Choosing the right ball valve size is pivotal in ensuring that your piping system operates efficiently and effectively. Ball valves help maintain optimal flow rates, pressure control, and seamless system operations when sized correctly. The right valve allows fluids to move through the system without resistance, ensuring smooth functionality, reducing wear and tear, and preventing energy losses.
What is Ball Valve Sizing and Why Does it Matter?
Defining Ball Valve Size
Ball valve sizing refers to the process of determining the appropriate valve dimensions required for a particular piping or fluid control system. It’s not just about picking a valve that physically fits, but rather selecting one that can effectively handle the system’s flow rates, pressures, and specific operational demands. The critical dimensions and parameters you’ll need to consider when measuring ball valve size include:
Valve Bore Size: The valve bore (also known as the port size) is the internal opening through which the fluid flows. The bore size directly impacts the flow capacity of the valve and is often the most important factor in sizing a ball valve.
Nominal Pipe Size (NPS) and Diameter Nominal (DN): These two measurements refer to the size of the pipe the valve is designed to fit into. NPS is commonly used in the United States, while DN is the metric equivalent used in other parts of the world. These measurements are key to ensuring that the valve connects seamlessly to the piping system.
Valve Body Size: The valve body size refers to the overall size and shape of the valve housing. This dimension affects how well the valve fits within the system and influences factors like weight, material selection, and flow dynamics.
Flow Coefficient (Cv): The Cv value indicates the valve’s flow capacity. It measures how much liquid (usually water) can pass through the valve at a specific pressure drop. Cv is critical in determining whether the valve will be able to handle the required flow rate without causing pressure loss or other system inefficiencies.
Pressure Rating: Each ball valve is designed to handle a specific range of pressures. Choosing a valve that aligns with your system’s pressure requirements is essential to prevent over-pressurization or valve failure.
Valve Seat and Stem Dimensions: The valve seat and stem work together to create a seal that controls the flow. The size and configuration of these parts can affect how tightly the valve seals and its overall performance, especially under high pressure or extreme conditions.
Understanding these key dimensions helps in accurately sizing the valve for your system, ensuring that it functions efficiently, maintains pressure, and supports the flow requirements.
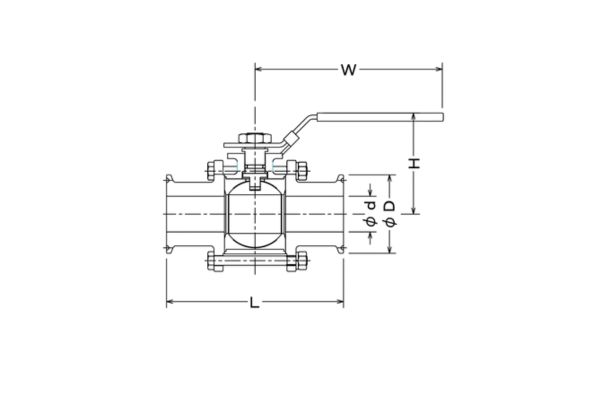
The Role of Ball Valve Sizing in Fluid Control Systems
Proper ball valve sizing plays a critical role in ensuring smooth and efficient operation within any fluid control system. The size of the valve determines its ability to regulate flow, maintain pressure, and perform under different operating conditions. Here’s why ball valve sizing is so crucial:
Ensuring Optimal Flow Rates: Ball valves are often used to control the flow of fluids in pipelines. If the valve is too large or too small, it can either restrict flow or allow too much fluid to pass through, which can create system imbalances, energy inefficiencies, or even damage to equipment downstream. Proper valve sizing ensures that the fluid moves at the right speed and volume, minimizing energy waste.
Maintaining Pressure Control: In pressurized systems, the size of the valve directly impacts the pressure drop (the reduction in pressure as the fluid passes through the valve). Incorrectly sized valves can cause excessive pressure loss, which can damage equipment or disrupt operations. A properly sized ball valve ensures that the pressure remains within acceptable limits and that the system operates safely and efficiently.
