Hydraulic hoses play a crucial role in a wide range of industrial applications, acting as essential conduits for transporting pressurized fluids that power machinery, equipment, and systems. These hoses ensure efficient fluid flow and are integral to various sectors, including manufacturing, construction, agriculture, and more. With the right choice of hydraulic hose, companies can enhance operational performance, increase safety, and reduce downtime.
What Are Push-Lock Hoses?
Definition and Design
Push-Lock hoses are a type of hydraulic hose that features a simple yet innovative design, eliminating the need for clamps or specialized fittings. This design allows the hose to “push” securely onto barbed fittings, creating a tight seal through friction alone. The outer cover is typically made of a rubber compound, while the inner tube is designed to resist the particular fluids being conveyed. The hose itself often includes a reinforcing layer, which can be textile braids or similar materials, adding durability while maintaining flexibility.
The absence of clamps in Push-Lock hoses is their defining characteristic, making them highly convenient for quick installations. Unlike traditional hoses, where fittings need to be secured with wrenches and clamps, Push-Lock hoses require only a firm hand push onto the fittings, ensuring a snug fit without the risk of leaks. This makes them especially practical for applications that require frequent assembly or reconfiguration.
Common Applications
Push-Lock hoses are best suited for low to medium pressure systems, where the pressure typically ranges from 200 to 350 psi, depending on the hose design and manufacturer specifications. Their flexibility makes them ideal for use in air tools, pneumatic systems, industrial machinery, and certain types of hydraulic systems where pressure requirements are moderate.
These hoses are frequently used in lubrication lines, fuel lines, and general-purpose fluid transfer, especially in settings where speed and convenience of installation are critical. Their lightweight and pliable nature also makes them suitable for applications where space is constrained, such as in automotive and light machinery setups.
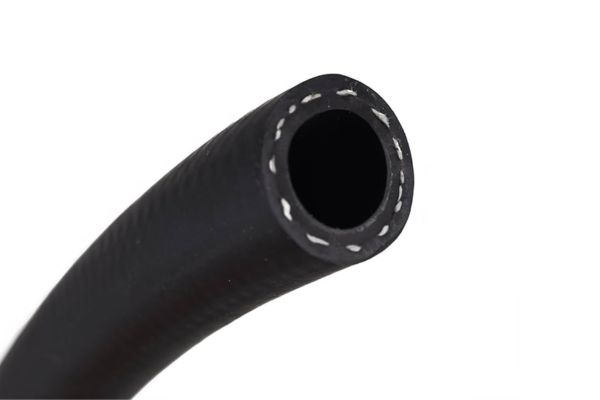
Advantages
Quick Installation: One of the biggest advantages of Push-Lock hoses is their ease and speed of installation. The lack of clamps and other securing hardware means that fitting these hoses takes only a few seconds, reducing installation time and labor costs.
Flexibility: Push-Lock hoses offer superior flexibility compared to most Traditional hoses. Their bend radius is usually tighter, allowing them to be routed easily in tight spaces and around corners. This makes them adaptable to complex hydraulic systems or applications with limited space.
Cost-Effectiveness: These hoses are typically more cost-effective, not only because of lower material costs (e.g., no clamps required) but also due to reduced labor costs during installation. They are often a go-to choice for budget-conscious operations needing efficient fluid transfer.
Maintenance-Friendly: Push-Lock hoses can be easily removed and reinstalled, making maintenance and replacement straightforward. This is particularly useful in settings where frequent hose changes or reconfiguration of the hydraulic system is necessary.
Limitations
Lower Pressure Capacity: Push-Lock hoses are generally designed for lower-pressure applications. Their friction-fit design limits the pressure they can handle, making them unsuitable for high-pressure hydraulic systems where pressures can exceed 2,000 psi.
Potential Fluid Compatibility Issues: While Push-Lock hoses are compatible with many fluids, some aggressive hydraulic fluids (e.g., certain types of oils or chemicals) may not be suited for this hose type, leading to degradation over time. The material composition of the inner tube must be carefully checked to ensure compatibility with the intended fluid.
Risk of Accidental Disconnection: Due to their push-fit nature, there is a small risk of the hose detaching from the fitting, especially if improperly installed or used in applications exceeding their pressure ratings. Proper inspection and adherence to manufacturer guidelines are essential to avoid leaks and failures.
What Are Traditional Hoses?
