Hydraulic hoses play a crucial role in a variety of industrial applications, from construction and agriculture to automotive and manufacturing. These flexible conduits are essential for transferring hydraulic fluids under high pressure, enabling machinery to function effectively and efficiently.
Understanding Hydraulic Hose Structure
Hydraulic hoses are integral to the efficiency and safety of hydraulic systems. Understanding their structure is essential for appreciating how innovations can lead to lighter yet equally strong designs.
A. Components of Hydraulic Hose
Inner Tube The inner tube is the primary component of a hydraulic hose, responsible for carrying the hydraulic fluid. Typically made from materials that resist oil and temperature variations, the inner tube is designed to withstand high pressures. It must be impermeable to prevent leakage and maintain fluid integrity.
Reinforcement Layers
Surrounding the inner tube are reinforcement layers, which provide the hose with its strength and structural integrity. These layers can consist of various materials, including:
Steel Wire Braids: Often used for high-pressure applications, these braids increase the hose’s ability to handle extreme pressures without bursting.
Textile Braids: Lighter than steel, textile braids offer flexibility and can be used in lower-pressure applications.
Spiral Wound Wire: This construction method involves spiraling steel wire around the hose, providing superior strength for high-pressure systems while maintaining flexibility.
Outer Cover
The outer cover serves as the protective layer of the hose, shielding it from environmental hazards such as abrasion, chemicals, and UV exposure. Made from durable materials like synthetic rubber or thermoplastics, the outer cover is crucial for extending the hose’s lifespan and ensuring safe operation.
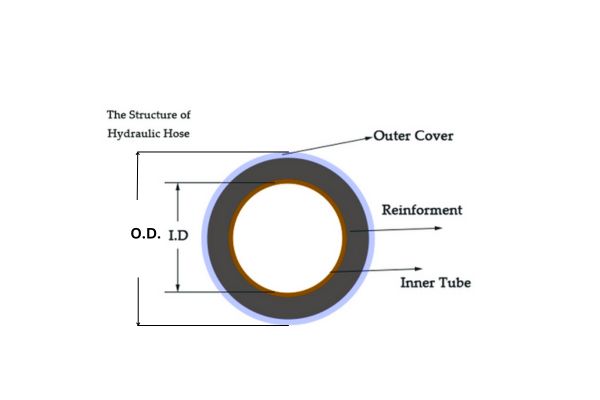
B. Common Materials Used in Hose Construction
The selection of materials for hydraulic hose construction is pivotal in determining performance characteristics. Common materials include:
Rubber: Natural or synthetic rubber is frequently used for the inner tube and outer cover due to its flexibility, resistance to wear, and ability to withstand a range of temperatures and pressures.
Thermoplastics: These materials are often utilized for their lightweight properties and chemical resistance. They can be engineered to enhance flexibility and reduce weight.
Steel Wire: Used in reinforcement layers, steel wire provides exceptional tensile strength and durability, making it suitable for high-pressure applications.
Composite Materials: Emerging technologies are introducing composite materials that combine the benefits of various substances, offering improved strength-to-weight ratios.
C. The Role of Reinforcement in Maintaining Strength
Reinforcement is critical in maintaining the strength and functionality of hydraulic hose. The primary functions of the reinforcement layers include:
Pressure Resistance: Reinforcement layers absorb and distribute pressure throughout the hose, preventing deformation or failure under extreme conditions. The specific design and material of the reinforcement determine the hose’s maximum operating pressure.
Flexibility: While providing strength, reinforcement must also allow for flexibility. This balance is essential, especially in applications where hoses need to bend or maneuver around obstacles. Innovative reinforcement designs are being explored to enhance flexibility while maintaining strength.
Durability: The reinforcement contributes to the overall durability of the hose, protecting it from external forces, abrasions, and environmental factors. A well-engineered hose will resist wear and tear, extending its operational lifespan.