Preventing System Strain and Damage: An oversized valve can lead to unnecessary wear, while an undersized valve can place strain on the system as it tries to force fluid through a restrictive passage. Both scenarios increase the likelihood of leaks, equipment failure, and costly repairs. Correct sizing keeps the entire system in balance, reduces maintenance, and prolongs the life of components.
Ensuring Compatibility with System Requirements: Fluid control systems often have unique requirements based on the type of fluid being transported, the temperature, and the pressure conditions. Ball valve sizing ensures compatibility with these variables. For example, the size of the valve may need to be adjusted depending on whether the fluid is a liquid, gas, slurry, or corrosive material.
How to Measure Ball Valve Size: A Step-by-Step Guide
Step 1: Measure the Valve Bore Size (Flow Path)
The first and most critical measurement when determining the size of a ball valve is the valve bore size. This refers to the internal diameter of the valve’s ball or flow path. The bore size dictates how much fluid can pass through the valve at a given time and is directly linked to the valve’s flow capacity.
To measure the valve bore:
Remove the valve from the system: If possible, remove the valve to measure it accurately.
Measure the internal diameter: Using calipers or a micrometer, measure the inner diameter of the valve’s opening (also known as the port size or flow path). This size is usually given in inches or millimeters, depending on the valve’s specification.
Consider the flow rate: Larger bore sizes allow for higher flow rates, making this an important factor if you need the valve to handle large volumes of fluid.
Choosing the correct bore size ensures that the ball valve can handle the system’s required flow rate without causing unnecessary pressure loss or restriction.
Step 2: Determine the Nominal Pipe Size (NPS) vs. Diameter Nominal (DN)
After measuring the valve bore, the next step is to determine the Nominal Pipe Size (NPS) or Diameter Nominal (DN). These terms are used to describe the size of the pipes that the valve will connect to and ensure compatibility between the valve and the piping system.
Nominal Pipe Size (NPS): This is the standard measurement used primarily in the United States. It refers to the approximate internal diameter of the pipe and is usually given in inches (e.g., 1-inch, 2-inch, etc.).
Diameter Nominal (DN): This is the international standard measurement used in metric systems. It corresponds to the same general size as NPS but is given in millimeters (e.g., DN 50 for a 2-inch pipe).
To measure NPS or DN:
Check the pipe’s specification: Review the piping system’s documentation or measure the internal diameter of the pipe using calipers.
Verify compatibility with the valve: The NPS or DN of the pipe should roughly match the valve size to ensure a proper fit. In some cases, slight variations in diameter may be accounted for by using adapters or flanges.
Correctly matching the NPS or DN ensures a leak-proof connection between the valve and the pipe.
Step 3: Measure the Valve Inlet and Outlet
The valve inlet and outlet dimensions refer to the openings where the fluid enters and exits the valve. These are crucial for ensuring the valve is properly sized to connect with your piping system.
To measure the inlet and outlet:
Measure the diameter of each opening: Using a tape measure or calipers, measure the inner diameter of both the valve inlet (where fluid enters) and the outlet (where fluid exits).
Check for consistency: The inlet and outlet should generally be consistent with the nominal pipe size (NPS/DN) of the valve. If they differ, adjustments (such as adapters or reducers) may be needed to maintain system flow.
The inlet and outlet measurements are essential for maintaining consistent flow and pressure throughout the system. Mismatched sizes could lead to turbulence, pressure drops, or inefficiencies.
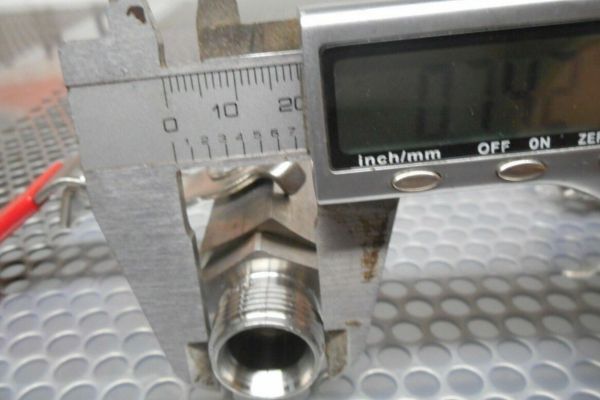
Step 4: Check Valve Pressure Rating and Compatibility
Each ball valve is designed to withstand a certain pressure rating. The pressure rating tells you the maximum pressure the valve can handle safely without risk of failure. Selecting a valve with the correct pressure rating is critical to preventing leaks, burst valves, or other operational failures.
