UNF threads, with their fine pitch, are ideal for applications requiring high strength and tight tolerances, while UNJF threads, designed for high-precision industries like aerospace, are tailored for more specialized, high-stress environments. The right thread type enhances performance, improves safety, and prevents mismatched parts or system failure, making it essential to match thread variations to specific project demands.
What Are UNJF vs UNF Threads?
Definition and History of UNF Threads
UNF threads, or Unified National Fine threads, are part of the Unified Thread Standard (UTS), which was introduced in the early 20th century to standardize threads in the United States. The UNF thread series was developed to offer a fine-pitched thread option, providing higher precision and stronger fastenings compared to coarse threads. This fine-pitch design allowed for greater holding power in smaller spaces, making it ideal for applications requiring high tension and minimal space. UNF threads are commonly used in a wide range of mechanical systems, from automotive to industrial machinery, where tight tolerance and high strength are necessary.
The UNF thread series has become one of the most widely adopted hydraulic fitting standards in the United States and globally, particularly in manufacturing, automotive, and construction sectors. Over time, variations such as UNC (Unified National Coarse) and UNJ (Unified National Aerospace) were introduced to cater to different needs, but UNF threads have remained a staple due to their versatile and reliable design.
The Rise of UNJF Threads: Why Was It Introduced?
The UNJF thread series, or Unified National Fine Thread Aerospace series, was introduced to meet the stringent demands of the aerospace and defense industries. The evolution from UNF to UNJF was driven by the increasing need for higher precision, better performance under extreme conditions, and tighter tolerances in high-stress environments.
Unlike UNF threads, which were designed for general mechanical applications, UNJF threads were engineered specifically to handle the extreme forces encountered in aerospace applications. These forces include high vibrations, pressure changes, and severe temperature variations. Additionally, the aerospace industry required a standardized thread that could guarantee the safety and integrity of components, given the critical nature of the equipment and the potentially hazardous consequences of failure.
UNJF threads are crafted with stricter tolerances and are designed to provide greater load-bearing capabilities. They are often used in aircraft, satellites, and military equipment, where failure is not an option. The introduction of UNJF threads represented a significant leap forward in thread technology, offering aerospace engineers a fastener that could withstand the rigorous demands of their field.
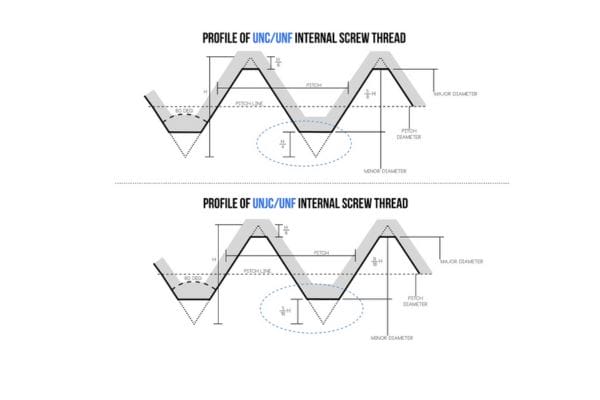
The Key Differences in Design and Application
While UNF and UNJF threads share similarities due to their common origin under the Unified Thread Standard, several key differences set them apart:
Parameter | UNF (Unified Fine Thread) | UNJF (Unified National Aerospace Fine Thread) |
Origin | Part of the Unified Thread Standard | Based on Unified Standard, specifically engineered for high-performance applications |
Thread Geometry | Standard fine-thread design | Modified geometry with a larger root radius for increased load-bearing capacity |
Tolerance & Precision | Standard tolerances, suitable for most industrial uses | Much tighter tolerances (typically Class 3A/3B), critical for aerospace-level precision |
Typical Applications | Automotive, construction, general mechanical and manufacturing | Aerospace, defense, and other high-stress, high-temperature, high-vibration environments |
Vibration Resistance | Adequate for most uses | Specifically designed for high-vibration and fatigue-resistance |
Thread Pitch | Finer than UNC, but generally not as fine as UNJF | Often finer and optimized for enhanced holding power in critical systems |
Load Capacity | Strong and reliable for general mechanical assemblies | Superior strength for extreme load conditions like in aircraft engines or spacecraft |
Interchangeability | Widely used and interchangeable within standard systems | Not interchangeable with UNF—incorrect substitution can cause thread damage or failure |
UNF vs UNJF: What’s the Real Difference?
Thread Pitch Comparison: Fine Threads vs. Coarse Threads
One of the most notable differences between UNF and UNJF threads lies in their thread pitch. Thread pitch refers to the distance between adjacent threads on a fastener, and it plays a significant role in determining the strength and application of a thread.
