Hydraulic fittings (commonly referred to as hydraulic connectors) come in a variety of sealing forms. Each form has its specific structure and application scenarios. The sealing types of hydraulic fittings can mainly be divided into two categories: Flat Seals and Tapered Surface Seals, along with some other special sealing forms.
Flat Sealing Forms
Flat sealing relies on the use of various sealing elements that create a sealing face when compressed between the mating surfaces of hydraulic fittings. These sealing elements are typically made of materials such as rubber, metal, or composite materials, depending on the specific application and requirements. The primary goal of flat sealing is to prevent leakage by maintaining a tight, reliable seal under pressure. Below are the main types of flat sealing forms commonly used in hydraulic systems:
E-type Column End Seals
Features: The E-type column end fitting typically features an outer thread end that is machined with a ring groove. This groove is designed to accommodate a filler seal, such as an ED seal (Elastic Ductile seal), which is installed into the groove. The presence of this groove ensures that the sealing element stays in place and provides a tight seal when the fitting is tightened.
Materials: The ED seal used in this type is usually made of an elastomer, such as nitrile rubber, which provides flexibility and resilience, enhancing the seal’s ability to adapt to varying pressure conditions and preventing fluid leakage.
Application: E-type seals are ideal for situations where higher sealing performance is required, such as in high-pressure systems or those involving aggressive fluids that demand strong and durable seals. The combination of the groove and the ED seal ensures a high level of sealing integrity, preventing leaks even under demanding conditions.
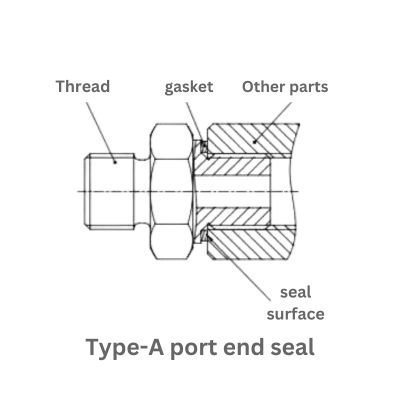
A-type Column End Seals
Features: The A-type column end fitting is designed with an outer thread end that incorporates a positioning cone surface. This conical surface serves as the primary sealing area and requires the installation of a copper washer or composite sealing washer to complete the seal. The washer’s function is to compress and create a reliable sealing interface when the fitting is tightened.
Materials: Copper washers or composite materials are commonly used in this type of seal. Copper washers offer excellent compressibility and resilience, making them suitable for high-temperature applications. Composite washers, which may combine metals with elastomers, provide enhanced flexibility and better performance in dynamic systems.
Application: A-type column end seals are typically used in systems where there is a need to prevent radial movement of the sealing washer, such as in cases where the fitting may be subjected to vibration or movement. The conical surface ensures that the washer stays in position, providing a stable and leak-free seal even in applications with significant mechanical forces.
Hinged Bolt Seals
Features: Hinged bolt seals use a unique assembly that involves hinged bolts and hinged joints. This design allows the connection to be sealed via the pressure exerted by the bolt connection, which compresses the sealing element, often an O-ring or gasket, between the two mating surfaces. The hinged design facilitates easy installation and disassembly.
Materials: The sealing element used in hinged bolt seals is typically an elastomeric O-ring, which provides excellent sealing under moderate pressures and temperatures. The O-ring is usually made from materials like nitrile or fluorocarbon rubber, depending on the compatibility with the hydraulic fluid and the operating environment.
Application: This type of seal is ideal for applications where space is limited, or where the system needs to be frequently disassembled for maintenance or replacement of components. The hinged design allows for easy access and quick removal of the fittings without requiring specialized tools or extensive labor, making it ideal for use in compact systems or machinery that undergoes frequent maintenance.
Flange Seals
Features: Flange seals are commonly used in hydraulic systems where the fitting is connected via a flange. These seals are typically achieved through a combination of flange connectors, split flanges, and O-rings or other sealing elements. The O-ring, placed in a groove on the mating flange surface, forms the primary sealing mechanism, while the flanged connection itself provides the necessary mechanical strength to withstand high pressures.
Materials: Flange seals often use O-rings made from elastomers such as nitrile, EPDM (ethylene propylene diene monomer), or Viton, depending on the fluid and temperature requirements. The flanges themselves are typically made from steel or other durable metals to ensure the fitting can handle the mechanical stresses of high-pressure systems.
Application: Flange seals are widely used in applications requiring high-pressure connections, such as in pumps, motors, hydraulic cylinders, and connections between high-pressure hoses and machinery. Their versatility and ability to create tight, secure seals make them ideal for heavy-duty industrial equipment that operates under high loads and pressures. Flange seals also provide easy disassembly and reassembly, making them suitable for systems that require periodic maintenance.
