Ball valves are crucial in fluid control systems, offering precise flow regulation for liquids and gases. Their open and closed positions significantly impact system efficiency, pressure regulation, wear and tear, energy consumption, and safety. When open, ball valves allow full flow, maintaining steady pressure with minimal resistance, ideal for high-flow systems. In contrast, the closed position isolates sections of the system, preventing leaks, controlling pressure, and ensuring safety.
What Happens When the Ball Valve is Open?
Understanding the Ball Valve Open Position
A ball valve is designed with a spherical ball inside the valve body that has a hole (port) through its center. When the valve handle or actuator is turned to the open position, the hole aligns with the fluid path, allowing the fluid to pass through freely. This simple mechanism is what makes the ball valve highly effective for controlling fluid flow in both on/off and flow-regulation applications.
In its open position, the ball valve operates as a nearly unobstructed passage for fluid to move through. The size of the port, the flow path, and the ball’s material all contribute to how efficiently fluid can pass through the valve. The open position is the default setting for many applications, providing continuous flow and facilitating the desired system operation.
How the Open Position Affects Fluid Flow and System Dynamics
Full Flow Path: When the ball valve is fully open, the fluid path is essentially wide open, and the system experiences minimal resistance to flow. The fluid can move through the valve without significant pressure loss or turbulence. The valve essentially becomes a straight-through conduit.
Minimal Pressure Drop: One of the major advantages of a ball valve in the open position is the minimal pressure drop it causes across the valve. Since the ball’s hole directly aligns with the fluid path, it creates very little friction or resistance. This makes ball valves ideal for high-flow systems where maintaining consistent pressure is crucial.
Impact on System Pressure: While the open position of a ball valve allows for fluid to flow freely, it also has an indirect impact on the system’s overall pressure regulation. If multiple valves are open within a system, the flow rate can increase, which might result in changes in pressure depending on the size of the pipes, the fluid viscosity, and the capacity of the pump. Understanding how each ball valve interacts with the system’s pressure dynamics is essential for efficient operation.
Fluid Velocity Control: The flow rate can be influenced not just by the ball valve itself, but also by factors like the size of the valve’s opening, the viscosity of the fluid, and the pressure at which the fluid enters. In larger valves with wide ports, the fluid velocity is higher, while smaller ports restrict the flow and reduce the velocity.
Bypass or Full-Open Configurations: In some systems, ball valves may be used in bypass configurations, allowing a small fraction of the total flow to pass through while the rest is directed elsewhere. Even in these setups, the open position allows the flow to bypass certain system components without a significant reduction in overall system performance.

The Role of Ball Valve Open in Flow Control and Pressure Regulation
Flow Regulation in Open Position: Although ball valves are typically known for their simple on/off function, some ball valves are designed with special features to regulate flow even when in the open position. These features may include V-port ball valves or valves with adjustable actuators that allow for more precise control over the flow rate. For instance, a partially open valve can create a regulated amount of fluid flow through the system, balancing the system’s need for flow and pressure.
Maintaining System Pressure: In open position, ball valves can help maintain pressure by providing an unrestricted flow path. However, the pressure throughout the system may change if the valve is not properly sized or if it is used in a large, complex network of valves and pipes. It’s important to ensure that the system as a whole is balanced and that the open position of the ball valve doesn’t lead to fluctuations in pressure that could harm the system or cause inefficiency.
Isolation vs. Open Flow: While the open position provides unrestricted flow, it also means that the valve is not isolating any part of the system. This can be both a benefit and a drawback, depending on the context. In certain situations, you may want to isolate sections of the system for maintenance, safety, or regulation. Ball valves can help facilitate that by fully closing when needed, but in the open position, they offer continuous flow with no isolation.
Pressure Balancing: In many systems, pressure regulators are used in conjunction with ball valves to control downstream pressure. When a ball valve is open, the pressure regulator must adjust to the flow rate to keep the pressure within the desired range. The ball valve’s open position helps allow for this regulation by offering a stable, non-restricted flow path for the fluid to pass through.
Shutting Off Flow for Maintenance: In certain applications, the ball valve may be part of a larger system where it serves not only to allow flow but also to shut off sections of the system during maintenance. The open position ensures that the system can operate as needed, while the closed position allows for necessary repairs or inspections without disrupting the rest of the system.
Efficiency and Energy Conservation: Maintaining proper fluid flow through an open ball valve can help improve the overall energy efficiency of the system. By minimizing resistance and pressure drops, the pump or compressor downstream can run more efficiently, conserving energy and lowering operational costs. Properly controlling the open position ensures that the fluid moves smoothly without unnecessary friction, allowing the entire system to function more efficiently.
