Hydraulic fittings are critical components in hydraulic systems, used to connect hoses, pipes, and other parts to create leak-proof connections. Understanding the key terminology related to these fittings is essential for selecting the right components and ensuring the system operates smoothly and efficiently. But how can you quickly grasp these basic concepts? This article serves as a simple guide to help you understand the fundamental terms of hydraulic fittings, clearing up any confusion and giving you the knowledge needed to make informed decisions in hydraulic system design and maintenance.
Fluid Transmission in Hydraulic Systems
Fluid transmission is the cornerstone of hydraulic system operation, enabling the transfer of power through the controlled movement of an incompressible fluid, typically oil. This principle allows for the generation of significant force and precise motion, making hydraulic systems indispensable in applications requiring heavy lifting or intricate control. The efficiency and reliability of fluid transmission are directly impacted by the quality and suitability of the components used, including adapters that connect various parts of the hydraulic circuit.
Fluid Transmission Definition
In the context of hydraulic systems, fluid transmission refers to the process of conveying hydraulic fluid between different components, such as pumps, cylinders, valves, and motors. This is achieved through a network of hoses, pipes, and tubes, interconnected by various fittings and adapters. The primary purpose of these connections is to ensure a leak-proof and pressure-tight seal, allowing the hydraulic fluid to transmit power effectively. The design and material of adapters are crucial in preventing fluid loss, contamination, and pressure drops, all of which can impair system performance and longevity. Different adapter types are selected based on factors like operating pressure, fluid compatibility, and the specific requirements of the connection point.
Pressure Concepts in Hydraulic Systems
Hydraulic systems operate under varying pressure levels, which are critical for their function. Understanding pressure concepts such as working pressure, maximum working pressure, and pressure tolerance is essential for selecting appropriate components, including adapters, to ensure both safety and optimal performance. Adapters must be able to withstand the system’s operating pressures without leaking or failing, as this could lead to system malfunction, damage, or safety hazards.
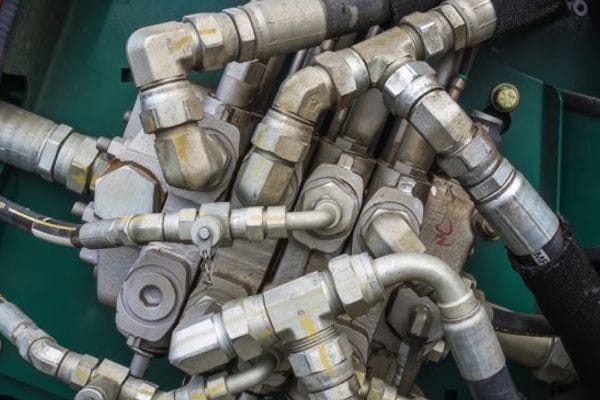
Working Pressure
Working pressure refers to the normal operational pressure range within a hydraulic system. Hydraulic adapters are designed to function reliably within this specified pressure range. When selecting an adapter, it’s crucial to match its rated working pressure with the system’s requirements. Exceeding the recommended working pressure can lead to premature wear, seal failure, or even catastrophic failure of the adapter, potentially causing system downtime and safety risks.
Maximum Working Pressure
Maximum working pressure is the highest pressure that a hydraulic component, such as an adapter, can sustain safely during operation. This value is typically higher than the normal working pressure to account for occasional pressure spikes or surges within the system. It is imperative that the maximum working pressure rating of an adapter is not exceeded. Doing so could compromise the structural integrity of the adapter, leading to leaks, bursts, or other forms of failure, which can have serious consequences for the equipment and personnel.
Pressure Tolerance
Pressure tolerance, often referred to as proof pressure in some contexts, indicates the adapter’s ability to withstand pressures significantly above its maximum working pressure for a short duration without permanent deformation or failure. This is a critical safety factor, ensuring that the adapter can handle unexpected pressure surges that might occur due to system malfunctions or external factors. For instance, an adapter might be rated to handle twice its maximum working pressure. This provides a safety margin, contributing to the overall robustness and reliability of the hydraulic system.