Definition and Design
Traditional hydraulic hoses are the most common type of hoses used in high-pressure hydraulic systems. Unlike Push-Lock hoses, Traditional hoses require fittings, clamps, or crimped connections to securely attach to equipment. The fittings are typically threaded or crimped using specialized tools to ensure a tight, leak-proof seal. This design provides a robust and reliable connection that can withstand the high pressures typical of demanding hydraulic applications.
These hoses are constructed with multiple layers for added strength. They typically include an inner tube made from rubber or thermoplastic material, reinforced with either steel wire braids, spirals, or synthetic textile layers, and protected by an outer rubber cover. The reinforcement layer is crucial, as it allows Traditional hoses to handle significantly higher pressures than Push-Lock hoses, often exceeding 2,000 psi, making them suitable for intense industrial environments.
Common Applications
Traditional hydraulic hoses are primarily used in high-pressure systems and are an essential component of heavy-duty equipment such as construction machinery, excavators, mining rigs, and agricultural equipment. Their strength and durability make them ideal for long-term installations, where reliability and resistance to wear and tear are critical.
These hoses are widely employed in hydraulic pumps, motors, cylinders, and other components that require the transmission of pressurized fluids over extended periods. Due to their ability to handle high pressures and temperatures, Traditional hoses are also suitable for power steering systems, lift trucks, and other high-demand hydraulic setups.
Their robust design makes them well-suited for use in harsh operating conditions, such as in mining sites, marine environments, and off-road applications, where they are exposed to dirt, vibrations, and potential impacts.
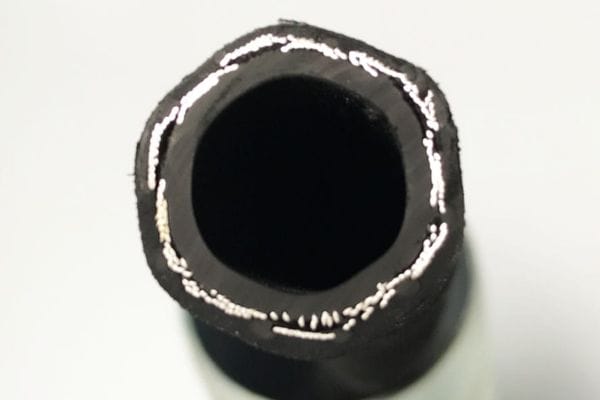
Advantages
High-Pressure Tolerance: One of the biggest advantages of Traditional hoses is their ability to handle high pressures. The reinforcement layers—whether steel wire or textile braid—provide exceptional strength, allowing these hoses to operate in systems with pressures well beyond what Push-Lock hoses can manage.
Durability: Traditional hoses are built to withstand harsh conditions, including abrasion, extreme temperatures, and impacts. Their robust construction ensures a longer service life, making them a cost-effective choice for heavy-duty applications where reliability is critical.
Wide Fluid Compatibility: Traditional hoses are typically compatible with a broad range of hydraulic fluids, including petroleum-based, synthetic, and water-based fluids. This versatility makes them ideal for a wide variety of applications, including those involving aggressive fluids or harsh chemicals.
Leak-Proof Connections: The use of crimped or threaded fittings provides a secure, leak-proof seal that minimizes the risk of fluid loss. This is especially important in high-pressure applications where fluid leaks can lead to significant safety hazards and equipment failures.
Limitations
Installation Complexity: Unlike Push-Lock hoses, Traditional hoses require special tools and fittings for installation, making the process more complex and time-consuming. Proper crimping or threading is essential to ensure a secure fit, which often demands skilled labor.
More Labor-Intensive Maintenance: Regular maintenance and inspection are critical for Traditional hoses, particularly in high-pressure applications. Any wear or damage to fittings, clamps, or the hose itself must be promptly addressed, which can be labor-intensive. Replacing these hoses often involves dismantling parts of the system, increasing downtime and labor costs.
Limited Flexibility: Due to their reinforced structure, Traditional hoses are generally less flexible than Push-Lock hoses. This can make routing through tight spaces more challenging, potentially increasing the installation time and requiring additional components like hose supports or bend restrictors.
Installation and Maintenance Comparison
Ease of Installation
Push-Lock Hoses: Push-Lock hoses are designed for quick and easy installation, making them a preferred choice for applications where minimizing downtime is critical. The installation process involves simply pushing the hose onto barbed fittings, which creates a tight seal through friction. No clamps, crimping, or specialized tools are needed, making the process straightforward and fast.
