A proper understanding of a ball valve‘s markings and abbreviations is crucial when selecting one. These markings provide valuable information that helps determine whether a valve will perform as required in a specific application. WOG (Water, Oil, Gas) is a marking commonly found on valves, but what exactly does it signify?
What is WOG?
Definition of WOG
WOG is an abbreviation that stands for Water, Oil, and Gas, a standard marking found on ball valves, and it represents the valve’s suitability for use in systems that handle these three specific types of media. The WOG rating indicates the maximum pressure a valve can safely handle when it is exposed to water, oil, or gas, ensuring that the valve performs optimally under the conditions for which it was designed.
The WOG pressure rating is typically marked on the valve body and serves as an essential guideline for choosing the correct valve for a given application, ensuring it will withstand the pressure and temperature limits associated with the media. Without this rating, the valve might be subjected to conditions that could cause leaks, failure, or safety hazards.
Water Suitability
A ball valve with a WOG rating that includes water suitability is designed to handle pressurized water systems without compromising the valve’s integrity. The valve can withstand water’s various properties, such as its density and viscosity, which vary with temperature. For example, in systems like plumbing, irrigation, or fire suppression, the valve must handle not only normal water pressure but also potential spikes, such as during surges or system starts.
Oil Suitability
For oil systems, the WOG rating signifies the valve’s capacity to handle oil at specific temperatures and pressures. Oil systems can include hydraulic systems, lubrication systems, or fuel delivery systems, where the flow and viscosity of oil require valves that can endure higher pressures and temperature fluctuations. Oil is more viscous than water and has different chemical properties that may demand specific materials (such as corrosion-resistant alloys) for the valve to avoid degradation over time.
Gas Suitability
Gas systems, including those transporting natural gas, air, steam, or other gases, demand a different set of considerations. The WOG rating for gas indicates that the valve can maintain its seal and function effectively under the operating pressure of the gas. For instance, gases are compressible and can vary in density depending on temperature and pressure. Therefore, the valve needs to be designed to manage these conditions without risk of leakage or damage. Gas systems often experience fluctuations in pressure and temperature, which the valve must accommodate without failure.
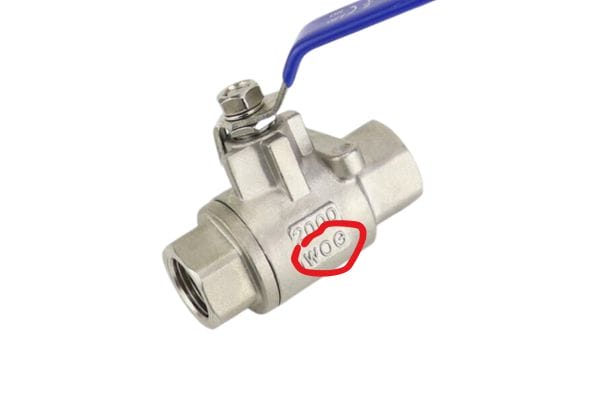
Purpose of WOG Pressure Ratings
The primary function of the WOG pressure rating is to define the valve’s operational limits based on the type of media it is handling. Each of the three media—water, oil, and gas—has unique properties that impact the pressure and flow rate the valve can safely withstand. For example:
Water is typically incompressible and might be subject to hydraulic surges or thermal expansion.
Oil has a higher viscosity than water and might require special materials to prevent corrosion or wear over time, especially in systems that operate under high pressure.
Gas, being compressible, introduces unique challenges regarding pressure variations, especially in systems that experience fluctuating operating conditions.
The WOG rating serves as a guideline to ensure the valve is not exposed to conditions that exceed its capacity, which could lead to failure, leakage, or safety hazards. For instance, using a valve rated for a lower pressure in a high-pressure system can result in catastrophic failure, whereas using a valve rated for too high a pressure in a low-pressure application can be unnecessarily costly.
Relationship Between WOG and Pressure Ratings
Pressure Ratings and PSI
The WOG rating of a valve is typically expressed in PSI (Pounds per Square Inch), which is a unit of pressure used to measure how much pressure the valve can safely handle for a particular medium—whether it’s water, oil, or gas. PSI provides a standard measurement of pressure, and the WOG rating indicates the maximum pressure the valve can withstand under normal operating conditions.
WOG Pressure Rating
The WOG pressure rating is the maximum allowable pressure that the valve can handle for a given medium (water, oil, or gas) without risk of failure. For example, a valve marked as 200 WOG means that the valve is rated to safely operate under pressures up to 200 PSI for water, oil, or gas.
