You look at a simple steel hydraulic fitting and it seems basic. It is tempting to think all fittings are the same, but a low-quality one can cause leaks, downtime, and dangerous failures.
A truly reliable hydraulic fitting is defined by three silent factors: the specific grade of steel it’s made from, the quality and thickness of its protective coating, and the microscopic precision of its threads and sealing surfaces. Getting these right is what separates a good fitting from a bad one.
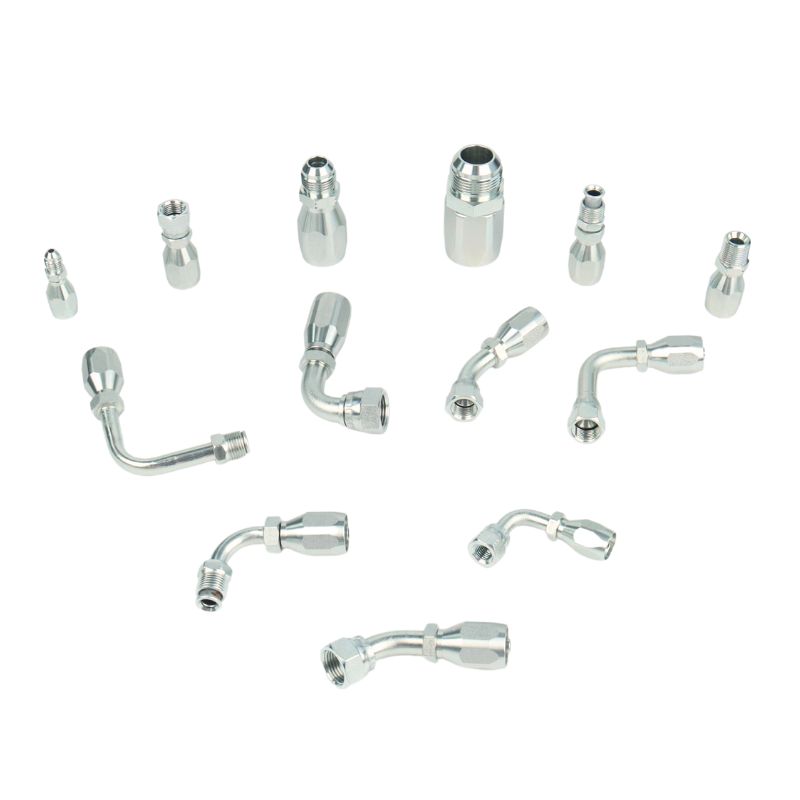
What Material Are Your Hydraulic Fittings Made From, and Why Does It Matter?
A fitting fails under pressure, and you think it was just a faulty part. The real culprit is often the cheap, weak metal it was made from, a hidden flaw from the very beginning.
We manufacture our standard hydraulic fittings from #45 carbon steel. This material provides the high tensile strength needed to withstand extreme pressure and vibration. For corrosive environments, we use stainless steel grades like 304 or 316 to ensure long life and operational safety.
The foundation of any quality fitting is the raw material. You cannot build a strong house on a weak foundation, and you cannot make a reliable fitting from inferior steel. The choice of material directly impacts the fitting’s pressure rating, its resistance to fatigue, and its overall durability. This isn’t just a technical detail; it is the most fundamental aspect of the component’s safety.
Why Carbon Steel is the Industry Standard
The vast majority of hydraulic systems operate in environments where strength is more important than corrosion resistance. Carbon steel is the perfect choice for this. Specifically, we use #45 steel (equivalent to grades like 1045 or S45C). This is a medium carbon steel known for its excellent combination of high tensile strength, wear resistance, and good machinability. It can be forged into complex shapes like elbows and tees without losing its structural integrity. This strength ensures that when a fitting is properly installed, it can easily handle the rated working pressure of the system, including the intense pressure spikes that occur during normal operation.
When Stainless Steel is Necessary
For some of my customers, especially those in the marine, chemical, or food processing industries, corrosion is a bigger enemy than pressure. In these situations, we use stainless steel.
