The importance of check valves lies in their ability to maintain system integrity by preventing reverse flow, which can cause equipment failure, contamination, or process disruption. In industries where fluid dynamics are critical, such as oil and gas, chemical processing, and HVAC systems, check valves protect pumps, pipelines, and other equipment from damage caused by backflow. Additionally, they ensure that systems operate at optimal efficiency by regulating flow direction, contributing to overall operational safety and cost-effectiveness.
How Check Valves Work
Basic Operation Mechanism
Check valves are automatic valves designed to permit fluid flow in one direction and prevent reverse flow in a system. The basic working principle involves a mechanism that opens the valve when there is forward flow and closes it when the flow reverses. In normal operation, when fluid moves in the intended direction, pressure pushes the valve’s disc (or other closing mechanism) away from the seat, allowing the fluid to pass. If the flow reverses, the backpressure causes the disc to return to its seated position, sealing off the passage and preventing backflow.
This one-way operation is critical in ensuring the protection of sensitive equipment like pumps, compressors, and pipelines from damage due to reverse flow. It also helps maintain the efficiency and safety of the system by preventing contamination, fluid loss, and pressure surges.
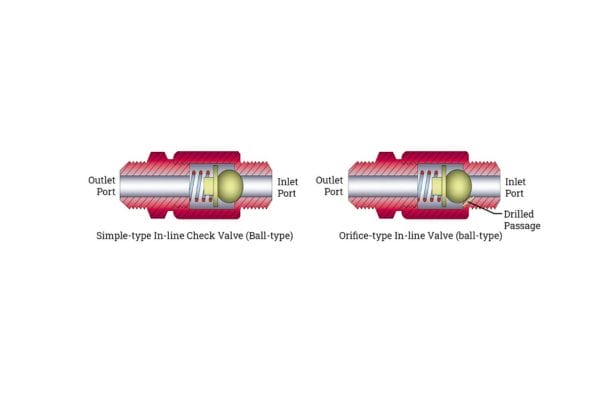
Components of a Check Valve
Check valves are simple devices with several key components that work together to regulate fluid flow:
Body: The outer casing of the valve, is typically made from materials such as stainless steel, brass, or plastic, depending on the application and fluid type.
Disc: The movable part that controls the flow. In different types of check valves, this may be a ball, diaphragm, or plate, depending on the design.
Seat: The part of the valve where the disc rests when closed. It ensures a tight seal to prevent backflow.
Hinge or Spring Mechanisms: Depending on the valve type, either a hinge (as in a swing check valve) or a spring (as in a spring-loaded check valve) helps control the movement of the disc. Springs are used to assist the closure of the valve, especially in vertical installations, while hinges work in gravity-based designs.
Inlet and Outlet Ports: The two ends of the valve through which fluid enters and exits, respectively. These ports are connected to the pipeline, ensuring the check valve fits into the system seamlessly.
Why Choosing the Right Type Matters
Selecting the appropriate type of check valve is crucial to ensure efficient and reliable operation. Different types of check valves are designed for specific applications, flow characteristics, and system conditions. Using the wrong check valve can lead to several problems:
Inefficiency: A check valve that doesn’t match the system’s pressure or flow requirements can create excessive pressure drops, reducing the overall efficiency of the system. For example, a valve that requires too much pressure to open might restrict fluid flow, leading to wasted energy.
Equipment Failure: If a check valve fails to close properly or operates too slowly, it can cause reverse flow, potentially damaging pumps, compressors, or other equipment. Water hammer, a high-pressure surge caused by sudden valve closure, can also occur if the wrong type of check valve is used.
Leakage: If the valve components such as the seat or disc are not designed to handle the system’s fluid properties, leaks can occur. This can result in contamination, loss of fluid, or even system failure, particularly in sensitive industries like chemical processing or food production.
Thus, choosing the right check valve for the specific fluid type, system pressure, and flow rate is essential to ensure system safety, efficiency, and long-term reliability.