The WOG rating will depend on factors like:
Material: The construction material (e.g., brass, stainless steel, or carbon steel) impacts the valve’s ability to withstand high pressures. Some materials may be more resistant to corrosion or wear and may handle higher pressures.
Valve Design: The structural design and sealing mechanism (e.g., ball, butterfly, or gate valve) also influence the pressure rating. Ball valves generally offer a good balance between cost and performance for many applications, but specialized designs may be required for extreme pressure conditions.
Size: Larger valves with bigger diameter openings are typically rated for higher pressures, though their actual pressure limits will depend on their material and construction.
Pressure Ranges for Different Media
The WOG rating varies not only based on the material and size of the valve but also the specific medium (water, oil, or gas) it is designed for. Even valves made from the same material may have different pressure ratings depending on the media they are intended to handle.
Water: Water is relatively incompressible, so it typically requires higher pressure ratings, especially in applications like plumbing, irrigation, and water treatment. Valves rated for water often have higher WOG ratings to account for the continuous pressure load.
Oil: Oil systems, like those in hydraulic or lubrication circuits, usually have a different pressure profile. Since oil is more viscous than water and does not compress as easily as gas, oil systems often require valves with a WOG rating tailored to handle these unique characteristics. Additionally, the chemical properties of certain oils might require specific valve materials to avoid corrosion or degradation.
Gas: Gas is compressible, so pressure ratings for gas valves are often different from those of water or oil. Valves handling gas need to withstand the fluctuating pressures that can occur in gas pipelines, tanks, or HVAC systems. While gas valves may sometimes have lower WOG ratings than water valves of similar size, they must be capable of handling the varying pressures associated with gas flow, especially in systems where the pressure fluctuates significantly.
How to Adapt Pressure Ratings for Different Media
Each medium—water, oil, and gas—has different physical properties that affect how pressure is handled within a system. Understanding these differences is critical when selecting valves for specific applications. Here’s how to adapt the pressure ratings for each type of media:
Water
Water, being nearly incompressible, requires valves with higher pressure ratings to prevent bursting under high pressure. It also tends to cause erosion in valve components if not properly handled, especially at higher velocities. When adapting a WOG rating for water:
Pressure fluctuations: Water pressure can experience surges due to pump starts or system cycles, so it is important to select a valve with a WOG rating that accounts for these fluctuations.
Temperature: Water temperature changes can affect pressure, so valves in high-temperature water systems need to be rated for higher pressures, especially in industries like power generation and chemical processing.
Oil
Oil is generally more viscous than water, which means it requires more energy to flow and will put more stress on the valve’s components. In addition, the chemical properties of oil, such as its lubricating and corrosive effects, can impact valve material selection.
Viscosity: High-viscosity oils require special consideration because the valve must manage the resistance to flow. A valve rated for oil must be robust enough to handle pressure without damaging internal components.
Chemical resistance: Depending on the oil’s chemical composition (e.g., petroleum-based vs. synthetic oils), valve materials need to be resistant to corrosion or degradation. Stainless steel and other corrosion-resistant materials are often preferred in such systems.
Gas
Gas is compressible, which means that gas systems tend to experience larger fluctuations in pressure due to temperature changes, pipeline movement, or system cycling.
Pressure drops and surges: Gas systems often require valves with pressure ratings that can handle sudden increases or drops in pressure. Gas valves should be able to operate reliably under fluctuating pressures while still maintaining a tight seal.
Temperature and pressure relationships: For gases, particularly natural gas or high-pressure gas systems, the pressure rating must also account for temperature variations, as the volume and pressure of a gas change with temperature. This is especially important in systems exposed to external temperature shifts, such as those used in refrigeration or natural gas pipelines.
Common Valve Abbreviations and Their Meanings
Valves come with various abbreviations that provide critical information regarding their design, performance, and compatibility with different systems. These markings and symbols help ensure that ball valves are used correctly and safely in specific applications. Below is an overview of some of the most common valve-related abbreviations:
SWP (Standard Working Pressure)
SWP refers to the Standard Working Pressure of a valve, which indicates the maximum pressure the valve can handle during normal operating conditions. It’s typically measured in PSI (Pounds per Square Inch) or bar and reflects the pressure the valve is designed to withstand under typical system conditions, without any extreme fluctuations.
Importance: Understanding SWP helps users ensure that the valve won’t be subjected to excessive pressure, which could cause failure or leaks. For instance, a valve with a 1000 SWP rating is designed to safely handle up to 1000 PSI in a typical operational environment.
Use Case: SWP is relevant for systems where the pressure is constant or where pressure does not exceed the specified limit during regular operation.
