Temperature is one of the most critical factors affecting the performance and longevity of ball valves. When fluid temperatures exceed the valve’s rated operating limits, overheating can occur, leading to significant damage and reduced efficiency.
Understanding Overheating Affects Ball Valves
What is Overheating?
Overheating in ball valves refers to the condition where the internal temperature of the valve exceeds the maximum design or operational temperature limits specified by the manufacturer. Each valve is rated to function optimally within a certain temperature range, often expressed as a minimum and maximum temperature threshold. When these thresholds are surpassed, the valve’s performance can degrade, leading to potential failure and system inefficiencies.
Ball valves typically handle temperatures ranging from -20°F to 400°F (-29°C to 204°C), depending on the materials used for construction and sealing. However, extreme conditions, such as steam, hot gases, or aggressive chemicals, can elevate the valve’s internal temperature, pushing it beyond the safe operating limits. This is especially problematic in industries like oil and gas, chemical processing, and HVAC, where high-pressure and high-temperature environments are common.
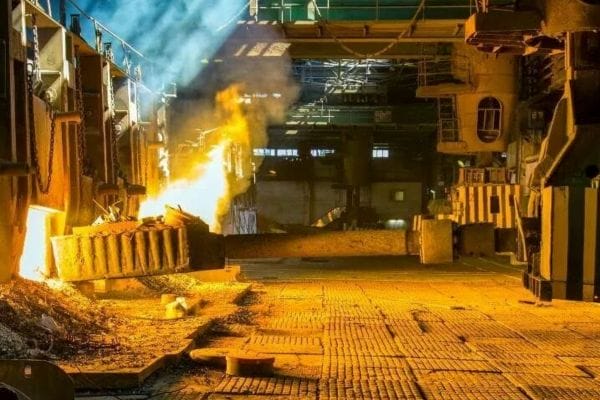
Causes of Excessive Heat in Fluid Systems
High Fluid Temperature: The most direct cause of overheating is when the fluid passing through the valve is too hot. This can result from high-pressure steam, overheated chemicals, or other hot substances in the pipeline.
Improper System Settings: Incorrect system configurations, such as misadjusted pressure or temperature controls, can cause the valve to experience heat levels it wasn’t designed to handle.
Lack of Cooling Mechanisms: In some systems, the valve may be exposed to excess heat due to the absence of cooling mechanisms like temperature regulators or heat exchangers.
Environmental Factors: External factors, such as high ambient temperatures or poor heat dissipation, can exacerbate overheating, especially in outdoor installations where direct sunlight or nearby heat sources increase the temperature around the valve.
Types of Ball Valves Affected by Overheating
Ball valves come in various types, including manual, pneumatically actuated, and electrically actuated valves. Each type is susceptible to overheating in different ways, depending on its construction and method of operation.
Manual Ball Valves: These valves are operated by turning a handle or lever. They may not be as vulnerable to overheating as actuated valves since they don’t rely on motors or air pressure systems. However, excessive heat can still warp the valve body or damage seals, particularly if the valve is in contact with hot fluids for extended periods. Manual valves are more susceptible to operator difficulty when temperatures rise, as the handle mechanism may become stiff or difficult to turn if the valve body expands due to heat.
Pneumatically Actuated Ball Valves: These valves use compressed air to operate. Overheating can affect both the valve body and the actuator. Excessive heat may damage the seals or gaskets in the actuator, leading to loss of air pressure and failure to operate the valve properly. Overheated air can also cause the pneumatic actuator to become sluggish or unresponsive, impairing the valve’s opening and closing actions.
Electrically Actuated Ball Valves: These valves rely on an electric motor or solenoid for operation. Overheating in electrically actuated valves can be particularly damaging, as the motor or electrical components may overheat and burn out. If the valve body also experiences excessive heat, the plastic or rubber seals could degrade, and the valve’s operation could become erratic or cease altogether.
