Ball valves are essential components in fluid control systems, designed to regulate the flow of liquids and gases with remarkable efficiency. Their simplicity, reliability, and ability to completely shut off or allow flow make them popular choices across various industries, from plumbing and water management to oil, gas, and chemical processing. Unlike other types of valves, ball valves stand out for their quick operation and minimal wear, making them ideal for a wide range of applications where precision and durability are critical.
What Is a Ball Valve?
Definition
A ball valve is a mechanical device used to control the flow of fluids—liquids or gases—by using a rotating spherical ball inside the valve body. The ball has a hole, or port, through its center, which allows fluid to pass when aligned with the valve openings. When rotated 90 degrees, the ball blocks the flow, effectively shutting off the passage. Ball valves are widely known for their reliability, quick operation, and ability to provide a complete shut-off, making them a popular choice for various industries, including water, gas, and chemical systems.
Ball valves can handle high pressures and temperatures, making them versatile for different applications. Their simple operation, along with the ability to withstand wear, makes them a go-to valve type for situations where frequent opening and closing are required.
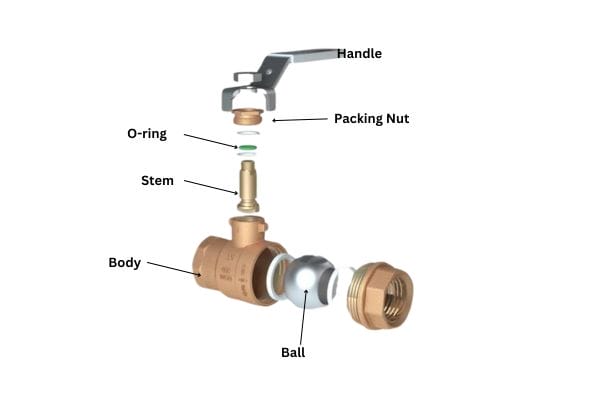
Key Components
Body
The body of a ball valve is the outer shell that houses all internal components. It is typically made from materials such as brass, stainless steel, or PVC, depending on the application. The material choice determines the valve’s durability, corrosion resistance, and ability to handle different types of fluids and environmental conditions. For industrial applications, metals like stainless steel are preferred due to their strength and resistance to harsh chemicals or high temperatures.
Ball
At the heart of the ball valve is a spherical ball, which is designed with a hollow center or port. When the hole in the ball aligns with the valve’s inlet and outlet, the fluid can flow through without restriction. Rotating the ball 90 degrees turns the solid side of the ball toward the flow, stopping it entirely. The precision with which the ball rotates ensures that ball valves offer an excellent seal, making them highly effective for on/off flow control.
Seats
The seats in a ball valve are soft or metal rings that fit tightly around the ball, providing a seal between the ball and the valve body. These seats prevent fluid from leaking when the valve is closed. Depending on the valve design, materials for the seats can vary, with common choices being Teflon, rubber, or metal. The seats play a critical role in ensuring the valve’s tight closure and long-term functionality by reducing wear on the ball and maintaining sealing integrity.
Stem
The stem connects the ball to the actuator or handle. When the actuator or handle is turned, the stem rotates, which in turn moves the ball. Stems are designed to withstand the torque exerted during operation and are typically made from the same material as the valve body to ensure durability. A properly functioning stem is crucial for smooth valve operation, as it allows the ball to rotate efficiently with minimal effort.
Actuator or Handle
Ball valves are operated manually using a handle or automatically using an actuator. Manual valves typically have a lever handle, which provides an easy, visual indication of whether the valve is open (aligned with the flow) or closed (perpendicular to the flow). For automated systems, electric or pneumatic actuators are used to control the valve remotely. This is especially useful in applications where manual control is impractical or unsafe.
