The specifications define the physical and operational characteristics of the valve, such as pressure ratings, temperature limits, materials used, and size options. These details ensure that the valve can perform effectively and safely in its intended application.
The Basics of Ball Valve Standard Specification
What Does “Ball Valve Standard Specification” Mean?
Ball valve standard specification refers to the set of guidelines, requirements, and parameters that define the design, materials, performance, and testing criteria for a ball valve. These specifications ensure that the valve meets a certain level of quality and reliability, regardless of the manufacturer or location. Standard specifications include key details like pressure ratings, material types, valve sizes, temperature limits, and flow characteristics, all of which play a critical role in the performance and safety of the valve in its intended application. Adhering to these specifications ensures consistency, interchangeability, and compliance with industry safety and operational standards.
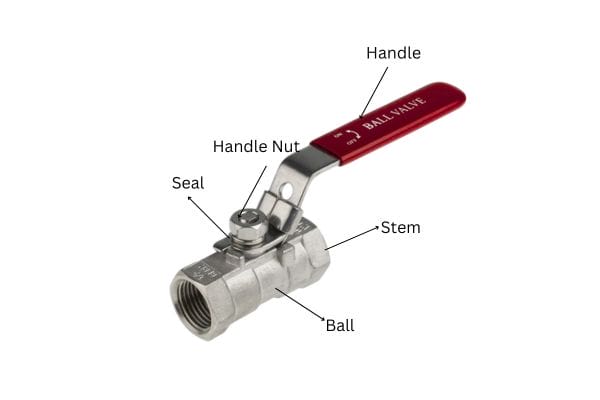
Overview of Common Valve Standards (ANSI, ISO, API)
ANSI Standards (American National Standards Institute): ANSI standards provide guidelines for the design, materials, and performance characteristics of ball valves used in various industries, especially within the United States. These standards help ensure that valves are manufactured to be safe, reliable, and compatible with other components in the system. Key ANSI standards for ball valves include ANSI B16.34, which outlines the dimensions, materials, and pressure-temperature ratings for valves.
ISO Standards (International Organization for Standardization): ISO standards are internationally recognized and are used for ball valves in global industries. The most relevant ISO standard for ball valves is ISO 17292, which covers design, construction, testing, and materials for valve performance. These global standards help ensure uniformity and compatibility across international markets and industries.
API Standards (American Petroleum Institute): API standards focus on valves used primarily in the oil and gas industry, specifying requirements for safety, materials, pressure ratings, and operational performance. API 6D is the most widely known standard, detailing the specifications for pipeline valves, including ball valves. These standards ensure that the valves used in critical and high-risk industries meet the required safety and performance levels.
How Standards Ensure Safety and Performance
Ball valve standards play an essential role in ensuring safety, reliability, and performance in various industrial applications. Here’s how they work:
Safety: Standards ensure that the valves are built to withstand the pressures, temperatures, and environmental conditions they will face during operation. This reduces the risk of failures that could lead to catastrophic incidents, such as leaks, explosions, or contamination. By defining materials, pressure ratings, and sealing performance, standards ensure that the valves operate safely within their designed limits.
Quality Assurance: Adhering to established standards guarantees that ball valves are manufactured with consistent quality. This includes using the right materials, maintaining proper tolerances, and performing necessary quality control checks during production. Standards help eliminate variations in valve quality that could affect system performance or lead to premature failures.
Interchangeability and Compatibility: When valves meet standardized specifications, they can be easily replaced or integrated into existing systems without needing extensive modifications. This ensures that components from different manufacturers will work together seamlessly, minimizing downtime and improving operational efficiency.
Performance Reliability: Standard specifications also define the operational characteristics of the valve, such as flow rate, leakage performance, and pressure limits. By adhering to these standards, manufacturers ensure that the ball valves will function as expected, providing efficient flow control, minimal leakage, and long-term durability.
Testing and Certification: Valve standards often include specific testing procedures to ensure the valve meets performance criteria before it is used in service. This may include pressure testing, material testing, and sealing tests to ensure the valve’s reliability under real-world conditions. These tests help identify defects and ensure that each valve operates safely and efficiently according to its specifications.
