By allowing hoses to rotate and align correctly, live swivel fittings play a critical role in preventing wear and tear. This not only extends the life of the hoses but also ensures that the hydraulic system operates more efficiently and safely. The use of hydraulic live swivel fittings can significantly reduce maintenance costs and downtime by minimizing the factors that contribute to hose wear, making them an essential component in modern hydraulic systems.
Understanding Hose Wear in Hydraulic Systems
A. Causes of Hose Wear
Abrasion
Abrasion occurs when hydraulic hoses rub against other surfaces, such as machinery parts, walls, or other hoses. This friction wears down the outer cover of the hose, exposing the reinforcement layers, which can lead to leaks and hose failure.
External abrasion is often caused by improper routing, where hoses are not secured properly or are placed too close to moving parts.
Fatigue
Hydraulic hoses are frequently subjected to bending, flexing, and twisting, especially in applications where there is constant movement. Over time, this repeated stress can cause the hose material to weaken, leading to cracks, splits, or kinks.
Fatigue is particularly common in hoses that are installed in areas with limited space, where they are forced to bend sharply or twist continuously.
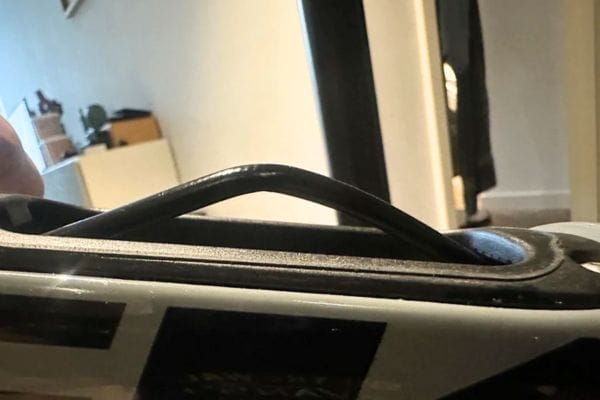
Pressure Surges
Hydraulic systems often experience pressure surges or spikes, which can place extreme stress on hoses. These sudden changes in pressure can cause the hose to expand and contract rapidly, leading to internal damage, such as blistering or bursting.
Hoses that are not rated for the maximum system pressure or that have deteriorated over time are particularly susceptible to damage from pressure surges.
Misalignment
Misalignment occurs when hoses are not routed correctly, causing them to be pulled or stretched in unnatural directions. This can lead to increased stress on the hose, resulting in wear and premature failure.
Misaligned hoses are often found in systems where the layout has not been optimized, leading to unnecessary strain on the hose and its connections.
B. Consequences of Hose Wear
Decreased System Efficiency
Worn hoses can restrict fluid flow, leading to reduced system efficiency. This can result in slower operation, increased energy consumption, and lower overall productivity.
Leaks caused by hose wear can also reduce the amount of fluid available in the system, further decreasing its efficiency and effectiveness.
Increased Maintenance Costs
Hose wear leads to more frequent maintenance, as hoses need to be inspected, repaired, or replaced to prevent failure. This increases the cost of maintenance, both in terms of materials and labor.
Unplanned maintenance due to hose failure can also result in significant downtime, adding to the overall cost.
Risk of System Failure and Downtime
Severe hose wear can lead to catastrophic failure, such as a burst hose or a major leak, which can cause the entire hydraulic system to shut down. This results in costly downtime, lost productivity, and potential safety hazards.
System failure due to hose wear can also damage other components, leading to more extensive repairs and longer downtime.
What Are Live Swivel Fittings?
Definition and Functionality
Live swivel fittings are specialized components designed to connect hoses and tubes in hydraulic systems, allowing them to rotate freely while under pressure. This rotation capability is crucial for accommodating the natural movement and alignment of hoses during operation.
These fittings consist of a rotating joint within the fitting body, which enables the hose or tube to turn without twisting, kinking, or causing stress at the connection point. This reduces wear on the hose and helps maintain the integrity of the hydraulic system.
Live swivel fittings are engineered to handle high-pressure environments, ensuring that they perform reliably even in demanding applications. The rotating joint is typically sealed to prevent leaks, making it a durable and effective solution for reducing hose wear.
Comparison with Standard Fittings
Unlike live swivel fittings, standard hydraulic fittings are rigid and do not allow for rotation or movement once installed. This lack of flexibility can lead to problems such as hose twisting, kinking, or misalignment, which contribute to accelerated wear and potential failure.