Function Overview
In general, ball valves function by offering two main states: fully open or fully closed. In the open position, the ball’s port allows fluid to pass through freely, with minimal restriction. When closed, the solid part of the ball blocks the flow, creating a tight seal. Ball valves are primarily used for shut-off applications, where their reliable and quick operation is essential. Because they do not throttle flow, ball valves are less suitable for fine-tuning fluid control, but they are ideal for applications that require complete on/off control.
How Ball Valves Work
Basic Mechanism
At the core of a ball valve’s functionality is a rotating spherical ball with a hollowed-out center (or “bore”). The most common mechanism involves turning the ball 90 degrees to open or close the valve. When the ball is rotated so that its bore aligns with the flow path of the fluid, the valve is in the “open” position, allowing the fluid to pass through. Conversely, when the ball is turned so that the solid part of the ball faces the flow path, the valve is in the “closed” position, blocking the fluid from flowing.
This 90-degree rotational movement is the fundamental operation of a ball valve, and it can be easily controlled using a handle or an actuator. In manual systems, the handle is turned 90 degrees to open or close the valve, providing a quick and clear visual indicator of the valve’s status. When the handle is parallel to the pipe, the valve is open; when it’s perpendicular, the valve is closed.
Bore Alignment and Flow
The ball inside the valve has a bore or opening that runs through it. When this bore is aligned with the valve’s inlet and outlet ports, the fluid flows freely. In this position, the cross-sectional area available for the fluid to pass through is almost identical to that of the connected pipe, ensuring minimal flow restriction.
However, when the ball is rotated 90 degrees, the bore is no longer aligned with the ports, and the solid part of the ball blocks the flow entirely. The quick transition from open to closed is one of the main reasons ball valves are used in applications where complete shut-off is needed.
Flow Control Mechanism
Ball valves are mainly used for simple on/off control of fluid flow. Unlike other types of valves, such as globe valves or needle valves, ball valves are not designed to throttle or regulate flow. This is because the flow control mechanism of a ball valve does not allow for precise adjustments in fluid flow. Instead, it excels in providing a reliable, leak-proof seal when closed and an unobstructed flow when open.
The binary nature of flow control (either fully open or fully closed) makes ball valves ideal for situations that demand rapid and complete shut-off. In scenarios where throttling or fine flow control is required, ball valves are generally not recommended because partial opening can lead to damage or wear on the seats and ball, resulting in leaks over time.
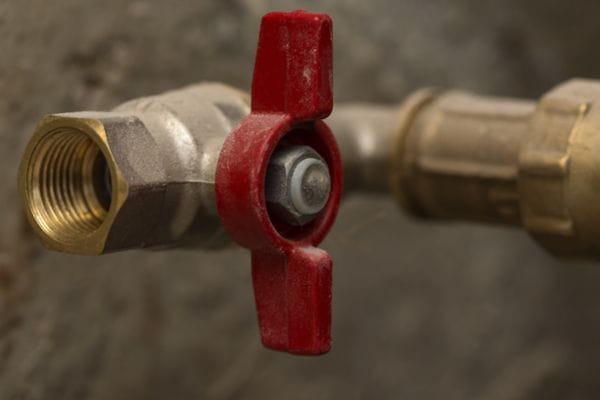
Full Port vs. Reduced Port
There are two primary configurations of ball valves: full port and reduced port.
Full Port Ball Valves:
In a full port ball valve, the bore inside the ball has the same diameter as the connected pipe. This ensures that there is no restriction in flow, and the fluid passes through as if the valve wasn’t there at all. Full port ball valves are used in applications where maintaining the maximum flow rate is critical, such as in high-demand industrial processes.
Reduced Port Ball Valves:
In reduced port (or standard port) ball valves, the bore is smaller than the diameter of the connected pipe. This creates a slight restriction in the flow, leading to some pressure drop as the fluid moves through the valve. Reduced port ball valves are used in situations where the highest flow rate is not essential, but the need for reliable shut-off remains.