The Case for Lighter Hoses
The pursuit of lighter hydraulic hose has garnered significant attention in recent years, driven by the need for enhanced performance and efficiency across various industries. By exploring the benefits of reducing hose weight, we can understand the compelling case for innovation in hose design.
A. Benefits of Reducing Hose Weight
Improved Handling and Installation
Lighter hoses are considerably easier to handle during installation and maintenance. Workers can maneuver them with greater ease, reducing the physical strain associated with heavy hoses. This ease of handling not only enhances safety during installation but also minimizes the risk of damage to both the hoses and the machinery they connect to. Moreover, the simplified installation process can lead to quicker turnaround times, enhancing overall productivity.
Increased Flexibility in Tight Spaces
Hydraulic systems are often constrained by space limitations, particularly in compact machinery or equipment. Lighter hoses typically offer greater flexibility, allowing them to bend and adapt to tight corners without kinking or compromising performance. This adaptability is particularly valuable in applications where space is at a premium, enabling engineers to design more compact and efficient systems without the worry of hose failure.
Potential for Cost Savings in Transportation
The weight of hoses directly impacts transportation costs, especially in industries where hoses are shipped in large quantities. Lighter hoses can significantly reduce shipping weights, leading to lower freight costs and reduced carbon footprints. Additionally, reduced weight means that companies can optimize their logistics, transporting more hoses in a single shipment without exceeding weight limits. This efficiency not only saves money but also supports sustainability initiatives, making lighter hoses a more environmentally friendly option.
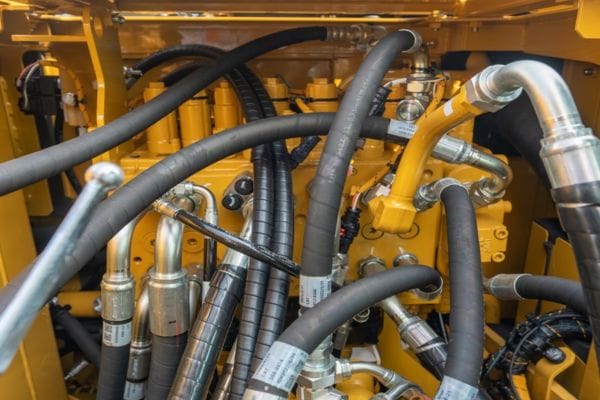
B. Examples of Industries Benefiting from Lighter Hoses
Agriculture In the agricultural sector, lighter hoses can improve the efficiency of machinery such as tractors and harvesters. These machines often operate in varied terrains and conditions, making flexibility crucial. Lighter hoses reduce the overall weight of equipment, allowing for better fuel efficiency and maneuverability in the field. This is particularly beneficial during planting and harvesting seasons when time and efficiency are critical.
Construction
The construction industry relies heavily on hydraulic equipment, such as excavators and bulldozers. Lighter hoses enable these machines to operate more effectively, enhancing their performance and reducing wear on components. The ability to handle hoses easily on construction sites also minimizes downtime, ensuring that projects stay on schedule.
Automotive
In the automotive industry, particularly in the production of lighter vehicles, the reduction of hose weight is essential. Hoses are integral to systems such as power steering and brake systems. By utilizing lighter hoses, manufacturers can contribute to the overall weight reduction of vehicles, which improves fuel efficiency and performance. Additionally, lighter hoses facilitate the design of more compact engine layouts, further optimizing vehicle design.
Aerospace
The aerospace industry has long been at the forefront of material innovation, where every gram counts. Lightweight hoses contribute to the overall weight reduction of aircraft, enhancing fuel efficiency and payload capacity. The flexibility of lighter hoses also allows for easier integration into complex systems, such as landing gear and hydraulic control systems.
Marine
In marine applications, lighter hoses are advantageous for both performance and fuel efficiency. Vessels equipped with lighter hoses can achieve better handling and reduce the overall weight of the ship, which is critical for performance in various marine environments.
