of low-carbon steel by heating it in a carbon-rich environment, typically in a furnace or a gas atmosphere. After the steel is exposed to the carbon source, the material is rapidly quenched to lock in the hardened surface layer.
Purpose: The primary goal of carburizing is to produce a hard, wear-resistant surface while maintaining a softer, tougher core. This creates a material that has excellent wear resistance on the outside but retains high toughness and shock resistance in the core, which is crucial for components that experience both high surface wear and impact loading.
Applications: Carburizing is commonly used for parts that require high surface hardness and wear resistance, such as gears, crankshafts, camshafts, and other high-performance automotive and industrial components.
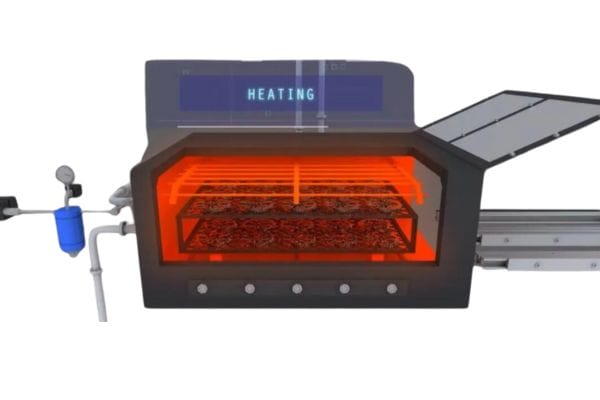
Nitriding
Process: Nitriding involves introducing nitrogen into the surface of a steel or alloy at elevated temperatures, typically in the range of 500–550°C. This process forms hard, nitrogen-rich compounds (like iron nitrides) on the surface of the material, which significantly enhances its hardness.
Purpose: Unlike carburizing, nitriding does not require quenching, which helps reduce dimensional changes and distortion. The surface treatment increases the hardness, wear resistance, and corrosion resistance of the material, making it ideal for parts that operate in corrosive environments or under high wear conditions.
Applications: Nitriding is often used for components such as valves, pistons, turbine blades, and other precision mechanical parts where surface durability and resistance to corrosion are critical.
Induction Hardening
Process: Induction hardening uses electromagnetic induction to heat a localized area of the workpiece to a high temperature, typically using high-frequency alternating currents. Once the desired surface temperature is reached, the part is rapidly quenched, usually in water or oil, to achieve hardening.
Purpose: This process is particularly effective for hardening specific areas of a part, such as the outer surfaces of shafts, gears, or bearings, without affecting the core properties. The surface becomes hard and wear-resistant, while the core remains tough and ductile, which is ideal for components subjected to cyclic loading or high-impact conditions.
Applications: Induction hardening is commonly used in automotive and industrial applications for parts like gears, shafts, and other components that require localized hardening to resist wear and fatigue while maintaining a strong core.
Other Treatments
Solution Treatment
Process:
Solution treatment involves heating an alloy to a high temperature range (typically 980°C to 1250°C), maintaining a constant temperature within the single-phase region to allow excess phases to dissolve into the solid solution. After a specific period, the material is rapidly cooled, usually by water or oil quenching, to preserve the dissolved state.
Purpose:
Achieving a Single-Phase Austenitic Structure: By heating the alloy to a high temperature, all phases dissolve into the solid solution, resulting in a uniform microstructure.
Improving Ductility and Toughness: This treatment helps enhance the plasticity and toughness of materials, preparing them for subsequent treatments like precipitation hardening.
Solid Solution Strengthening: Dissolving different phases improves the material’s hardness, toughness, and resistance to corrosion.
Relieving Internal Stresses: Solution treatment eliminates internal stresses within the material, which is important for further processing or forming.
Cryogenic Treatment
Process:
Cryogenic treatment involves cooling a material, typically after quenching, to extremely low temperatures, usually between -40°C and -80°C, using mediums like dry ice or liquid nitrogen. The material is held at this low temperature for a period, allowing for uniform cooling, before gradually bringing it back to room temperature.
Purpose:
Enhanced Wear Resistance: Cryogenic treatment helps transform retained austenite into martensite, increasing hardness and wear resistance.
Reduced Residual Stresses: It reduces internal stresses, improving dimensional stability in precision components.
Improved Toughness: The treatment can also enhance the material’s toughness by reducing brittleness, particularly in high-strength steels.
Refined Microstructure: The process refines the grain structure, which can improve the overall mechanical properties of the material.
Aging
Process:
Aging, or precipitation hardening, is a heat treatment process that involves heating a material (often an alloy) to a specific temperature, holding it there for a set period, and then cooling it. This process promotes the precipitation of fine particles within the material, which strengthens the solid solution by obstructing dislocation movement.
Purpose:
Increased Strength and Hardness: Precipitation hardening forms fine precipitates that hinder dislocation motion, increasing the material’s strength and hardness.
Control of Material Properties: The aging process can be adjusted to achieve specific material properties, such as increased hardness or improved corrosion resistance.
