A ball valve uses a spherical ball with a hole through the center to regulate flow, making it ideal for quick shut-off and easy flow control. However, proper installation is crucial for ensuring these valves function as intended. Incorrect installation can lead to performance issues, leaks, and even system failures, making it important to address installation mistakes early. These mistakes—such as alignment problems, poor sealing, misapplied torque, and inadequate valve connections—can compromise the entire system’s safety and performance.
Common Ball Valve Installation Problems
While ball valves are relatively simple to install, several common issues can arise during the installation process. These issues, if not addressed, can lead to reduced performance, leaks, and even valve failure. Understanding the typical problems and their causes is crucial for ensuring a successful installation.
Inadequate Valve Alignment and Its Impact on Performance
Proper alignment is critical when installing a ball valve. If the valve isn’t aligned correctly with the pipework, it can cause strain on the valve components, leading to leaks, difficulty in operation, or even valve failure. Misalignment can also affect the flow of fluid, causing uneven pressure distribution or unwanted turbulence. Ensuring that the valve is perfectly aligned with the piping system from the start is essential for optimal performance.
Incorrect Valve Seat Installation: Why It Matters
The valve seat plays a vital role in sealing the ball valve. If the seat is improperly installed, it can lead to leaks, reduced sealing effectiveness, and poor flow control. Incorrect seat installation can also cause the valve to wear out faster, compromising the entire system. It’s important to ensure that the seat is positioned correctly, the right material is used, and it is installed securely to prevent any sealing issues.
Improper Valve Connections: Common Mistakes to Avoid
Valve connections are an integral part of the installation process. Improperly connecting the valve to the pipeline, whether through threaded, flanged, or welded connections, can result in leaks or system failures. Common mistakes include over-tightening, under-tightening, or using incorrect fittings that don’t match the valve’s specifications. Always ensure that the connections are made according to the manufacturer’s guidelines to guarantee leak-free operation.
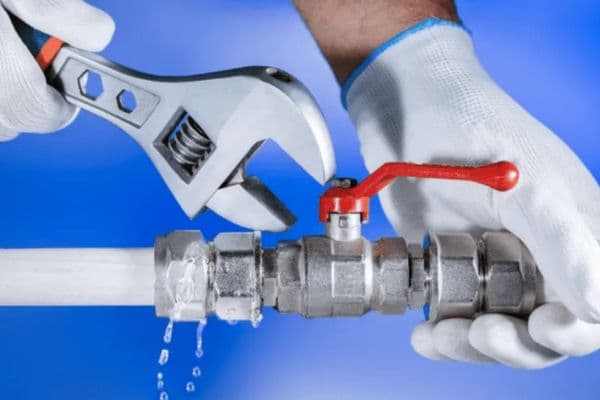
Failure to Properly Seal the Valve: Causes and Consequences
A failure to adequately seal the valve can lead to significant operational issues, including leaks and pressure loss. Sealing issues are often caused by the use of incorrect materials, improper installation techniques, or failure to apply the right amount of torque. If the valve isn’t sealed correctly during installation, it can compromise the entire system’s performance, leading to costly repairs and potential safety hazards.
Valve Tightening Issues: How Over-tightening and Under-tightening Affect Performance
Tightening the valve too much or not enough can result in significant problems. Over-tightening can cause damage to the valve components, leading to deformation, leaks, and difficulty in operation. On the other hand, under-tightening can cause the valve to remain loose, leading to leaks or an inability to regulate flow properly. It’s essential to follow the manufacturer’s recommended torque specifications to ensure the valve is tightened just right for optimal performance.
Signs of Ball Valve Leaks and How to Fix Them
Ball valve leaks are one of the most common issues faced after installation. Leaks can affect the performance of the valve and the entire piping system, leading to inefficiency and potential safety hazards. Identifying and addressing these leaks early is crucial for maintaining the integrity of your system. In this section, we’ll explore how to identify ball valve leaks, the best ways to seal them, and preventative measures to avoid future issues.
