Hydraulic hose connections play a critical role in the functionality and safety of hydraulic systems, which are essential in various industries, from manufacturing to construction. These connections are the lifelines of hydraulic machinery, facilitating the transmission of pressurized fluid that powers equipment. A secure and efficient hose connection ensures optimal system performance, minimizes the risk of leaks, and contributes to the overall longevity of the hydraulic system.
Understanding Hydraulic Connection Ports
A. Definition of Hydraulic Connection Ports
Hydraulic connection ports are specialized fittings designed to join hoses and pipes within hydraulic systems, facilitating the efficient transfer of pressurized fluid. These ports ensure a secure connection between components, preventing leaks and maintaining the integrity of the hydraulic circuit. The effectiveness of these connections is critical to the overall performance of hydraulic systems, which rely on precise fluid control for functionality.
B. Types of Hydraulic Hose Connection Ports
Male and Female Connectors
Male and female connectors are among the most common types of hose connections. Male connectors feature external threads or protrusions that fit into female connectors, which have corresponding internal threads or recesses. This design allows for a secure and tight seal, reducing the risk of fluid leakage under pressure.
Threaded Ports (NPT, BSP)
Threaded ports, such as National Pipe Thread (NPT) and British Standard Pipe (BSP), are prevalent in hydraulic applications. NPT fittings are designed with a tapered thread that provides a tight seal as they are tightened. BSP fittings, on the other hand, are available in both parallel and tapered forms, making them versatile for various applications. Understanding the differences between these standards is crucial for compatibility and performance.
Flange Connections
Flange connections consist of flat plates that are bolted together, creating a strong and stable joint. These connections are ideal for high-pressure applications and larger pipe sizes, as they distribute stress evenly across the joint. Flanges come in various designs, including raised face, flat face, and ring-type joint, each suited for specific operational conditions.
Quick-Disconnect Fittings
Quick-disconnect fittings allow for rapid connection and disconnection of hoses without the need for tools. This convenience is particularly valuable in applications requiring frequent hose changes, such as maintenance or equipment swaps. These fittings often incorporate a locking mechanism to ensure a secure connection while providing ease of use.
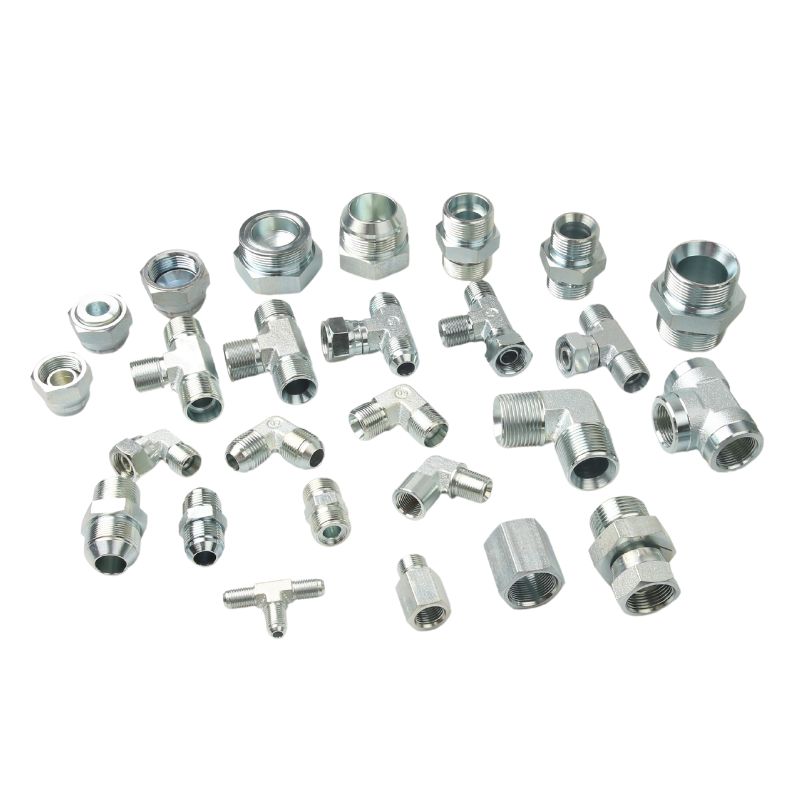
C. Key Characteristics of Connection Ports
Size and Compatibility
The size of hydraulic hose connection ports is a critical factor in ensuring compatibility within a hydraulic system. Ports must match the diameter and thread type of the hoses and fittings they connect to. Standardization in sizes, such as those outlined by SAE and ISO, helps manufacturers create compatible components, minimizing the risk of assembly errors.
