Misconnections or improperly assembled hoses can compromise both, leading to system failures, leaks, and potential hazards to personnel. Without secure connections, a hydraulic system can quickly lose its ability to function efficiently, costing time and money to repair.
Common Reasons Hydraulic Hoses Won’t Connect
Residual Pressure
One of the most common causes of difficulties when connecting hydraulic hoses is residual or trapped pressure within the system. When hydraulic systems are shut down, pressure can remain trapped inside the hose or fitting, which can make it impossible to properly connect or disconnect hoses. This residual pressure can create resistance or cause the connection to be misaligned, preventing a secure fit.
How Residual Pressure Affects Connections:
The trapped fluid can create an imbalance, causing the fittings to become misaligned or making it difficult to fully engage the hose with the fitting.
Pressure within the hose may force the connection out of alignment or even cause leakage once the system is pressurized again.
Solutions to Relieve Residual Pressure:
- Bleed the System: Always depressurize the hydraulic system before attempting to disconnect or reconnect hoses. Use the system’s relief valve or pressure release valve to safely release trapped fluid and pressure.
- Use Pressure-Relief Fittings: Some systems are equipped with pressure-relief fittings that automatically release trapped pressure, preventing issues when connecting or disconnecting hoses.
- Check for Hydraulic Pressure Leaks: If residual pressure persists, there may be a pressure leak or a faulty valve, which should be addressed before attempting any further connections.
By ensuring that residual pressure is properly released, you will avoid unnecessary stress on the hose and fitting and reduce the risk of damage.

Incorrect Fitting Size
Another common issue when connecting hydraulic hoses is using the wrong size hose fittings. Mismatched sizes prevent the fitting from properly connecting to the hose or component, leading to leaks, pressure loss, or misalignment. Hydraulic fittings come in various sizes and thread types, and selecting the wrong one can be a major cause of connection failure.
How Incorrect Fitting Size Affects Connections:
- Loose Fittings: If the fitting is too small for the hose, it may not create a tight seal, leading to fluid leaks.
- Over-tightening: Conversely, if the fitting is too large, it may cause unnecessary stress on the hose, which can lead to damage or deformation.
How to Identify the Correct Hose and Fitting Sizes:
- Match the Hose Diameter: Ensure that the internal diameter of the hose matches the size of the fitting. This is critical for achieving the proper fluid flow and pressure rating.
- Match the Thread Type: Threads must be matched between the hose fitting and the fitting on the component. Common thread types include BSP, NPT, JIC, and SAE. Always ensure the threads on both ends are compatible.
- Check Pressure Ratings: Make sure the hose and fitting have matching pressure ratings for optimal performance and safety.
By carefully selecting the right fitting for each application, you ensure a secure connection and avoid unnecessary system failures.
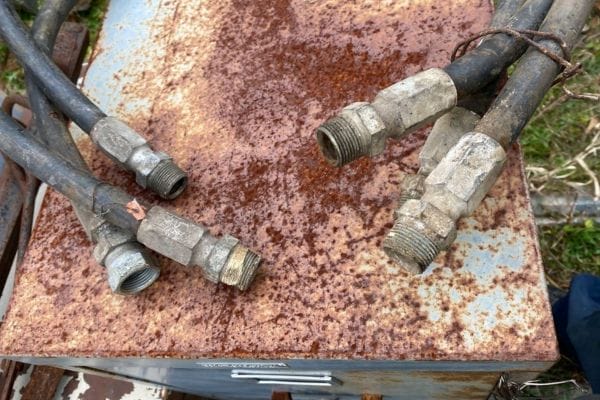
Damaged Hose or Fittings
Wear and tear, corrosion, or physical damage to hoses or fittings is another common cause of failed connections. Over time, hydraulic hoses can suffer from abrasion, chemical exposure, UV degradation, or pressure fatigue, all of which weaken the hose and fitting connections. Similarly, fittings can become damaged through corrosion or physical impacts, preventing a proper seal.
How Damaged Components Affect Connections:
- Leaking Hose or Fitting: Physical damage or corrosion can create gaps or weak points in the hose or fitting, resulting in fluid leakage and pressure loss.
