Choosing the wrong hydraulic hose can bring your entire job site to a standstill. A sudden failure isn’t just about a messy spill; it’s about crippling downtime, expensive repairs, and serious safety risks for your team.
Hydraulic hoses are the essential lifelines of all heavy construction machinery. They are responsible for transmitting immense power to actuators, managing precise control for steering and braking, and handling low-pressure fluid return. Understanding each specific application is the only way to select the right hose and prevent catastrophic failure.
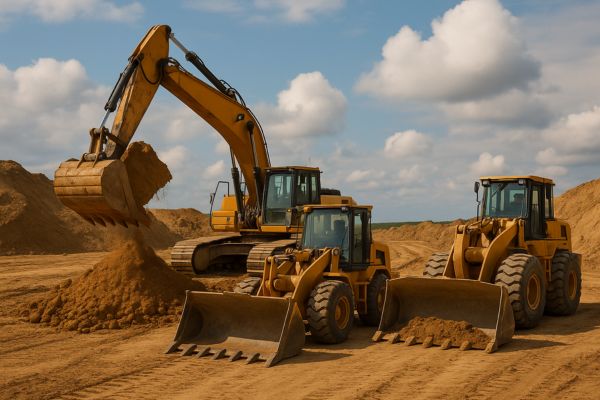
It is one thing to look at a spec sheet and match a pressure rating. It’s another thing entirely to understand why a certain hose is used for a certain job in the harsh reality of a construction site. The stresses on a hose running a bucket cylinder are worlds apart from those on a steering line or a low-pressure return line. Getting this detail right is the fundamental difference between a machine that runs reliably for thousands of hours and one that is constantly down for frustrating repairs.
Why Is Matching the Hose to the Machine So Critical?
Thinking “a hose is just a hose” is one of the most expensive mistakes you can make. Using a generic, all-purpose hose for a specialized task is a gamble that almost always ends in premature failure, leaks, and lost productivity.
It’s absolutely critical because each function—whether it’s lifting, steering, or simply returning fluid—imposes a unique combination of demands on the hose. These demands relate to pressure, temperature, flexibility, and durability. A mismatch between the hose and its task is the number one reason I see for unexpected equipment breakdowns in the field.
Over my years in this business, I’ve seen countless customers focus only on the pressure rating. But that’s just one piece of a much larger puzzle. A hose that can handle 5000 PSI might be far too stiff for a steering application, causing it to fail from fatigue after just a few weeks of constant bending. Another hose with the right pressure and flexibility might get destroyed in days if its outer cover can’t handle the abrasive dust and rocks on your site.
Beyond Pressure Ratings: The Trifecta of Performance
When we consult with a new client, we always encourage them to think beyond a single number on a spec sheet. True performance comes from a balance of three factors.
Understanding Pressure: Static vs. Dynamic
Many people see a pressure rating and think of it as a simple limit. But in hydraulics, there are two types of pressure. Static pressure is a constant, steady load. **Dynamic pressure**, or impulse, involves rapid spikes and drops. A hydraulic hammer or the sudden stop of a heavy excavator boom creates massive impulses. A spiral-wire hose (like an SAE 100R13 or R15) is designed to absorb these shocks, while a braided hose (like a 100R2) might fail under the same conditions, even if its static pressure rating seems adequate.
The Temperature Factor: Internal and External
Temperature is another two-sided problem. You have the internal temperature of the hydraulic oil itself, which can get very hot during continuous operation. But you also have the external, ambient temperature. A hose routed near a hot engine or exhaust system is being “cooked” from the outside. A standard hose will become brittle and crack. You must select a hose with a cover and inner tube rated for the highest temperature it will encounter, both inside and out.
Bend Radius: The Flexibility Myth
A common myth is that a thicker, higher-pressure hose is always “better.” But if that hose is used in an application that requires tight bends, its stiffness becomes a weakness. Every hose has a minimum bend radius. Forcing it into a tighter bend puts immense stress on the wire reinforcement, leading to rapid fatigue failure. For steering lines or other articulating parts, choosing a more flexible hose (like an SAE 100R16) with a tighter bend radius is far more important than just getting the highest pressure rating.