Pressure Safety Standards
Adherence to pressure safety standards is paramount in the design and operation of hydraulic systems. These standards dictate the minimum requirements for components to ensure they can operate safely under specified pressure conditions. For hydraulic adapters, this often involves considerations of burst pressure, which is a critical parameter in preventing catastrophic failures.
Minimum Burst Pressure
Minimum burst pressure is the lowest pressure point at which a hydraulic fitting or adapter is expected to rupture or fail. Industry standards, and often manufacturer specifications, typically require the minimum burst pressure to be a multiple of the maximum working pressure. For example, it’s common for the minimum burst pressure to be three or four times the maximum working pressure. This safety margin is crucial because it ensures that even under extreme, unforeseen pressure surges, the adapter is unlikely to fail catastrophically, thus protecting equipment and personnel.
Key Components of Hydraulic Fittings
Hydraulic fittings, often referred to as hydraulic adapters in many contexts, are crucial components that facilitate the connection of various parts within a hydraulic system. They ensure the integrity of the fluid path, preventing leaks and maintaining pressure. The design and material of these adapters are critical for the overall performance and safety of hydraulic machinery.
Hydraulic Fittings / Hydraulic Adapters
Hydraulic fittings, or adapters, serve as the connectors between different sections of hydraulic lines, such as hoses, pipes, and tubes, or between lines and components like pumps, cylinders, and valves. Their primary role is to create a secure, sealed connection that can withstand the operating pressures and temperatures of the hydraulic system. The selection of the appropriate fitting type depends on the specific application, including the type of fluid, pressure requirements, and the materials of the components being connected.
Fitting Body
The fitting body is the main structural part of the hydraulic adapter. It is typically manufactured from materials like carbon steel, stainless steel, or brass, chosen for their strength and compatibility with hydraulic fluids. The body houses the sealing mechanisms and provides the threaded or flanged surfaces for connection. Different configurations of fitting bodies exist, such as straight connectors, elbows, tees, and crosses, to accommodate various routing requirements and system layouts. The design of the fitting body, including its material and construction, directly impacts its pressure rating and durability.
Below is a table summarizing common hydraulic adapter types and their typical applications. This information is crucial for selecting the right adapter for a specific hydraulic system requirement, ensuring both efficiency and safety.
Adapter Type | Description | Typical Applications |
Straight Adapter | Connects two components in a straight line. | General purpose connections |
Elbow Adapter | Changes the direction of flow (e.g., 45°, 90°). | Tight spaces, routing around obstacles |
Tee Adapter | Splits flow into two directions or combines flow from two lines into one. | Branching lines, pressure gauge installation |
Cross Adapter | Splits flow into three directions or combines flow from three lines. | More complex branching |
Reducer/Expander | Connects components with different diameters. | Adapting sizes in a system |
Bulkhead Adapter | Passes through a panel or wall, providing a connection point on either side. | Panel mounting, through-wall connections |
Plug/Cap | Seals off unused ports or lines. | System maintenance, preventing contamination |
Swivel Adapter | Allows for rotation to prevent hose kinking or twisting. | Applications with moving parts, hose management |
Types of Thread Connections
The integrity of a hydraulic system heavily relies on the quality of its connections. Thread connections are a common method for joining hydraulic components, and understanding the different types of threads is essential for ensuring a secure and leak-free system. The choice of thread type often depends on the pressure requirements, the type of fluid being conveyed, and the specific standards followed in a given industry or region.
External Thread at End of Fitting
Many hydraulic adapters feature an external thread at one or both ends, designed to mate with a corresponding internal thread on another component, such as a port or another fitting. The precision of these threads is critical for achieving a proper seal and preventing leaks, especially under high pressure. Different thread standards exist, each with its own specifications for thread angle, pitch, and diameter.
Below is a table outlining common hydraulic thread types and the standards they adhere to. This information is vital for selecting compatible adapters and ensuring the safety and efficiency of the hydraulic system.