- Imbalanced Connection: Damaged components may lead to misalignment, making it difficult to properly secure the hose to the fitting.
Inspecting Hoses and Fittings for Damage:
- Regular Visual Inspections: Check for visible signs of wear, such as cracks, frays, or bulging in the hose, and corrosion, rust, or scratches on the fittings.
- Pressure Testing: Perform pressure tests to identify leaks or weakness in the hose or fitting.
- Replace Damaged Components: If damage is detected, replace the damaged hose or fitting to ensure the system operates safely and efficiently.
Ensuring that all components are in good condition will help maintain a reliable connection and minimize the risk of system failure.
Improper Hose Routing
Improper hose routing is a common issue that often leads to problems with hydraulic hose connections. Bending hoses too sharply, improper alignment, or poor placement can cause stress on the hose and fittings, making it difficult to connect them properly or causing them to fail prematurely.
How Improper Routing Affects Connections:
- Kinking and Twisting: Sharp bends or twists in the hose can cause internal pressure points, making it harder to align or connect hoses to fittings. This may also lead to internal hose damage over time.
- Compression and Overstretching: Routing the hose through tight spaces or across edges may cause it to compress or stretch, compromising its integrity and causing difficulty when trying to secure the connection.
Proper Installation Techniques:
- Avoid Sharp Bends: Always ensure that hoses are routed with gentle curves and never bent beyond the recommended bend radius.
- Use Hose Supports: Use clamps, brackets, or other supports to hold hoses in place and prevent them from sagging or moving, which can cause alignment issues.
- Allow for Flexibility: Ensure that hoses have enough slack to accommodate system movement or vibration without placing excessive stress on the connections.
Proper hose routing is critical for preventing damage to hoses and fittings and ensuring that connections remain secure.
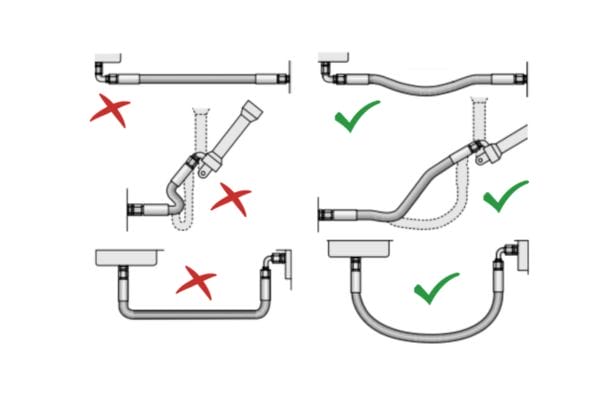
Dirty or Contaminated Fittings
Contaminants such as dirt, dust, oil residue, or rust can prevent hydraulic hoses from connecting properly. Even a small amount of dirt or foreign matter can interfere with the sealing surfaces of the fitting and hose, leading to leaks or difficulty in securing the connection.
How Dirt and Contaminants Affect Connections:
- Impaired Sealing: Contaminants can prevent the fitting from properly sealing with the hose, leading to fluid leakage or poor pressure retention.
- Increased Wear: Dirt and rust on fittings can lead to accelerated wear, eventually resulting in system failure or performance issues.
How to Clean and Maintain Fittings:
- Clean Fittings Before Installation: Use a clean cloth or brush to remove dirt, rust, or any other debris from the fitting before installation. Avoid using solvents that could contaminate the fluid system.
- Check for Rust or Corrosion: Inspect metal fittings for signs of corrosion and replace any damaged or heavily corroded parts.
- Use Filters: Incorporate filtration systems into the hydraulic system to prevent contaminants from entering the hoses and fittings.
How to Fix Hydraulic Hose Connection Issues
Relieving Residual Pressure
Residual or trapped pressure within hydraulic hoses is one of the primary causes of difficulties when connecting or disconnecting hoses. Trapped pressure can make it difficult to properly install or remove hoses, and if not addressed, it can also cause unsafe situations.
Step-by-Step Guide on Safely Relieving Trapped Pressure:
- Turn Off the Hydraulic System: Ensure the hydraulic system is powered off to prevent any unintentional pressure buildup during the process.
- Locate the Pressure Relief Valve: Most hydraulic systems have a pressure relief valve that helps to safely release trapped pressure from the system. This valve is typically located on the pump or the system manifold.
