Did you know that over 50% of hydraulic hose failures are linked to insufficient or irregular inspections? Studies show that neglecting routine checks significantly increases the risk of sudden failures, resulting in unexpected downtime, costly repairs, and even serious safety hazards. For industries that rely on hydraulic systems, the consequences of these failures can be severe, affecting both productivity and profitability. Regular inspection of hydraulic hoses isn’t just a matter of routine maintenance—it’s essential for ensuring operational safety, maximizing efficiency, and ultimately reducing overall costs.
Factors Affecting Hydraulic Hose Inspection Frequency
When determining the ideal inspection frequency for hydraulic hoses, several critical factors come into play. Each of these factors can significantly impact hose performance, safety, and longevity.
Pressure Levels
Operating pressure is one of the primary determinants of how often hydraulic hoses should be inspected. Hoses that consistently handle high-pressure loads are at a greater risk of wear, bulging, or failure due to the constant stress they endure. Elevated pressure levels can lead to:
Accelerated internal damage, including weakened reinforcement layers.
Increased likelihood of cracking, leaks, and other forms of deterioration.
To mitigate these risks, hoses operating under high pressure should undergo more frequent inspections, ideally weekly or even daily in some high-risk scenarios. In contrast, hoses operating under moderate or low pressures might be inspected less frequently but still regularly to ensure consistent performance.
Temperature Extremes
Hydraulic hoses are also highly susceptible to temperature variations. Extreme temperatures—whether too high or too low—can severely impact hose materials:
High temperatures can cause the hose’s outer cover to become brittle, leading to cracking and potential leaks.
Low temperatures may result in loss of flexibility, making hoses more prone to damage when bent or stressed.
The impact of temperature extremes necessitates frequent checks in environments where temperature fluctuates significantly or remains consistently high or low. Pay particular attention to signs of material degradation, such as discoloration, hardening, or softening of the hose surface.
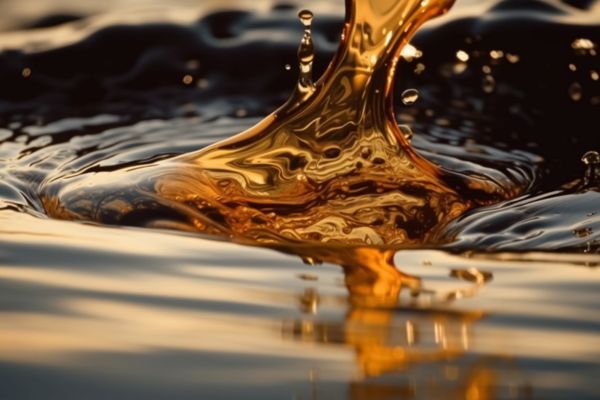
Fluid Type and Compatibility
The type of fluid being transported through the hose also affects inspection frequency. Fluids that are corrosive, abrasive, or chemically incompatible with the hose material can lead to premature failure. For instance:
Hydraulic fluids with high water content can lead to internal corrosion if hoses aren’t specifically designed to handle them.
Incompatible fluids can cause material swelling or softening, leading to leaks or bursts.
Inspecting hoses that carry corrosive fluids should be prioritized, with checks focusing on both the internal lining and the fittings to ensure there is no chemical-induced damage or leaks.
Environmental Conditions
External environmental factors can be as damaging as internal pressures or fluids. Hoses exposed to dust, moisture, UV rays, or chemicals may deteriorate faster, requiring more vigilant inspection routines:
Dust and debris can cause abrasion on the hose surface, especially in construction or mining environments.
Moisture and chemical exposure can lead to external corrosion, weakening the hose material over time.
In such challenging environments, daily visual checks combined with regular physical inspections are recommended to catch potential issues early and prevent unexpected failures.
Usage Patterns
The frequency of hose use directly impacts how often they need to be checked. Hoses that are used continuously or for extended periods face more wear than those used intermittently:
Frequent use can lead to fatigue, both at the connections and along the hose body, making it critical to inspect them more frequently—at least weekly.
Hoses used occasionally may have longer inspection intervals but should still be checked regularly to ensure they’re in good condition before each use.
Adjusting inspection frequency based on usage patterns helps prevent wear-related failures and ensures hoses are in optimal condition for every operation.