Thread Type | Standard | Sealing Method | Common Applications |
NPT/NPTF (National Pipe Taper Fuel) | ANSI B1.20.1 | Tapered threads, sealant often used. | General industrial, fluid power (NPTF for higher pressure) |
BSPP (British Standard Pipe Parallel) | ISO 228 | Parallel threads, sealing with bonded washer or O-ring. | UK, Europe, Asia, Australia – low to medium pressure |
BSPT (British Standard Pipe Taper) | ISO 7 | Tapered threads, sealant often used. | UK, Europe, Asia, Australia – low to medium pressure |
JIC (Joint Industry Council) 37° Flare | SAE J514 / ISO 8434-2 | Metal-to-metal seal on 37° flared cone. | High-pressure hydraulics, especially in North America |
SAE Straight Thread O-ring Boss (ORB) | SAE J1926 / ISO 11926 | O-ring seal. | High-pressure hydraulics, good vibration resistance |
Metric Parallel | ISO 6149 | O-ring seal. | Hydraulic systems, often with metric tubing |
Metric Taper | DIN 3852 | Tapered threads, often with sealant. | Hydraulic systems, less common than parallel |
SAE Flange (Code 61 & 62) | SAE J518 | O-ring seal between flange faces. | High-pressure, high-flow applications, split flange design |
It is important to consult manufacturer specifications and consider the specific operating conditions, including the type of hydraulic fluid, temperature range, and potential exposure to corrosive elements, when selecting the material for hydraulic adapters. Using an incompatible material can lead to premature failure, leaks, and potential safety hazards.
Installation Considerations
Proper installation of hydraulic adapters is paramount to ensure the safety, efficiency, and longevity of any hydraulic system. Even the highest quality adapter can fail if not installed correctly, leading to leaks, pressure loss, component damage, or even catastrophic system failure.
Installation Torque
Installation torque refers to the precise amount of rotational force that must be applied when tightening a threaded hydraulic adapter. Applying the correct torque is critical. Insufficient torque can result in loose connections, leading to leaks or even detachment under pressure. Conversely, excessive torque can damage the threads, crush seals, or even crack the adapter body or the component it’s being connected to.
Manufacturers typically provide recommended torque specifications for their hydraulic adapters. These specifications are based on the adapter’s material, size, and thread type. It is essential to use a calibrated torque wrench and adhere strictly to these recommendations during installation. Factors such as the presence of lubrication can also affect the actual clamping force achieved at a given torque, so manufacturer guidelines should always be the primary reference.
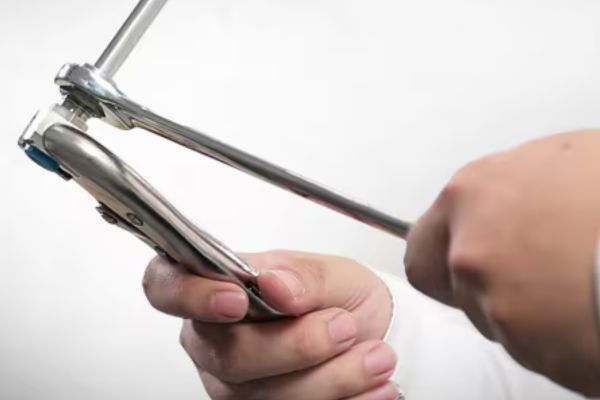
Adjustable Column End
Some hydraulic adapters, particularly those used in complex configurations or where precise orientation is necessary, feature an adjustable column end. This design allows the main body of the adapter to be rotated relative to its threaded base after the base has been tightened. This is particularly useful for elbow fittings, tee fittings, or cross fittings where the outlet ports need to be aligned in specific directions after the threaded connection to the main hydraulic line or component is secured.
The adjustable column end typically involves a locking nut or a similar mechanism that, once the adapter is oriented correctly, can be tightened to fix the adapter’s position and ensure a pressure-tight seal. This adjustability simplifies the assembly of complex hydraulic circuits and helps prevent undue stress on hoses or pipes that might arise from misaligned fixed fittings.
Fixed Column End
In contrast to adjustable column ends, fixed column end adapters have a predetermined orientation once tightened. These are common in simpler, straight connections where the directionality of the flow is not a complex factor. While lacking the flexibility of adjustable ends, fixed adapters are often more straightforward to install in direct line connections and can be more robust in certain applications due to fewer moving parts or adjustment mechanisms.