Top Types of Check Valves
Swing Check Valve
Design and Function
A swing check valve operates using a hinged disc (or flapper) that swings open to allow flow in the forward direction and closes when the flow reverses, preventing backflow. The valve’s design allows fluid to pass through with minimal resistance, and when the flow decreases or reverses, gravity or backpressure pushes the disc back into its seat, sealing the valve and stopping reverse flow. The swinging mechanism makes it ideal for horizontal installations.
Advantages
Low-pressure drop: The swing check valve allows fluid to pass with minimal resistance, reducing pressure loss in the system.
Ideal for low-velocity flows: The design is well-suited for systems where the flow rates are low and consistent, such as in water distribution systems.
Limitations
Not suitable for pulsating flows: The valve may wear out faster in systems with rapid flow changes, leading to improper sealing.
Potential for water hammer: In high-velocity systems, the valve’s rapid closure can cause water hammer, leading to pressure surges that can damage equipment.
Common Applications
Water and wastewater systems: The low-pressure design of swing check valves makes them ideal for water distribution and wastewater systems.
HVAC systems: They are commonly used in heating, ventilation, and air conditioning systems to regulate fluid flow and prevent backflow.
Oil and gas pipelines: In these industries, swing check valves help maintain the efficiency and safety of the pipeline systems by preventing backflow in low-velocity applications.
Ball Check Valve
Design and Function
A ball check valve uses a spherical ball that moves within the valve body to block reverse flow. When fluid flows forward, the pressure lifts the ball off the seat, allowing the fluid to pass. When the flow reverses, the ball is forced back into the seat, creating a tight seal that prevents backflow. The simplicity of its design ensures that the valve works effectively in a range of fluid types, especially those containing particulates or debris.
Advantages
Simple design, low maintenance: The lack of complicated moving parts makes ball check valves easy to maintain and ideal for systems that need reliability.
Effective in systems with contaminated media: The ball’s ability to handle particulate matter makes this valve ideal for slurry or viscous fluids, where debris could hinder other types of valves.
Limitations
May cause higher pressure drops: Due to the design, ball check valves may result in slightly higher pressure drops compared to other types of check valves.
Not suitable for low-pressure systems: In low-pressure applications, the ball may not seat properly, leading to leakage or inefficient operation.
Common Applications
Pump discharge applications: Ball check valves are commonly used at the outlet of pumps to prevent reverse flow and maintain system integrity.
Slurry and viscous fluid systems: In industries such as mining or wastewater treatment, where fluids may contain particulates, ball check valves excel.
Food processing industries: Their ability to handle fluids with varying viscosity makes ball check valves a good choice for food and beverage applications.

Lift Check Valve
Design and Function
In a lift check valve, the disc or piston moves vertically within the valve body to allow forward flow and closes when the flow reverses. As forward flow pressure increases, it lifts the disc off the seat, allowing fluid to move through. When the flow decreases or reverses, gravity or backpressure causes the disc to fall back into place, sealing the valve and stopping reverse flow. Lift check valves are well-suited for horizontal and vertical installations, provided there is sufficient pressure.
Advantages
Suitable for high-pressure applications: Lift check valves are robust enough to handle high-pressure systems, making them ideal for heavy-duty industrial processes.
Effective in horizontal and vertical piping: The design allows the valve to work in both horizontal and vertical orientations, providing flexibility in system design.
Limitations
Not ideal for dirty or slurry media: The tight clearance between the disc and the seat can become blocked or damaged by particulate matter, leading to valve failure.
Requires proper alignment for optimal functioning: Proper installation is critical to ensure that the disc lifts and seats correctly.
Common Applications
Steam and gas systems: Lift check valves are often used in steam and high-pressure gas systems due to their ability to withstand high temperatures and pressures.
High-pressure water applications: They are commonly used in high-pressure water pipelines where forward and reverse flow needs to be carefully controlled.