The choice between full port and reduced port valves depends on the specific application. Full port valves are ideal for systems requiring high flow rates and minimal pressure loss, while reduced port valves are more suitable for systems where cost savings and compact size are more important considerations than maintaining the full flow rate.
Directional Flow
Ball valves are versatile in terms of the directional flow they can accommodate, making them suitable for a wide range of fluid control applications.
Single-Direction Flow
In many systems, ball valves are used for single-direction flow, meaning that the fluid is intended to move in one direction through the valve. These valves are designed to allow fluid to pass when the valve is open and block the fluid entirely when the valve is closed. Single-direction ball valves are commonly used in applications such as plumbing systems or industrial fluid control, where controlling flow in one direction is essential.
Multi-Directional Flow
Ball valves can also be designed to handle multi-directional flow, providing even greater versatility. Multi-port ball valves typically feature two or more ports, allowing them to direct fluid flow in different directions or switch between different flow paths. These valves are ideal for applications that require fluid diversion, mixing, or distribution.
For example:
Two-Way Ball Valves: These are the most common type, allowing fluid to flow in or out of two ports. A two-way valve has a simple on/off function that controls fluid flow in one path.
Three-Way Ball Valves: These valves have an additional port, which enables them to direct flow from one inlet to either of two outlets or vice versa. They are commonly used in systems that need to divert or mix fluid flow. The ball inside the valve can be designed in an L or T shape, providing different flow configurations based on the needs of the system.
Accommodating Different Flow Types
The design of ball valves allows them to handle a variety of flow types, whether it’s a simple one-way flow or a more complex multi-directional flow setup. The ball’s ability to rotate easily and block or permit flow in specific directions makes it possible to use ball valves in highly specialized applications where precise control of fluid movement is required.
For instance, in systems requiring alternate flow paths or fluid distribution, a multi-port ball valve can efficiently switch between different outlets, reducing the need for multiple valves and simplifying the piping layout.
Types of Ball Valves
Based on Bore Size
The size of the bore, or the opening inside the ball, directly affects how fluid flows through the valve. There are three common types of ball valves based on bore size:
Full Port Ball Valves
Description:
Full port (or full bore) ball valves have a bore that matches the diameter of the connected pipe. This design ensures that there is no restriction to fluid flow, allowing the maximum flow rate through the valve without any pressure drop. The ball inside the valve has a larger opening, providing an uninterrupted flow of fluid.
Advantages:
Maximum flow with minimal friction loss.
No significant pressure drop.
Ideal for applications where maintaining the flow rate is critical, such as in pipelines or systems that require high-volume flow.
When They Are Used:
Full port ball valves are commonly used in industries where maintaining high flow efficiency is essential, such as in gas pipelines, water distribution systems, and processing plants. They are also favored in systems where fluid characteristics (such as particle size) demand that the flow path remains unobstructed.
Reduced Port Ball Valves
Key Features:
In reduced port ball valves (also known as standard port ball valves), the bore is smaller than the pipe diameter, leading to a reduction in flow capacity. This design results in a slight pressure drop because the fluid flow is constricted as it passes through the valve.
Applications:
Suitable for applications where a slight reduction in flow is acceptable.
Cost-effective due to smaller ball size and body dimensions, which reduce material usage.
Commonly used in water distribution systems, chemical processes, and HVAC systems where full flow is not always required.
V-Port Ball Valves
How They Offer Better Flow Control:
V-port ball valves are designed with a “V” shaped notch in the ball, allowing for more precise flow control. This feature makes them suitable for throttling applications, where controlling the rate of fluid flow is critical. As the valve opens, the V-notch creates a more controlled, gradual increase in flow compared to standard ball valves.
Precise Regulation:
Allows for accurate flow regulation by controlling the fluid at different stages of valve opening.
More resistant to wear in throttling applications due to the gradual opening and closing process.
When They Are Used:
V-port ball valves are ideal for applications requiring precise flow control, such as chemical processing, water treatment, and systems where fluids need to be delivered at a specific rate or pressure.