Standard fittings may suffice in static applications where there is little to no movement, but in dynamic systems where hoses are subjected to constant motion, live swivel fittings offer significant advantages.
The key difference lies in the ability of live swivel fittings to adjust to the movement and pressure changes within the system, thereby minimizing stress on the hoses and extending their service life.

Advantages of Using Live Swivel Fittings
Reduction of Abrasion
Live swivel fittings allow hoses to rotate freely, preventing them from rubbing against other components or surfaces. This rotation minimizes external abrasion, which is one of the leading causes of hose degradation. By reducing wear from friction, swivel fittings help maintain the hose’s integrity over a longer period.
Prevention of Fatigue
In hydraulic systems, hoses often undergo repeated bending and twisting, leading to material fatigue over time. Swivel fittings mitigate this by allowing hoses to move naturally with the system’s operation, preventing the sharp bends and twists that cause fatigue cracks and eventual hose failure.
Protection Against Pressure Surges
Hoses in hydraulic systems are subject to fluctuating pressures, which can cause them to expand and contract repeatedly. Live swivel fittings help absorb these pressure surges, distributing the stress more evenly across the hose and preventing localized wear that could lead to failure.
Correct Alignment
Proper hose alignment is critical for reducing stress and wear. Swivel fittings ensure that hoses remain aligned even as they move, reducing the risk of kinking or unnatural bends that can shorten hose life. This proper alignment helps maintain the hose’s optimal condition, leading to a longer service life.
How Live Swivel Fittings Prevent Hose Wear
A. Reducing Abrasion
Live swivel fittings are designed to enable hoses to rotate freely without becoming twisted or kinked. This free rotation minimizes the friction that occurs when hoses rub against surfaces, machinery parts, or even other hoses.
By reducing the amount of direct contact and friction, swivel fittings protect the outer layer of the hose from being worn down, which is a common cause of hose failure.
B. Preventing Fatigue and Kinking
Live swivel fittings allow hoses to rotate and adjust to movement without bending sharply or twisting. This flexibility reduces the stress on the hose material that typically results from repeated bending and twisting during operation.
By preventing these repetitive stresses, swivel fittings help maintain the structural integrity of the hose, reducing the likelihood of fatigue-related damage such as cracking or splitting.
Benefits of Reducing Hose Fatigue and the Risk of Kinking
Extended Hose Lifespan:
By minimizing fatigue and preventing kinking, swivel fittings can extend the life of hydraulic hoses, leading to fewer replacements and lower overall costs.
Improved System Performance:
Hoses that are free from kinks and fatigue-related issues maintain consistent fluid flow, which is crucial for the efficient operation of hydraulic systems.
Enhanced Safety:
Reducing the risk of hose kinking also minimizes the chances of sudden hose failure, which could lead to dangerous situations in high-pressure systems.

C. Managing Pressure Surges
Pressure surges in hydraulic systems can cause hoses to expand and contract rapidly, leading to wear and potential failure. Live swivel fittings help manage these surges by allowing the hose to move and adjust to the pressure changes without being subjected to excessive strain.
The rotational movement provided by the fittings ensures that the hose can distribute the pressure evenly, reducing the risk of localized damage that can occur during sudden pressure spikes.
Technical Details on Pressure Distribution and Absorption
Pressure Distribution:
Swivel fittings enable hoses to align more naturally with the flow of hydraulic fluid, which helps in distributing pressure evenly throughout the hose. This even distribution prevents weak spots from forming, which are often the starting points for wear and failure.
Pressure Absorption:
The rotating mechanism of the swivel fitting acts as a buffer during pressure surges, absorbing some of the force and reducing the direct impact on the hose. This absorption capability is particularly beneficial in high-pressure applications where surges are frequent.
D. Addressing Misalignment Issues
Role of Live Swivel Fittings in Maintaining Proper Hose Alignment
Misalignment is a common cause of hose wear, as it leads to unnatural bending and stretching of the hose. Live swivel fittings address this issue by allowing the hose to rotate and align itself properly during operation.
This self-alignment capability ensures that the hose remains in a natural position, free from the excessive stress that misalignment can cause.
Impact on Reducing Stress and Extending Hose Life
Stress Reduction:
By maintaining proper alignment, swivel fittings reduce the overall stress on the hose, preventing wear and prolonging its life. This stress reduction is particularly important in systems with complex hose routing, where misalignment is more likely to occur.
Hose Longevity:
Properly aligned hoses are less likely to develop weak points or suffer from premature wear. As a result, the use of swivel fittings can lead to a significant extension of hose life, reducing the frequency of replacements and associated costs.