Installation Quality
Lastly, the quality of the initial hose installation plays a crucial role in determining inspection needs. Poor installation practices, such as excessive bending, improper routing, or using incorrect fittings, can lead to accelerated wear and tear:
Incorrect bend radii can stress the hose beyond its designed limits, causing cracks and leaks.
Improper fitting connections may result in loose fittings or leakage, necessitating immediate attention.
Recommended Inspection Frequency
General Guidelines
Manufacturers typically provide inspection guidelines that serve as a baseline for establishing inspection intervals. These general guidelines are structured to ensure safety, optimize performance, and extend the lifespan of hydraulic hoses:
Weekly Inspections: Hoses operating in high-demand systems or severe conditions (e.g., high pressure, extreme temperatures).
Monthly Inspections: Standard for most hydraulic hoses, especially in moderate use scenarios. A monthly check allows you to identify signs of wear, leakage, and connection issues early.
Quarterly Inspections: Recommended for low-pressure or lightly used hoses. Quarterly inspections can be sufficient to identify minor issues before they escalate, as long as additional visual checks are performed periodically.
These intervals can vary depending on the specific application and manufacturer’s guidelines, so it’s essential to refer to the original equipment manual when establishing your inspection routine.
Inspection Based on Usage Type
Heavy-Duty Use
Hydraulic hoses used under constant high pressure, in harsh environments, or critical systems require frequent and thorough inspections:
Daily Visual Checks: Quick visual inspections should be performed daily to identify obvious signs of leaks, cracks, or significant wear.
Weekly Physical Inspections: Include pressure testing, checking for abnormal bulges, and examining the fittings and couplings for any signs of loosening or wear.
Monthly Comprehensive Inspections: Detailed checks involving both visual and physical inspections, possibly using advanced methods like infrared thermography or ultrasound detection to identify internal damages.
High-Risk Applications: In extremely demanding applications like construction, mining, or heavy manufacturing, hoses might need to be checked before each shift to ensure safety and functionality.
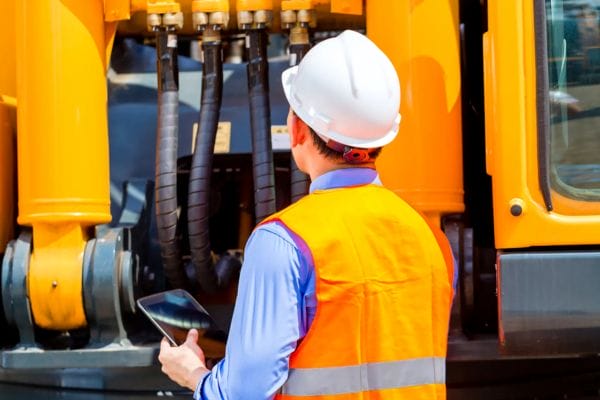
Moderate Use
For hoses used regularly but not under extreme conditions, a slightly less frequent inspection routine can be adopted:
Weekly Visual Checks: Regular visual checks should still be performed weekly to monitor for surface damage, leakage, or wear signs.
Bi-weekly Physical Inspections: These inspections should include bending tests, connection checks, and pressure testing to identify any developing issues.
Monthly Detailed Inspections: A full inspection, including internal checks where feasible, is advisable to catch any potential problems that could worsen with continuous use.
Light Use
Hydraulic hoses used occasionally or in low-pressure systems require a less frequent inspection routine, focusing more on ensuring readiness before use:
Pre-Use Visual Checks: Each time the hose is used, a quick visual inspection is necessary to ensure there are no visible cracks, leaks, or fitting issues.
Monthly Physical Inspections: Even for light use, a monthly physical inspection is recommended to identify any internal or external degradation that may not be visible immediately.
Quarterly Detailed Inspections: A comprehensive review, including pressure tests and material checks, ensures the hose remains in optimal condition despite infrequent use.
Special Cases: High-Risk Applications
Certain high-risk applications may demand daily inspection routines due to the potential severity of failures in these environments. Examples include:
Emergency Response Vehicles: Hydraulic systems in emergency vehicles, such as fire trucks or ambulances, require daily pre-operational checks to guarantee performance and safety in critical situations.
Heavy Construction Equipment: Excavators, bulldozers, and cranes are exposed to extreme conditions that make frequent checks (often before each use) a necessary safety measure.
High-Temperature or Corrosive Fluid Handling: Systems handling extreme temperatures or corrosive fluids should have hoses inspected daily to monitor for early signs of material degradation or leakage.