Current Design Practices and Their Limitations
A. Overview of Traditional Reinforcement Methods
Traditional hydraulic hose design typically relies on several reinforcement methods to ensure strength and reliability. The primary reinforcement strategies include:
Braided Reinforcement:
Steel Wire Braids: This method involves weaving steel wires around the inner tube, forming a braid that provides high tensile strength. These hoses are commonly used in high-pressure applications, offering significant resistance to bursting. However, while steel braids are effective, they can add considerable weight and reduce flexibility.
Spiral Reinforcement:
Spiral Wound Wire: In this approach, steel wire is wound in a spiral pattern around the inner tube. Spiral hoses are known for their ability to withstand high pressures while maintaining flexibility. The design allows for a more uniform distribution of stress throughout the hose, but like braided reinforcement, it can contribute to added weight.
Textile Reinforcement:
Textile fibers, such as polyester or nylon, are used for lighter-duty hoses. This method offers flexibility and is often used in lower-pressure applications. While textile reinforcements reduce weight, they may not provide the same level of pressure resistance as metal reinforcements.
Combination Reinforcement:
Many modern hoses utilize a combination of braided and spiral reinforcements to balance strength and flexibility. While this hybrid approach can optimize performance, it often results in increased weight and complexity.
B. Analysis of Mean Diameter vs. Fitting Nipple Diameter
A critical aspect of hydraulic hose design is the relationship between mean diameter and fitting nipple diameter. Traditionally, engineers have focused on mean diameter as the standard measurement for hose performance. However, this approach has limitations:
Mean Diameter Considerations:
Mean diameter refers to the average diameter of the hose, which influences its pressure rating and flow characteristics. Designing hoses around this metric can lead to overengineering, where hoses are made thicker and heavier to meet pressure requirements that may not be necessary for all applications.
Fitting Nipple Diameter as a Design Metric:
Recent analyses suggest that designing hoses based on the fitting nipple diameter—specifically the size of the end fittings—may provide a more accurate reflection of the hose’s operational environment. By aligning the hose’s design more closely with the dimensions of the fittings, engineers can potentially reduce the amount of reinforcement needed, leading to lighter hoses without compromising safety or performance.
Implications for Efficiency:
This shift in focus from mean diameter to fitting nipple diameter could allow for the creation of hoses that are tailored to specific applications, optimizing performance while minimizing weight. It encourages a more application-specific approach rather than a one-size-fits-all methodology, fostering innovation in hose design.
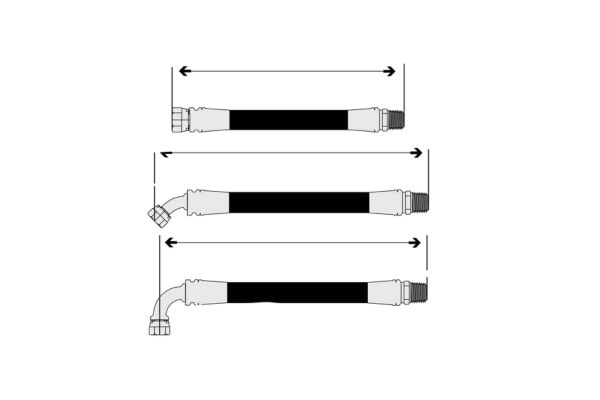
C. Limitations of Overengineering and the Implications on Performance
While the intent behind traditional hose design practices is to ensure safety and durability, overengineering poses significant drawbacks:
Increased Weight:
Overengineering often results in unnecessarily heavy hoses. The added weight can hinder the performance of machinery, especially in applications where flexibility and ease of handling are paramount. In industries such as agriculture and construction, where mobility is key, excessive weight can lead to inefficiencies and increased operational costs.
Reduced Flexibility:
Hoses designed with excessive reinforcement can become rigid and difficult to maneuver, particularly in confined spaces. This lack of flexibility can lead to kinking, twisting, or even premature failure, undermining the hose’s intended performance. Operators may struggle with installation and maintenance, resulting in downtime and potential safety hazards.