Material Considerations
The materials used for hose connection ports greatly influence their durability and performance. Common materials include steel, stainless steel, brass, and plastic. Steel fittings offer high strength and resistance to corrosion, making them suitable for high-pressure applications. Stainless steel is often preferred in corrosive environments, while brass fittings provide good corrosion resistance and ease of installation. The choice of material must align with the specific requirements of the hydraulic system, including operating temperature and fluid type.
Pressure Ratings and Burst Strength
Each hydraulic connection port is rated for a specific pressure, which is the maximum operating pressure the fitting can withstand without failure. Understanding these pressure ratings is essential for ensuring safe operation, as exceeding these limits can lead to catastrophic failures. Additionally, burst strength indicates the maximum pressure a connection can handle before it ruptures. When selecting fittings, it’s crucial to consider the working pressure of the hydraulic system and choose ports that exceed this requirement to ensure a margin of safety.
The Science of Hose Connection Design
A. Engineering Principles Behind Connection Design
Fluid Dynamics Considerations
The design of hydraulic hose connections is fundamentally grounded in the principles of fluid dynamics. When pressurized fluid flows through a hose connection, it experiences various forces that can affect the performance of the entire system. The connection must minimize turbulence and pressure loss, which can be achieved through careful design of the internal geometry. Smooth transitions and properly sized ports help maintain a steady flow, reducing the risk of cavitation—where low pressure causes the formation of vapor bubbles, which can lead to damaging hydraulic hammer effects.
Stress and Strain Analysis
The structural integrity of hose connections is crucial, as they must withstand both internal pressures and external forces. Engineers use stress and strain analysis to evaluate how materials respond to these forces. When a hose connection is subjected to high pressure, it experiences tensile and shear stresses that can lead to deformation or failure if not properly accounted for in the design. Finite element analysis (FEA) is often employed to simulate how different designs will perform under various load conditions, allowing engineers to optimize the design for strength and durability.
B. The Role of Surface Finish and Geometry
The surface finish and geometry of hose connections play significant roles in their performance and reliability. A smooth surface finish reduces friction between the fluid and the walls of the connection, allowing for better flow characteristics and lower energy losses. Conversely, a rough surface can create turbulence, increasing the likelihood of cavitation and fluid erosion.
The geometry of the connection is equally important. Sharp bends or sudden changes in diameter can lead to significant pressure drops and turbulence. Engineers strive to create connections that have gentle curves and consistent diameters to promote smooth flow. Additionally, the shape of the connection must ensure proper alignment with hoses to prevent undue stress and potential failure.

C. Importance of Seal Integrity
Types of Seals (O-rings, Gaskets)
Seals are critical components in hydraulic hose connections, preventing fluid leaks that can compromise system performance and safety. The most common types of seals include O-rings and gaskets. O-rings are circular rubber or elastomeric seals that fit into grooves between mating surfaces. They provide a reliable seal under pressure and are widely used due to their simplicity and effectiveness. Gaskets, on the other hand, are flat materials that fill the space between two surfaces, providing a seal through compression. They are often used in flanged connections where the sealing surface area is larger.
Impact of Seal Failure
Seal integrity is paramount for the reliability of hydraulic systems. A failure in a seal can lead to fluid leaks, resulting in reduced system pressure and performance. In severe cases, seal failure can cause catastrophic equipment failure or safety hazards due to loss of hydraulic control. The causes of seal failure can vary, including improper installation, material degradation from exposure to hydraulic fluids, or excessive pressure and temperature conditions. Regular inspection and maintenance of seals are essential to identify signs of wear or damage before they lead to significant issues.