To check the valve’s pressure rating:
Locate the pressure rating on the valve body: Most manufacturers will mark the pressure rating (e.g., 150 psi, 300 psi, etc.) directly on the valve’s body. It may also be listed in the valve’s technical specification sheet.
Consider the system pressure: Ensure that the valve’s pressure rating exceeds or matches the maximum pressure expected in your system.
Check the material compatibility: The material of the valve (e.g., stainless steel, brass) must be able to handle the pressure and the type of fluid being transported. For high-pressure or corrosive systems, ensure you select a valve made from a durable, pressure-resistant material.
Matching the valve’s pressure rating to the system’s needs helps avoid pressure-related failures and ensures safe operation.
Step 5: Assess Valve Seat and Stem Size for Precision
The valve seat and valve stem play a key role in controlling the flow of fluid through the valve. Proper sizing of these components ensures that the valve operates smoothly and maintains an effective seal. The stem size and the seat configuration determine the precision and reliability of the valve’s on/off function.
To assess the valve seat and stem size:
Check the valve seat: The seat is the area where the ball makes contact to form a seal. It should be sized to fit snugly around the ball to prevent leakage. The material of the seat should be compatible with the type of fluid being used, such as metal or soft-seated options.
Measure the valve stem: The stem connects the actuator (manual or automated) to the ball inside the valve. It should be appropriately sized to handle the mechanical force needed to open and close the valve without causing wear or sticking.
Consider the valve type: Depending on the type of valve (e.g., full port or standard port), the seat and stem dimensions may differ. Full port valves have larger openings and typically require a different seat configuration.
How to Calculate the Correct Valve Size for Your System
Valve Size Calculation: How to Match Valve to Pipe Size and Flow Rate
Selecting the right valve size involves carefully matching the valve to both the pipe size and the flow rate requirements of your system. This ensures that the valve operates efficiently, without causing excessive pressure drops or restricting fluid flow.
Step 1: Match Valve to Pipe Size (NPS or DN): Start by determining the Nominal Pipe Size (NPS) or Diameter Nominal (DN) of your system. These measurements give you the general size of the pipe and indicate the size of the valve needed for the connection. Typically, a valve should match the pipe size closely to maintain a smooth flow of fluid.
Step 2: Calculate the Required Flow Rate: The flow rate is the amount of fluid that needs to pass through the valve within a given time, typically measured in gallons per minute (GPM) or liters per minute (LPM). To calculate this, you need to understand the fluid’s velocity, which depends on the type of fluid and the system’s design. A flow rate that is too high or too low can result in system inefficiencies.
Step 3: Use Flow Coefficients (Cv) to Adjust Valve Size: The Cv value (flow coefficient) helps determine the valve’s capacity to allow fluid flow at a specific pressure drop. By using the required flow rate and Cv, you can calculate the exact valve size needed to achieve the desired flow under the given system conditions.
By aligning these factors—pipe size, flow rate, and Cv—you can calculate the correct valve size that balances flow capacity and pressure control for your system.
The Role of Pipe Diameter and Pressure Drop in Valve Sizing
Understanding the pipe diameter and pressure drop is essential for accurate valve sizing, as these factors directly influence how the valve will perform in the system.
Pipe Diameter and Flow Velocity: The diameter of the pipe plays a key role in determining the required valve size. A larger pipe diameter typically requires a larger valve to ensure adequate flow. The flow velocity within the pipe should also be considered, as too high of a velocity can cause erosion or increased friction, leading to a greater pressure drop across the valve.
