Pressure testing plays a vital role in confirming that hydraulic systems can operate safely and efficiently under their designed pressure conditions. During hydraulic pressure testing, technicians simulate real-world conditions to check whether the system can handle the expected pressure without failure. The process identifies any weak points or potential issues before they cause major disruptions or safety hazards.
Why Hydraulic Pressure Testing Matters
Hydraulic systems are complex networks where every component, from pumps to hoses, works in tandem under high-pressure conditions to perform critical functions. When pressure testing is skipped or improperly executed, it puts the entire system at risk of operational failure. Let’s break down why pressure testing is non-negotiable in maintaining the integrity and safety of hydraulic systems.
Preventing Leaks and Failures in Hydraulic Systems
Leaks are one of the most common and costly issues in hydraulic systems. A leak, no matter how small, can lead to:
Fluid Loss: Hydraulic fluid is the lifeblood of the system, and any loss can reduce the system’s effectiveness, leading to poor performance.
Component Wear: Even minor leaks can cause increased wear on nearby components, especially if fluid escapes onto critical parts like seals or electrical connections.
System Failure: In the worst-case scenario, a failure to address leaks can cause catastrophic system breakdowns, resulting in unexpected downtime and expensive repairs.
Pressure testing helps detect these leaks early by pressurizing the system and visually inspecting it for signs of failure, before they become larger problems. Identifying and repairing leaks during pressure testing helps maintain the reliability of the system and prevent future disruptions.
Ensuring Safety in High-Pressure Environments
Hydraulic systems operate at extremely high pressures, sometimes exceeding several thousand PSI (pounds per square inch). Under such conditions, even the slightest weakness in a hose, valve, or connection can result in a dangerous failure. A rupture or burst in a high-pressure system can lead to serious injuries, environmental damage, or fatalities.
Pressure testing helps ensure that:
Pressure Limits Are Safe: Systems are tested to ensure they can safely withstand the maximum operating pressure without risking rupture or failure.
Components Are Secure: By checking for leaks and faulty seals, pressure testing ensures that critical components, such as hydraulic hoses and fittings, are securely installed and functioning as intended.
Worker Safety: Preventing catastrophic failures through pressure testing reduces the risk of accidents, ensuring the safety of operators and maintenance personnel working with the system.
Without proper pressure testing, you’re essentially working blind, leaving the system vulnerable to unsafe conditions that could have been detected and rectified during testing.
The Impact on Performance and Longevity of Hydraulic Components
Hydraulic systems are a significant investment for any operation, and the longevity and performance of the system’s components are essential to maximizing that investment. Pressure testing plays a crucial role in:
Ensuring Optimal Performance: If a hydraulic system is not pressurized properly or has an undetected fault, it will not operate at peak efficiency. Pressure testing ensures all components work as designed, allowing the system to perform at its best.
Extending Component Lifespan: Regular pressure testing helps identify weak points before they lead to wear and tear. By addressing these issues early, the lifespan of costly hydraulic components like pumps, motors, and valves is extended, reducing the need for expensive replacements.
Reducing Unscheduled Downtime: Without pressure testing, unnoticed faults or weak components can cause sudden breakdowns, resulting in unexpected downtime. By catching issues early, pressure testing helps to maintain consistent performance and avoid costly disruptions to operations.
Types of Hydraulic Pressure Testing
Pressure testing is not a one-size-fits-all process. Depending on the type of system, components, and operational conditions, different testing methods may be more suitable for identifying potential issues.
Static vs. Dynamic Pressure Testing
Pressure testing can be broadly categorized into two types based on how the system is tested:
Static Pressure Testing
Definition: Static pressure testing is performed while the hydraulic system is at rest, meaning no flow of fluid is involved during the test. The system is pressurized and held at a certain level for a designated period to check for leaks, structural integrity, and other issues.
When to Use: This test is ideal for checking the overall integrity of the system, including connections, seals, and valves. It’s commonly used for systems that do not require constant fluid motion during operation or where flow is not critical.
Benefits: It allows for detailed inspection of individual components like hoses, valves, and pipes without the distraction of moving fluid. It’s particularly useful for spotting slow leaks and ensuring no system parts are under undue stress.
Dynamic Pressure Testing
Definition: Dynamic pressure testing, on the other hand, simulates real working conditions by introducing pressure while the fluid is flowing through the system. This allows you to assess the system’s performance under operational pressure and flow.