The choice between an adjustable or fixed column end adapter will depend on the specific requirements of the hydraulic system design, the space available for installation, and the need for precise angular positioning of the connected line
Hose Fittings and Their Characteristics
Hydraulic hoses are fundamental for conveying fluid under high pressure in hydraulic systems, offering flexibility that rigid pipes or tubes cannot. Hose fittings are the critical components that connect these hoses to other parts of the system, such as pumps, cylinders, or other hoses. The integrity of these fittings is paramount for system safety and efficiency, as any failure can lead to significant fluid loss, pressure drops, and potential hazards.
Hose Fitting Definition and Importance
A hydraulic hose fitting is a connector specifically designed to attach to the end of a hydraulic hose, creating a secure and leak-proof seal. Their importance cannot be overstated, as they are the primary interface between the flexible hose and the rigid components of a hydraulic circuit. A properly selected and installed hose fitting ensures several critical functions:
- Containment of High-Pressure Fluids: Hydraulic systems often operate at thousands of PSI. Hose fittings must reliably contain these pressures to prevent dangerous blowouts or leaks.
- Maintaining System Integrity: A secure connection prevents the ingress of contaminants (dirt, moisture) into the hydraulic system, which can damage sensitive components and reduce system lifespan.
- Ensuring Efficient Power Transmission: Leaks at fittings lead to a loss of hydraulic fluid and pressure, reducing the efficiency of power transmission and potentially causing system malfunctions.
- Facilitating Assembly and Maintenance: Hose fittings allow for the modular assembly of hydraulic systems and simplify the replacement of hoses during maintenance.
These fittings are typically made from materials like carbon steel, stainless steel, or brass, chosen for their strength, corrosion resistance, and compatibility with various hydraulic fluids. The design of a hose fitting must ensure that it can grip the hose securely without damaging its structural layers (e.g., reinforcement braids or spirals), while also providing a reliable connection point to the rest of the hydraulic system.
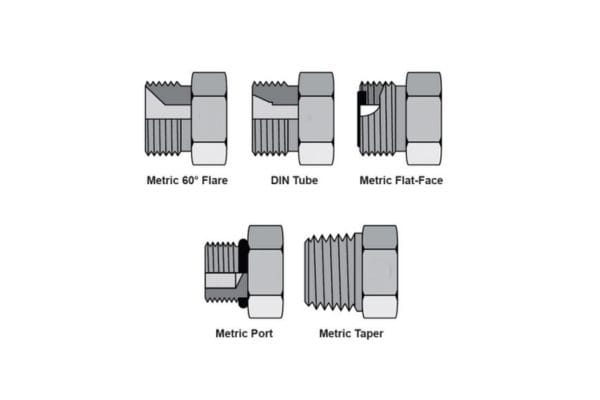
Components of a Typical Hose Fitting
While designs vary, many hydraulic hose fittings share common structural components that contribute to their sealing and holding capabilities. Understanding these components is key to appreciating how they function:
Internal Conical Sealing Face
Many hydraulic hose fittings, particularly those that form metal-to-metal seals, utilize an internal conical sealing face. This is a precisely machined, angled surface within the fitting (often on the male half or a corresponding seat in the female half). When the fitting is connected and tightened to a mating component that has a compatible conical seat, these two surfaces are forced together, creating a metal-to-metal seal. This type of seal is highly effective at preventing leaks, especially under high-pressure conditions. The angle of the cone (e.g., 24°, 37° as in JIC fittings) and the surface finish are critical for the integrity of this seal. This type of seal can often be reconnected multiple times, though care must be taken to avoid damaging the sealing surfaces.
Ball-Sealed Hose Fitting Core
Another sealing mechanism found in some hydraulic hose fittings involves a ball-sealed core. In this configuration, a spherical ball, typically made of hardened steel or a durable polymer, is designed to rest against a precisely machined seat within the fitting’s core. When pressure is applied in one direction, or when the fitting is disconnected (in the case of quick couplings), the ball is forced against its seat, blocking any potential leak paths. This type of sealing is common in quick-disconnect couplings where rapid and repeated connections and disconnections are required. The precision of both the ball and its seat is crucial for the effectiveness of the seal, especially under dynamic pressure conditions.