Key Elements of Ball Valve Specifications
Valve Pressure Ratings: What You Need to Know
Valve pressure ratings define the maximum pressure a ball valve can handle while maintaining safe and reliable operation. Understanding the pressure rating is crucial for selecting the right valve for your system. Ball valves are typically rated based on their ability to withstand certain pressure classes, such as:
Class 150, 300, 600, etc. (ANSI standards): These classes indicate the maximum pressure a valve can handle at a specific temperature. For instance, a Class 150 valve can typically handle pressures up to 285 psi (at 100°F), whereas a Class 600 valve can withstand up to 1,480 psi.
PN Ratings (ISO standards): In the international context, valves are often rated using Pressure Nominal (PN) values, which refer to the maximum pressure the valve can handle at a given temperature. For example, PN 16 indicates a maximum working pressure of 16 bar (around 232 psi).
Selecting the correct pressure rating is essential for preventing valve failure, as exceeding the rating can cause leaks, cracks, or complete valve rupture. Always choose a valve with a pressure rating higher than the system’s maximum operating pressure to account for fluctuations and safety margins.
Ball Valve Sizes and Their Impact on Performance
Ball valve size is a critical factor that influences the performance of a system. The size of the valve determines the flow capacity, installation requirements, and how effectively it controls fluid or gas flow. Common factors related to size include:
Nominal Pipe Size (NPS): This is the standard measurement used for ball valve sizes, corresponding to the diameter of the pipeline in which the valve will be installed. Ball valves come in a range of sizes, from small (1/4 inch) to large (up to 24 inches or more).
Flow Capacity: The size of the ball valve directly impacts its ability to control flow. Larger valves allow for higher flow rates but can also create more resistance in the system if not correctly sized. Too large a valve can cause excessive turbulence or energy loss, while too small a valve may result in inadequate flow or excessive pressure.
Connection Types: The size of the valve also affects the type of connection required (e.g., threaded, flanged, or welded). This must be considered during installation to ensure compatibility with the system.
Understanding Valve Performance and Flow Control
How Ball Valves Control Flow in Different Systems
Ball valves control flow by utilizing a spherical ball with a hole or bore through the center. When the valve handle is turned, the ball rotates, aligning the hole with the pipeline to allow fluid to flow, or rotating it perpendicular to the pipeline to block the flow. The simplicity of this design makes ball valves particularly effective for on/off flow control, though they can also be used for throttling in some cases. Here’s how they control flow in different systems:
On/Off Control: The most common use of a ball valve is to provide a quick and reliable shut-off mechanism. The quarter-turn design allows operators to quickly stop or start the flow of fluids or gases, making it ideal for emergency shutdowns or maintenance.
Throttling: Although traditionally used for on/off control, ball valves can also regulate flow (throttling) by partially opening or closing the valve. However, ball valves are generally less effective for throttling compared to other valves like globe valves, as the flow characteristics may become unstable at low openings.
Multi-Flow Control: In advanced systems, specially designed ball valves can be used to control multiple fluid paths or varying flow rates. Some ball valves come with multiple ports or V-port designs to adjust flow in precise amounts.
Ball valves are particularly beneficial in systems that require quick, efficient, and reliable flow control. However, they are better suited for full open or closed states, and their throttling capabilities are limited compared to other valve types.
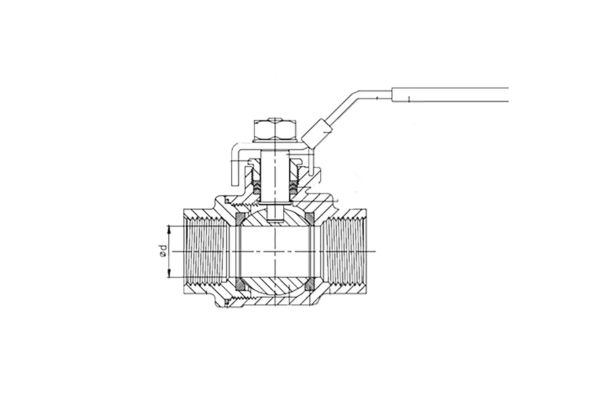
The Impact of Valve Design on Flow Efficiency
The design of a ball valve directly influences its flow efficiency, and several factors must be considered when determining the right valve for optimal performance:
Full-Bore vs. Reduced-Bore Design: Full-bore ball valves have a bore diameter that matches the pipe’s diameter, allowing fluid to flow with minimal restriction. This design maximizes flow efficiency, minimizes turbulence, and reduces pressure drop. Reduced-bore ball valves, however, have a smaller bore diameter and can create more resistance to flow, leading to higher energy consumption and less efficient performance in certain systems.