Consequences of Overheating
When a ball valve experiences overheating, several negative consequences can affect the valve’s functionality and lead to costly repairs or operational disruptions. These impacts can be categorized into damage to valve components, loss of sealing ability, and mechanical failure:
Impact on Seals, Gaskets, and Valve Components: Ball valves typically rely on various sealing materials (such as O-rings, PTFE gaskets, or elastomers) to maintain a tight seal when in operation. Overheating can cause these seals to lose their elasticity, become brittle, or melt. As a result, the valve may develop leaks, allowing fluid to escape or enter areas where it shouldn’t. This can not only affect the performance of the valve but also compromise the entire system’s integrity. Gaskets may warp or crack, further exacerbating the leakage problem.
Structural and Mechanical Damage to Valve Body and Internal Components: Overheating causes the valve body to expand and contract, which can lead to mechanical stresses. Repeated thermal cycling (heating and cooling) can cause material fatigue, leading to cracks or warping in the valve body itself. Additionally, the ball inside the valve may experience thermal expansion, which could cause it to seize or make it difficult for the valve to open or close properly. This damage often results in the valve becoming stuck, reducing the efficiency and safety of the system.
Loss of Sealing Effectiveness and Leaks: As overheating degrades the valve’s sealing components and internal parts, the most immediate consequence is a loss of sealing integrity. The valve may no longer function as a reliable shut-off mechanism, leading to leaks that can not only damage the system but also pose significant safety hazards, especially in systems handling hazardous chemicals or high-pressure fluids. The ability of the valve to maintain a tight seal under pressure and temperature fluctuations is critical, and overheating compromises this capability.
System Shutdown and Downtime: In extreme cases, the internal components of the ball valve may fail, causing a system shutdown or unplanned downtime. For example, if the valve cannot close properly due to overheating, it may lead to uncontrolled flow, increased pressure, and potential damage to other system components. This could result in costly downtime, emergency repairs, and potentially even catastrophic failures depending on the nature of the system.
Signs and Symptoms of Overheating in Ball Valves
Physical Signs of Overheating
One of the first indications of overheating in a ball valve is often visible damage to the valve body and its components. Here are some common physical cues to look out for:
Discolored Valve Bodies: Excessive heat can cause a ball valve’s outer body or internal components to change color, often appearing darker or more brittle than usual. This discoloration is a clear sign that the material has been exposed to heat beyond its operating limits. Steel or brass valve bodies may show signs of oxidation or a rust-like appearance, especially if exposed to elevated temperatures for extended periods.
Damaged Seals and Gaskets: The high temperatures associated with overheating can cause the rubber or elastomer seals within the valve to degrade. Overheated seals may crack, warp, or become brittle, leading to compromised sealing capabilities. You might notice visible damage, such as cracks around the stem or flange areas, which can cause leaks and loss of sealing effectiveness.
Cracked or Warped Parts: Overheating can cause internal components such as the valve ball, stem, or actuator housing to warp or crack. If the valve is subjected to frequent temperature extremes, the expansion and contraction of materials can lead to permanent structural damage. Look for physical distortions or signs of cracking, particularly on metal parts.
Performance Indicators
In addition to visual cues, performance-related indicators are often the first signs of overheating during regular valve operation. These symptoms can impact the efficiency and reliability of the valve, signaling that the valve is under stress and may soon fail if not addressed.
Reduced Valve Response or Difficulty in Opening/Closing: One of the most common symptoms of an overheated ball valve is a sluggish or stiff response when attempting to open or close the valve. High temperatures can cause the valve ball to expand, making it difficult for the actuator to rotate the ball or causing friction that slows down the valve’s operation. If you notice the valve becoming harder to turn or the actuator responding slowly, it could be due to overheating.
Leaking at the Valve Stem or Body: Overheating can lead to seals losing their integrity. If you observe leaks at the valve stem or body, it might be due to thermal expansion or seal degradation caused by excessive heat. Even slight leaks can escalate over time, causing further damage to the valve and surrounding equipment. Leaking fluid, especially if it’s hazardous or pressurized, is a major safety concern and should be addressed immediately.