How Do Excavators Use Different Hoses for Power and Precision?
Your excavator arm suddenly goes limp, and the entire operation grinds to a halt. A single burst hose on a primary function can cost your project thousands of dollars for every hour of downtime.
Excavators use a highly specialized variety of hoses for different functions. Extremely robust four- or six-wire spiral hoses (4SH/6SH) are required for the boom, arm, and bucket. More flexible two-wire hoses manage the swing motor and tracks, while simple one-wire hoses safely handle low-pressure return lines.
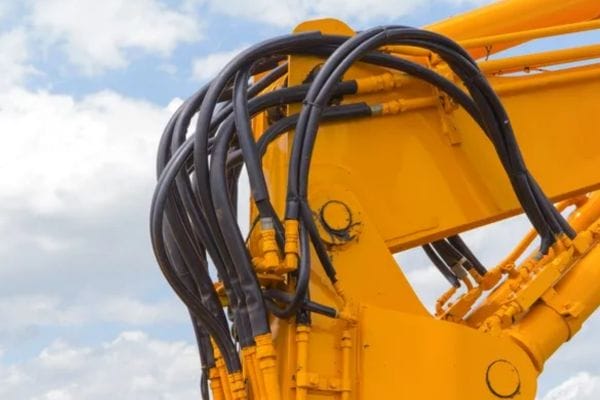
The hydraulic system on an excavator is a masterclass in managing immense power. The pressure spikes generated when an operator abruptly stops a heavy, fully loaded bucket can be incredible. A standard two-wire braided hose simply cannot survive those repeated impulses for long.
The Agile Mover: Swing and Travel Motor Hoses
The hoses that power the excavator’s swing motor and track drive system also handle high pressures, but they have an added requirement: flexibility. These hoses often need to be routed through tight spaces in the machine’s carbody. Here, a more flexible two-wire braided hose like an SAE 100R2 or a compact 100R16 is often the better choice. They provide the necessary pressure containment while being easier to install and more resistant to fatigue from machine vibration.
The Nervous System: Pilot Lines and Low-Pressure Circuits
It’s not all about high pressure. The joystick controls in the cab send low-pressure signals through small-diameter pilot hoses to the main control valves. A failure in one of these “control” lines can be just as debilitating as a main hose burst—the machine simply won’t respond. Reliability, not pressure, is the key here.
Suction and Return Lines
Finally, you have the large-diameter suction hoses (SAE 100R4) that bring oil from the tank to the pump, and the return lines that bring it back. The key requirement for a suction hose is collapse resistance, to prevent the pump from being starved of oil, a condition known as cavitation which can destroy a pump in minutes.
What Makes Hoses on Wheel Loaders Unique?
Your wheel loader’s steering suddenly becomes stiff or completely unresponsive. The machine is now a multi-ton roadblock, creating a massive safety hazard and bringing all work to a complete stop.
The constant, complex flexing at the central articulation joint is what makes wheel loader hoses unique. Critical steering systems require hoses with an excellent bend radius and exceptionally high fatigue resistance. For these applications, flexibility and long-term reliability are far more important than just having the highest possible pressure rating.
The Articulation Joint: A Point of Constant Stress
Think about how a wheel loader moves. It steers by pivoting in the middle. The hoses that cross this joint are constantly being bent, twisted, and stretched in multiple directions. A standard, stiff high-pressure hose isn’t designed for this kind of dynamic flexing.
Selecting for Fatigue Resistance
This is where the concept of “fatigue cycles” comes in. A hose designed for high flexibility can endure hundreds of thousands more bend cycles before its wire reinforcement starts to break down. I remember a fleet owner in the USA who faced this exact challenge. We switched him from a standard SAE 100R2 hose to a 100R16 type. The R16 offers a similar pressure rating but has a significantly tighter bend radius and is built for higher fatigue resistance. The change completely solved his recurrent failures because the hose was designed to *flex*, not just to hold pressure.
Powering the Load & Lift Cylinders
The hoses for the main lift and tilt cylinders on a loader are a different story. These are high-pressure applications, much like an excavator’s boom. However, they don’t experience the same constant, tight-radius flexing as the steering lines. For these, a robust two-wire or four-wire hose is often the perfect balance of pressure capacity and durability.