Standards and Regulations
A. Overview of Industry Standards (SAE, ISO)
Industry standards play a crucial role in the design, manufacture, and application of hydraulic hose connections. Two of the most widely recognized organizations that establish these standards are the Society of Automotive Engineers (SAE) and the International Organization for Standardization (ISO).
SAE Standards
SAE develops standards that focus on various aspects of automotive and hydraulic applications. Key SAE standards related to hydraulic hose connections include SAE J517, which outlines the specifications for hydraulic hoses, and SAE J514, which covers hydraulic tube fittings. These standards ensure compatibility and performance across different manufacturers and applications, fostering a level of reliability in hydraulic systems.
ISO Standards
ISO provides international standards that enhance compatibility and safety across various industries. ISO 8434, for example, specifies requirements for metallic tube fittings, including those used in hydraulic applications. Adherence to ISO standards helps manufacturers meet global market demands, ensuring their products are recognized and accepted internationally.
Both SAE and ISO standards address essential parameters such as material specifications, pressure ratings, and testing methods, providing a framework that manufacturers must follow to ensure their products meet industry expectations.
B. Importance of Adhering to Standards
Adhering to established standards is vital for several reasons:
Safety
Compliance with industry standards ensures that hydraulic hose connections can withstand the pressures and conditions they will face in operational environments. This minimizes the risk of failure, which can lead to dangerous accidents, fluid leaks, and equipment damage.
Interchangeability
Standards promote interchangeability among components from different manufacturers. This is crucial in hydraulic systems, where various parts must work together seamlessly. Standardized dimensions and specifications allow for easy replacement and maintenance without the need for custom components.
Quality Assurance
Following established standards is often synonymous with higher quality. Manufacturers that adhere to these standards are more likely to implement rigorous testing and quality control measures, resulting in reliable and durable products. This commitment to quality enhances customer trust and satisfaction.
Regulatory Compliance
Many industries are subject to regulatory requirements that mandate compliance with specific standards. Adhering to these standards helps organizations meet legal obligations, reducing the risk of penalties and ensuring smooth operations.
C. How Standards Affect Design and Safety
The impact of standards on the design and safety of hydraulic hose connections is profound:
Design Specifications
Standards provide detailed design specifications that guide engineers in developing components that meet performance and safety criteria. These specifications include dimensional tolerances, material requirements, and performance testing protocols. By adhering to these guidelines, manufacturers can produce reliable products that meet the demands of their intended applications.
Testing and Certification
Standards outline testing methods that components must undergo to verify their performance and safety. For instance, pressure testing ensures that hose connections can handle specified pressures without failure. Certification processes based on standards give users confidence that products will perform as intended, promoting safety in hydraulic systems.
Continuous Improvement
Industry standards are not static; they evolve over time to incorporate new technologies, materials, and knowledge gained from research and field experience. This adaptability encourages continuous improvement in design and manufacturing practices, leading to safer and more efficient hydraulic systems.
Market Access
Compliance with recognized standards can also facilitate market access for manufacturers. Many industries prefer or require suppliers to meet specific standards, and adhering to these can enhance a company’s reputation and competitiveness in the market.
Best Practices for Hose Connection Installation
A. Tools and Equipment Needed for Installation
Proper installation of hydraulic hose connections requires a set of specialized tools and equipment to ensure reliability and safety. Below are the essential tools commonly used in the installation process:
Wrenches: Adjustable wrenches and torque wrenches are vital for tightening fittings without damaging them. A torque wrench is especially important to apply the correct amount of force to prevent leaks and ensure the integrity of the connection.
Cutting Tools: Hose cutting tools, such as hose cutters or utility knives, are necessary for making clean cuts in hydraulic hoses. Clean cuts are crucial to maintaining the integrity of the hose and ensuring a proper fit with the fittings.