Chemical and petrochemical industries: The valve’s ability to withstand high pressures makes it suitable for use in chemical and petrochemical processing plants.
Diaphragm Check Valve
Design and Function
A diaphragm check valve uses a flexible rubber or elastomer diaphragm that flexes open under forward flow pressure and closes when the flow reverses. The diaphragm acts as both the disc and the seal, creating a smooth, tight closure that prevents backflow. These valves are commonly used in systems where maintaining sanitary conditions or avoiding contamination is critical.
Advantages
Suitable for sanitary applications: Diaphragm check valves are designed to meet hygiene standards, making them ideal for food, beverage, and pharmaceutical industries.
Prevents contamination, ideal for sensitive media: The diaphragm design ensures a tight seal, preventing contaminants from entering the system and protecting sensitive fluids.
Limitations
Limited use in high-pressure environments: Diaphragm check valves are not suitable for very high-pressure systems, as the diaphragm may fail under intense pressure.
Susceptible to wear from abrasive fluids: Abrasive media can damage the diaphragm, leading to leaks and reduced valve efficiency over time.
Common Applications
Pharmaceutical and food processing: Diaphragm check valves are widely used in these industries due to their ability to maintain sanitary conditions and avoid contamination.
Medical equipment: Their ability to handle sensitive media makes them suitable for use in medical devices that require precise fluid control.
Chemical dosing systems: Diaphragm check valves are commonly used in low-pressure chemical dosing systems where contamination must be avoided.
Wafer Check Valve
Design and Function
Wafer check valves are compact, thin valves that use a dual-plate or single-disc design to regulate flow. The discs swing open when fluid flows forward and close when the flow reverses, creating a compact and efficient sealing mechanism. The wafer-style design allows the valve to be installed between two flanges, making it ideal for systems where space is limited.
Advantages
Space-saving, compact design: The thin, lightweight design of wafer check valves allows for installation in tight spaces, reducing the overall size and weight of the system.
Low weight and easy to install: Wafer check valves are simple to install and require minimal support due to their lightweight construction.
Limitations
Not suited for high-viscosity fluids: The design may struggle to accommodate thicker, more viscous fluids, as the lightweight discs may not close effectively.
Limited to smaller pipelines: Wafer check valves are typically used in smaller-diameter pipes due to their compact size and design.
Common Applications
Power plants and energy systems: Wafer check valves are often used in power generation systems, where space is a premium, and compact designs are needed.
HVAC systems: These valves are ideal for HVAC systems, providing reliable flow control in tight spaces.
Industrial piping systems: Wafer check valves are used in a variety of industrial applications, particularly where space constraints and flow efficiency are key considerations.
Spring-Loaded Check Valve
Design and Function
A spring-loaded check valve uses a spring mechanism to assist the closure of the valve. In this design, the valve disc or piston is connected to a spring that automatically closes the valve when forward flow stops. The spring ensures a quick, reliable closure, preventing backflow and water hammer in systems with pulsating flows or high-pressure conditions.
Advantages
Prevents water hammer: The spring mechanism ensures a smooth, controlled closure that prevents the pressure surges that lead to water hammer.
Reliable operation even in vertical installations: Spring-loaded check valves are effective in both horizontal and vertical installations, providing flexibility in system design.
Limitations
Higher pressure drop due to the spring: The presence of the spring can cause a higher pressure drop, reducing system efficiency in certain applications.
Regular maintenance required in high-use systems: Over time, the spring may wear out or lose tension, requiring periodic maintenance to ensure reliable operation.
Common Applications
Water pumping systems: Spring-loaded check valves are commonly used in water pumping systems, where preventing backflow is critical.
Compressed air systems: These valves are also widely used in compressed air applications to maintain system pressure and prevent reverse flow.
Chemical processing plants: The quick closure and reliability of spring-loaded check valves make them ideal for use in chemical processing, where fluid control is crucial.