CWP (Cold Working Pressure)
CWP stands for Cold Working Pressure, which refers to the maximum pressure a valve can handle when the medium inside the system is at a low temperature. This rating is especially important for systems that operate in cold environments or those that are exposed to freezing conditions.
Importance: CWP is crucial when working with materials or environments where low temperatures can alter the characteristics of fluids or gases. A valve with a CWP rating is tested to ensure it will not fail due to brittleness or material weaknesses at low temperatures.
Use Case: CWP is commonly used for valves in refrigeration systems, cryogenic tanks, and industries where low temperature is a factor, like in gas transport or storage.
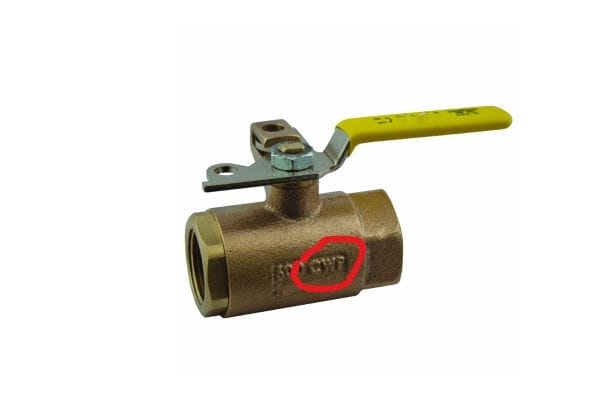
NPT (National Pipe Thread)
NPT refers to the National Pipe Thread, which is a standardized pipe thread used in the United States for plumbing and industrial systems. NPT threads are tapered, meaning the diameter of the threads decreases as they go down the pipe, creating a seal as the threads are tightened.
Importance: NPT markings indicate the type of threading used for connecting the valve to the piping system. It ensures a tight seal, preventing leaks in fluid and gas systems. The NPT standard is widely recognized for its robustness and reliability in industrial applications.
Use Case: NPT threads are used in piping systems for both low and high-pressure systems, including residential plumbing, oil and gas, and hydraulic systems.
ANSI (American National Standards Institute)
ANSI refers to the American National Standards Institute, a private non-profit organization that oversees the development of standards for a variety of industrial applications, including valves. When a valve is marked with an ANSI abbreviation, it means that it adheres to ANSI standards for performance, safety, and quality.
Importance: ANSI standards are important because they provide a uniform set of guidelines for valve design, material specifications, pressure ratings, and dimensional requirements. Compliance with ANSI standards ensures that valves are reliable and safe for use in critical systems.
Use Case: ANSI-compliant valves are commonly used in North America across various industries, such as chemical, power, and water treatment plants, where standardized equipment is required for safety and performance.
API (American Petroleum Institute)
API refers to the American Petroleum Institute, a trade association that sets standards for the petroleum industry, particularly in the areas of drilling, exploration, and pipeline systems. Valves that are marked with the API abbreviation comply with the standards set by the API, which is recognized for its rigorous requirements.
Importance: API valves are built to meet the high-pressure, high-temperature, and harsh conditions commonly encountered in the oil and gas industry. API valves are designed to withstand extreme pressures and resist corrosion and wear from aggressive chemicals.
Use Case: API-compliant valves are commonly found in the oil and gas sector, particularly in drilling rigs, oil refineries, and upstream/downstream operations, where equipment must handle high-pressure fluids and gases in challenging environments.
Other Common Valve Abbreviations
FPM (Fluorocarbon Elastomer): This abbreviation refers to a type of material used in valve seals and gaskets that are resistant to high temperatures and chemicals.
DN (Diameter Nominal): This designation is often used in metric countries and refers to the nominal size of the valve’s diameter in millimeters.
PSI (Pounds per Square Inch): A unit of pressure commonly used in North America to express pressure ratings of valves and other equipment.
CWP (Cold Working Pressure): As noted earlier, this is the maximum pressure a valve can safely handle in cold working conditions.
How to Correctly Interpret the Valve Marking
Interpreting valve markings is essential to ensuring that a valve is used correctly in a given application. These markings provide key information such as the valve’s pressure rating, media compatibility, material type, and certification standards. Here’s a guide to understanding the key valve markings and how to correctly interpret them:
Marking Position and Symbol Meaning
Valve markings are typically stamped or etched directly onto the valve body, and they are often located near the valve’s connection points or on flat surfaces of the valve housing. Some of the most common markings you will encounter include:
WOG Rating: The WOG (Water, Oil, Gas) pressure rating, such as 200 WOG, indicates the maximum pressure the valve can safely handle for the specified media (water, oil, or gas). This marking is typically found near the valve’s connection points.