Nut or Body That Holds the Entire Fitting Together
The structural integrity and the compressive force required for sealing in a hose fitting assembly are typically provided by a nut or the main body of the fitting.
- Nut: In many reusable or field-attachable fittings, and in the connection of the fitting to another component, a threaded nut is employed. This nut, when tightened, draws the mating parts of the fitting together, or compresses the hose end onto the fitting stem/nipple. The threads on the nut must be robust enough to handle the tightening torque and the operational stresses.
- Body/Socket/Ferrule: For crimp-on fittings, the main body (often called a socket or ferrule) is a sleeve that is placed over the hose end and the fitting stem. This ferrule is then radially compressed (crimped) using a specialized machine. The crimping process deforms the ferrule, forcing it to grip the hose tightly against the barbed or profiled stem inserted into the hose. This creates a permanent, high-strength connection and seal. The design of the ferrule and stem, along with the crimping parameters, are critical for a reliable hose assembly.
Materials Used in Hydraulic Adapters
The choice of material for hydraulic adapters is critical, as it directly impacts their strength, durability, corrosion resistance, and compatibility with different hydraulic fluids and operating environments. Different applications may necessitate different materials to ensure optimal performance and longevity of the hydraulic system.
Below is a table summarizing common materials used in the manufacture of hydraulic adapters, along with their key properties and typical applications. This information can help in selecting the most appropriate adapter material for a given hydraulic system’s operational requirements.
Material Properties and Considerations for Hydraulic Adapters
Material | Properties | Common Applications | Considerations |
Carbon Steel | Good strength, relatively low cost. Often plated for corrosion resistance. | General hydraulic systems. | Susceptible to corrosion if plating is damaged. Not suitable for corrosive fluids. |
Stainless Steel | Excellent corrosion resistance, high strength, good temperature resistance. | Marine environments, chemical processing, food industry. | Higher cost than carbon steel. |
Brass | Good corrosion resistance, easy to machine. | Low-pressure applications, fuel lines, air brakes. | Lower strength than steel, not suitable for high pressures. |
Aluminum | Lightweight, good corrosion resistance. | Aerospace, mobile hydraulic systems where weight is a factor. | Lower strength and wear resistance compared to steel. |
Titanium | High strength-to-weight ratio, excellent corrosion resistance. | Aerospace, high-performance applications. | Very high cost, difficult to machine. |
It is important to consult manufacturer specifications and consider the specific operating conditions, including the type of hydraulic fluid, temperature range, and potential exposure to corrosive elements, when selecting the material for hydraulic adapters. Using an incompatible material can lead to premature failure, leaks, and potential safety hazards.
Conclusion
In conclusion, understanding the core terminology of hydraulic fittings is crucial for anyone working with hydraulic systems. Whether you’re selecting components for a new project or maintaining existing equipment, knowledge of key terms like working pressure, burst pressure, and hose fittings will ensure you make informed decisions for optimal performance and safety. We hope this guide has provided clarity on the essential aspects of hydraulic fittings. If you have any questions or need assistance in selecting the right components for your system, feel free to reach out to us. We’re here to help with your inquiries and provide the best solutions for your needs.
FAQ
What is the difference between working pressure and maximum working pressure in hydraulic systems?
Working pressure is the typical operational pressure, while maximum working pressure is the highest pressure a component can safely handle.
Why is minimum burst pressure important when choosing hydraulic fittings?
Minimum burst pressure ensures that fittings can withstand extreme pressure conditions without failure, providing safety in high-pressure applications.
What is the purpose of adjustable column ends in hydraulic fittings?
Adjustable column ends allow the fitting to be oriented before tightening, offering flexibility in connecting fittings in complex systems.
How does installation torque affect hydraulic fitting performance?
Correct installation torque ensures fittings are securely connected, preventing leaks or damage to threads and seals.
Can you explain the role of the fitting body in a hydraulic system?
The fitting body is the main connecting piece that joins hydraulic components, and it plays a crucial role in ensuring a leak-proof connection.
What are the main components of a hose fitting?
Hose fittings typically consist of an internal conical sealing face, ball-sealed hose fitting core, and a nut or body that holds the assembly together.