How to Select the Right Check Valve
Considerations Based on Application
Media Type (Liquids, Gases, Slurries)
The type of fluid flowing through the system plays a significant role in selecting the right check valve. Some check valves are designed to handle clean liquids, while others are better suited for gases or slurries containing particulates.
Liquids: For clean water or other liquid systems, swing or lift check valves are commonly used. However, for contaminated or viscous liquids, such as those in wastewater or food processing, a ball check valve may be more effective, as it can handle particles without jamming.
Gases: Systems carrying gases require valves with minimal leakage. Lift check valves or spring-loaded check valves are good choices for gas systems due to their ability to provide a reliable seal.
Slurries: In slurry systems, where the fluid contains suspended solids, the diaphragm or ball check valves are often preferred. These designs are less prone to clogging or wear from abrasive particles.
Pressure and Temperature Ranges
The operating pressure and temperature of the system should also guide valve selection. Different check valve types are designed to withstand varying pressure and temperature levels.
High-pressure systems: Lift and spring-loaded check valves are ideal for high-pressure applications because of their robust design and ability to handle extreme conditions.
Low-pressure systems: For low-pressure systems, a swing check valve may be sufficient, as it offers low resistance and minimal pressure drop.
Temperature considerations: In high-temperature environments, such as steam or chemical processing, material compatibility becomes critical. Metal-bodied valves, such as stainless steel or brass, are generally more suited to high temperatures, while plastic or rubber-based valves may degrade quickly.
Flow Rates and System Design
Flow rate is another important consideration when selecting a check valve. Valves must be chosen based on the desired flow capacity to avoid unnecessary pressure drops or system inefficiencies.
Low-velocity flows: Swing check valves are ideal for low-flow systems, as they open easily with minimal pressure. However, in systems with fluctuating or pulsating flow, this valve type may not seal effectively, leading to water hammer or system damage.
High-velocity flows: Spring-loaded check valves or lift check valves are better suited for systems with higher flow rates or pressure fluctuations. Their design ensures quick closure to prevent reverse flow, even at high velocities.
Piping configuration: System layout is also important. Wafer check valves, for instance, are compact and ideal for space-constrained systems. They can be installed between flanges in tight piping configurations.
Factors to Consider When Choosing a Check Valve
Pressure Drop
Pressure drop refers to the reduction in fluid pressure as it passes through the valve. Different valve designs cause varying degrees of pressure loss, which can impact the system’s efficiency.
Swing check valves: These valves generally cause a low-pressure drop due to their larger flow passage and smooth operation. They are ideal for systems where maintaining minimal resistance is critical.
Ball check valves: While effective in many applications, ball check valves may result in higher pressure drops compared to other types because of the smaller flow area created by the ball.
Spring-loaded check valves: These valves tend to introduce more pressure drop due to the spring mechanism resisting flow. However, they offer reliable performance in high-pressure systems.
It’s important to balance the need for preventing reverse flow with the impact the valve will have on overall system pressure.
Installation Orientation
The orientation of the valve within the system, whether horizontal or vertical, can influence valve performance.
Horizontal installation: Swing check valves and ball check valves are more effective in horizontal systems where gravity helps keep the valve disc or ball in position when closed.
Vertical installation: For vertical systems, particularly those with upward flow, lift check valves and spring-loaded check valves are better suited, as they use gravity or spring tension to ensure a secure seal even when fluid is not flowing. Installing a swing check valve in vertical piping can lead to operational issues if the disc doesn’t close properly.
Material Compatibility
The material of the check valve must be compatible with the media to avoid corrosion, wear, or contamination. Different materials offer varying levels of resistance to chemicals, temperature, and abrasion.
Metal valves: Stainless steel, brass, and cast iron valves are commonly used in systems involving high temperatures, chemicals, or pressure. Stainless steel, in particular, offers excellent corrosion resistance, making it suitable for aggressive chemicals or corrosive fluids.