Deburring Tools: After cutting, using deburring tools helps smooth the edges of the hose and fittings, preventing damage to seals and ensuring a secure connection.
Hose Clamps: These are used to secure hoses to fittings and prevent leakage. Ensure that the right size and type of clamp are chosen for the application.
Cleaning Supplies: Before installation, it’s essential to clean the fittings and hoses to remove any debris, dust, or contaminants that could affect the seal. Lint-free cloths and cleaning solvents are often used for this purpose.
Safety Gear: Always wear appropriate safety gear, including gloves and eye protection, to prevent injuries during installation.

B. Step-by-Step Installation Guide
Preparing the Hose and Fittings
Inspection: Before installation, inspect the hose and fittings for any signs of damage, wear, or defects. Ensure that the components are compatible in size and pressure ratings.
Cutting the Hose: If necessary, cut the hose to the desired length using a hose cutter. Ensure the cut is straight and clean to facilitate a proper seal.
Deburring: Use a deburring tool to remove any sharp edges from the cut end of the hose, ensuring a smooth surface that will help prevent leaks.
Proper Torque Specifications
Assembly: Begin assembling the hose and fitting. Insert the hose end into the fitting until it is fully seated.
Tightening: Using a torque wrench, tighten the fitting to the manufacturer’s recommended torque specifications. It’s essential to avoid overtightening, which can damage the fitting or hose and lead to premature failure.
Final Check: After tightening, perform a visual inspection to ensure that the fitting is correctly aligned and seated.
Testing the Connection
Once installed, test the hose connection by gradually increasing the pressure in the system. Monitor for any signs of leaks or failures during this initial pressurization. If leaks are detected, release the pressure and check the fittings and seals.
C. Common Mistakes to Avoid During Installation
Inadequate Preparation: Failing to properly clean and prepare the hose and fittings before installation can lead to contamination and leaks. Always ensure that all components are free from dirt and debris.
Incorrect Torque Application: Over or under-tightening connections is a frequent error that can compromise the integrity of the hose connection. Always refer to the manufacturer’s torque specifications and use a torque wrench for accuracy.
Neglecting Seal Integrity: Ignoring the condition of seals or using the wrong type can result in leaks. Always inspect seals for wear and ensure they are appropriate for the specific application.
Improper Hose Routing: When installing hoses, avoid sharp bends or kinks, which can restrict flow and increase stress on the hose. Follow best practices for routing hoses to ensure optimal performance.
Using Incompatible Components: Mixing components from different manufacturers without checking compatibility can lead to failures. Always ensure that hoses, fittings, and connectors are compatible in size and specifications.
Ignoring Manufacturer Guidelines: Each hydraulic system may have specific requirements based on the application and components used. Ignoring these guidelines can lead to improper installation and potential system failures.
Failing to Conduct a Final Inspection: After installation, it’s crucial to conduct a thorough inspection of all connections. Skipping this step can lead to undetected leaks and failures in the hydraulic system.
Troubleshooting Common Issues
A. Identifying Leaks in Hose Connections
Leaks in hydraulic hose connections can lead to significant performance issues and safety hazards. Identifying these leaks promptly is crucial for maintaining the integrity of the hydraulic system. Here are key steps to detect leaks effectively:
Visual Inspection: Start with a thorough visual inspection of all hose connections and fittings. Look for signs of fluid accumulation around connection points, as well as wet spots or puddles beneath the hoses. Pay close attention to joints, as these are common areas for leaks to occur.
Pressure Testing: If a leak is suspected but not visible, conducting a pressure test can help. Increase the pressure in the system gradually and monitor the connection points for any signs of escaping fluid. Using a pressure gauge can help ensure that you do not exceed the safe operating pressure.
Use of Leak Detection Fluid: Applying a leak detection fluid (often a soapy solution) to the suspected areas can help identify leaks. Bubbles will form at the site of a leak, making it easier to pinpoint the issue.