Pressure Drop and System Efficiency: Pressure drop refers to the reduction in pressure that occurs as fluid flows through the valve. If the valve is too small, it will create a significant pressure drop, which can reduce system efficiency and increase energy consumption. A larger valve may not restrict flow as much, but if it’s too large, it can result in excessive fluid velocity or turbulence, which could cause wear or loss of control.
When selecting the valve, you need to ensure that the pressure drop remains within acceptable limits for the system’s operation, ensuring the system maintains efficiency without excessive energy usage.
Flow, Pressure & Hydraulic Conditions in Valve Sizing
Accurate valve sizing depends heavily on understanding how flow rate, system pressure, and fluid characteristics interact—especially in hydraulic environments. These factors collectively determine how well a valve will perform in terms of efficiency, control, and longevity.
Flow Rate and Its Role in Valve Sizing
Flow rate is a critical sizing factor—it directly affects how much fluid can pass through the valve and how much resistance or pressure drop will result. If the valve is too small, it will restrict flow, causing pressure drops and reducing efficiency. If it’s too large, it may offer poor control and increase energy waste due to turbulence.
Determining Flow Requirements:
- High-flow applications (e.g., industrial systems) need larger valves to accommodate volume.
- Low-flow systems (e.g., residential plumbing, small HVAC circuits) need smaller, precision-controlled valves.
To match the valve to your flow needs, use the Cv (flow coefficient) value, which represents how much flow a valve allows at a 1 psi pressure drop:
Q=Cv×√ΔP/SG
Where:
- Q = Flow rate
- ΔP = Pressure drop
- SG = Specific gravity of the fluid
Pressure and Hydraulic Considerations
In hydraulic systems, flow is controlled using high-pressure fluids, often under variable and demanding conditions. Valve sizing in this context requires even more precision.
Pressure Rating:
Hydraulic valves must be rated for the maximum operating pressure of the system. Underrated valves can fail under load, while overrated valves may be oversized and inefficient.
Viscosity & Fluid Type:
Viscosity affects flow resistance:
- High-viscosity fluids (e.g., oils) require larger valves to reduce pressure loss.
- Low-viscosity fluids (e.g., water) can use smaller valves, assuming appropriate pressure ratings.
Design Features for Hydraulic Precision
For hydraulic applications, it’s not just about flow and pressure—valve design matters too:
Responsive flow control is essential for systems requiring rapid changes in pressure or direction.
Throttling capability allows fine control of flow.
Conclusion
In conclusion, accurate ball valve sizing is essential for achieving optimal system performance, extending equipment lifespan, reducing costs, and enhancing safety. By carefully measuring the right dimensions and using the right tools, you can ensure that your fluid control system runs smoothly, efficiently, and safely for years to come.
FAQ
How do I measure the bore size of a ball valve?
To measure the bore size, use a caliper or micrometer to measure the internal diameter of the valve’s flow path. This size directly affects the flow capacity of the valve.
What’s the difference between NPS and DN?
NPS (Nominal Pipe Size) is the US standard measurement, usually in inches, while DN (Diameter Nominal) is the metric equivalent, measured in millimeters. Both refer to the pipe size, which should be matched with the valve size for compatibility.
How do I calculate the correct valve size for my system?
To calculate the correct valve size, consider the required flow rate, the pressure drop across the valve, and the pipe diameter. Use a Cv value calculator to match the valve’s flow capacity with your system’s needs.
Why is valve seat size important in valve sizing?
The valve seat ensures a tight seal when the valve is closed. It’s important for preventing leaks, maintaining pressure, and ensuring the valve functions properly under pressure and flow conditions.
What happens if I choose the wrong valve size?
Choosing the wrong valve size can lead to flow restrictions, pressure drops, increased energy consumption, premature valve wear, or system failure. It’s crucial to select the right size to avoid inefficiencies and costly repairs.
Can I use an online valve sizing calculator to choose the right valve?
Yes! Online valve sizing calculators are a great tool. By entering your system’s flow rate, pressure, and pipe size, they can help you quickly determine the correct valve size, saving time and ensuring accuracy.