Inspection Process and Techniques
Visual Inspection
Visual inspection is the first line of defense in identifying potential issues with hydraulic hoses. It’s simple, and quick, and can often reveal obvious signs of wear or damage that may lead to failure if left unaddressed.
How to Conduct a Visual Inspection: Walk around the hydraulic system, observing the hose from end to end. Look for visible defects or anomalies that could indicate internal problems.
Checklist of Common Signs:
Cracks or Fraying: Look for surface cracks or fraying of the outer cover, which can signal aging or material deterioration.
Leaks: Inspect for visible leaks, especially around fittings and connections. Even minor leaks can indicate a significant problem inside the hose.
Bulges: Bulging or swelling along the hose can suggest internal pressure issues or damage to the reinforcement layers.
Abrasion Marks: Check for signs of abrasion, particularly in areas where the hose may rub against machinery or other surfaces. Abrasion can compromise the hose’s outer cover, leading to accelerated wear.
Worn Fittings: Inspect the fittings for wear, rust, or signs of loosening. Loose or worn fittings can result in leaks or connection failures.
While visual inspection is effective for spotting external damage, it should be performed regularly—ideally before each use in high-risk environments or at least weekly in lower-risk scenarios.
Physical Testing
Physical testing goes beyond visual checks by applying stress or pressure to the hose to assess its performance under working conditions. This method helps identify hidden weaknesses that could lead to sudden failures.
Pressure Testing: This involves applying pressurized fluid to the hose to check for leaks or signs of weakness. It is especially useful for detecting internal damage that is not visible externally. Conduct pressure testing safely by following these steps:
Isolate the hose from the rest of the system.
Gradually increase pressure to the recommended test level.
Monitor the hose for any leaks, bulges, or deformations during the test.
Release pressure slowly once the test is complete to avoid shock loads on the hose.
Bending Tests: Bending the hose manually (within its specified bend radius) can reveal potential issues like stiffness, cracking, or delamination of the inner layers.
Look for any unusual resistance or audible cracking sounds that might indicate internal damage.
Leak Detection Techniques: Use soapy water to identify leaks—spray it on the hose surface and fittings while the hose is under pressure. Bubbles forming on the surface indicate the presence of a leak.
Regular physical testing helps ensure the hose’s ability to handle operational pressures, reducing the risk of unexpected failures.
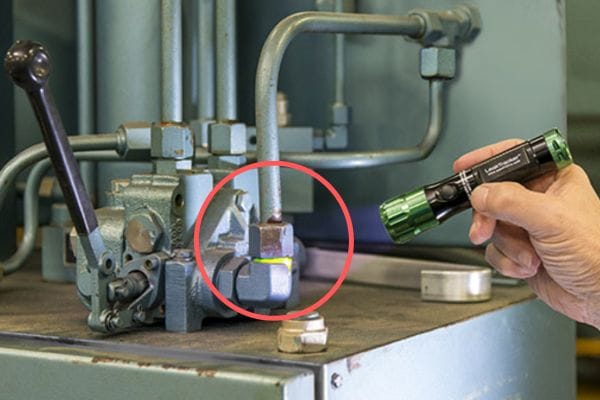
Use of Technology
Advancements in inspection technology have enhanced the ability to detect internal damage that is otherwise difficult to identify. Using these technologies can improve the accuracy of inspections and extend the service life of hydraulic hoses.
Infrared Thermography: This method involves using an infrared camera to detect temperature variations along the hose.
How it Works: Abnormal temperature patterns (e.g., hot spots) can indicate internal blockages, fluid turbulence, or friction points that might not be visible externally.
Benefits: Infrared thermography is non-invasive, making it ideal for identifying issues without disrupting system operation.
Ultrasound Devices: Ultrasonic inspection uses high-frequency sound waves to detect internal flaws or material inconsistencies.
How it Works: The device emits sound waves through the hose material, and any anomalies (e.g., delamination, cracks, or voids) will disrupt the sound wave’s travel, indicating a potential issue.
Benefits: Ultrasound is particularly effective for finding hidden internal defects, making it an excellent tool for preventive maintenance.
Best Practices for Effective Inspections
Training Personnel
Proper training is the foundation of effective hydraulic hose inspections. Personnel conducting inspections must understand the specifics of hydraulic systems and be familiar with potential failure signs to identify issues accurately.