When to Use: This method is most useful for testing systems under real-world operating conditions, where factors such as fluid flow, pressure surges, and temperature changes are in play.
Benefits: Dynamic testing gives insight into how the system performs under operational stresses and can help detect issues that would not be visible under static conditions, such as flow-induced vibrations or pressure spikes.
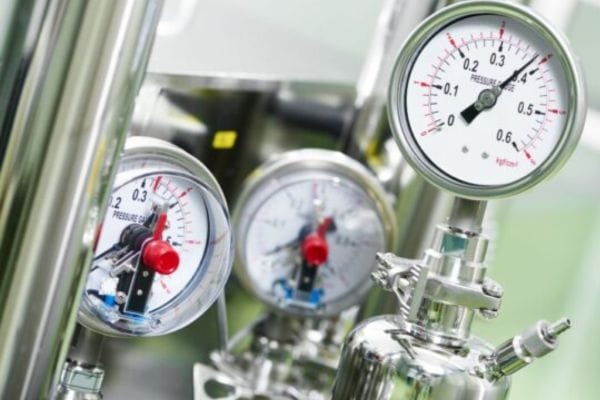
Hydrostatic Testing vs Pneumatic Testing
Hydrostatic and pneumatic testing are two of the most common methods used for pressure testing, and both have their unique applications and advantages.
Hydrostatic Testing
Definition: Hydrostatic testing involves filling the system with a liquid—usually water or hydraulic fluid—and then pressurizing it to check for leaks and structural integrity. Since water is virtually incompressible, it provides a stable and reliable medium for testing under pressure.
When to Use: Hydrostatic testing is typically used for testing pressure vessels, pipelines, and other components designed to carry liquids. It’s ideal for systems that use incompressible fluids like hydraulic oils.
Benefits: It’s one of the safest methods for high-pressure testing since water does not create a significant risk of explosion under pressure. Additionally, water can be easily monitored for leakage, and any fluid escaping from the system will be visible.
Pneumatic Testing
Definition: Pneumatic testing uses compressed air or another gas to pressurize the system instead of liquid. This method is typically used when the system will eventually operate with gases or air, such as in some pneumatic or gas-driven systems.
When to Use: Pneumatic testing is often used for low-pressure or gas-based systems, where hydraulic fluids are not involved. It’s also used when the system must be tested at a higher pressure than the system can safely handle with liquids.
Benefits: Pneumatic testing is ideal for systems that will operate with gases or compressed air. However, it requires extra caution due to the risk of explosive decompression if a failure occurs.
Burst Testing and Its Significance in Hydraulic Systems
Definition: Burst testing involves pressurizing a system or component to its maximum tolerance until it fails, or bursts. This test is used to determine the breaking point of a system and identify the maximum pressure the system can withstand.
When to Use: Burst testing is typically performed during the design or certification phase of hydraulic components, such as hoses, pipes, or pressure vessels, to verify their strength and safety under extreme conditions.
Benefits: This method provides critical data on the maximum pressure a component can safely endure before failure. It helps manufacturers design systems that can handle unexpected pressure surges without catastrophic failure.
Step-by-Step Guide to Pressure Testing Procedures
Pressure testing is a crucial process to ensure the safety and efficiency of your system. A well-executed test can help you identify weaknesses and prevent catastrophic failures.
Pre-Test Preparations and System Checks
Before applying any pressure to your hydraulic system, it’s essential to perform a series of checks and preparations to ensure the test is both accurate and safe.
Clean the System
Ensure that the system is free of contaminants, such as dirt, debris, or old fluid, which can affect test accuracy or cause system damage. Flush the system if necessary.
Inspect System Components
Check Hoses, Fittings, and Seals: Examine hoses, fittings, and seals for signs of wear or damage. These are often the first points where leaks occur, and it’s crucial that they are in optimal condition before testing.
Examine Valves and Pumps: Inspect valves and pumps to ensure they are functioning properly. Faulty components can give misleading test results.
Check Fluid Levels and Type
Ensure that the hydraulic fluid is at the correct level and that the correct type of fluid is being used for the test. Incorrect fluid could impact the system’s performance during the test.
Check Safety Equipment
Verify that all necessary safety equipment, such as pressure relief valves, are installed and functioning correctly. Safety glasses, gloves, and appropriate protective clothing should also be worn.
Setting the Correct Test Pressure
The pressure you apply during testing is crucial in simulating real operating conditions. Setting the correct test pressure ensures that the system is properly evaluated without being subjected to unnecessary strain.