- Grade 304 Stainless Steel: This is a great general-purpose choice, offering excellent corrosion resistance in most environments.
- Grade 316 Stainless Steel: This grade contains molybdenum, which gives it superior resistance to chlorides (like salt water) and other harsh chemicals. It is the preferred material for marine applications and extreme chemical processing.
Material Feature | #45 Carbon Steel | 316 Stainless Steel |
Primary Benefit | High Strength & Wear Resistance | Extreme Corrosion Resistance |
Cost | More Economical | Premium Price |
Appearance | Zinc-Plated (Silver or Gold) | Natural Bright Silver Finish |
Best For | Construction, Agriculture, Industry | Marine, Chemical, Food & Beverage |
How Does the Coating on a Fitting Protect It From Failure?
Your new fittings look great, but after a few months in the field they are covered in rust. This not only looks bad but signals that the fitting is weakening and heading toward failure.
We protect our carbon steel fittings with a robust, trivalent zinc plating. This coating acts as a sacrificial barrier, corroding first to protect the steel underneath. This process, verified by salt spray testing, prevents rust and dramatically extends the fitting’s lifespan in real-world conditions.
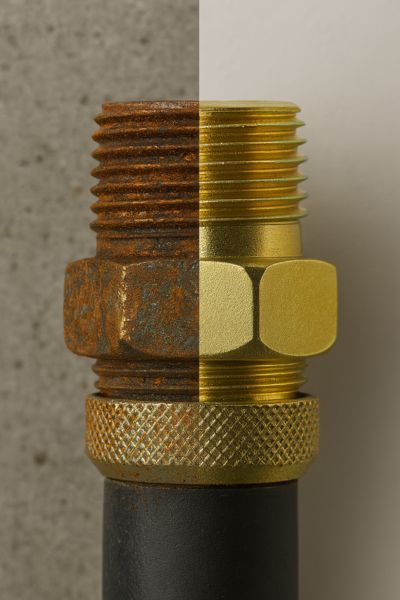
The shiny silver or yellowish-gold finish on a fitting is not for decoration. It is a critical layer of technical protection. I always tell my B2B clients in places with high humidity, like the Philippines or Ghana, that the quality of the plating is just as important as the strength of the steel. A fitting that rusts is a fitting that is dying. The rust can contaminate the hydraulic system and, more importantly, it means the steel is losing its structural integrity.
The Science of Sacrificial Protection
Zinc is a less noble metal than steel. This means that when the two metals are in contact in the presence of an electrolyte (like moisture in the air), the zinc will corrode preferentially. It sacrifices itself to protect the steel from rusting. A thick, high-quality plating provides a longer period of this protection. We use a trivalent chromium passivation process over the zinc. This is the modern, environmentally safer standard (free of dangerous Hexavalent Chromium) that adds another layer of protection and gives the fitting its final color.
Our Quality Guarantee: Salt Spray Testing
How can you be sure the coating is good? We prove it with standardized testing. We place our fittings in a sealed chamber and spray them with a continuous, dense salt fog. This accelerates the corrosion process. A quality fitting must be able to withstand this harsh environment for a specific number of hours without showing signs of red rust. Our standard fittings are rated for a minimum of 72 hours, with higher-performance options available, ensuring they will survive and perform in the field for years.
Why Are Precisely Machined Threads the Key to a Leak-Proof Seal?
You tighten a fitting as much as you can, but a small, annoying leak persists. Overtightening just damages the threads, making the problem worse and costing you a new fitting.
The leak is not about tightness; it is about precision. Our fittings are made on modern CNC machines to guarantee the threads and sealing surfaces meet strict international standards (like JIC, BSPP, DIN, etc.). This precision creates a perfect mating between parts, ensuring a leak-free connection with normal tightening force.
The threads on a fitting have two jobs: they provide the mechanical clamping force to hold the connection together, and they guide the two halves of the fitting into a position where a seal can be made. If these threads are imperfect—if their angle, pitch, or diameter is even slightly off—they will fail at both jobs.