Tools Needed: No special tools are required for Push-Lock hose installation, although some manufacturers recommend using lubricant to ease the fitting process.
Time Consumption: The simplicity of installation significantly reduces the time needed compared to Traditional hoses. Since there are no fittings to crimp or secure with clamps, operators can connect these hoses quickly, making them ideal for applications where hoses need frequent changes or replacements.
Labor Costs: Push-Lock hoses require minimal labor, as the fitting process can often be done by less specialized personnel. The reduced need for skilled labor and the shorter installation time translates into lower overall labor costs. Additionally, Push-Lock hoses allow for reconfiguration or adjustment without incurring significant downtime, making them cost-effective for dynamic setups.
Traditional Hoses: Traditional hydraulic hoses require a more complex and labor-intensive installation process. These hoses rely on crimped fittings or threaded connections, which must be secured tightly to ensure a leak-proof fit. Crimping or threading requires specialized tools, such as crimping machines, wrenches, and in some cases, pressure gauges to ensure the connection is secure and can withstand the intended pressure.
Tools Needed: Crimping machines, wrenches, and other fitting tools are essential for Traditional hose installation. Crimping machines, in particular, are necessary to compress fittings onto the hose, ensuring a strong and leak-proof connection.
Time Consumption: Installing Traditional hoses is more time-consuming, as each fitting must be carefully crimped or threaded, tested, and secured. Proper alignment of the fittings and hose is crucial to avoid leaks or hose failures, making the process more meticulous.
Labor Costs: Due to the complexity of installation, Traditional hoses often require skilled labor. Technicians must be trained in crimping techniques and proper fitting procedures to ensure the hose operates safely at high pressures. This increases labor costs compared to Push-Lock hoses. Additionally, the potential for installation errors can add to downtime and costs, as improper crimping can lead to leaks or hose failures.
Maintenance Requirements
Push-Lock Hoses: Push-Lock hoses are generally easier to maintain due to their straightforward design. Their maintenance requirements are often lower, as they are typically used in low-to-medium pressure applications, which exert less stress on the hose.
Maintenance Schedule: Push-Lock hoses require regular visual inspections for wear, leaks, or disconnections. Checking for any signs of degradation, such as cracks, hardening, or bulging, is essential to maintain performance.
Common Repair Needs: Push-Lock hoses may develop issues like fitting detachment if they are improperly installed or subjected to pressure beyond their rated capacity. However, repairs or replacements are relatively simple, as the hoses can be quickly reattached to the fittings without the need for crimping tools.
Potential Downtimes: Downtime for Push-Lock hoses is generally lower since they can be replaced or reconnected rapidly. This quick turnaround minimizes operational disruptions and is particularly beneficial for facilities that prioritize continuous operations.
Traditional Hoses: Traditional hoses require more rigorous maintenance due to their role in high-pressure applications. Regular inspections and preventive measures are crucial to ensure safe operation.
Maintenance Schedule: Maintenance for Traditional hoses is more intensive, requiring frequent checks of the fittings, crimps, and the hose’s outer cover for any signs of wear, corrosion, or leaks. Because they handle high pressures, even minor damages can lead to significant failures, so periodic pressure tests are often conducted to verify their integrity.
Common Repair Needs: Common issues with Traditional hoses include fitting leaks, worn-out hose covers, or internal wear from abrasive fluids. Repairing or replacing Traditional hoses often involves dismantling parts of the system, making it a more laborious process. Crimped fittings, if damaged or leaking, must be re-crimped or replaced entirely, which requires tools and skilled labor.
Performance Under Pressure
Pressure Tolerance
Push-Lock Hoses: Push-Lock hoses are designed primarily for low-to-medium pressure applications, typically handling pressures ranging from 200 to 350 psi. They rely on a friction-based seal with barbed fittings, which makes them suitable for situations where extreme pressure is not a factor. These hoses perform well in pneumatic systems, lubrication lines, air tools, and other general industrial uses where pressure demands are moderate.
However, their pressure tolerance is limited by the friction-fit connection, which can only handle a certain level of force before potentially detaching or leaking. For this reason, Push-Lock hoses should never be used in high-pressure systems, as the seal may not hold under such conditions. While they offer dependable performance within their specified pressure range, exceeding the recommended capacity can result in rapid wear, failure, or blow-off of the hose from the fitting.
Traditional Hoses: Traditional hydraulic hoses, on the other hand, are built to withstand high-pressure environments, often handling pressures exceeding 2,000 psi and even reaching up to 10,000 psi in some applications. This capability is due to their reinforced construction, typically featuring multiple layers of steel wire braids or spirals, which offer added strength and prevent expansion under pressure.