Choosing the Right Live Swivel Fittings
A. Factors to Consider
Pressure Rating:
Ensure that the live swivel fitting you choose is rated for the maximum pressure of your hydraulic system. Using a fitting with an inadequate pressure rating can lead to failures, leaks, and safety hazards.
It’s essential to match the pressure rating of the fitting with that of the hoses and other system components to maintain overall system integrity.
Compatibility with Existing Hoses and Systems:
The selected swivel fitting must be compatible with the hoses, connectors, and other components already in use within the hydraulic system. This includes considering the hose size, thread type, and connection style to ensure a secure fit.
Compatibility also involves ensuring that the swivel fitting can handle the specific fluid used in the system, whether it’s hydraulic oil, water, or another medium.
Material Considerations for Different Environments
Corrosive Environments:
In environments where the fitting will be exposed to corrosive substances or conditions (e.g., saltwater, chemicals), selecting a swivel fitting made from corrosion-resistant materials like stainless steel or brass is crucial.
Corrosion-resistant fittings help prevent material degradation, leaks, and potential system failures, especially in marine or chemical processing industries.
High-Temperature Environments:
For applications where the hydraulic system operates at elevated temperatures, it’s vital to choose swivel fittings that can withstand these conditions without losing their mechanical properties.
Materials such as high-temperature alloys or thermoplastics may be necessary to ensure the fitting performs reliably under extreme heat.
Other Environmental Factors:
Consider the fitting’s exposure to factors like UV radiation, extreme cold, or abrasive materials, and choose materials that can endure these conditions without deteriorating.
B. Common Mistakes to Avoid
Selecting the Wrong Type of Swivel Fitting
Improper Angle Selection:
Choosing a swivel fitting with the wrong angle (e.g., selecting a 90-degree fitting when a 45-degree fitting is needed) can lead to improper hose routing, increased stress on the hose, and eventual wear or failure.
It’s important to assess the system’s layout and movement to determine the most appropriate fitting type, whether it’s inline, 45-degree, or 90-degree.
Incompatible Size or Thread Type:
Selecting a fitting with the incorrect size or thread type can lead to poor connections, leaks, and increased wear on both the fitting and hose.
Always verify the size and thread compatibility with existing components to ensure a secure and leak-free connection.
Ignoring Manufacturer Specifications and Recommendations
Overlooking Pressure and Temperature Ratings:
Manufacturers provide specific pressure and temperature ratings for their swivel fittings, and ignoring these can lead to catastrophic failures. It’s essential to adhere to these specifications to ensure the fitting can handle the system’s demands.
Disregarding Installation Guidelines:
Proper installation is critical to the performance of live swivel fittings. Ignoring manufacturer recommendations for installation, such as torque settings or alignment instructions, can result in suboptimal performance, leaks, or fitting failure.
Neglecting Maintenance Recommendations:
Regular maintenance, as recommended by the manufacturer, is necessary to keep swivel fittings functioning optimally. Skipping maintenance checks can lead to undetected wear and tear, reducing the fitting’s lifespan and the overall system reliability.
Conclusion
If you’re experiencing frequent hose wear, unexpected system failures, or costly maintenance in your hydraulic systems, it’s time to consider the benefits of live swivel fittings. By choosing the right fittings for your specific needs, you can protect your hoses, extend their lifespan, and ensure that your hydraulic systems run smoothly and efficiently. Don’t wait until hose wear becomes a critical issue—take proactive steps now by integrating live swivel fittings into your system and reap the long-term benefits of reduced maintenance costs, enhanced performance, and greater reliability.
FAQ
What are live swivel fittings?
Live swivel fittings are hydraulic components that allow hoses or tubes to rotate freely while under pressure, reducing wear and preventing kinks.
How do live swivel fittings prevent hose wear?
They allow the hose to rotate naturally, minimizing friction, preventing fatigue from repeated bending, and maintaining proper alignment.
What types of live swivel fittings are available?
Common types include 45-degree, 90-degree, and inline swivel fittings, each designed for specific routing needs in hydraulic systems.
Why are live swivel fittings better than standard fittings?
Unlike standard fittings, live swivel fittings enable movement and rotation, reducing stress on the hose and extending its lifespan.
Can live swivel fittings be used in high-pressure applications?
Yes, live swivel fittings are designed to handle high-pressure environments, making them suitable for demanding hydraulic systems.
What materials are live swivel fittings made from?
They are typically made from materials like stainless steel, brass, or high-temperature alloys, depending on the application and environmental conditions.