Plastic valves: Plastic valves made from materials like PVC or polypropylene are suitable for lower-pressure, non-corrosive applications such as water systems. However, they are less durable under high temperatures or when exposed to harsh chemicals.
Elastomers and rubber: Diaphragm check valves often use elastomer components, such as EPDM or PTFE, to handle sensitive fluids without contamination. Care must be taken to ensure these materials are compatible with the chemicals being transported, as some chemicals can cause degradation.
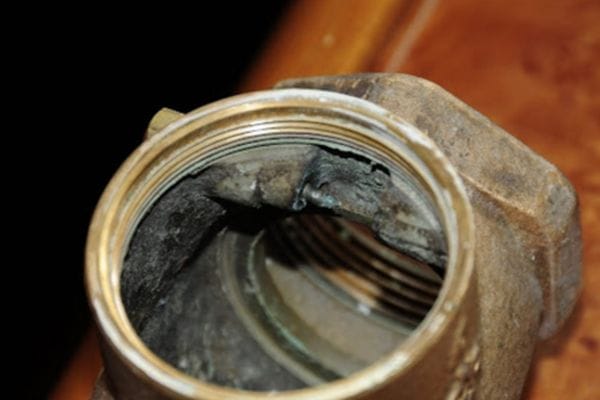
Maintenance and Lifespan of Check Valves
Regular maintenance is essential for ensuring the long-term performance and safety of check valves. While check valves are designed for durability, they are not immune to wear and tear. Maintenance practices vary depending on the valve type and the environment in which it operates.
Inspection Frequency
Establishing a routine inspection schedule is important to catch early signs of wear, corrosion, or malfunction. Regular inspections help identify issues like valve sticking, leakage, or degradation before they lead to system failure.
Swing check valves: The hinge or disc may wear down over time, especially in high-use or abrasive applications. Regular inspection of these components is essential to prevent operational issues.
Spring-loaded check valves: Over time, the spring may lose tension or become corroded. Regular checks of the spring mechanism can help prevent valve malfunction, particularly in high-pressure systems.
Diaphragm check valves: Diaphragms should be inspected frequently in systems where they come into contact with abrasive or corrosive media. They can wear down or become brittle, leading to leakage or valve failure.
Cleaning and Debris Removal
In systems transporting slurries or fluids containing particulates, debris can accumulate in the valve, causing clogging or improper sealing. Ball check valves, in particular, are susceptible to clogging in systems with high levels of contamination. Regular cleaning or flushing of the system can extend the life of the valve and maintain performance.
Valve Replacement
Even with regular maintenance, check valves have a finite lifespan. Knowing when to replace a check valve is important to prevent leaks, system damage, or inefficient operation. Monitoring signs like increased pressure drops, leakage, or sluggish operation can help determine when a valve has reached the end of its useful life.
Conclusion
Selecting the correct check valve is essential for maintaining system efficiency and preventing costly issues such as reverse flow, water hammer, or equipment failure. It is important to match the valve type to the media, pressure, flow rate, and system design to ensure reliable performance and longevity. Additionally, regular maintenance and inspection are key to extending the life of the valve and keeping your system running smoothly.
FAQ
What is a check valve?
A check valve is a one-way valve that allows fluid to flow in one direction and prevents reverse flow.
How does a check valve work?
Check valves use a disc, ball, or diaphragm that opens when fluid flows forward and closes when the flow reverses, preventing backflow.
What are the main types of check valves?
Common types of check valves include swing check valves, ball check valves, lift check valves, diaphragm check valves, wafer check valves, and spring-loaded check valves.
Where are check valves used?
Check valves are widely used in industries such as oil and gas, water systems, HVAC, chemical processing, and pharmaceuticals.
Can a check valve be installed vertically?
Yes, certain types of check valves, like lift check valves and spring-loaded check valves, can be installed vertically, but proper orientation must be ensured for effective operation.
What causes a check valve to fail?
Common causes of check valve failure include debris buildup, wear and tear of internal components, improper installation, or using the wrong valve type for the system.