- Activate the Relief Valve: Slowly open the relief valve to let trapped hydraulic fluid escape. It’s crucial to do this gradually to avoid a sudden release of pressure, which could cause injury or damage.
- Check the System’s Pressure Gauge: If the system has a pressure gauge, monitor it as you open the valve to confirm that the pressure is being safely released.
- Cycle the System (if applicable): In some cases, cycling the hydraulic system (activating the hydraulic cylinders or valves) can help to release any residual pressure in the lines.
- Confirm Pressure is Fully Released: Before proceeding with hose disconnection, confirm that all pressure has been safely relieved by checking for any resistance when attempting to disconnect the hose.
Tools and Techniques for Pressure Release:
- Pressure Relief Valve: Always use the pressure relief valve designed for your system to release pressure. It ensures that the process is done safely.
- Hydraulic System Gauges: Use the system’s built-in pressure gauge or a dedicated test gauge to confirm that pressure has been fully relieved.
By following these steps, you can safely relieve residual pressure from hydraulic hoses, ensuring a secure and hassle-free connection process.
Ensuring the Correct Fitting Size
Mismatched fittings are a common issue when working with hydraulic hoses. Using the wrong fitting size can result in poor connections, leading to leaks, pressure loss, and system failures. It is essential to select the correct size fitting for the hose and application.
How to Properly Measure and Select the Right Fitting for Your Hose:
- Measure the Hose Diameter: Begin by measuring the internal diameter (ID) of the hose to determine the appropriate fitting size. A proper fit ensures that the fluid flows smoothly through the system without obstruction.
- Match the Fitting Threads: Different hydraulic systems use different thread types, such as NPT (National Pipe Thread), JIC (Joint Industrial Council), BSP (British Standard Pipe), and SAE (Society of Automotive Engineers). Ensure that the thread type on the hose fitting matches the thread type on the component or port.
- Verify Fitting Length and End Type: Ensure that the length and type of the fitting match the system’s requirements. For instance, if using a straight fitting, ensure it is the correct length for the hose’s needs. Also, make sure the fitting end (male or female) matches the port configuration.
- Check the Sealing Surface: A proper sealing surface is essential to prevent leaks. Check for any damage to the sealing surface of both the hose and fitting. If either is damaged or worn out, it will compromise the connection.
Best Practices for Matching Hoses and Fittings:
- Always double-check the specifications of both the hose and the fitting.
- Use matching components from trusted manufacturers to ensure compatibility.
- Use a thread sealant or O-rings, when necessary, to ensure a leak-proof connection.
Taking the time to measure and select the right fitting size for your hose will prevent many connection-related issues and ensure that your hydraulic system operates safely and efficiently.
Replacing Damaged Components
Hydraulic hoses and fittings experience wear and tear over time due to factors such as exposure to high pressure, temperature fluctuations, chemical exposure, and physical damage. Worn-out or damaged hoses and fittings can prevent a secure connection, leading to leaks, system failures, and unsafe working conditions.
How to Check for and Replace Worn-Out or Damaged Hoses and Fittings:
Inspect Hoses for Damage:
- Look for visible cracks, frays, bulges, or abrasions on the hose surface.
- Check for signs of swelling, which could indicate internal damage due to excessive pressure or temperature.
- Ensure that the hose is not kinked or bent beyond its recommended bend radius, as this can cause internal stress and lead to failure.
Inspect Fittings for Corrosion and Wear:
- Examine the fittings for signs of corrosion, rust, or physical damage such as nicks and scratches.
- Check the threads of the fitting for wear. Worn threads can prevent proper sealing and cause leaks.
Replace Worn or Damaged Components:
- For Hoses: If the hose is damaged or worn out, replace it with a new hose of the same type and size. Ensure that the new hose meets or exceeds the required pressure rating.
- For Fittings: Replace any damaged fittings, ensuring that the new ones match the required thread type, size, and material.
- Pressure Test After Replacement: After replacing the damaged components, conduct a pressure test to verify that the new hose and fittings are securely connected and capable of withstanding operational pressures without leaking.