Excessive Wear on Moving Parts (Ball, Actuator): Prolonged exposure to high temperatures can cause excessive wear and tear on moving parts, particularly the valve ball, actuator, and the stem. The ball inside the valve may become worn down due to thermal expansion, friction, or the degradation of lubricant, leading to rough movement or sticking. This wear can result in the valve not functioning as effectively or leading to a complete failure over time.
Audible Signs
Overheating in ball valves can sometimes cause unusual noises, which are not typical in normal operations. These sounds may indicate that components inside the valve are under stress or experiencing friction due to temperature-induced changes.
Unusual Noises from the Valve Actuator: If you hear whining, grinding, or screeching sounds from the valve actuator or other moving parts, this could be a sign that the valve is overheating. These noises may indicate excessive friction due to the expansion of internal components, such as the valve ball or actuator piston. Such sounds are often associated with inadequate lubrication, which can occur when the temperature exceeds the design limits of the valve and breaks down lubricants.
Valve Movement Sounds: You may also hear sounds that suggest the valve ball is having trouble moving freely. A “sticking” ball, which is unable to rotate smoothly due to thermal expansion, can make grinding or clunking noises as it tries to move through the valve body. Over time, this friction can cause additional damage to internal surfaces, leading to further wear and tear.
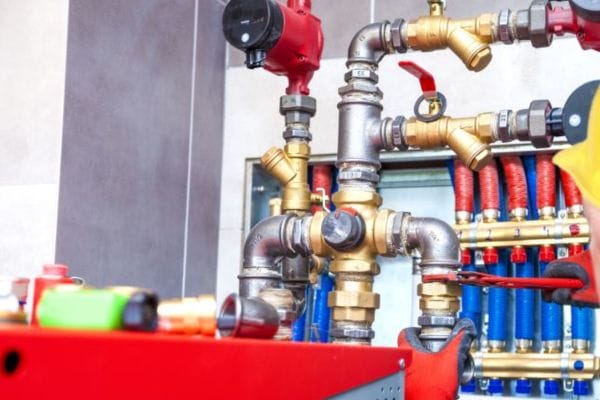
Pressure and Temperature Readings
Another effective method to detect overheating in ball valves is to monitor the system’s pressure and temperature readings. Abnormal pressure or temperature readings may be indicative of a valve failure due to excessive heat.
Abnormal Temperature Readings: Temperature gauges or sensors attached to the ball valve or pipeline can provide direct indications of overheating. If you notice that the temperature in the valve or nearby pipeline is consistently higher than the operational range specified by the manufacturer, this could signal that the valve is being subjected to temperatures that exceed its rated limits. A sudden spike in temperature can also be a precursor to valve failure if the system doesn’t have mechanisms in place to regulate it.
Pressure Fluctuations: Excessive heat can cause pressure to fluctuate, especially if the fluid inside the valve expands due to high temperature. If you notice erratic or inconsistent pressure readings, it may indicate that the ball valve is struggling to manage the flow or seal properly due to the heat. Overheating can lead to a drop in pressure or unsteady pressure control as seals fail and the valve is unable to function as intended.
Troubleshooting Overheating Problems in Ball Valves
Step-by-Step Troubleshooting Guide for Overheating
Check Temperature Readings:
The first step is to verify the temperature levels within the system. Use temperature gauges or sensors to check whether the ball valve is operating within the manufacturer’s specified range. A temperature reading higher than the recommended threshold is a clear indicator of overheating.
Inspect Valve Body for Discoloration or Damage:
Visually inspect the valve body, seals, and gaskets for signs of discoloration, cracking, or warping. Overheated valves often show physical signs of thermal stress, such as darkened surfaces or damaged seals. Cracks or deformities in the valve body may indicate that the valve has been exposed to excessive heat for too long.
Listen for Unusual Noises:
Overheating often causes unusual operational sounds, such as grinding or squealing. If you hear strange noises when the valve is in operation, it could indicate that the valve ball or actuator components are experiencing excessive friction due to thermal expansion. This is often a sign that lubrication is insufficient or that the valve components are starting to seize due to heat.