Identifying the Source of Ball Valve Leaks
The first step in fixing a ball valve leak is identifying where the leak is coming from. Leaks can occur at various points in the valve, including:
The valve stem: Often caused by wear on the packing or improper sealing.
The valve body: Leaks can develop at the connections or between the valve body and the seat.
The valve connections: Leaks can occur where the valve connects to the pipework, often due to improper tightening or damaged gaskets. To diagnose a leak, inspect the valve thoroughly for visible signs of moisture or fluid accumulation around the valve, valve stem, or connections. Pressure testing can also help pinpoint the exact location of the leak.
How to Seal Leaks Effectively: Valve Sealing Materials and Techniques
Once the leak has been identified, it’s time to focus on sealing the valve effectively. The choice of sealing materials and techniques is critical for a leak-free installation. Common sealing materials include:
PTFE (Teflon) tape: Ideal for sealing threaded connections.
Rubber or elastomer gaskets: Used for sealing flanged connections.
O-rings: Essential for sealing between the valve stem and body. When sealing a ball valve, it’s important to:
Clean the sealing surfaces thoroughly before applying any sealant.
Use the correct type of sealant based on the material and pressure rating of your system.
Apply sealant evenly and avoid over-application, which could cause clogs or impair valve function.
Ball Valve Leak Prevention Tips
Preventing leaks in ball valves is always more efficient than fixing them later. Here are a few practical tips to help you avoid leaks during and after installation:
Use the right sealing materials: Ensure you are using compatible materials for your system’s temperature, pressure, and chemical conditions.
Ensure proper tightening: Avoid over-tightening or under-tightening, as both can lead to leaks. Use a torque wrench to apply the recommended torque specification.
Regular maintenance: Inspect valves periodically to check for signs of wear, corrosion, or any other damage that could cause leaks. Replace damaged seals or gaskets before they fail.
Lubricate moving parts: Keeping the valve stem lubricated helps prevent wear and reduces the chances of leaks at the stem.
Step-by-Step Guide to Fixing Leaky Ball Valves
If you discover a leak in your ball valve, follow these steps to fix it properly:
Turn off the system: Isolate the valve from the rest of the system by turning off the pressure and ensuring the system is de-energized.
Identify the leak: Thoroughly inspect the valve and connections to pinpoint where the leak is occurring.
Disassemble the valve: Depending on where the leak is, you may need to remove the valve from the pipeline. This could involve unthreading connections, loosening bolts, or unscrewing flanges.
Replace damaged seals: If the leak is due to a damaged seal, O-ring, or gasket, remove the damaged part and replace it with a new, compatible one.
Reassemble the valve: After replacing the necessary parts, reassemble the valve carefully, ensuring all connections are properly aligned and sealed.
Tighten the valve correctly: Use a torque wrench to tighten the valve to the manufacturer’s recommended torque specifications.
Test for leaks: Once the valve is reassembled, perform a pressure test to ensure the leak is fixed and that the valve is operating properly.
Troubleshooting Ball Valve Installation Problems
Ball valve installation can sometimes lead to issues that affect the performance and longevity of the valve. When these problems arise, it’s essential to have a clear approach to troubleshooting and resolving them.
How to Troubleshoot Valve Pressure Issues
Pressure issues in ball valves can stem from several sources, including improper valve installation, incorrect valve size, or blockages in the system. Here’s how to troubleshoot pressure issues effectively:
Check the Valve Size: Ensure the valve is correctly sized for your system’s pressure and flow requirements. An oversized or undersized valve can cause issues.
Inspect the System Pressure: Use a pressure gauge to confirm whether the system pressure is within the valve’s rated specifications. Overpressurization can cause leaks or failure, while under-pressurization may affect the valve’s operation.
Look for Blockages: Blockages or debris in the valve or the pipeline can restrict flow and cause pressure imbalances. Disassemble the valve and clear any obstructions.