Flow Path Smoothness: The smoother the ball’s surface and the seat area, the less resistance the fluid will face as it flows through the valve. A rough surface can cause friction, turbulence, and energy loss. Therefore, smooth internal components are essential for maintaining high flow efficiency.
Port Configuration: Ball valves come in different port configurations—1-way, 2-way, 3-way, or multi-way ports. The number of ports and their alignment affect how the fluid flows through the valve and how effectively the valve can manage multiple flow paths. For example, a 3-way valve can manage more complex flow control, which is often needed in manifold systems.
The key to achieving the highest flow efficiency lies in choosing the right valve design based on the application’s flow rate, pressure, and fluid type.
Achieving Optimal Flow Control with the Right Ball Valve Specifications
Achieving optimal flow control involves selecting a ball valve that is correctly specified to match the specific needs of the system. Here’s how you can achieve that:
Correct Sizing: A ball valve that is too small for the system can cause excessive pressure drops, while one that is too large can result in wasted energy and inefficient flow. Sizing the valve correctly is key to maintaining a smooth flow rate with minimal energy loss.
Pressure Rating Alignment: Ensure that the ball valve’s pressure rating aligns with your system’s operating pressure. A mismatch can lead to valve failure or improper flow control.
Material Selection: The materials of both the ball and the seat are crucial for flow control. Selecting materials that are chemically compatible with the fluid being transported ensures that the valve will operate efficiently without degradation or corrosion, which can impede flow.
Flow Coefficient (Cv Value): The Cv value represents the valve’s flow capacity. A higher Cv indicates a higher flow rate for a given pressure drop. When selecting a ball valve, consider its Cv value to match the system’s required flow characteristics.
Actuation and Automation: For systems that require fine-tuned flow adjustments, automated ball valves with actuators can provide precise control. Using actuators with integrated controllers or feedback mechanisms allows for better regulation of flow based on real-time system demands.
Selecting the Right Ball Valve for Your Application
Valve Selection Guide
When selecting the right ball valve, understanding your application’s specific requirements is critical. This ensures the valve operates efficiently, safely, and lasts as long as possible. Here’s how to select the perfect valve based on key factors:
Flow Requirements:
Full-Bore vs. Reduced-Bore: For high-flow systems or applications requiring minimal pressure drop, a full-bore ball valve is often preferred. It ensures maximum flow capacity by maintaining a pipe-diameter-sized opening. For smaller systems or when space is constrained, reduced-bore ball valves can be used, but they may cause higher pressure drops.
Throttling Needs: If your application requires flow control (not just on/off), you may want to opt for a valve with a V-port or specially designed ball valve, as these provide better throttling capabilities.
Pressure Requirements:
Every system has a maximum operating pressure, and it’s essential to choose a valve that can handle it without risk of failure. Valve pressure ratings come in different classes (e.g., ANSI Class 150, 300, 600) and are available in different pressure ratings according to materials and design. Always select a valve with a higher pressure rating than your system’s maximum to provide a safety margin.
Application Type:
General Industry: For standard applications like water, air, or low-viscosity fluids, most standard ball valves will work.
Chemical and Corrosive Fluids: For applications involving corrosive chemicals or gases, you’ll need a ball valve with corrosion-resistant materials (e.g., stainless steel, PTFE seats, or specialized coatings) to ensure longevity.
High-Temperature Applications: If you’re working in environments where high heat is common (e.g., steam or hot oils), ensure the valve is rated for high-temperature resistance, typically made with materials like Monel or Hastelloy.
By considering these factors—flow rate, pressure, and application type—you can narrow down your valve options and ensure reliable, long-term performance.