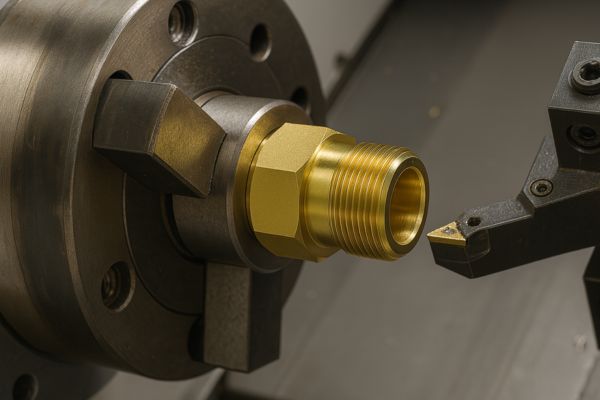
Different Threads for Different Jobs
The world of hydraulics uses several major thread types, and each one seals in a slightly different way. We manufacture all of them to exact specifications.
- JIC (37° Flare): This is very common in North America. The seal is made on a metal-to-metal cone surface. The threads provide the clamping force.
- BSPP (British Standard Pipe Parallel): Common in Europe and Asia. The threads are parallel and do not seal. The seal is made by a bonded washer or an O-ring on the face of the fitting.
- NPT (National Pipe Taper): A tapered thread where the threads themselves deform and create the seal. This type requires a sealant tape or paste.
The Importance of Tiny Details
Beyond the thread itself, other features are critical. The small, beveled edge at the start of a thread is called a chamfer. A good chamfer prevents cross-threading during installation and protects O-rings from being cut. Likewise, the surface finish on a sealing cone must be extremely smooth. Any tiny scratch from the machining process can become a leak path. Our quality control process includes checking these fine details to ensure every fitting is perfect.
Thread Type | Sealing Method | Primary Region of Use |
JIC | Metal-to-metal on a 37-degree cone | North America |
BSPP | Bonded seal or O-ring on a flat face | UK, Europe, Asia, Global |
NPT | Threads themselves deform (tapered) | North America |
DIN | Metal-to-metal on a 24-degree cone with O-ring | Europe |
Is a Forged Fitting Body Stronger Than One Machined From Bar Stock?
You are comparing two fittings that look the same, but one is forged and one is not. The manufacturing method is a hidden quality factor you need to understand.
Yes, for complex shapes like elbows and tees, a hot-forged body is significantly stronger. The forging process aligns the steel’s internal grain structure with the shape of the part, giving it superior resistance to vibration, pressure spikes, and fatigue compared to a part machined from solid bar stock.
This is a technical point, but an important one that I explain to customers from an engineering background. How a fitting begins its life—either as a solid block of steel or a red-hot forged blank—determines its ultimate strength.
The Power of Aligned Grain Flow
Think of the grain in a piece of wood. A wooden beam is strongest when the load is applied along the grain. If you cut across the grain, you create a weak point. The same is true for steel.
- Machining from Bar Stock: When you machine an elbow from a solid block, you are cutting across the steel’s natural grain structure. This is perfectly fine for simple, straight fittings.
- Hot Forging: In this process, we heat a piece of steel until it is red-hot and then press it into a die in the shape of the fitting. This forces the internal grain of the steel to flow and align with the fitting’s shape. This continuous, unbroken grain structure makes the final part much stronger and more resistant to cracking under stress. For all of our elbow, tee, and cross fittings, we insist on using forged bodies for maximum reliability.
Why is Final Inspection and Packaging So Important?
You receive a box of fittings, but they are loose, uncovered, and banging against each other. Some are already damaged before you even use them.
A great fitting can be ruined by poor handling. Our final inspection and packaging process ensures every fitting is perfect when you receive it. We use thread protectors and organize fittings in strong boxes to prevent any damage to critical threads and sealing surfaces during shipping.