Examine Seals and Gaskets: Damaged seals or gaskets can cause pressure loss. If these components are worn or incorrectly installed, replace them with new, compatible materials.
Diagnosing and Solving Valve Performance Problems
Valve performance issues often stem from improper installation, wear and tear, or system misalignment. To diagnose and fix these problems:
Check for Smooth Operation: Manually operate the valve to ensure it opens and closes smoothly. If the valve is difficult to turn or is stuck, the ball may be misaligned or the stem may be damaged.
Monitor Flow Rates: If the flow rate is lower than expected, the valve may not be fully opening. Ensure the actuator is functioning properly and that there are no obstructions within the valve body.
Evaluate the Valve Seat: A worn or damaged valve seat can prevent proper sealing, leading to performance issues. Inspect and replace the valve seat if necessary.
Inspect Actuator and Stem: If the valve is part of an automated system, check the actuator and stem for wear or misalignment. Damaged components may require repair or replacement to restore proper function.
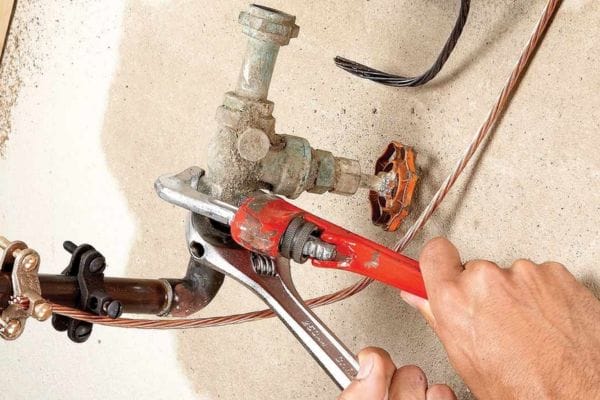
Common Troubleshooting Techniques for Hydraulic and Industrial Ball Valves
Hydraulic and industrial ball valves often face unique challenges due to high-pressure environments and harsh operating conditions. To troubleshoot these valves:
Check for Fluid Leaks: Hydraulic valves are prone to leaks due to high pressure. Use a leak detection system or visually inspect all connections and seals for any signs of fluid leakage.
Perform a Pressure Test: Conduct a pressure test to ensure the valve is maintaining the desired operating pressure. This test can help identify internal leaks or valve failure.
Verify Flow Control Settings: In industrial settings, flow control is critical. Ensure the valve is correctly set to regulate the required flow rate, especially in systems with varying pressure and temperature.
Look for Signs of Wear and Tear: Inspect the valve for signs of corrosion, pitting, or excessive wear that could affect performance. Regular maintenance and timely part replacement can prevent these issues from escalating.
How to Troubleshoot Valve Pressure Issues
Pressure issues in ball valves can manifest as poor flow control, system instability, or unexpected drops in pressure. To troubleshoot valve pressure issues effectively, follow these steps:
Check for System Overpressure Ball valves have a maximum pressure rating, and exceeding this rating can cause failures. Check the system’s pressure with a gauge to confirm that it’s within the acceptable range for the valve. Fix: If the pressure is too high, consider installing a pressure regulator or a different valve designed for higher-pressure systems.
Ensure Valve Size Compatibility Using a valve that is too small or too large for the system can cause pressure problems. A valve that’s too small may restrict flow, while a valve that’s too large may cause excessive turbulence. Fix: Verify that the ball valve size matches the system’s flow and pressure requirements. If necessary, upgrade or downgrade the valve size for optimal performance.
Look for Blockages or Obstructions Blockages within the valve or the connected pipeline can lead to increased pressure or uneven flow. Fix: Disassemble the valve and inspect the internal components for debris or blockages. Clean the valve and piping, and replace any damaged parts before reassembling.
Examine the Valve for Leaks Leaks can cause a drop in pressure. If the valve is leaking, it may be allowing fluid to escape and reducing the pressure within the system. Fix: Tighten connections, replace worn seals, and address any leaks around the valve stem or valve body.