Tapered Surface Sealing Forms
Tapered surface sealing relies on the precise fit between a tapered surface and the sealing element to form an effective seal. In this form of sealing, the connection is achieved through the contact of conical or tapered surfaces, which tightly compress the sealing material. This type of sealing is ideal for situations where higher mechanical strength and reliable performance under pressure are required. Hydraulic pipe fittings with tapered surface sealing generally include the following types:
Flared Seals
Features: Flared seals have a fitting end that incorporates a flared structure, such as a 37° or 45° flare. The flare is designed to fit into a matching tapered surface, providing a tight seal through metal-to-metal contact. When the fitting is tightened, the flared end of the pipe is compressed against the mating surface of the fitting, ensuring that the seal is maintained by the tight, frictional fit.
Materials: Flared seals typically involve the use of copper or brass for the flared end, while the fitting may be made from stainless steel or other durable metals. The hardness of the metal allows for a secure and long-lasting seal under pressure.
Application: Flared seals are most commonly used for connections between copper pipes and thin-walled steel pipes. They are particularly suitable for high-pressure systems, such as those in hydraulic systems, automotive applications, and aerospace equipment. The robust nature of the flared connection makes it resistant to vibration and pressure changes, which is important in systems that endure constant movement or fluctuating pressure levels.
30° Tapered Seals
Features: The 30° tapered seal features an outer thread end that incorporates a groove designed to position the sealing element, often an O-ring. The inner thread end has a 30° tapered structure that ensures the fitting mates precisely with the O-ring to form a tight seal. When the fitting is tightened, the tapered surface pushes the O-ring against the inner side of the fitting, providing an excellent seal that prevents fluid leakage.
Materials: The O-ring used in these seals is usually made of elastomeric materials, such as nitrile, Viton, or EPDM, depending on the pressure and temperature requirements of the system. The 30° taper itself is typically made from high-strength metals, such as stainless steel or alloy steel, which are resistant to corrosion and wear.
Application: 30° tapered seals are commonly used in connections between valve bodies and fittings in hydraulic systems. They are also frequently found in system pressure measurement ports and other components that require precise, leak-free connections. This sealing form is ideal for situations where the sealing performance needs to withstand high pressures and the system must remain secure under extreme operational conditions.
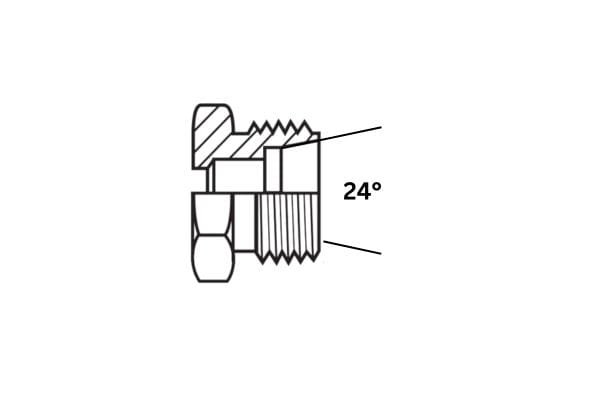
24° Tapered Seals (Composite Sealing)
Features: The 24° tapered seal is a composite sealing system that combines metal-to-metal hard sealing with the flexibility of an O-ring elastic seal. The metal-to-metal contact occurs on the tapered surfaces of the fitting, while the O-ring provides an additional layer of sealing by compressing against the metal surface. This dual approach ensures a high level of sealing reliability, as the metal-to-metal contact handles the bulk of the sealing, while the O-ring provides extra compression to prevent any leakage.
Materials: The 24° tapered seal typically uses a combination of durable metals for the fitting and an elastomeric O-ring made of materials like nitrile rubber, fluorocarbon, or silicone, depending on the fluid compatibility and temperature resistance needed.
Application: This sealing form is highly effective in environments that require a reliable seal under both high pressure and temperature fluctuations. It is often used in systems where both metal-to-metal sealing and elastic sealing are beneficial, such as in hydraulic and pneumatic systems, heavy machinery, or industrial equipment. The 24° taper allows for a stronger seal under higher working pressures, while the O-ring enhances the overall sealing performance, making this type of seal ideal for more demanding applications.
Other Special Sealing Forms
In addition to flat and tapered surface seals, hydraulic systems also use other specialized sealing forms, each designed to meet the specific requirements of different working environments. These special seals often offer unique advantages such as ease of installation, durability, or adaptability to certain system configurations. Below are some common types of special sealing forms, including Sleeve-type Seals and other variants, each with its distinct characteristics:
Sleeve-type Seals
Features: Sleeve-type seals consist of a sleeve (often a metal or composite material) that is placed over the fitting or pipe. This sleeve is then compressed to form a seal, typically in combination with an elastomeric sealing element, such as an O-ring or gasket. The sleeve helps distribute the compressive force evenly across the sealing surface, improving the integrity of the seal and reducing the risk of damage or wear.
Materials: The sleeve is typically made of durable metals such as stainless steel or aluminum, while the sealing element (such as an O-ring or gasket) is made from elastomers like nitrile, Viton, or EPDM, depending on the chemical and temperature conditions of the fluid being sealed.
Application: Sleeve-type seals are often used in applications where flexibility and easy installation are required, as well as in systems that need to be disassembled frequently for maintenance or inspection. They are commonly found in hydraulic cylinders, pumps, and high-pressure systems where there is a need to prevent leakage while also allowing for easy repair or replacement of seals.