Importance of Training: Well-trained staff can recognize signs of wear, diagnose potential issues, and suggest preventive measures. This minimizes downtime and helps prevent unexpected hose failures.
Components of Training
Visual identification of wear signs like cracks, bulges, and leaks.
Hands-on testing methods, such as pressure and bending tests.
Understanding of safety protocols to follow during inspection.
Familiarity with advanced inspection tools, such as infrared cameras or ultrasonic devices, to detect internal damage.
Continuous Skill Development: Regular refresher courses, updates on new inspection technologies, and hands-on training sessions keep personnel skills current and effective.
Standard Operating Procedures (SOPs)
Creating and following Standard Operating Procedures (SOPs) ensures inspections are consistent, thorough, and repeatable across the team.
Establishing SOPs: Develop a clear, step-by-step protocol that includes:
Inspection intervals based on hose usage and application (e.g., weekly, monthly).
Detailed checklists for visual, physical, and technological inspections.
Defined response actions if issues are identified (e.g., isolate the hose, report damage, schedule repairs).
Consistency and Documentation: SOPs ensure that every inspection is performed consistently, reducing variability and increasing reliability. Accurate documentation of each inspection also provides a historical record that helps track hose performance over time and supports predictive maintenance efforts.
Adaptability: While SOPs provide a structured approach, they should be adaptable to different hose types, applications, and operating conditions.
Using Manufacturer’s Recommendations
Aligning inspection routines with manufacturer guidelines is crucial to maintaining hose integrity and meeting safety standards.
Follow Manufacturer Guidelines: Manufacturers typically provide recommended inspection intervals, acceptable pressure levels, bending radii, and material compatibility guidelines. Adhering to these recommendations helps ensure hoses are maintained according to their design specifications.
Leverage Manufacturer Support: Manufacturers often offer resources like training materials, detailed manuals, and technical support that can assist with setting up effective inspection routines.
Customizing Inspections: Tailor your inspection approach based on the specific brand, type, and material of the hose, as manufacturer requirements can vary significantly between different products.
Safety Precautions During Inspections
Safety should always be a priority during hose inspections, as potential risks include high-pressure fluid leaks, mechanical injuries, and exposure to hazardous materials.
Ensure System Shutdown: Before conducting any physical testing or hose maintenance, ensure that the hydraulic system is fully depressurized and safely shut down.
Wear Personal Protective Equipment (PPE): Inspectors should wear appropriate PPE, including gloves, safety glasses, and protective clothing, to reduce the risk of injury from leaks or ruptures.
Avoid Direct Contact with Pressurized Hoses: Never handle a hose when it is under pressure. Inspectors should maintain a safe distance and use tools to check for leaks or damage.
Be Cautious with Hot Surfaces: In high-temperature systems, hoses can retain heat even after the system is shut down. Allow sufficient cooling time before beginning an inspection, and always use thermal gloves if necessary.
Conclusion
Now is the time to review your current inspection routines and ensure they meet the needs of your hydraulic systems. Take proactive measures by adjusting inspection schedules based on the insights shared in this article. A well-maintained system not only improves safety but also maximizes efficiency and reduces costs in the long run. Start refining your inspection practices today for a safer and more reliable operation.
FAQ
How often should I inspect my hydraulic hoses?
The recommended frequency varies based on usage. High-pressure or heavy-duty hoses may require daily or weekly checks, while moderate-use hoses should be inspected monthly, and light-use hoses quarterly.
What are the signs that a hydraulic hose needs to be replaced?
Common signs include cracks, bulges, leaks, abrasion marks, and worn fittings. If you notice any of these during an inspection, it’s time to consider replacing the hose.
Can I use technology to improve hose inspections?
Yes, tools like infrared thermography and ultrasound devices help detect internal damage and can improve the accuracy and efficiency of inspections.
What safety precautions should I take during hose inspections?
Always ensure the system is depressurized, wear protective equipment (e.g., gloves, safety glasses), and maintain a safe distance from pressurized hoses.
Do manufacturers provide specific inspection guidelines?
Yes, manufacturers typically offer guidelines on inspection intervals, pressure limits, and compatible fluids. Following these guidelines ensures safe and optimal hose performance.
What happens if I don’t inspect hydraulic hoses regularly?
Failing to inspect regularly can lead to unexpected failures, safety hazards, increased downtime, and higher repair costs, impacting both safety and productivity.