Check for Leaks:
If you notice leaks around the valve stem, body, or actuator, overheating may be the cause. Excessive heat can cause seals and gaskets to degrade, leading to leaks. Inspect the valve’s sealing surfaces and look for any visible gaps or dripping fluids.
Monitor Valve Operation:
If the valve becomes harder to open or close, or if it operates sluggishly, it is likely that thermal expansion is causing internal friction. Excessive wear on moving parts, such as the valve ball or actuator mechanism, may also be a sign of overheating. The inability to rotate the valve ball freely can result in partial or complete failure of the valve’s function.
Solutions for Overheating
Once the overheating issue has been identified, it’s time to take corrective action. Here are some steps you can take to fix or prevent further overheating issues:
Adjust System Settings:
Review the temperature and pressure settings within the system to ensure they are within the recommended operating range for the valve. If system settings are too high, adjust the pressure relief valves, pressure regulators, or temperature controls to bring the system back into the proper range. Implementing a temperature or pressure control system can prevent future overheating issues.
Replace Damaged Components:
If the valve has been subjected to excessive heat and is showing signs of seal or gasket failure, it is essential to replace the damaged components immediately. Check the valve seals, O-rings, and gaskets for signs of degradation, and replace them with new ones. If the valve body or internal components have become cracked or deformed, you may need to replace the entire valve or specific damaged parts.
Install Additional Cooling or Heat Management Equipment:
If overheating is a recurring issue, consider installing additional cooling equipment, such as heat exchangers or cooling jackets, around the valve or in the pipeline. This can help dissipate excess heat and maintain the valve at an optimal operating temperature. For high-temperature applications, consider using valves made of heat-resistant materials, such as stainless steel or special alloys, that are better suited to withstand extreme temperatures.
Lubricate Moving Parts:
If overheating has caused moving parts, such as the valve ball or actuator, to wear excessively, lubrication may help reduce friction and improve valve operation. Ensure that the valve and actuator are properly lubricated with high-quality, temperature-resistant lubricants to reduce friction and prevent seizing.
Reevaluate Valve Selection:
In some cases, overheating may be a result of using the wrong type of ball valve for the application. If the ball valve is not rated for the temperature or pressure conditions it is exposed to, you may need to replace it with one that is designed to handle higher temperatures. Selecting the right valve material and design for the specific fluid and environmental conditions is critical to avoiding future overheating issues.
Conclusion
The key to avoiding overheating issues lies in proper maintenance, correct valve selection, and early detection. By adhering to manufacturer guidelines for operating temperatures and ensuring that valves are installed and maintained correctly, you can significantly extend the life of your ball valves and keep your fluid control systems running smoothly.
FAQ
What causes overheating in ball valves?
Overheating in ball valves can be caused by factors such as excessive temperature in the fluid passing through the valve, improper system settings (too high pressure or temperature), and insufficient cooling.
How can I tell if my ball valve is overheating?
Signs of overheating include discoloration of the valve body, leaking at the valve stem or body, difficulty in opening or closing the valve, unusual noises from the actuator, and abnormal pressure or temperature readings on the system gauges.
What happens to the ball valve when it overheats?
Overheating can lead to degradation of seals and gaskets, resulting in leaks. It may also cause internal components like the ball or actuator to warp or seize due to thermal expansion, reducing the valve’s efficiency or causing it to fail entirely.
Can overheating damage the valve permanently?
Yes, if overheating is not addressed promptly, it can cause permanent damage to the valve’s internal components, seals, and body.
How do I prevent overheating in ball valves?
To prevent overheating, regularly monitor system temperature and pressure, ensure proper valve selection for the operating conditions, and schedule periodic maintenance.
What should I do if my ball valve is overheating?
First, check temperature and pressure readings to confirm overheating. Inspect the valve for physical damage, leaking, or unusual sounds. Replace damaged components like seals or gaskets, and consider adjusting system settings or installing cooling solutions to prevent further issues.