Higher Costs:
The complexity of overengineered hoses can also lead to higher manufacturing costs. These costs are often passed down to the end users, making hydraulic systems more expensive to produce and maintain. In a competitive market, this can deter companies from investing in the latest technologies and innovations.
Sustainability Concerns:
Overengineering also raises sustainability issues. Heavier hoses require more energy for transportation, contributing to a larger carbon footprint. Reducing weight through optimized design practices can lead to a more sustainable approach, aligning with the growing emphasis on environmental responsibility in manufacturing.
Innovative Approaches to Hose Design
A. Alternative Materials and Their Properties
Composite Materials
Composite materials combine two or more constituent materials with different physical or chemical properties. This results in a material that exhibits enhanced characteristics compared to its components. In hoses, composites can offer several advantages:
Weight Reduction: Composite materials are often significantly lighter than traditional rubber or metal reinforcements. This weight reduction enhances the overall efficiency of hydraulic systems.
High Strength-to-Weight Ratio: Many composites provide excellent strength without adding excessive weight. For example, carbon fiber composites are known for their incredible strength while remaining lightweight, making them ideal for high-performance applications.
Corrosion Resistance: Composites can be engineered to resist corrosion and chemical degradation, extending the lifespan of hoses used in harsh environments.
Advanced Polymers
Advanced polymers, including thermoplastic elastomers (TPEs) and polyurethanes, are increasingly being used in hydraulic hose construction. These materials provide several benefits:
Flexibility and Resilience: Advanced polymers offer superior flexibility, making them easier to handle and install. They can bend without kinking, ensuring reliable performance even in tight spaces.
Enhanced Durability: Many modern polymers are engineered to withstand extreme temperatures, pressures, and environmental conditions. This durability reduces the likelihood of failure and extends the service life of the hoses.
Weight Efficiency: Compared to traditional rubber materials, advanced polymers can be formulated to achieve lower weight while maintaining necessary strength, contributing to overall system efficiency.
B. New Reinforcement Techniques
Reinforcement Based on Fitting Nipple Diameter
As discussed previously, a shift toward designing hoses based on fitting nipple diameter instead of mean diameter represents a significant innovation in hose design. This technique involves:
Tailored Reinforcement: By aligning the hose’s reinforcement design with the fitting dimensions, engineers can create hoses that are optimized for specific applications. This alignment allows for reduced material usage without compromising safety.
Enhanced Performance: This approach can lead to improved flow characteristics, as hoses can be designed with optimal cross-sectional areas that correspond to the fittings. This optimization enhances the overall efficiency of hydraulic systems, reducing energy loss and improving performance.
Weight Reduction: With less material required for reinforcement, the hoses become lighter, enhancing handling and installation processes.
Hybrid Designs
Hybrid designs represent another innovative approach to hose reinforcement. These designs incorporate multiple materials and reinforcement methods to achieve an optimal balance between strength, flexibility, and weight. Key features include:
Combination of Reinforcement Types: A hybrid hose might use a combination of braided metal and textile fibers, leveraging the strengths of both materials. This method can provide the high-pressure resistance of metal while maintaining the flexibility of textiles.
Layered Construction: Hybrid designs can utilize a layered approach, where different materials are strategically placed within the hose structure. For example, a lightweight polymer might be used for the inner layer, while a stronger material is employed for the outer layer. This layering can optimize performance under varying conditions.
Application-Specific Solutions: Hybrid hoses can be tailored to specific industry needs, allowing for customization that meets unique performance criteria. For instance, hoses designed for aerospace applications may prioritize weight reduction and flexibility, while those for construction may focus on durability and pressure resistance.
Safety Considerations
As the hydraulic hose industry moves toward lighter and more innovative designs, ensuring safety remains paramount. The reduction of weight must not compromise the hoses’ ability to perform reliably under pressure.
A. Ensuring Safety While Reducing Weight
Material Selection: The choice of materials is critical in ensuring safety while reducing hose weight. Advanced polymers and composite materials can offer significant weight savings without sacrificing strength. However, engineers must ensure that these materials meet or exceed the required pressure ratings and resistance to environmental factors. Thorough testing and validation of new materials are essential to confirm their performance in real-world applications.