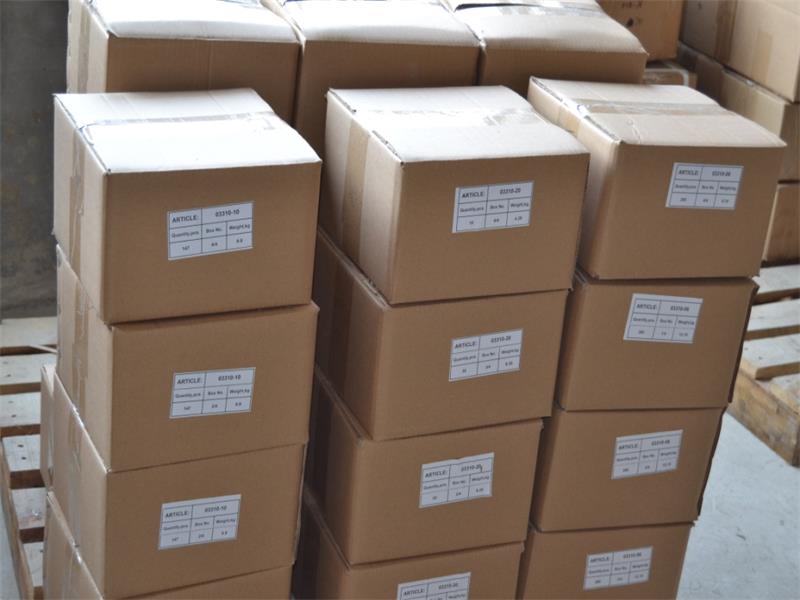
Our commitment to quality does not stop when the machine finishes cutting the part. I know from experience that shipping problems are a major frustration for my customers. A fitting that is damaged in transit is useless. That is why our final steps are so critical.
The Final Quality Check
Before any fitting is packaged, it undergoes a final visual and dimensional check. We use “Go/No-Go” thread gauges to instantly verify thread accuracy. We visually inspect every sealing surface for scratches or imperfections. Only perfect parts are allowed to move on to packaging.
Protection Until Installation
Every single one of our fittings with male threads or sensitive sealing surfaces is capped with a plastic protector. This is a simple but vital step. It prevents the fine threads from being dented and keeps the sealing cones clean and free from scratches. We then arrange the parts neatly in reinforced cartons to ensure they arrive at our customers’ facilities—whether in Romania or Zimbabwe—in the same perfect condition they left our factory. This attention to detail prevents problems and shows respect for the customer and the product.
How Do You Ensure Consistency Across a Large Order?
You need to order thousands of fittings. How can you be sure that the last fitting in the box is the exact same quality as the first?
Consistency comes from a documented, repeatable manufacturing and quality control process. By using calibrated CNC machines, strict raw material standards, and multiple quality checkpoints, we guarantee that every fitting in every batch meets the exact same high standard of precision and reliability.
This is the ultimate concern for any professional buyer. A single good sample is easy to provide, but consistent quality across thousands of units is what defines a truly reliable supplier. Our reputation is built on this consistency.
Process Control, Not Just Product Inspection
We achieve consistency by controlling the entire process. It starts with sourcing our #45 steel only from certified mills. Our CNC machines are programmed with the exact dimensions for each fitting and are regularly calibrated to maintain accuracy. We do not just inspect the final product; we inspect parts at multiple stages throughout the manufacturing process.
Traceability and Accountability
Every batch of fittings we produce is linked to a production run and a specific batch of raw materials. This allows for full traceability. If a customer ever has an issue, we can trace the part back and review the entire production history. This system creates accountability and drives our commitment to continuous improvement. It is this systematic approach that gives our customers, from small workshops to large construction companies, the confidence to trust our products in their most critical applications.
Conclusion
A fitting’s reliability is born from its material, protected by its coating, and guaranteed by the precision of its machining. Partnering with a supplier who masters these details is essential. If you have hydraulic couplings needs or need customized hydraulic fittings, contact Topa. We can quickly provide you with products as well as services!