The use of crimped or threaded fittings also contributes to their superior pressure tolerance, providing a secure, leak-proof connection that can sustain high pressure over prolonged periods. These hoses excel in demanding applications such as heavy machinery, construction equipment, and hydraulic power units, where maintaining high pressure is critical for operational efficiency.
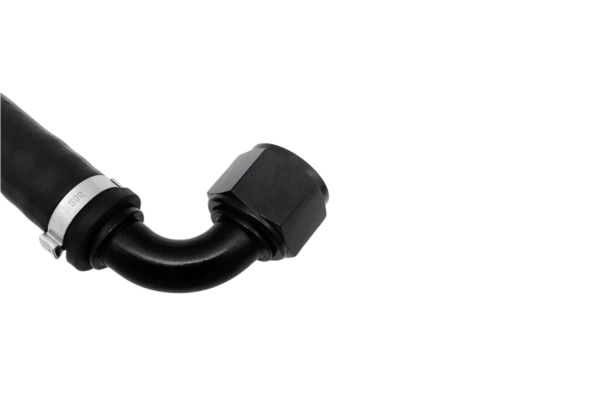
Temperature Resistance
Push-Lock Hoses: Push-Lock hoses generally offer moderate temperature resistance, with most standard models capable of handling temperatures ranging from -40°F to 212°F (-40°C to 100°C). This range is sufficient for many industrial applications, including indoor environments and machines that operate under stable temperatures.
However, in extreme conditions—such as exposure to high heat near engines or severe cold in outdoor settings—Push-Lock hoses may become prone to cracking or hardening. The materials used in these hoses, typically rubber or thermoplastic, can degrade faster when exposed to extreme temperatures, affecting their flexibility and pressure retention. For applications involving frequent temperature variations or extreme environments, Push-Lock hoses may require more frequent inspections and potential replacements to ensure safety and performance.
Traditional Hoses: Traditional hoses offer superior temperature resistance, with many models capable of enduring temperatures from -70°F to 250°F (-56°C to 121°C), and specialized versions able to withstand even higher temperatures. The outer covers of these hoses are often made from synthetic rubber or specialized compounds designed to resist heat, cold, and UV exposure.
This enhanced temperature resistance allows Traditional hoses to perform reliably in both high-heat environments, like construction equipment near engines or furnaces, and in low-temperature conditions, such as in cold storage facilities or outdoor winter settings. The robustness of Traditional hoses in extreme temperatures makes them ideal for applications that demand consistent performance regardless of environmental conditions.
Flexibility and Bend Radius
Push-Lock Hoses: Push-Lock hoses are known for their high flexibility, making them easy to route through tight spaces and complex layouts. They feature a tighter bend radius, allowing them to bend more sharply without kinking or collapsing. This makes Push-Lock hoses suitable for applications where compact routing is necessary, such as in automotive assembly lines, air tools, and industrial machinery with limited space.
The flexibility of Push-Lock hoses not only simplifies installation but also allows for dynamic movement, such as in robotic arms or moving components where the hose must bend repeatedly during operation. This adaptability is one of the major advantages of Push-Lock hoses in low-pressure systems, as it minimizes installation constraints and potential hose stress.
Traditional Hoses: While Traditional hoses are generally less flexible than Push-Lock hoses due to their reinforced construction, they still offer varying levels of flexibility depending on the type of reinforcement used. Hoses with a steel wire braid typically offer more flexibility compared to those with a spiral reinforcement, which is stiffer but provides greater strength.
The bend radius of Traditional hoses is larger than that of Push-Lock hoses, making them more challenging to install in tight spaces. However, they are engineered to withstand bending without compromising pressure capacity or structural integrity. In high-pressure systems, maintaining an appropriate bend radius is crucial to prevent hose fatigue, kinking, or premature wear. Specialized models with enhanced flexibility are available for applications that require bending but still demand high-pressure handling.
Material Compatibility and Fluid Resistance
Push-Lock Hoses:
Push-Lock hoses are generally made from rubber or thermoplastic materials with textile reinforcement, designed to provide compatibility with a wide range of hydraulic fluids. These hoses are particularly well-suited for water-based and oil-based fluids, including fluids used in pneumatic systems, lubricants, and low-pressure hydraulic applications. However, the material composition of Push-Lock hoses can vary, making it essential to verify compatibility with specific fluids before use.