Based on Valve Design
Ball valves can also be categorized based on their internal design, particularly in how the ball is supported within the valve body.
Floating Ball Valve
How It Works:
In floating ball valves, the ball is suspended inside the valve body by the seats, without any additional support mechanisms. The ball is free to move slightly in response to fluid pressure, which helps to create a tight seal when the valve is in the closed position.
Features:
Simple design and lower cost.
The floating ball pushes against the downstream seat to create a reliable seal.
Best suited for lower to medium pressure applications.
Applications:
Floating ball valves are commonly used in industries such as water distribution, oil and gas, and manufacturing systems. They are especially effective in low- to medium-pressure environments where a tight shutoff is needed.
Trunnion Ball Valve
Working Principle:
Trunnion ball valves feature an additional mechanical anchoring system for the ball. The ball is supported by a trunnion, which is a shaft that holds the ball in place and reduces the stress on the seats. This design allows the valve to operate under higher pressures without excessive wear on the seats.
Suitability for Higher Pressure Systems:
Handles higher pressures more effectively than floating ball valves.
Less torque required to operate the valve, which makes it easier to automate.
Ideal for high-pressure applications in oil and gas, power generation, and petrochemical industries.
Applications:
Trunnion ball valves are typically found in large-scale systems where high pressure and flow control are essential, such as in gas transmission pipelines, power plants, and large-scale water systems.
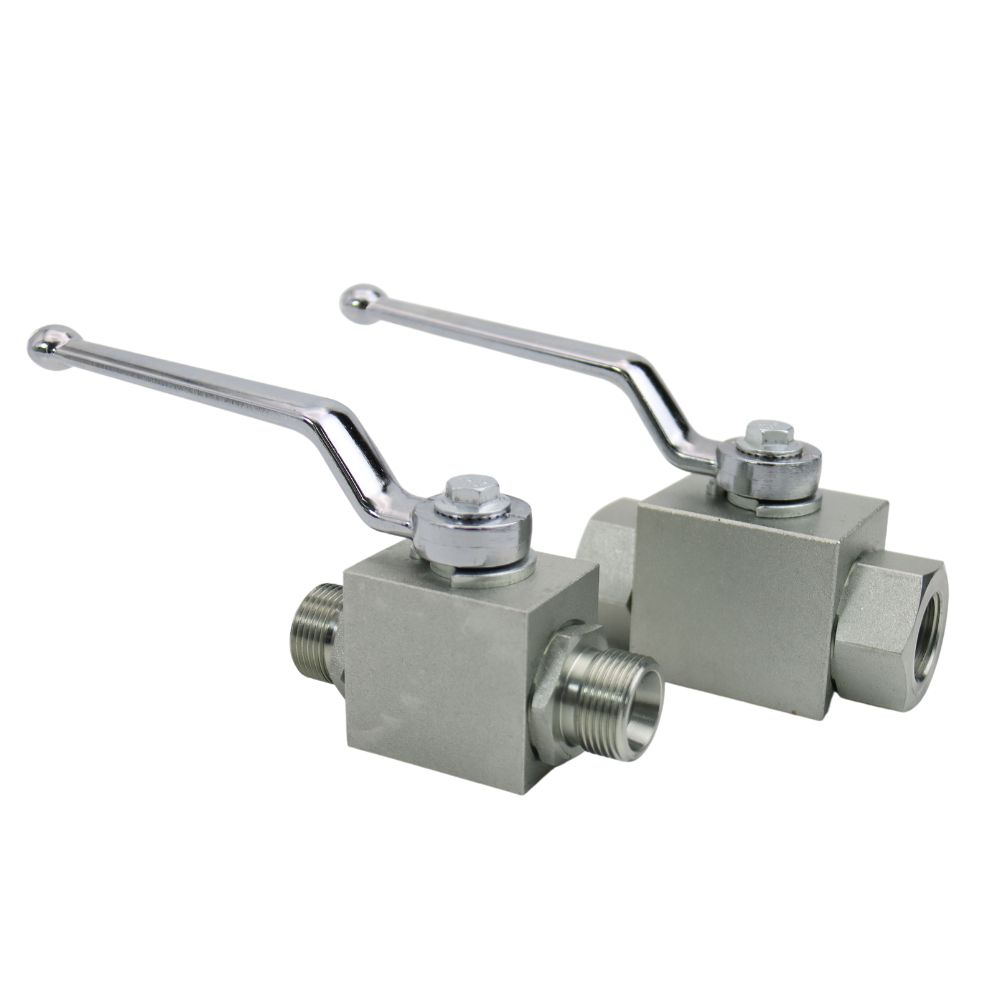
Based on Material
The material of the valve body is another key factor in determining its suitability for different applications. The most common materials used for ball valves are brass, stainless steel, and PVC.