UNF Thread Pitch: UNF threads are considered fine threads, meaning the threads are closely spaced compared to coarse threads (such as UNC threads). The fine pitch provides higher precision and allows for a greater number of threads in a given length, which results in a finer, more compact connection. This makes UNF threads ideal for applications where a higher level of strength and tension control is required within a limited space. Fine threads also offer better resistance to vibration loosening, making them more suitable for mechanical systems exposed to fluctuating forces.
UNJF Thread Pitch: UNJF threads, on the other hand, have an even finer thread pitch than UNF threads. The tighter pitch of UNJF threads is specifically designed to provide maximum strength and load distribution, making them highly suitable for applications where safety, high tension, and extreme environmental conditions are critical. This is especially important in aerospace, where components may be exposed to tremendous forces, temperature fluctuations, and vibrations. The finer threads in UNJF offer superior precision and greater durability under stress.
In essence, while both UNF and UNJF threads fall under the “fine thread” category, UNJF threads are a refinement of UNF, engineered for even higher performance in specialized applications.
Thread Form and Its Impact on Strength
The thread form refers to the geometric shape of the thread, which directly influences how well the threads fit together, the strength of the fastener, and its ability to bear loads.
UNF Thread Form: UNF threads have a V-shaped thread form, which is common in many thread types. This shape provides a good balance of strength and ease of manufacturing, making it suitable for a variety of applications, from general machinery to automotive and industrial uses. The V-shaped form of UNF threads offers a decent amount of tensile strength and resistance to shear forces, but it’s not designed for the extreme loads and vibrations found in highly demanding fields.
UNJF Thread Form: UNJF threads also use a V-shaped thread form but with slightly modified angles and dimensions to handle higher loads and perform better under pressure. The modifications in the UNJF thread form help distribute forces more evenly across the thread, improving its shear strength and torque resistance. This makes UNJF threads more capable of handling stress in high-precision, high-performance applications, such as aerospace and defense industries, where failure is not an option.
The thread form of UNF and UNJF is closely related to their strength capabilities. The more finely tuned thread form of UNJF offers enhanced durability, making it a preferred choice for systems that must withstand extreme environmental and mechanical stresses.
Size Differences: UNF vs UNJF Thread Diameter
Another key difference between UNF and UNJF threads lies in their size and diameter.
UNF Thread Diameter: UNF threads come in a wide range of sizes, with diameters ranging from small precision fasteners to larger bolts and screws. UNF threads are commonly used in sizes ranging from 1/4 inch to 3 inches in diameter, offering flexibility for a variety of general industrial applications. The fine-pitch design of UNF allows for tight tolerances, making it suitable for high-strength, compact connections, especially where space is at a premium.
UNJF Thread Diameter: UNJF threads generally feature the same diameter range as UNF threads but with specific sizes designed to meet the needs of aerospace and specialized industries. While the diameters of UNF and UNJF may overlap, the UNJF threads are made with higher precision and stricter tolerances. They are specifically designed to ensure a more accurate and secure fit, even in extreme conditions. The diameter tolerance in UNJF threads is tighter, making them ideal for applications where failure is not an option, such as in aircraft components, satellites, and military systems.
Thread Geometry: The Science Behind the Shape
Thread Angle, Pitch, and Depth in UNF vs UNJF
Each aspect of thread geometry—angle, pitch, and depth—plays a significant role in determining how well the threads perform under load.
Thread Angle:
UNF Threads: The standard thread angle for UNF threads is 60 degrees, which is the same as the common V-shaped thread form. This angle strikes a balance between strength and ease of manufacture, making UNF threads suitable for general-purpose applications.
UNJF Threads: Although UNJF threads also use the 60-degree thread angle, their design includes finer tolerances and modifications to optimize the thread’s performance in critical environments like aerospace. The angle is optimized for better load distribution, which helps improve the fastener’s overall strength and resistance to failure, especially in high-stress environments.
Thread Pitch:
UNF Threads: The pitch (distance between threads) of UNF threads is fine but relatively standard when compared to other thread types. This provides a good balance of grip and thread strength, making it ideal for general mechanical and industrial uses. Fine-pitched threads also offer better resistance to vibration-induced loosening.
UNJF Threads: UNJF threads typically have a finer pitch than UNF threads, which improves thread engagement. A finer pitch allows for greater precision, better load distribution, and higher stress resistance. This is crucial in industries like aerospace, where even slight variations in thread engagement can compromise the entire system’s integrity.