Reinforcement Strategies: When adopting new reinforcement techniques, such as those based on fitting nipple diameters or hybrid designs, it is essential to maintain adequate pressure resistance and flexibility. Engineers should analyze the stress distribution within the hose to prevent failure points. This analysis can help identify optimal reinforcement patterns that provide safety while reducing weight.
Design Optimization: Incorporating design optimization tools, such as finite element analysis (FEA), can enhance safety in lightweight hose designs. These tools allow engineers to simulate various stress scenarios, ensuring that the hose can withstand operational demands without compromising safety. By identifying potential weaknesses in the design early in the development process, manufacturers can make informed adjustments to enhance safety.
B. Testing Standards and Regulations
Industry Standards: Hoses are subject to various industry standards and regulations that govern their performance and safety. Organizations such as the International Organization for Standardization (ISO) and the Society of Automotive Engineers (SAE) set guidelines that manufacturers must adhere to. These standards typically cover aspects such as pressure ratings, burst strength, and environmental resistance.
Testing Procedures: Rigorous testing procedures are essential to ensure that hoses meet established safety standards. Common tests include:
Burst Testing: This test evaluates the maximum pressure a hose can withstand before failure, ensuring that it can operate safely within specified limits.
Impulse Testing: This assesses the hose’s durability under repeated pressure cycles, simulating real-world conditions to identify potential fatigue points.
Environmental Testing: Hoses must be evaluated for resistance to chemicals, temperature fluctuations, and UV exposure to ensure they can perform safely in various environments.
Certification Processes: Obtaining certification from relevant regulatory bodies can enhance customer confidence in the safety and reliability of hoses. Certification processes typically involve comprehensive testing and validation of materials, design, and manufacturing practices. By achieving certification, manufacturers demonstrate their commitment to safety and quality.
C. Risk Management in Hose Design
Identifying Risks: Risk management begins with identifying potential hazards associated with hoses. This includes understanding the operational environment, potential pressure fluctuations, and the effects of temperature and chemical exposure. A thorough risk assessment allows engineers to anticipate failure modes and develop strategies to mitigate these risks.
Design Reviews and Quality Control: Implementing design reviews and quality control processes throughout the manufacturing cycle is vital for risk management. Regular inspections, both during production and after completion, help ensure that hoses meet safety and performance standards. Quality control measures should include verification of materials, reinforcement methods, and compliance with testing protocols.
Conclusion
Ultimately, the hydraulic hose industry stands at the forefront of innovation, poised to meet the challenges of modern applications while prioritizing safety and sustainability. By embracing these changes, the industry can pave the way for a new era of hydraulic solutions that enhance performance, reduce environmental impact, and improve overall functionality.
FAQ
What are hoses made of?
Hydraulic hoses are typically made from rubber, thermoplastic, or composite materials, often reinforced with layers of steel or textile to provide strength and flexibility.
How do I know if a hydraulic hose is the right size?
To ensure the correct size, measure the inner diameter and the overall length required for your application, and match it to the specifications of the hydraulic fittings used.
What is the typical lifespan of a hydraulic hose?
The lifespan of a hydraulic hose varies based on usage, environment, and maintenance, but it generally lasts between 5 to 10 years with proper care.
What are the signs that a hydraulic hose needs to be replaced?
Look for signs of wear such as cracks, bulges, leaks, or severe abrasions. Any noticeable changes in performance, like reduced pressure, can also indicate the need for replacement.
Can I use a hydraulic hose in extreme temperatures?
Yes, but it is essential to choose hoses specifically designed for extreme temperatures. Check the manufacturer’s specifications for temperature ratings to ensure safe operation.
How can I maintain hoses to prolong their life?
Regularly inspect hoses for signs of wear, keep them clean, avoid sharp bends or kinks, and ensure they are properly secured to prevent movement and abrasion.