Brass Ball Valves
Durability and Resistance:
Brass is a durable material that offers good resistance to corrosion and wear, making it suitable for various fluid types, including water, gas, and certain chemicals. Brass ball valves are widely used in plumbing and low- to medium-pressure applications due to their cost-effectiveness and durability.
Applications:
Residential and commercial plumbing.
HVAC systems.
Low-pressure industrial processes.
Stainless Steel Ball Valves
Strength and Corrosion Resistance:
Stainless steel ball valves are highly resistant to corrosion, high temperatures, and pressure. They are ideal for use in harsh environments and systems that require the handling of aggressive chemicals, such as in the food and beverage industry, marine applications, and oil and gas systems.
Applications:
Chemical processing.
Oil and gas production.
Marine systems and seawater applications.
PVC Ball Valves
Lightweight and Cost-Effective:
PVC (polyvinyl chloride) ball valves are lightweight, inexpensive, and resistant to corrosion. They are commonly used in systems that handle non-corrosive fluids, such as water or certain chemicals. However, they are not suited for high-pressure or high-temperature applications.
Applications:
Irrigation systems.
Swimming pool equipment.
Water distribution in residential and commercial settings.
Based on Operation Mechanism
Ball valves can be manually operated, or they can be automated using electric or pneumatic actuators. Each method of operation has its own advantages depending on the system’s needs.
Manual Ball Valves
Handle-Operated Ball Valves:
Manual ball valves are the simplest type, operated by turning a lever or handle to rotate the ball inside the valve. This type of valve is commonly used in systems where ease of operation and immediate feedback on the valve’s status (open or closed) are essential.
Applications:
Plumbing systems.
HVAC systems.
Low-pressure industrial applications.
Electric Ball Valves
Automation and Electric Actuation:
Electric ball valves are automated using electric actuators that turn the valve on and off remotely. These valves are often used in systems that require precise control over the valve’s operation or where manual operation is impractical due to the location of the valve.
Applications:
Automated manufacturing processes.
Remote pipeline control.
Building automation systems.
Pneumatic Ball Valves
Compressed Air for Valve Operation:
Pneumatic ball valves are operated using compressed air to move the actuator, allowing for rapid opening and closing. Pneumatic valves are typically used in industrial systems where speed and reliability are critical. They are especially useful in hazardous environments where electric components could pose a risk.
Applications:
Oil and gas systems.
Chemical plants.
Industrial automation.
Limitations and Considerations
While ball valves are highly versatile and reliable for on/off flow control, they do have some limitations that should be considered when selecting them for specific applications.
Not Suitable for Throttling
Ball valves are primarily designed for quick, complete shut-off or opening, but they are not ideal for flow regulation or throttling. The key reason lies in the design of the valve. Unlike globe or needle valves, which are specifically engineered to allow gradual adjustment of flow, ball valves operate in a binary manner — they are either fully open or fully closed.