Thread Depth:
UNF Threads: The depth of UNF threads is designed to balance strength and ease of installation. The thread depth is sufficient for most industrial applications, ensuring that the fastener has the required strength without being too deep to interfere with other components.
UNJF Threads: UNJF threads have a deeper thread depth that increases the overall surface area of the thread engagement. This deeper engagement ensures that the threads hold more securely under tension and shear forces. This makes UNJF threads ideal for applications where the fastener must withstand higher levels of stress, such as in aircraft engines or other critical systems.
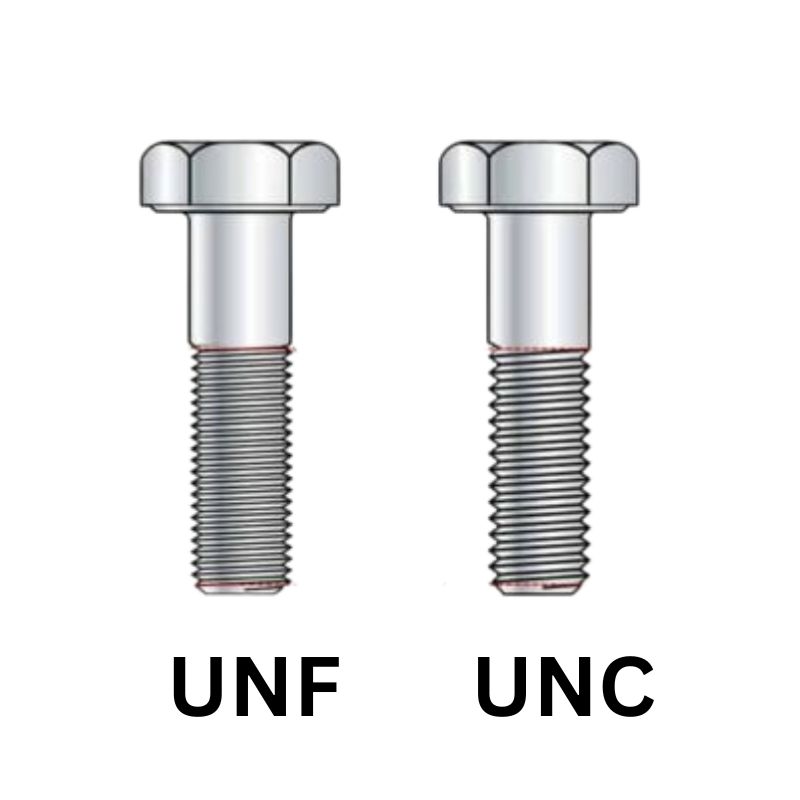
The Impact of Geometry on Durability and Strength
The geometry of UNF and UNJF threads has a direct impact on the durability and strength of the fastener. Thread geometry influences how well the threads distribute forces, resist wear, and interact with the mating part.
UNF Thread Durability: UNF threads are known for their resilience in general mechanical applications. The fine pitch and standard thread form allow UNF threads to provide excellent resistance to vibration and torsional forces. However, due to their standard tolerances and geometry, UNF threads are more suited for moderate load applications where extreme precision and load-bearing capacity are not as critical. In terms of durability, UNF threads hold up well under typical industrial conditions, though they may not perform as effectively in high-stress environments.
UNJF Thread Strength and Durability: UNJF threads are engineered with much more precise geometry, which plays a significant role in improving their strength and durability. The finer pitch, tighter tolerances, and deeper thread depth allow UNJF threads to handle higher levels of tension, shear, and vibration. These threads provide greater contact area between the fastener and the mating component, distributing loads more evenly. As a result, UNJF threads are more durable, offering superior resistance to wear and fatigue. They are highly resistant to stripping, thread fatigue, and other types of mechanical failure, which is why they are favored in high-performance industries such as aerospace and military applications.
Bolt Sizing and Screw Sizing: Choosing the Right Fit
Why Correct Sizing Is Essential for Fastener Performance
Correct sizing is crucial when selecting bolts and screws for any mechanical assembly, as it directly influences the performance, safety, and longevity of the fastener. Using improperly sized fasteners can lead to a range of issues, including loose connections, thread stripping, failure under stress, and vibration-induced loosening.
When the bolt or screw is too small, it may not provide sufficient clamping force or resist the mechanical loads applied to it. On the other hand, if the fastener is too large, it can put excessive stress on the surrounding material, potentially leading to thread damage or compromised structural integrity. Additionally, incorrect sizing can affect the tightening torque and may not provide the proper thread engagement, resulting in unstable connections.