Refer to Manufacturer Guidelines
Always check the manufacturer’s specifications for the system to determine the maximum operating pressure and test pressure recommendations. For most hydraulic systems, the test pressure is usually 1.5 to 2 times the system’s maximum working pressure.
Consider the Type of Test
Hydrostatic Testing: For hydrostatic testing, you typically apply a test pressure that is 1.5 to 2 times the working pressure to assess the system’s ability to withstand extreme conditions.
Pneumatic Testing: For pneumatic tests, the test pressure is usually slightly lower than the hydrostatic test pressure due to the compressibility of air, but it’s still important to ensure the system can safely handle the pressure.
Ensure a Steady Pressure Increase
Gradually apply pressure to avoid sudden surges that could cause damage or inaccurately simulate real operating conditions. This step is especially important during dynamic testing.
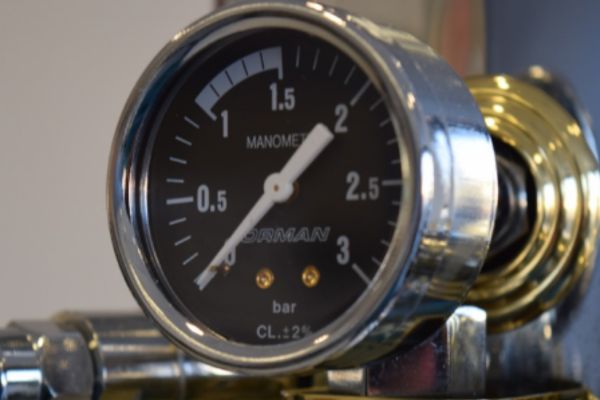
How to Perform a Hydraulic Pressure Test
Once all preparations are made and the correct test pressure is set, it’s time to conduct the test. The procedure involves applying pressure, monitoring the system, and checking for issues.
Connect the Test Equipment
Attach pressure gauges, sensors, or transducers to the appropriate points in the system. Ensure that they are properly calibrated and can measure the required pressure range.
Connect any additional test devices, such as flow meters, if needed.
Gradually Increase Pressure
Begin by slowly increasing the pressure to the system, ensuring the pressure is applied steadily and gradually. Monitor the system for any immediate signs of distress, such as unusual sounds or vibrations.
Hold the Pressure
Once the target pressure is reached, hold it for a specified period (usually 5 to 15 minutes). During this time, continuously monitor the system for leaks, pressure drops, or other issues.
Keep an eye on the pressure gauge to ensure the system maintains the test pressure for the entire duration of the test.
Inspect for Leaks or Failures
Visually inspect all parts of the hydraulic system, including hoses, fittings, seals, and valves. Look for any signs of fluid leakage or component deformation. Use a leak detection solution if necessary to identify small or hidden leaks.
Listen for any abnormal sounds that might indicate a problem, such as hissing (which may point to air leaks) or a sudden drop in pressure.
Post-Test Inspection and Data Interpretation
After the pressure test is complete, the system needs to be inspected for any changes in pressure, leaks, or damage. The data gathered during the test is crucial for determining the condition of the system and whether it is fit for operation.
Release Pressure Safely
Slowly release the pressure from the system in a controlled manner, ensuring that the pressure decreases gradually to avoid any sudden changes that could damage components.
Examine Pressure Readings
Review the pressure readings from the test. If there was a significant drop in pressure during the test, it indicates a leak or failure somewhere in the system. The pressure should ideally remain constant if the system is intact.
Inspect Components Thoroughly
After the test, thoroughly inspect all hydraulic components, including hoses, pumps, valves, and seals. Look for signs of wear, deformation, or leaks that may have developed during the test.
If any issues were detected during the test, identify the specific components that need to be repaired or replaced.
Record Data
Document all test results, including test pressure, duration, any issues encountered, and the condition of the components. This data is crucial for future reference, maintenance planning, and system improvements.
Make Necessary Repairs
If the test identifies leaks, pressure drops, or any signs of failure, perform the necessary repairs or replacements before returning the system to service. It may also be a good idea to re-test the system after repairs to ensure the issue has been fully resolved.
Best Practices for Hydraulic System Maintenance and Pressure Testing
How Often Should Hydraulic Pressure Tests Be Performed?
The frequency of pressure testing largely depends on factors such as system complexity, operating conditions, and manufacturer recommendations. However, here are some general guidelines:
At Installation or After Major Repairs
Always perform a pressure test immediately after installing a new system or replacing critical components like pumps, valves, or hoses. This helps confirm that the system is operating within its designed parameters and there are no leaks or faults.