Improved Wear Resistance: The strengthening phase formed during aging also improves the wear resistance of the material.
Enhanced Thermal Stability: The treatment increases the material’s ability to resist deformation and degradation at high temperatures.
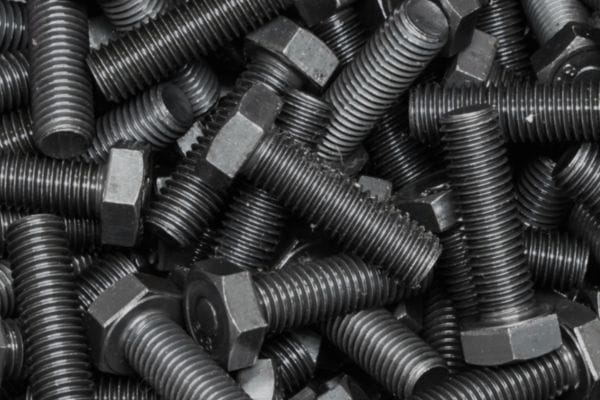
Blackening
Process:
Blackening (also known as black oxide coating) is a surface treatment that forms a protective oxide layer on the metal, typically using a chemical bath. The metal is immersed in a bath containing oxidizing agents, and a thin black oxide layer is formed on the surface, which provides both corrosion resistance and an attractive finish.
Purpose:
Corrosion Resistance: The black oxide layer offers some protection against corrosion, preventing rust and oxidation, especially in mild conditions.
Improved Appearance: It provides an aesthetically pleasing, uniform black finish to the metal, often used in consumer goods or decorative applications.
Reduced Friction: The process can reduce friction and wear, making it suitable for parts subject to regular movement or interaction.
Enhanced Durability: In some cases, blackening can enhance the durability of components by reducing surface oxidation under exposure to certain environments, although it’s not as protective as other coatings like galvanizing or anodizing.
Applications of Surface Heat Treatments
Surface heat treatments play a critical role in enhancing the surface properties of materials while preserving the desirable characteristics of the core. These techniques are widely used in industries where components are subjected to high wear, corrosion, or fatigue, such as automotive, aerospace, manufacturing, and tooling. Below are two prominent applications of the surface heat treatments process that significantly improve the performance of metal parts.
Induction Hardening (High-Frequency Hardening)
Process: Induction hardening involves locally heating a specific area of a workpiece using electromagnetic induction, followed by rapid cooling (quenching). The heating is typically done using high-frequency currents, which focus the heat on the surface layer of the metal, leaving the inner core unaffected.
Purpose: The primary goal of induction hardening is to increase the surface hardness and wear resistance of the component while keeping the core relatively soft and tough. This technique allows manufacturers to selectively harden parts without affecting their entire structure.
Applications: Induction hardening is commonly used for components like gears, shafts, camshafts, and tool parts that require a high surface hardness for wear resistance but need to maintain internal toughness for strength and shock resistance. It is especially useful for parts that experience concentrated, localized stresses, such as gears in transmissions or high-speed motors.
Advantages: The process offers precise control over the depth and location of the hardened zone. It also allows for quick processing times, minimizing energy consumption compared to traditional methods like furnace hardening. Additionally, the parts are hardened without altering the overall dimensions, making it ideal for complex geometries.
Laser Cladding (Laser Surface Alloying)
Process: Laser cladding, also known as laser surface alloying, uses a high-powered laser beam to melt a metal powder or wire feed that is applied to the surface of a workpiece. The heat generated by the laser causes the surface to melt, and the added material bonds to the substrate, forming a new layer of hard, wear-resistant metal.
Purpose: This process creates a hard, corrosion-resistant surface on the workpiece. The cladded layer can improve the material’s resistance to wear, corrosion, oxidation, and other harsh environmental factors. Laser cladding can also be used to repair worn-out components or to add new properties to existing materials without affecting the bulk material’s integrity.
Applications: Laser cladding is widely used in industries such as aerospace, automotive, and power generation. For example, it is commonly applied to turbine blades, molds, and dies, as well as engine components that require a hard surface capable of withstanding high-temperature conditions. It is also utilized for adding wear-resistant coatings to parts that are exposed to frictional wear.
Advantages: One of the significant advantages of laser cladding is its precision. The laser beam can be tightly controlled, ensuring that the coating is applied only to the targeted areas, reducing material waste. Additionally, the process can be used to apply a wide variety of materials, including alloys with specialized properties for corrosion or wear resistance. Furthermore, the rapid cooling of the cladded layer can result in improved hardness and metallurgical bonding between the surface layer and the base material.
Selection and Optimization of Heat Treatment Processes
The selection and optimization of heat treatment processes are crucial steps in achieving the desired material properties for a specific application. Heat treatment allows manufacturers to tailor a material’s mechanical properties, such as hardness, strength, toughness, and wear resistance, to meet the demands of different industries and applications.