Control Over Flow Volume: The size of the ball valve and its opening can also be adjusted to control the volume of fluid flowing through the system. Larger ball valves allow more flow, while smaller ball valves limit the volume. This flexibility is important in applications where specific flow rates are necessary for optimal system function, such as in cooling systems, water treatment, or chemical processing.
The Ball Valve Closed Position: The Power of Isolation
Ball Valve Closed Position Explained
The ball valve’s closed position is just as crucial as its open position, if not more so in certain applications. When a ball valve is turned to the closed position, the hole in the ball rotates 90 degrees, so it no longer aligns with the flow path. This creates a tight seal, effectively stopping the flow of fluid through the valve. In this state, the ball valve isolates the portion of the system downstream of the valve, preventing fluid from passing through.
In its closed position, the ball valve is typically used for shutting off the flow completely, allowing for maintenance, system shutdown, or isolating sections of the system to control pressure or prevent backflow. Whether manually or automatically operated, the ball valve’s ability to close tightly is essential for system control and safety.
Preventing Fluid Flow: How the Closed Position Works
Fluid Isolation: In the closed position, the ball valve provides a nearly perfect seal that prevents fluid from flowing through the valve. This is ideal when you need to shut off the flow of fluids in piping systems for maintenance, repairs, or emergencies. With the ball positioned perpendicular to the flow direction, it acts as an impenetrable barrier.
Pressure Containment: When closed, the ball valve serves as a pressure containment feature. In many systems, the valve is used to isolate sections of the pipeline under pressure, enabling operators to safely work on other parts of the system without worrying about fluid leakage or pressure loss.
Quick Shutoff Capability: One of the biggest advantages of a ball valve in the closed position is its ability to shut off fluid flow very quickly. Unlike other valve types that may require multiple turns or complex operations, the ball valve’s quarter-turn motion makes it ideal for rapid on/off control. This quick shutoff is particularly important in emergency situations or when precise control over fluid flow is needed.
No Flow Through the Valve: The design of the ball valve ensures that when it is closed, no fluid can bypass the ball. The ball itself is perfectly aligned with the valve seat, and the seal around the valve is engineered to prevent any leakage, even under high pressure. This absolute isolation is one of the key benefits of using ball valves in fluid handling systems.
The Importance of Seal Integrity in the Closed Position
Prevention of Leaks: The primary function of the closed position in a ball valve is to prevent leaks and fluid bypass. For this to work effectively, the integrity of the valve seals is critical. The ball valve’s seals, including the stem seals and seat seals, must remain intact to ensure a tight shutoff. If these seals wear out or become damaged, the valve will not be able to close properly, potentially leading to fluid leakage and system inefficiency.
Maintaining Pressure and Safety: Seal integrity is crucial in maintaining the safety and pressure integrity of the system. A compromised seal can result in a slow leak, leading to pressure drops or potentially hazardous situations, especially in systems that handle dangerous or high-pressure fluids. If the seals fail, it can also cause increased wear on the valve and other system components.
Material Selection for Seals: The material of the seals in the ball valve must be chosen based on the type of fluid being handled and the pressure and temperature conditions. Common seal materials include rubber, PTFE, and various elastomers. If these materials degrade due to exposure to certain chemicals, extreme temperatures, or high-pressure conditions, the valve’s ability to seal completely in the closed position will be compromised.
Regular Maintenance for Seal Integrity: To maintain proper isolation and prevent leaks in the closed position, regular maintenance and inspection of the valve seals are essential. This includes checking for wear, cracking, or signs of chemical degradation. Replacing worn-out seals can restore the valve’s functionality and help avoid costly system shutdowns or safety risks.
The Role of Seal Seating: Proper seating of the valve’s ball against the valve seat is vital for achieving an effective closed position. Over time, the seating area can experience wear due to the constant opening and closing of the valve, leading to an imperfect seal. Regular inspection and re-lubrication of the valve seats can help extend their lifespan and maintain reliable sealing performance.
The Mechanics Behind Ball Valve Operation
How Ball Valves Function: The Quarter-Turn Mechanism
The simplicity and effectiveness of the ball valve lie in its quarter-turn operation. This mechanism allows the valve to quickly switch between fully open and fully closed positions with a 90-degree rotation of the valve handle or actuator.
Basic Operation: The ball valve contains a hollow, perforated sphere (the ball) inside its valve body. When the valve is in the open position, the hole in the ball aligns with the flow path, allowing fluid to pass through. In the closed position, the ball is rotated 90 degrees so that the hole is perpendicular to the flow, effectively blocking any passage of fluid.
Speed of Operation: One of the biggest advantages of the quarter-turn mechanism is its speed. Unlike multi-turn valves that require multiple rotations to fully open or close, the ball valve’s quick, 90-degree turn allows for fast and efficient on/off control, which is particularly valuable in applications where time-sensitive shutoff is critical.