Material Type: The material of the valve is often marked with abbreviations such as SS (Stainless Steel), CS (Carbon Steel), or Brass. This ensures that the valve is compatible with the fluid or gas being controlled, taking into account the potential for corrosion or wear.
Threading Type: Markings like NPT (National Pipe Thread), BSP (British Standard Pipe), or ISO indicate the type of threading used for connecting the valve to the piping. Correct thread types ensure a secure and leak-proof connection.
ANSI: The ANSI abbreviation indicates that the valve conforms to the standards set by the American National Standards Institute. This can be particularly important for valves used in North America in industries like chemical processing or power generation.
Pressure Ratings (SWP, CWP): As discussed earlier, SWP (Standard Working Pressure) and CWP (Cold Working Pressure) ratings indicate the maximum pressure the valve can handle under normal or cold-temperature conditions.
It’s essential to look for these markings in the correct places on the valve body to ensure they correspond to the right specifications for your application.
Matching Pressure Ratings to Your Actual Application
One of the most important steps in interpreting valve markings is ensuring that the pressure ratings match the requirements of your specific application. Here are some key points to consider:
WOG Rating: For example, a valve with a 200 WOG rating means that it can safely handle up to 200 PSI of pressure. Ensure that the operating pressure in your system does not exceed this rating, as exceeding the rating could cause valve failure, leakage, or unsafe conditions.
SWP Rating: The Standard Working Pressure (SWP) is used to determine the maximum pressure that can be sustained under normal operating conditions. Always check that the SWP rating aligns with the operating pressures of your system to avoid overloading the valve.
CWP Rating: If your system operates in extremely cold conditions, ensure that the valve’s Cold Working Pressure (CWP) rating matches the expected temperature and pressure conditions of the application. Cold temperatures can affect valve performance and material integrity, so matching the CWP rating is especially crucial in outdoor or refrigerated systems.
Tip: If you’re unsure whether the pressure rating aligns with your system’s needs, it is always safer to consult with a valve expert or manufacturer. Overestimating the pressure requirements could result in unnecessary costs, while underestimating them could compromise safety.
Combined with the Instruction Manual
Valve markings provide essential information, but for a comprehensive understanding of the valve’s capabilities and limitations, it’s essential to refer to the instruction manual. The instruction manual typically includes:
Explanation of Markings: The manual will clarify the meaning of each marking on the valve, helping to ensure you’re interpreting the valve’s specifications correctly.
Correct Application: The manual provides details on which applications the valve is suitable for, ensuring that you are using it in the right environment (e.g., water, oil, gas, etc.). This is especially important if the valve has multiple use cases, like being rated for both oil and water.
Maintenance Considerations: Regular maintenance is key to ensuring the valve’s longevity and optimal performance. The manual typically offers guidance on recommended inspection intervals, cleaning procedures, and how to detect early signs of wear or failure.
Safety Precautions: Most manuals also include essential safety warnings related to pressure limits, handling, and installation to prevent accidents during valve operation.
Conclusion
By choosing valves with the correct pressure ratings and certifications, you ensure the reliability and longevity of your fluid or gas system. Always remember that correct ball valve selection is critical to your system’s overall efficiency and safety.
FAQ
What does WOG mean on a ball valve?
WOG stands for Water, Oil, and Gas, indicating the maximum pressure a valve can safely handle for these specific media (water, oil, or gas). It’s a common pressure rating stamped on ball valves to ensure they are suitable for certain types of fluid systems.
What is the difference between SWP and CWP?
SWP (Standard Working Pressure) refers to the maximum pressure a valve can handle under normal operating conditions, while CWP (Cold Working Pressure) indicates the maximum pressure the valve can safely withstand at low temperatures, such as in freezing conditions.
What does NPT mean on a valve?
NPT (National Pipe Thread) refers to a type of tapered pipe threading used in the United States. This threading is designed to create a tight, leak-proof seal when valves are connected to pipes in plumbing or industrial systems.
How do I know if a valve is suitable for my application?
Always check the valve’s WOG rating, material type, and pressure ratings (such as SWP or CWP) to ensure it matches the requirements of your system. If you are unsure, consult the valve’s instruction manual for more details on compatibility and application guidelines.
Can I use a valve with a higher pressure rating than my system needs?
Yes, you can use a valve with a higher pressure rating, but it may be unnecessary and could increase costs. The key is to match the valve’s rating to your system’s operating conditions, so there is no risk of failure due to excessive pressure.
What do ANSI and API markings on a valve mean?
API (American Petroleum Institute) markings signify that the valve adheres to strict standards set for the oil and gas industry, typically designed to withstand high-pressure and harsh conditions.