Listen for Unusual Sounds: Sometimes, leaks can be identified by the sound of escaping air or fluid. Listening carefully to the system under pressure can help you locate problematic connections.
B. Performance Issues Related to Connection Ports
In addition to leaks, connection ports can lead to various performance issues that impact the efficiency of hydraulic systems:
Pressure Drop: A significant drop in pressure at the connection ports can indicate blockages or improperly sized fittings. This can cause a reduction in system efficiency and power output. Regularly monitoring pressure readings at various points can help identify problematic areas.
Turbulence and Cavitation: Poorly designed connection ports or sharp bends in hoses can lead to turbulence, increasing the likelihood of cavitation. This phenomenon can cause damage to components and reduce the overall performance of the hydraulic system.
Overheating: Excessive heat can be a sign of fluid restrictions at connection ports. Overheating can lead to fluid breakdown and damage to hydraulic components. Monitoring fluid temperatures can help detect issues early.
Wear and Tear: Frequent connections and disconnections can lead to wear on fittings and hoses, resulting in performance degradation. Inspecting connections for signs of wear, such as nicks or scratches, can prevent further issues.
C. Solutions and Corrective Actions
Once issues have been identified, appropriate solutions and corrective actions can be implemented:
Addressing Leaks:
Tightening Connections: If a leak is found, start by tightening the connection to the manufacturer’s specified torque settings. Use a torque wrench to ensure the right amount of force is applied.
Replacing Seals: If tightening does not resolve the leak, inspect seals (O-rings and gaskets) for damage. Replace any worn or damaged seals to restore integrity.
Resolving Pressure Drops:
Check Hose Sizing: Ensure that hoses and fittings are appropriately sized for the system’s flow requirements. If undersized, consider replacing them with larger components to reduce pressure drops.
Clear Blockages: Inspect for debris or obstructions in the hoses and ports. If blockages are found, clean or replace the affected components.
Minimizing Turbulence and Cavitation:
Redesigning Connections: If turbulence is identified, consider redesigning the hose layout to incorporate smoother transitions and avoid sharp bends. Use fittings that minimize flow restrictions.
Using Anti-Cavitation Devices: In high-risk applications, installing anti-cavitation devices can help mitigate the effects of cavitation.
Preventing Overheating:
Fluid Management: Regularly check fluid levels and quality. Ensure that the hydraulic fluid is suitable for the operating temperature and conditions. Consider using cooling systems if overheating is persistent.
Routine Maintenance: Implement a routine maintenance schedule to inspect and replace worn components, helping to prevent overheating due to excessive wear.
Addressing Wear and Tear:
Regular Inspections: Schedule regular inspections of hose connections and ports to catch signs of wear early. This proactive approach can prevent larger issues from developing.
Training: Train personnel on proper installation techniques and handling of hydraulic components to minimize wear from misuse or improper connections.
Conclusion
We encourage all professionals involved in hydraulic applications to commit to ongoing education and improvement. By prioritizing proper installation, regular maintenance, and adherence to industry standards, we can ensure the reliability and effectiveness of hydraulic systems for years to come.
FAQ
What are hydraulic connection ports?
Hydraulic connection ports are fittings that connect hoses to hydraulic systems, allowing for the transfer of fluid under pressure.
What types of hydraulic connection ports exist?
Common types include male and female connectors, threaded ports (NPT, BSP), flange connections, and quick-disconnect fittings.
How do I identify a leak in a hydraulic hose connection?
Look for fluid accumulation around connections, listen for hissing sounds, or use a leak detection fluid that bubbles at the leak site.
What tools are needed for installing hydraulic hose connections?
Essential tools include wrenches, hose cutters, deburring tools, hose clamps, and cleaning supplies.
What are common mistakes to avoid during installation?
Avoid inadequate preparation, incorrect torque application, neglecting seal integrity, and using incompatible components.
Why are industry standards important for hydraulic hose connections?
Standards ensure safety, compatibility, quality assurance, and regulatory compliance, helping maintain the integrity of hydraulic systems.