Sealing Function: The quarter-turn design also ensures a reliable sealing mechanism. As the ball moves to the closed position, the internal valve seat presses against the ball, creating a tight seal that prevents leakage. The material of the seat and the ball’s surface (often made of PTFE, stainless steel, or other high-quality materials) ensures that this seal remains effective even in demanding environments.
Minimal Maintenance: Due to the straightforward mechanism and the lack of complex internal moving parts, ball valves typically require less maintenance compared to other valve types. The ball’s simplicity reduces wear and tear, making it more durable for long-term use.
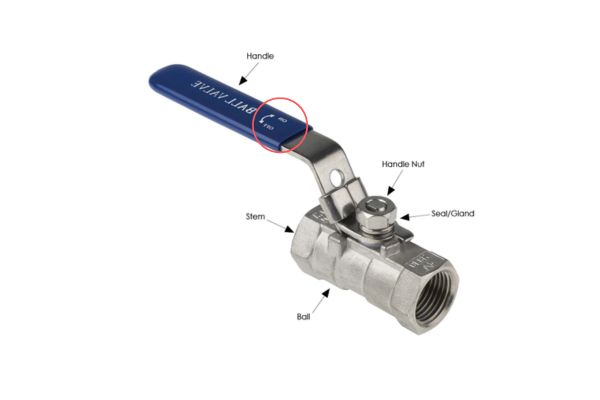
Valve Actuation: Manual vs. Automated Ball Valves
Ball valves can be operated manually or automatically, depending on the needs of the system. The choice between manual and automated actuation can have a significant impact on the valve’s operation and the overall efficiency of the system.
Manual Actuation:
Hand Lever: The most common manual actuator is the lever or handle, which allows operators to manually open or close the valve by turning it a quarter turn. This is ideal for smaller systems or situations where infrequent adjustments are needed.
Operator Control: Manual operation provides the operator with direct control over the valve, allowing for quick adjustments based on real-time system requirements. However, manual valves may not be practical for systems requiring frequent or precise adjustments.
Automated Actuation:
Electric Actuators: For larger systems or where automated, remote control is necessary, electric actuators are commonly used. These actuators can open or close the valve by sending an electric signal, allowing for more precise and frequent adjustments.
Pneumatic and Hydraulic Actuators: These types of actuators use compressed air or hydraulic pressure to operate the valve. Pneumatic actuators are often chosen for their speed and reliability in systems with high-pressure fluids.
Integration with Control Systems: Automated ball valves are often integrated into more complex control systems, enabling remote operation and monitoring, which is ideal for processes that require continuous or regulated flow control.
Selection Considerations: When choosing between manual and automated ball valves, the decision depends on factors like system size, frequency of operation, cost, and the level of control required. Automated valves offer higher precision and convenience but at a higher initial cost, while manual valves are more economical and suitable for less frequent use.
Fluid Flow Control with Ball Valves
Managing Fluid Flow
Flow Control in the Open Position:
When a ball valve is in the open position, it provides a full, unobstructed path for fluid to flow through. The size of the ball valve’s port determines the volume of fluid that can pass through. Larger ports allow higher flow rates, while smaller ports restrict flow, making ball valves versatile in applications where flow regulation is needed.
Ball valves are often used for on/off control rather than for fine modulation of flow. However, certain designs, such as V-port ball valves, can enable partial flow control even when the valve is open, allowing for a more regulated flow in specific applications.
Impact on System Flow: The flow characteristics of the system can change significantly when transitioning from the closed position to the open position. Fluid dynamics, such as velocity and pressure, can be adjusted by fine-tuning the valve size and the flow direction.
Flow Restriction in the Closed Position:
When the ball valve is in the closed position, fluid flow is completely stopped, isolating the downstream or upstream sections of the system. This isolation is crucial for maintenance, system shutdown, and controlling pressure.
Shutoff Capability: The ball valve’s quick shutoff function allows it to be used effectively in applications where the ability to stop fluid flow immediately is necessary for safety, system control, or pressure management.
Adjusting Flow with Partial Openings:
Some ball valves, especially those designed with specialized ports (e.g., V-port), can allow for controlled flow even when the valve is not fully open. These valves are used in situations where precise flow regulation is needed but still rely on the general principle of the ball valve’s simple open/close mechanism.
Flow Control in Industrial Systems: In more complex systems, partial openings can provide just enough flow to meet the operational needs without overloading the system, optimizing overall performance.
The Role of Ball Valve in Controlling Fluid Pressure
Pressure Drop and Ball Valve Performance:
In the open position, ball valves have a minimal pressure drop due to their smooth, straight-through flow path. This is one of the reasons why ball valves are preferred in high-flow, low-pressure loss applications.