Why They Aren’t Used for Flow Regulation:
Precision: Ball valves cannot provide the fine control needed for throttling. Partial opening of the ball creates an uneven flow path, which can cause turbulence and irregular flow rates.
Wear and Tear: Attempting to use a ball valve for throttling can cause the ball and the seats to wear prematurely. The high velocity and pressure of fluids passing through a partially open valve can erode the components, leading to leaks or valve failure over time.
Cavitation: In some cases, throttling with a ball valve can cause cavitation, where rapid pressure changes create vapor bubbles that can damage the valve’s internal parts. This can reduce the valve’s lifespan and effectiveness.
For applications requiring precise control over fluid flow, it’s advisable to use valves specifically designed for throttling, such as globe or needle valves.
Potential for Wear and Tear
Ball valves are known for their durability, but they are not immune to wear and tear, especially in demanding environments. Over time, certain components of the valve, particularly the seals and seats, can degrade due to continuous use, leading to reduced performance and potential failure.
Common Issues:
Wear on Seals and Seats: The seats and seals inside the valve are critical for creating a tight, leak-free seal when the valve is closed. However, with repeated operation, these components can wear out, especially if the valve is exposed to abrasive or corrosive fluids. This can lead to leaks or difficulty in fully closing the valve.
Erosion: In systems where high-pressure fluids flow through the valve at high speeds, the ball and seats can experience erosion. Over time, this erosion weakens the valve’s sealing ability, leading to leaks or failure to operate effectively.
Sticking or Seizing: In environments where the valve is exposed to harsh conditions, such as extreme temperatures or corrosive chemicals, the ball may stick or seize within the valve body. This makes it difficult or impossible to turn the valve without excessive force, potentially damaging the stem or handle.
To minimize wear and tear, regular maintenance and inspections should be carried out, and worn components such as seals and seats should be replaced as needed.
Pressure Limitations
While ball valves are highly effective in many low- to medium-pressure applications, they may not always be the best choice for extremely high-pressure systems. The design of ball valves — particularly floating ball valves — can create challenges in maintaining a reliable seal in high-pressure environments.
When to Consider Alternative Valve Types:
Floating Ball Valves: In high-pressure systems, floating ball valves may struggle to maintain a tight seal due to the increased pressure pushing the ball against the seats. This can result in leaks or difficulty operating the valve.
Trunnion Ball Valves: While trunnion ball valves are designed to handle higher pressures more effectively, even they have limits, particularly in systems where pressures exceed their rated capacity.
In systems with very high pressure, alternative valve types like gate valves or globe valves may provide more reliable performance. These valves are designed to withstand higher pressures without sacrificing sealing ability or durability.
Conclusion
Selecting the right type of ball valve is crucial for ensuring optimal performance in any system. Whether you need a full port valve for maximum flow, a trunnion valve for handling high pressure, or a brass or stainless steel valve for corrosion resistance, understanding the specific requirements of your application will guide you to the best choice. If you have any questions or need assistance in choosing the correct ball valve for your system, don’t hesitate to reach out.
FAQ
What is a ball valve used for?
A ball valve is used to control the flow of liquids or gases by opening, closing, or partially obstructing a flow path.
How does a ball valve work?
A ball valve works by rotating a ball with a hollow center inside the valve body. Turning the handle or actuator 90 degrees opens or closes the valve.
Can ball valves be used for throttling?
No, ball valves are not ideal for throttling as they are designed for full on/off control, not for precise flow regulation.
What materials are ball valves made of?
Ball valves can be made from materials like brass, stainless steel, and PVC, each suited for different types of fluids and environments.
What is the difference between a full port and a reduced port ball valve?
A full port ball valve has a bore equal to the pipe diameter, allowing maximum flow, while a reduced port valve has a smaller bore, causing some flow restriction.
Are ball valves suitable for high-pressure applications?
Some ball valves, like trunnion-mounted ball valves, are designed for high-pressure applications, while floating ball valves may not perform as well under extreme pressure.