Regular Interval Testing (Annually or Semi-Annually)
For most systems, it’s recommended to perform pressure testing at regular intervals. Annual or semi-annual testing is common, depending on the system’s usage and operating conditions.
High-usage or high-risk environments, such as construction equipment or manufacturing plants, may require more frequent testing to ensure safety and performance.
Post-Failure Testing
After any component failure or when troubleshooting issues like system leaks or pressure loss, pressure testing is necessary to identify the root cause and ensure the system is functioning correctly afterward.
During Preventive Maintenance
Routine maintenance tasks like changing fluid or inspecting components should always include a pressure test to ensure that the system continues to perform optimally.
Maintenance Tips for Hydraulic Pumps, Hoses, and Fittings
Hydraulic Pumps
Keep It Clean: Contamination is one of the leading causes of pump failure. Ensure that the pump’s filters are regularly cleaned or replaced to prevent debris from entering the system.
Check for Leaks and Wear: Periodically check for external leaks around pump seals and fittings. Worn seals or gaskets can lead to a loss in pressure and fluid contamination.
Monitor Performance: Keep an eye on the pump’s performance, such as noise levels, pressure output, and fluid temperature. Abnormal sounds or excessive heat are signs that the pump needs servicing.
Hoses and Fittings
Inspect Regularly: Hoses should be inspected for wear, abrasions, cracks, or bulging. Any signs of physical damage should be addressed immediately to prevent leaks or ruptures during operation.
Proper Storage: Avoid storing hydraulic hoses in direct sunlight or extreme temperatures, as UV rays and heat can degrade hose materials, leading to premature failure.
Ensure Proper Tightening: Loose or improperly tightened fittings are a common cause of leaks. Ensure all connections are securely tightened, but avoid over-tightening, which could damage the threads or seals.
Use Quality Components
Always use high-quality hydraulic components that meet manufacturer specifications. Subpar parts can compromise system performance and lead to costly repairs down the line.
Keeping Your Hydraulic System in Top Shape with Regular Pressure Testing
To ensure that your hydraulic system remains reliable over the long term, regular pressure testing is crucial. Here’s how you can integrate testing into your maintenance routine:
Test During Routine Inspections
Pressure testing should be part of your regular system inspections. Incorporating it into your annual or semi-annual maintenance schedule will help identify potential issues before they cause major failures.
Early Detection of Problems
Routine pressure tests allow you to detect early signs of wear, such as pressure fluctuations or minor leaks, which can be fixed before they escalate into larger, more expensive problems.
Maintain Proper Pressure Levels
Consistently testing for proper pressure levels ensures that your system is always operating within its designed parameters. If the system is running at higher pressures than it should, it can cause premature wear on components.
Optimize Fluid Quality and Pressure
Regular pressure testing helps to verify that the hydraulic fluid remains at the correct viscosity and that the system is not under excessive strain. This reduces the risk of fluid contamination and helps keep the system running efficiently.
Conclusion
In conclusion, pressure testing is a simple yet powerful tool that ensures the health of your system, keeps operations running efficiently, and prevents expensive and dangerous problems from arising. By integrating regular pressure testing and proactive maintenance into your system’s life cycle, you’ll improve both safety and performance while extending the lifespan of your hydraulic system.
FAQ
What is hydraulic pressure testing?
Pressure testing is a process where hydraulic systems are pressurized to a specified level to check for leaks, integrity, and performance under normal or extreme conditions.
Why is pressure testing important?
It helps prevent leaks, system failures, and safety hazards, ensuring that your hydraulic system operates efficiently and safely for a longer period.
How often should hydraulic pressure tests be performed?
Hydraulic pressure tests should be performed after major repairs or installations, at regular intervals (annually or semi-annually), and post-failure to ensure the system’s continued safety and reliability.
What are the common types of pressure testing?
Common testing methods include static pressure testing, dynamic pressure testing, hydrostatic testing, and pneumatic testing. Each method checks the system’s integrity under different conditions.
Can I perform pressure testing myself?
While it’s possible, it is recommended to have qualified personnel with proper tools and knowledge conduct pressure tests to ensure accuracy and safety.
What happens if pressure testing is skipped?
Skipping pressure testing can lead to unnoticed leaks, system failures, and potential safety hazards, causing costly repairs, downtime, and even accidents.