However, when the valve is partially closed or completely closed, pressure can build up upstream of the valve. If the valve is not sized correctly for the system, excessive pressure could lead to system failures or damage to the valve itself.
Pressure Regulation with Ball Valves:
Ball valves are often used in pressure-sensitive applications, and their positioning can have a significant impact on the fluid pressure in a system. By shutting off fluid flow in the closed position, the valve helps prevent the system from exceeding its desired pressure limits.
Safety and Control: Proper valve positioning ensures that the system operates within the desired pressure range. If the valve’s seals are in good condition and it is correctly aligned with the system, it can provide effective pressure regulation.
Application in High-Pressure Systems:
In high-pressure fluid systems, ball valves with reinforced bodies and seals are often used to manage and control pressure. The closed position of the valve can stop excessive pressure buildup, isolating the system or redirecting fluid flow to reduce risk of leaks, system bursts, or catastrophic failure.
Pressure Relief Systems: In conjunction with pressure relief valves, ball valves help ensure that pressure does not rise to dangerous levels. This is vital in systems handling volatile or hazardous fluids.
Control of Backpressure:
Ball valves can also be used in controlling backpressure, which is the pressure exerted by fluid in a downstream system when the valve is closed. Proper valve positioning helps maintain a balanced system pressure, preventing undesirable pressure spikes that could compromise the entire system’s integrity.
Optimizing Fluid Flow with Proper Valve Positioning
Achieving Optimal Flow with the Right Position:
Ensuring that a ball valve is in the correct open or closed position is essential for optimizing fluid flow in a system. While the open position allows for unrestricted flow, the closed position stops the flow to isolate sections of the system for maintenance, repair, or testing.
Partial Open Positioning for Flow Control: For applications requiring fluid regulation, ball valves with precise adjustments in the partially open position can provide the optimal flow rate while maintaining system efficiency. This is particularly important in processes requiring precise dosing, mixing, or cooling.
Valves with Flow Control Ports: Ball valves with specially designed ports, like the V-port or multi-port ball valves, allow for a more gradual adjustment of flow without requiring a fully open or closed position. These types of valves provide more nuanced control over the flow rate, optimizing performance in systems where regulation is necessary.
The Impact of Correct Valve Positioning on System Efficiency:
Correct valve positioning not only optimizes fluid flow but also improves energy efficiency in fluid handling systems. When the valve is open, the reduced pressure drop allows the system to operate with less energy consumption, while the closed position ensures that pressure is maintained at safe levels, preventing energy losses from overpressure situations.
Avoiding Cavitation and Flow Noise: Improper valve positioning can cause cavitation or flow noise due to turbulent flow. Ensuring the ball valve is in the optimal position for your application can mitigate these issues and promote smoother flow, improving both system lifespan and performance.
Flow Control in Complex Systems:
In larger, more complex systems, ensuring proper valve positioning is key to optimizing flow throughout the network. Multiple ball valves may be needed to control flow in different areas, and their correct positioning in relation to one another ensures that each section operates efficiently without causing flow disruption or pressure imbalance.
System Performance Monitoring:
Regular monitoring of ball valve positions helps identify any issues early on. A malfunctioning valve or a valve that is not correctly positioned can lead to inefficient fluid flow, pressure loss, or unnecessary wear and tear on system components.
Conclusion
To maximize performance, it’s important to select the right ball valve size, perform regular maintenance, install valves correctly, monitor seal integrity, and consider automated actuators for precise control. Understanding and maintaining ball valve operation enhances system efficiency, reliability, and safety, reducing downtime and costly repairs while ensuring long-term performance.
FAQ
What is the difference between an open and closed ball valve?
An open ball valve allows fluid to pass through as the ball’s hole aligns with the flow path. A closed ball valve blocks the flow by turning the ball, so the hole is perpendicular to the flow path.
How does the open position of a ball valve impact fluid flow?
In the open position, a ball valve provides a clear, unobstructed path for fluid to flow, enabling maximum throughput with minimal pressure loss, ideal for on/off control in systems.
When should I use a ball valve in the closed position?
The closed position is used to isolate sections of a system, prevent fluid flow during maintenance, or regulate pressure. It’s essential for shutoff and safety in fluid handling systems.
Can a ball valve control fluid flow when partially open?
Yes, certain types of ball valves, such as V-port valves, allow for partial flow control even when not fully open. However, ball valves are primarily designed for on/off control rather than fine modulation.
How do I ensure my ball valve operates effectively?
Regular maintenance, proper installation, correct valve sizing, and monitoring of seal integrity are crucial for ensuring optimal operation of your ball valve in any position.
What factors affect ball valve performance in open vs closed positions?
Flow rate, pressure, valve size, and seal quality all influence ball valve performance. The open position maximizes flow, while the closed position provides effective isolation and pressure regulation.