V-Ring Seals
Features: The V-ring seal consists of a flexible elastomeric ring that is shaped like the letter “V.” When compressed, the V-shape creates a dynamic seal by pressing against the mating surface, providing an effective barrier against leakage. These seals are particularly useful in rotating shaft applications or where there is movement between the components.
Materials: V-rings are typically made from rubber compounds, including nitrile, silicone, or polyurethane, which offer good resistance to wear, abrasion, and chemical exposure.
Application: V-ring seals are commonly used in rotating machinery, such as pumps, motors, and compressors. Their ability to adapt to varying pressures and speeds makes them ideal for sealing in applications that involve movement or rotation, such as in the automotive, agricultural, and heavy machinery industries.
Cup Seals
Features: A cup seal is a type of hydraulic seal that resembles the shape of a “cup” or “sleeve.” When compressed, the cup shape allows the seal to expand and create a tight, reliable barrier against leaks. This design is particularly useful in dynamic sealing applications, where the seal must accommodate changes in pressure or movement.
Materials: Cup seals are typically made from elastomeric materials like rubber or polyurethane, which provide flexibility and durability. Some designs also include a metal insert to add strength and prevent excessive wear.
Application: Cup seals are often used in hydraulic cylinders and pistons, where they perform in both static and dynamic sealing environments. They are especially effective in systems where there is a need to withstand high-pressure differentials or where the seal must prevent both internal and external leakage.
O-Ring Seals with Backup Rings
Features: O-rings with backup rings combine a standard O-ring with an additional ring placed behind the O-ring to prevent it from extruding into the gap between the sealing surfaces when exposed to high pressure. The backup ring can be made of hard materials like PTFE (polytetrafluoroethylene) or other composite materials, which help distribute pressure more evenly.
Materials: The O-ring is usually made from rubber materials like nitrile or silicone, while the backup ring is typically made from PTFE, metal, or a combination of these materials.
Application: These seals are commonly used in high-pressure applications where standard O-rings might be prone to extrusion or damage. Backup rings are often found in critical hydraulic systems, high-temperature environments, and applications such as pistons, cylinders, and pumps.
Radial Seals
Features: Radial seals create a sealing barrier by exerting pressure radially against the surface they seal. These seals are typically used in rotary applications where there is relative motion between the sealing elements and the surface to be sealed. They are designed to withstand radial forces and ensure a tight, leak-free seal under varying pressures.
Materials: Radial seals are made from various elastomers, depending on the fluid being sealed and the operating conditions. Materials like nitrile, Viton, and polyurethane are common choices due to their ability to withstand pressure, temperature, and abrasion.
Application: Radial seals are commonly used in rotary shafts, gears, and pumps where the sealing element is exposed to dynamic motion. They are particularly useful in sealing applications involving rotating machinery, such as in the automotive, aerospace, and industrial sectors.
Spring-loaded Seals
Features: Spring-loaded seals use a metal spring to apply continuous pressure to the sealing element, ensuring consistent compression against the sealing surfaces. This type of seal is particularly effective in dynamic sealing applications where there is movement or vibration, as the spring helps maintain the seal even under changing conditions.
Materials: The sealing element is often made from elastomers, while the spring is typically made from stainless steel or other corrosion-resistant metals. The combination of the spring and the elastomer ensures both durability and flexibility.
Application: Spring-loaded seals are commonly used in applications where pressure fluctuations or vibration could cause seal failure, such as in pumps, valves, and rotary equipment. The spring ensures that the seal maintains contact with the mating surface, reducing the risk of leakage even in demanding conditions.
Conclusion
In summary, hydraulic pipe fittings have a wide variety of sealing forms, each with its unique features and application scenarios. When selecting and using hydraulic pipe fittings, it is essential to consider factors such as the specific working requirements, pressure levels, and medium characteristics to ensure the sealing performance and reliability of the fittings.
FAQ
What is a hydraulic fitting seal?
A hydraulic pipe fitting seal is a component used to prevent fluid leakage between two connected pipes or fittings. It ensures that the hydraulic system maintains pressure and operates efficiently.
What are the main types of hydraulic pipe fitting seals?
The main types are flat seals, tapered surface seals, and special sealing forms such as sleeve-type seals, V-ring seals, and cup seals. Each has unique features for different applications.
How does a flared seal work?
A flared seal uses a fitting end with a flared structure that creates a tight, metal-to-metal seal when the pipe is compressed against the fitting. This type is commonly used for high-pressure connections between copper and steel pipes.
When should I use a 30° tapered seal?
A 30° tapered seal is ideal for connections between valve bodies and fittings, or pressure measurement ports. It uses a tapered thread and an O-ring to ensure a leak-free connection under pressure.
What is a sleeve-type seal?
A sleeve-type seal is a specialized sealing component that consists of a sleeve over the fitting, often combined with an O-ring or gasket. It provides flexibility and is often used in systems that require frequent maintenance or easy disassembly.
What are backup rings, and when are they needed?
Backup rings are used in conjunction with O-rings to prevent extrusion under high pressure. They are necessary for high-pressure applications to maintain the integrity of the O-ring and ensure a reliable seal.