Why Are Bulldozer Hoses Built for Maximum Durability?
Bulldozers operate in a constant storm of dirt, rock, and extreme heat. A hose without an exceptionally tough outer cover can be physically destroyed by abrasion in a matter of days, not weeks.
Bulldozer hoses are all about survival. They must withstand relentless external abrasion from debris and intense radiant heat from the engine. For this reason, hoses with special “tough covers” or MSHA-rated abrasion-resistant jackets are absolutely essential for blade control and powerful ripper functions.
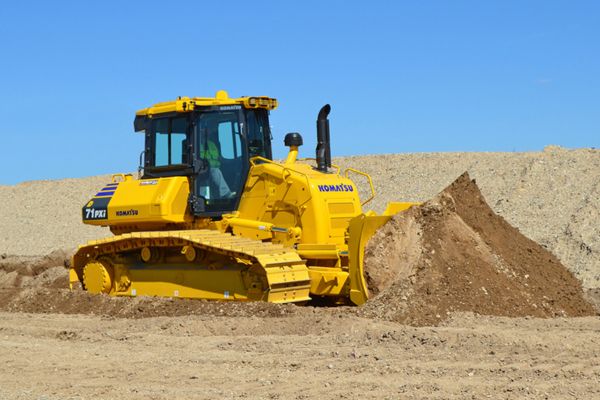
Nowhere is the operating environment more brutal than on a bulldozer. The hoses are continuously exposed to high pressure, high heat, and extreme external abrasion.
The Abrasive Environment: A Hose’s Worst Enemy
We had a client in a Ghanaian mining operation who was replacing blade lift hoses every single month. The hoses weren’t bursting from internal pressure. The outer covers were literally being ground away by constant contact with rock and sand, exposing the steel wire reinforcement to rust and physical damage. We supplied them with our Topa-brand hoses that feature a high-abrasion resistant cover. This single change extended the service life of the hoses by more than six times. It’s a perfect case study showing that sometimes, the outside of the hose is just as critical as the inside.
What is a “Tough Cover”?
A standard hose cover is made from neoprene or a synthetic rubber blend. A “tough cover” uses a different, much more durable polymer, often a special type of polyethylene. It is specifically engineered to resist being scraped, cut, and worn away.
Handling Shock Loads: The Ripper Function
The ripper at the back of a bulldozer is used to break up hard-packed earth or soft rock. When the ripper tooth snags on something solid, it sends a massive shockwave back through the hydraulic system. This is an even more extreme version of the impulse loading seen on an excavator. It is a job for the most robust spiral hoses, like the SAE 100R15, which are specifically designed to absorb these incredible, instantaneous shocks.
How Do Cranes Rely on Hoses for Safety and Reach?
Imagine a hydraulic line on a mobile crane’s outrigger begins to leak and then fails. The machine loses stability in a critical moment, putting the operator, the multi-million dollar load, and everyone on the ground in immediate and grave danger.
Cranes depend on hydraulic hoses for absolutely safety-critical functions like deploying their stabilizing outriggers and telescoping the boom. These applications demand the highest possible level of reliability, often using hoses with superior pressure ratings and robust construction to prevent any chance of catastrophic failure under heavy load.
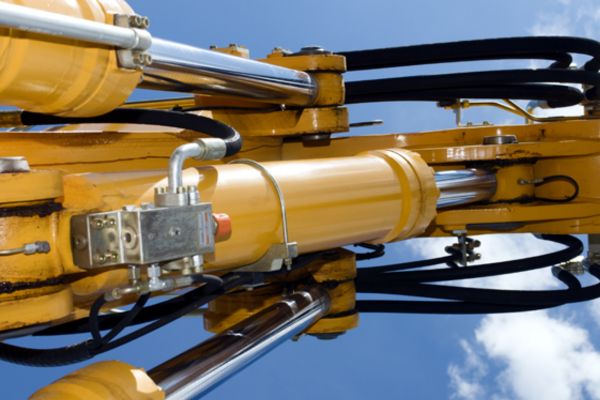
When we supply hoses for cranes, the conversation always centers on safety and reliability. A failed hose on an excavator bucket is a problem; a failed hose on a crane’s outrigger is a potential disaster.