Key Factors for Selecting Heat Treatment Processes:
Material of the Workpiece
The material composition is one of the most important factors in selecting a heat treatment process. Different metals and alloys respond differently to heat treatment. For example, steel alloys may undergo processes like carburizing or nitriding to enhance surface hardness, while aluminum alloys might require aging to improve strength.
The carbon content in steel, for example, plays a significant role in determining which heat treatment processes are applicable. High-carbon steels may be more suitable for processes like quenching, while low-carbon steels often undergo carburizing to improve their surface hardness.
Intended Use of the Component
The function of the part or component in its intended application dictates the required material properties. For example, parts that experience high stress, wear, or fatigue, such as gears, bearings, or tools, may require surface hardening methods like induction hardening or nitriding.
In contrast, parts that need high ductility, toughness, and formability, such as structural components or machine parts, may require annealing or normalizing processes to relieve internal stresses and improve machinability.
Size and Geometry of the Workpiece
The size and shape of the workpiece influence the heat treatment process chosen. Larger components may require more controlled heating and cooling rates to ensure uniform temperature distribution, while smaller parts can often be treated more rapidly and with greater precision.
The geometry of the workpiece also matters. For complex shapes, localized heat treatment methods, such as induction hardening, may be more appropriate for selectively hardening specific areas of the part without affecting the entire structure.
Required Performance Characteristics
Different applications require different combinations of material properties. For instance, high wear resistance and surface hardness may be required for components like cutting tools or gears, which would necessitate surface treatments like carburizing, nitriding, or laser hardening.
On the other hand, components that need a balance of hardness and toughness, such as structural parts or suspension components, may benefit from overall heat treatment processes like quenching followed by tempering to achieve an optimal combination of strength and ductility.
How to Optimize Heat Treatment Processes
Optimizing the heat treatment process involves selecting the most appropriate method based on the specific needs of the application. This requires a detailed analysis of the following:
Tailoring Process Parameters to Material Needs
Adjusting factors such as temperature, cooling rates, and time is essential to achieving the desired material properties. For example, controlling the cooling rate in quenching determines whether the material becomes brittle or retains its toughness. Fine-tuning the parameters ensures that the material achieves the right combination of hardness, toughness, and other properties.
Selecting the Right Method for the Application
Based on the application, the heat treatment method should be chosen to achieve the required mechanical properties. For example, carburizing may be optimal for improving wear resistance on parts like gears and shafts, while nitriding may be more suitable for parts that require improved fatigue resistance and corrosion resistance, such as engine components or turbine blades.
For applications requiring selective hardening, induction hardening is ideal, as it allows for precise control over which areas of the part are hardened.
Considering the Size and Production Efficiency
Larger batches or high-production volumes often require heat treatment processes that are efficient and scalable, such as furnace-based methods (annealing, normalizing). In contrast, smaller batch production or more complex geometries may benefit from more localized treatments such as induction hardening or laser hardening, where precision and speed are critical.
Minimizing Distortion and Residual Stresses
Optimizing the heat treatment process also involves minimizing distortions and residual stresses that can occur during heating and cooling. Techniques like controlled cooling or post-treatment stress relieving may be required to ensure the part maintains its shape and dimensional accuracy after heat treatment.
Balancing Cost and Performance
In industrial applications, cost-effectiveness is often a crucial factor. The selected heat treatment method should not only meet the performance requirements but also fit within budget constraints. For example, while processes like carburizing or nitriding offer excellent surface performance, they may be more expensive and time-consuming compared to simpler processes like annealing or normalizing.
Conclusion
In conclusion, while chemical and surface heat treatments already play a crucial role in improving the performance and longevity of metal hydraulic fitting components, ongoing developments in technology, environmental sustainability, and precision manufacturing promise to further enhance the effectiveness and efficiency of these processes. As industries continue to demand more advanced and specialized materials, heat treatment will remain a critical tool for ensuring that metal components can meet the increasingly complex and rigorous demands of modern manufacturing.
FAQ
What is heat treatment?
Heat treatment is a process used to alter the physical and mechanical properties of a metal by heating and cooling it in a controlled way. This process can improve characteristics such as hardness, strength, and durability.
What are the types of heat treatment?
The main types of heat treatment are overall heat treatment, surface treatment, and chemical heat treatment (which alters the material’s surface chemistry).
Why is heat treatment important in manufacturing?
Heat treatment is essential because it improves the material’s performance, extending its lifespan and ensuring it can withstand wear, stress, and fatigue in demanding environments like automotive, aerospace, and tooling.
What is carburizing?
Carburizing is a heat treatment process where carbon is introduced into the surface layer of steel at high temperatures to create a hard, wear-resistant surface while maintaining a tough, ductile core.
How does nitriding improve metal properties?
Nitriding involves introducing nitrogen into the surface of the steel, creating a hard, wear-resistant layer that also enhances corrosion resistance, making it ideal for components subjected to high wear, like gears and turbine blades.
How can I optimize the heat treatment process for my parts?
Optimizing heat treatment involves choosing the appropriate method based on the material, part size, and required properties. Factors like the workpiece’s intended use, required hardness, and wear resistance should guide your decision-making.