For both UNF and UNJF threads, precise sizing ensures that the fastener fits perfectly with the corresponding hole or nut, optimizing the strength of the connection and improving the overall reliability of the assembly. This is especially important in industries like aerospace, automotive, and manufacturing, where fasteners must withstand extreme stresses.
How to Measure UNF and UNJF Bolts and Screws
Measuring bolts and screws correctly is essential for selecting the right size and ensuring compatibility with the mating threads. For both UNF and UNJF threads, the measurement process involves determining several key dimensions:
Thread Diameter:
The diameter of the bolt or screw is one of the most important measurements. It refers to the outermost diameter of the threaded portion of the fastener.
For UNF and UNJF fasteners, the diameter is typically measured using a micrometer or a caliper, ensuring the measurement is taken at the widest point of the threads. Common sizes range from 1/4 inch to 3 inches for UNF and UNJF fasteners.
Thread Pitch:
Pitch refers to the distance between adjacent threads and is measured in threads per inch (TPI) for UNF and UNJF threads. The thread pitch is essential for ensuring that the threads of the bolt or screw will properly engage with the corresponding nut or hole.
To measure pitch, use a thread pitch gauge or count the number of threads within a set length (typically 1 inch) to determine the TPI. This is especially important for UNF and UNJF threads, as the precise pitch is what differentiates these threads from other types like UNC (coarse threads).
Thread Length:
Thread length is the portion of the bolt or screw that has threads. It is important to measure the length of the threaded section to ensure that it properly engages with the nut or threaded hole.
For UNF and UNJF bolts and screws, ensure the threaded length matches the requirements for the application—whether it’s a shallow engagement for general use or a deeper engagement for high-performance applications.
Bolt Length (Overall):
In addition to the threaded portion, the overall length of the bolt or screw must be measured. This determines how deep the bolt or screw can be inserted into the corresponding part and is essential for applications where a specific insertion depth is required.
Shank Diameter (Non-threaded portion):
In some cases, the shank diameter (the non-threaded portion of the bolt) may also need to be measured, particularly if the fastener needs to pass through a hole in a component before the threads engage. For UNF and UNJF bolts, the shank diameter must match the clearance hole to ensure proper fit and alignment.
The Importance of Accurate Bolt Diameter and Pitch
Accurate measurement of bolt diameter and pitch is essential for ensuring proper fit and optimal performance.
Bolt Diameter: The diameter of the bolt or screw must match the corresponding hole size or nut, as even slight variations can cause improper thread engagement, leading to a weaker connection. An incorrectly sized diameter can cause the threads to be too tight or too loose, leading to poor torque control, stripped threads, or inconsistent clamping forces.
Thread Pitch: The thread pitch is especially critical for UNF and UNJF threads, as these fine-pitched threads are designed to interlock precisely with the mating threads. If the pitch does not match, the threads may not engage fully, resulting in incomplete fastening, vibration loosening, and weakened connections. The finer pitch of UNF and UNJF threads allows for better control over torque and more resistance to fatigue, but only when the pitch is measured and matched correctly.
Conclusion
Choosing the right thread type—UNF or UNJF—depends on your application’s requirements. Understanding the differences between these threads is crucial for ensuring the performance, safety, and longevity of mechanical systems. The right choice prevents costly failures, enhances efficiency, and ensures reliable, secure connections in both every day and high-precision applications.
FAQ
What is the difference between UNF and UNJF threads?
UNF threads are fine-pitched threads used for general mechanical applications, while UNJF threads are a specialized version with tighter tolerances and stronger performance for high-stress environments, such as aerospace.
Can I use UNF fasteners instead of UNJF?
It depends on your application. UNF fasteners are suitable for most industrial applications, but UNJF fasteners are designed for high-precision and high-stress environments. Always consider the performance demands before substituting one for the other.
What industries use UNF threads?
UNF threads are commonly used in industries like automotive, machinery, and general manufacturing where strength, precision, and vibration resistance are important.
Why are UNJF threads used in aerospace?
UNJF threads are used in aerospace because they offer superior strength, durability, and precision, making them ideal for handling high vibrations, pressure, and temperature changes found in aerospace applications.
How do I measure the pitch of UNF and UNJF threads?
You can measure the pitch of UNF and UNJF threads using a thread pitch gauge or by counting the number of threads in one inch of the fastener.
What happens if I use the wrong thread size?
Using the wrong thread size can lead to poor thread engagement, weakening the connection and potentially causing stripped threads, loose fasteners, or even system failure under stress. Proper sizing is essential for ensuring a secure and durable fit.