Diagnosing and Solving Valve Performance Problems
Performance issues often arise from improper installation, wear, or insufficient maintenance. Diagnosing and solving these problems early can prevent more severe complications in the future.
Slow or Sticking Valve Operation If the valve is difficult to operate or gets stuck, it may be due to internal corrosion, misalignment, or a damaged actuator (in automated systems). Fix: Inspect the valve for any rust or corrosion. Clean the internal components and lubricate the valve stem. If the actuator is damaged, repair or replace it.
Irregular Flow Rates If the flow rate is inconsistent, the valve may not be fully opening or closing, which could be due to incorrect actuator settings, misalignment, or internal blockage. Fix: Check the actuator settings and ensure the valve is operating smoothly. Inspect for any obstructions and clean the valve as necessary.
Improper Valve Seating A valve that doesn’t seat properly can lead to poor sealing and inefficient flow control. This can occur due to poor installation, wear, or incorrect valve components. Fix: Inspect the valve seat for any damage or misalignment. Replace the seat or re-align the valve components to ensure proper sealing.
Excessive Leakage Leakage can compromise valve performance by causing loss of pressure or reducing system efficiency. Fix: Identify the leak source (valve stem, body, or connections) and repair it by replacing seals, gaskets, or tightening connections as needed.
Common Troubleshooting Techniques for Hydraulic and Industrial Ball Valves
Hydraulic and industrial ball valves often face additional challenges due to the higher pressures, temperatures, and harsh environments they operate in. Use the following techniques to troubleshoot these systems effectively:
Perform Pressure and Leak Tests Use pressure testing equipment to test the valve under operating conditions. A pressure drop during testing indicates a leak, misalignment, or other internal issues. Fix: If leaks are detected, replace the damaged seals, re-align the valve, or replace worn components.
Inspect Actuators and Control Systems In industrial systems with automated valves, issues may arise with the actuator, control systems, or electric connections. Fix: Test the actuator to ensure it’s receiving the correct signals. Inspect the electrical and pneumatic connections to identify any faults.
Examine the Valve for Contamination In hydraulic systems, contamination from dirt, debris, or incompatible fluids can cause performance issues. Fix: Clean the valve and surrounding system components, replace any contaminated fluid, and install filters to prevent future contamination.
Conclusion
Ensuring a successful ball valve installation begins with addressing common problems such as incorrect alignment, incorrect seat installation, leakage, and seal failure. By focusing on proper valve alignment, using the correct sealing material, applying the correct torque and performing regular inspections, you can prevent performance problems and ensure long-term reliability. Following best practices, such as selecting the correct valve size, staying within the rated pressure range, and avoiding over- or under-tightening, will help maintain optimal valve performance over time.
FAQ
What is a ball valve used for?
A ball valve is a quarter-turn valve used to control the flow of liquids and gases in piping systems. It uses a spherical ball with a hole in the center to either allow or block flow.
How do I know if my ball valve is installed correctly?
Check for proper alignment with the piping system, ensure connections are tight but not over-tightened, and confirm there are no leaks. Also, ensure the valve operates smoothly without any resistance.
What are common signs of a ball valve leak?
Leaks often appear around the valve stem, valve connections, or the valve body. Visible moisture, fluid accumulation, or drops of liquid around these areas are common signs.
Can I fix a leaky ball valve myself?
Yes, minor leaks can often be fixed by replacing damaged seals, tightening connections, or adjusting the valve packing. However, for more serious issues, professional assistance may be required.
How can I prevent leaks in my ball valve?
Use the correct sealing materials, apply the proper torque to valve connections, and inspect valves regularly for wear or damage. Ensuring the valve is properly aligned during installation also helps prevent leaks.
Why is valve alignment important during installation?
Improper alignment can cause uneven wear on the valve, leading to leaks, reduced performance, or even valve failure. Correct alignment ensures the valve operates smoothly and maintains system integrity.