By regularly inspecting hoses and fittings and replacing damaged components promptly, you can prevent failures and maintain the reliability of your hydraulic system.
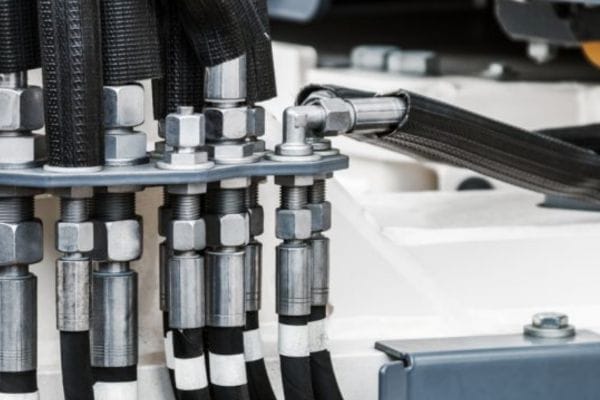
Proper Hose Routing
Incorrect hose routing is another common reason why hydraulic hoses fail to connect or function properly. Bending hoses too sharply, improper alignment, or poor placement can place excessive stress on hoses and fittings, leading to poor performance or failure. Proper hose routing is crucial to ensuring the long-term integrity of hydraulic systems.
Step-by-Step Guide to Correct Hose Installation:
- Check Manufacturer Specifications: Always refer to the manufacturer’s specifications for the recommended bend radius, alignment, and routing of hoses. This will help you avoid damaging the hose during installation.
- Avoid Sharp Bends: Ensure that hoses are routed with gradual bends. Sharp bends can cause the hose to kink, leading to pressure loss or hose rupture. Use the correct bend radius for the specific hose type.
- Use Hose Supports and Clamps: Route hoses through designated channels or use hose supports and clamps to secure the hoses in place and prevent them from sagging, rubbing against sharp edges, or being exposed to excessive movement.
- Allow for Flexibility and Movement: When routing hoses, ensure that they have enough slack or flexibility to allow for system movement and vibration. Stiff, tightly pulled hoses can be at risk of breaking or disconnecting under stress.
- Protect Against Abrasive Surfaces: Use protective sleeves or guards for hoses passing through rough surfaces or areas with high mechanical wear. This can prevent abrasion damage over time.
Tools and Techniques for Effective Hose Routing:
- Hose Bending Tools: Use tools such as bending springs or hydraulic hose benders to prevent sharp kinks and ensure a smooth curve.
- Clamps and Brackets: Use high-quality hose clamps and brackets to keep hoses securely in place and avoid unnecessary movement or stress.
Conclusion
To avoid connection issues and ensure optimal performance of your hydraulic system, it is crucial to follow best practices for installation, maintenance, and component inspection. Regular checks for wear and tear, correct installation of fittings, and adherence to routing specifications will significantly reduce the chances of encountering hose connection problems. For further information or assistance with hydraulic hose systems, consider reaching out to Topa experts in hydraulic hose fabrication and maintenance.
FAQ
What is the most common reason hydraulic hoses won’t connect?
The most common reason is residual pressure in the system, which can prevent the hose from connecting properly.
How can I fix hydraulic hose connection issues caused by incorrect fitting size?
To fix incorrect fitting size, ensure you are using the correct hose and fitting sizes by measuring both accurately. Check the thread types and sealing surfaces to ensure compatibility.
Can damaged hoses prevent hydraulic hose connections?
Yes, worn-out or damaged hoses, whether from wear, corrosion, or physical damage, can prevent a secure connection. It’s important to inspect hoses regularly and replace any damaged components.
How do I relieve residual pressure in a hydraulic system before connecting a hose?
To relieve residual pressure, you can use a pressure relief valve, or disconnect the hose from the system while ensuring the pressure is safely vented away from the connection point.
What’s the correct way to route hydraulic hoses to prevent connection issues?
Ensure hoses are routed with proper alignment, avoid sharp bends, and maintain the minimum bend radius. This prevents stress on the hose and ensures proper function.
How can I maintain my hydraulic fittings to avoid connection problems?
Clean fittings regularly to remove dirt, rust, or contaminants, and inspect them for wear or damage. Ensure proper lubrication and tightening to maintain a secure connection.