Stability and Safety: The Outrigger System
The outriggers are the crane’s foundation. The hoses that power these cylinders must be flawless. They handle high pressures and must hold that pressure without even the slightest drop. There is zero room for error. We work with clients in Romania and Qatar who operate large crane fleets, and my advice is always the same: inspect these hoses daily. Look for any signs of rubbing, kinking, fluid weeping from the fittings, or external damage.
Reaching for the Sky: Telescoping Boom Hoses
The hoses that run inside a telescoping boom present a unique challenge. They need to extend and retract smoothly over and over again without getting pinched, kinked, or abraded by internal boom components. These are often routed in special hose carriers or reels. Using a hose with a durable, low-friction cover is essential to ensure a long, trouble-free service life.
What is the Role of Hoses in Auxiliary Attachments?
You’ve just invested in a new hydraulic hammer for your skid steer, but the hoses you connected to it failed within the first week of use. The expensive attachment is now useless until you get the right hydraulic lines.
Auxiliary hoses are what give a base machine its incredible versatility. These lines must be carefully selected to handle the specific demands of the tool, whether it’s the high-frequency pressure spikes of a hammer, the continuous high flow needed for a brush cutter, or the clamping force of a grapple.
This is an area where we get a lot of questions, especially from our customers in the US and Australia who use a wide variety of attachments on skid steers and mini-excavators.
The Challenge of Versatility
The problem is that a “one-size-fits-all” auxiliary hydraulic circuit doesn’t really exist. The demands vary wildly.
High-Frequency Impulse: The Hydraulic Hammer
A hydraulic breaker, or hammer, is probably the most destructive attachment for a hydraulic hose. It creates an incredibly rapid series of intense pressure spikes. A standard braided hose will be shaken apart from the inside out in very short order. This application absolutely requires a multi-spiral hose to absorb the relentless impulses.
Constant Flow Applications: Mowers and Grinders
In contrast, an attachment like a mower, flail, or grinder doesn’t create high-pressure spikes. Instead, it requires a high volume of oil flow (measured in GPM or LPM) at a relatively steady pressure. For these reasons, the key is ensuring the hose has a large enough internal diameter to handle the flow without creating excessive heat and backpressure. A standard two-wire hose is often perfect for this.
Beyond the Bore: Why the Outer Cover is Your First Line of Defense
Your hoses are failing, but they aren’t bursting from pressure. Instead, the outer layer is cracked, peeling, or completely worn through, exposing the delicate wire reinforcement to the elements.
Yes, the cover is absolutely critical. It is the hose’s primary shield against abrasion, heat, ozone from sunlight, and chemical exposure. Choosing the wrong cover material can lead to the failure of a perfectly good hose just as quickly as choosing the wrong pressure rating.
I’ve seen so many cases of good hoses failing simply because their cover was not suited for the local environment.
Fighting the Elements: Ozone and UV Resistance
A standard black rubber cover can be surprisingly vulnerable. When exposed to direct, intense sunlight day after day, the UV radiation and ozone in the air can cause the rubber to break down, becoming hard and brittle. I remember a client in Mauritius who operates equipment right next to the ocean. He found his hose covers were getting sticky and degrading very quickly. We identified the cause as a combination of intense UV light and corrosive salt spray. Switching to a hose with a more resistant synthetic cover material completely solved his problem.
MSHA Certification: A Guarantee of Safety
For customers in mining or tunneling, the hose cover has a critical safety function. MSHA (Mine Safety and Health Administration) certified covers are fire-resistant. They are designed to not propagate a flame in the event of a fire, a vital safety feature in confined spaces. When we supply to our mining clients, we always ensure they are aware of and are using MSHA-rated hoses for all underground applications. It’s a standard we are proud to meet.
Conclusion
Selecting the right hydraulic hose is a science. It requires deep knowledge of the machine, its specific function, and its working environment. We help our customers get it right every time.