Water-Based Fluids: Push-Lock hoses perform well with water-based fluids like water-glycol solutions, which are commonly used in hydraulic systems for fire resistance. The inner tube material is typically resistant to water absorption, reducing the risk of swelling or degradation.
Oil-Based Fluids: Push-Lock hoses are compatible with many petroleum-based fluids, such as mineral oils and lightweight lubricants. The rubber or thermoplastic inner tube is often designed to resist swelling or softening when exposed to these fluids.
Synthetic Fluids: While Push-Lock hoses can handle some synthetic fluids, such as certain biodegradable oils or phosphate esters, their chemical resistance is generally more limited compared to Traditional hoses. Some aggressive synthetic fluids may cause swelling, softening, or degradation of the hose material, reducing performance and lifespan.
Traditional Hoses:
Traditional hoses are constructed with multi-layered designs, including steel wire or textile reinforcement, with an outer rubber layer designed for enhanced chemical resistance. This robust design allows Traditional hoses to be compatible with a broader range of fluids, making them a more versatile option in diverse hydraulic systems.
Water-Based Fluids: Traditional hoses are highly compatible with water-based fluids, including water-glycol solutions and water-oil emulsions. The reinforced inner tube and outer cover are designed to prevent swelling, cracking, or degradation, ensuring long-term performance.
Oil-Based Fluids: Traditional hoses offer excellent resistance to petroleum-based oils, hydraulic fluids, and lubricants. They are less prone to softening or swelling, making them ideal for high-pressure hydraulic systems where exposure to oil-based fluids is continuous and intense.
Synthetic Fluids: Traditional hoses excel in compatibility with aggressive synthetic fluids, such as phosphate ester-based hydraulic fluids, which are commonly used in aviation and other high-performance hydraulic systems. The inner tube material is often made from specialized compounds like Viton or Teflon, which provide superior resistance to chemical degradation.
Potential Risks of Corrosion or Degradation
Push-Lock Hoses: The primary risk for Push-Lock hoses is chemical degradation when exposed to aggressive synthetic fluids or harsh chemicals. Over time, certain fluids can cause the inner tube to swell, soften, or even crack, compromising the seal and resulting in potential leaks or blow-offs. In applications where highly corrosive fluids are used, Push-Lock hoses may require more frequent inspections and replacements to maintain safety and performance.
Another risk is ozone degradation, which can affect the outer cover of the hose if exposed to direct sunlight or harsh environmental conditions. Ozone-resistant materials are often used in Push-Lock hoses to minimize this risk, but this depends on the specific hose composition.
Traditional Hoses: Traditional hoses are engineered to handle corrosive fluids and high temperatures without significant degradation. However, certain fluids, like aggressive acids or solvents, can still pose a risk of chemical breakdown over time. To combat this, many Traditional hoses incorporate specialized inner tube materials designed for extreme chemical resistance.
The outer cover of Traditional hoses is often reinforced with abrasion-resistant and weather-resistant materials, reducing the risk of environmental degradation. Additionally, Traditional hoses typically have a longer lifespan when exposed to UV light, ozone, or harsh weather conditions, making them more reliable in outdoor and heavy-duty applications.
Conclusion
Ultimately, selecting the right hose depends on the specific industrial requirements of your application. Assessing factors like pressure capacity, fluid type, environment, and budget will help determine the best hose type for optimal performance and safety. Evaluate your operational needs carefully to make the most effective choice for your hydraulic system.
FAQ
What is the main difference between Push-Lock and Traditional hoses?
Push-Lock hoses are designed for low-to-medium pressure with easy installation, while Traditional hoses handle high pressures and require more complex installation.
Can Push-Lock hoses be used in high-pressure applications?
No, Push-Lock hoses are not suitable for high-pressure applications. They are best for low-to-medium pressure systems.
Are Traditional hoses more durable than Push-Lock hoses?
Yes, Traditional hoses are more durable, designed with reinforced layers to withstand high pressure and harsh conditions.
Which hose type is more cost-effective?
Push-Lock hoses are generally more cost-effective for short-term, low-pressure use, while Traditional hoses offer better long-term value in high-pressure setups.
How do I decide which hose to use?
Consider factors like pressure requirements, fluid type, installation complexity, and budget to choose the right hose type.
Are either of these hoses recyclable?
Both have limited recyclability, but some components, like metal fittings in Traditional hoses, can be reclaimed.