Understanding Valve Certifications for Quality Assurance
Valve certifications act as proof that the valve adheres to required safety, material, and operational standards. These certifications provide assurances about the valve’s quality, durability, and compliance with industry regulations. Key certifications to be aware of:
ISO Certification
ISO 9001: This certification indicates the manufacturer follows quality management practices to ensure consistent, high-quality products.
ISO 17292: A key standard for ball valves, this certification ensures that valves meet the necessary performance, design, and material specifications.
API Certification:
The American Petroleum Institute (API) offers specific certifications, such as API 6D, for valves used in pipeline applications. This certification ensures that the valve meets the performance standards required for the oil and gas industry.
ANSI Compliance:
ANSI B16.34 is one of the primary standards for valve design, covering pressure, temperature, material specifications, and dimensions. This ensures valves can withstand varying conditions and maintain consistent performance.
CE Marking:
In Europe, the CE Mark indicates compliance with European Union safety and environmental standards, making it necessary for valves used in specific industrial sectors.
FDA Approval:
For food-grade or pharmaceutical applications, a ball valve may need to meet FDA requirements to ensure it does not contaminate products and maintains hygienic conditions.
Matching Valve Specifications to Your Specific Needs
The final step in selecting the right ball valve is ensuring that the valve’s specifications align with the specific requirements of your system. This ensures efficient, safe, and reliable operation. Key considerations when matching valve specifications to your needs:
Pressure and Temperature Compatibility: Always match the valve’s pressure rating with your system’s maximum operating pressure. Additionally, ensure the valve material and design can handle the temperature extremes your system experiences.
Size and Flow Matching: Properly size the valve based on the pipe diameter and the required flow rate. Using a valve that’s too small can result in excessive pressure drops, while a valve that’s too large may waste energy and lead to inefficiencies.
Material Compatibility: Consider the chemical properties of the fluids or gases passing through the system. Choose materials that are resistant to corrosion, abrasion, or other potential damage from the fluid. For aggressive chemicals, materials like 316 stainless steel or PTFE are often used.
Seal and Seat Selection: Match the valve’s seals and seats to the fluid type and operating conditions. For example, if the fluid is highly abrasive or corrosive, metal seats or fluoropolymer seals may be required. For food or pharmaceutical applications, look for valves with FDA-approved seals and materials.
Environmental Considerations: If the valve is being used in an outdoor or extreme environment, ensure it’s rated for weather resistance. IP (Ingress Protection) ratings or NEMA ratings may be important if the valve is exposed to moisture, dust, or corrosive environments.
Conclusion
In summary, understanding ball valve specifications is critical not only for achieving optimal system performance today but also for staying ahead of future developments in valve technology and standards. As we look ahead, the industry is moving toward smarter, more efficient, and more sustainable valve solutions that will continue to enhance safety, reduce costs, and improve overall performance.
FAQ
What is a ball valve and how does it work?
A ball valve is a valve with a spherical ball inside that controls the flow of liquids or gases. When the valve handle is turned, the ball rotates, either allowing or blocking the flow depending on its alignment with the pipeline.
How do I determine the right size of ball valve for my system?
To choose the correct size, you need to match the valve size to your pipeline’s diameter and ensure that it supports the required flow rate and pressure of your system. A valve that’s too large or too small can affect performance.
What materials are commonly used in ball valves?
Common materials include stainless steel, carbon steel, brass, and various alloys. The material selection depends on the type of fluid, temperature, pressure, and the need for corrosion resistance in your application.
What is the difference between full-bore and reduced-bore ball valves?
A full-bore ball valve has an internal diameter that matches the pipeline size, allowing for unrestricted flow, while a reduced-bore valve has a smaller opening, which may cause increased pressure drops but can be used in specific flow control applications.
How do valve pressure ratings affect ball valve selection?
Valve pressure ratings define the maximum pressure a ball valve can handle. Ensure the valve’s pressure rating meets or exceeds the system’s maximum pressure to avoid damage or failure. Always select a valve with a safety margin.
Why are certifications like ISO or API important for ball valves?
Certifications ensure that the ball valve meets global safety, quality, and performance standards. Valves with recognized certifications like ISO, API, or ANSI are guaranteed to be reliable and safe for their intended application.