A ball valve’s mechanism consists of a spherical disc (the “ball”) that rotates within the valve body to regulate flow, either opening or closing the passage. However, as simple as this mechanism sounds, the operation of a ball valve depends heavily on the handle used to control the ball’s movement. The ball valve handle is a key component determining the valve’s functionality, ease of use, and safety.
What Are Ball Valve Handles?
A ball valve handle is the part of the valve that allows the operator to control the flow of fluid through the valve. It is directly connected to the valve’s internal mechanism, specifically the ball, which rotates to either allow or restrict the flow. Depending on the type of handle, it can either be manually operated or automated, with each design offering distinct advantages based on the application.
Role in the Valve Mechanism
The handle works in tandem with the ball inside the valve body. When the handle is turned, it rotates the ball within the valve. The ball has a hole (or port) through its center, and when the valve is in the open position, the hole aligns with the flow path, allowing fluid to pass through. When the handle is turned to the closed position, the ball rotates 90 degrees to block the flow, effectively stopping any fluid from passing.
In many cases, the ball valve handle also serves as an indicator of the valve’s position. For example, a lever handle may be parallel to the pipeline when the valve is open and perpendicular when it is closed. This simple yet effective visual cue helps operators quickly understand the valve’s state.
How Ball Valve Handles Control Fluid Flow
Ball valve handles operate by applying torque to the valve stem, which in turn rotates the ball inside the valve body. The movement is usually either manual or automated, depending on the type of handle installed:
Manual Handles: These include lever handles, which are typically used for small to medium-sized valves. Operators apply direct force to open or close the valve.
Automated Handles: These include electric or pneumatic actuators that control the valve’s position automatically, often used in large-scale industrial operations where frequent adjustments are necessary.
The design of the handle—whether a lever, handwheel, or actuator—dictates how much force is required, how quickly the valve can be opened or closed, and the overall user experience.
Importance in Different Industries
Ball valve handles are essential across a wide range of industries, ensuring smooth operation and safety in fluid control systems. Here are a few examples:
Manufacturing: In manufacturing plants, ball valves control the flow of liquids and gases in the production lines. The handles make it easy for operators to control flow rates and manage the system’s pressure.
Plumbing: Ball valve handles are common in residential and commercial plumbing systems. They provide easy on/off control for water flow, often installed in areas like water meters, irrigation systems, and water heaters.
Chemical Processing: In industries where hazardous fluids are involved, such as in chemical plants, ball valve handles provide precise control over the flow of potentially dangerous substances, helping ensure both safety and efficiency.
Oil & Gas: In the oil and gas sector, ball valve handles are crucial in managing the flow of petroleum and natural gas through pipelines. Their ability to quickly open or close the valve under high pressure is critical for safety.
Common Types of Ball Valve Handles
When it comes to ball valve handles, several designs cater to different operational needs, environments, and industries. Let’s break down some of the most common ball valve handle types, each with unique features, designs, and applications.
Lever Handles
Design and Function: Lever handles are the most common and straightforward design for ball valves. They consist of a long arm (lever) that’s attached to the valve stem. When the lever is turned, it rotates the valve ball, opening or closing the flow path. Lever handles typically feature a quarter-turn mechanism, meaning the handle only needs to be rotated 90 degrees (a quarter turn) to fully open or close the valve.
Best Use Cases and Industries: Lever handles are ideal for quick and easy manual operation of ball valves. They are most commonly used in residential, commercial, and industrial plumbing, as well as in oil & gas, water treatment plants, and chemical processing where frequent, rapid valve operation is required. Their simple design makes them perfect for smaller valves or environments where users need to open or close the valve quickly without applying significant force.
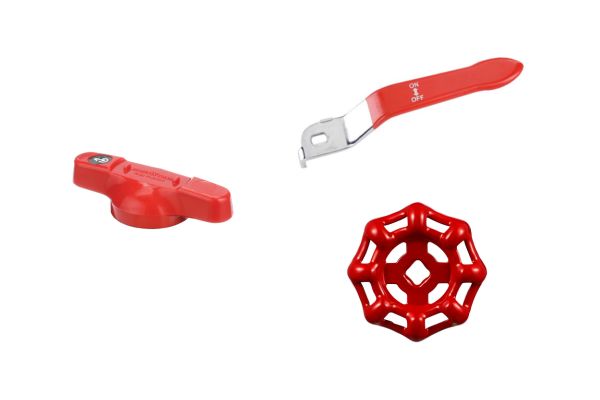
Handwheel Handles
Design and Function: Handwheel handles are more robust and designed for valves that require more precision or force during operation. A handwheel is typically a large, circular wheel attached to the valve stem, which is turned by hand to open or close the valve. Unlike lever handles, handwheels generally require multiple turns to fully open or close a valve, providing more control over the flow.
When to Choose a Handwheel Handle: Handwheels are often chosen for larger valves, valves that need more controlled movement, or situations where the fluid flow needs to be adjusted gradually. They are also preferred when greater torque is needed to operate the valve, making them suitable for high-pressure systems. Industries such as chemical processing, oil refineries, and power plants commonly use handwheels for their reliable performance in demanding environments where fine control is essential.
T-Handle and Butterfly Handle
Differences Between T-Handle and Traditional Lever Handles: The T-handle design is a variation of the lever handle, featuring a shorter, T-shaped handle that offers better grip and more control when turning. T-handles are often seen in applications where the user requires more leverage to operate the valve but still within a manageable range. In contrast, traditional lever handles are longer and more suitable for quick, high-torque operation, while T-handles offer a bit more precision for moderate force applications.
Specialty Applications: Butterfly handles, a variant of T-handles, are often used in applications where space constraints or a compact valve design are critical. The butterfly shape allows for easy gripping and operation, especially in systems where the valve needs to be operated in a restricted area or in tight spaces. T-handles and butterfly handles are frequently seen in agricultural systems, hydraulic equipment, and large industrial piping systems, where both durability and user control are necessary.
Lever Handle vs Handwheel: Which One Is Right for You?
When selecting a ball valve handle, the two most commonly considered options are lever handles and handwheel handles. Both serve the same purpose of controlling the ball valve, but they have distinct differences in terms of design, functionality, and suitability for specific applications. Let’s explore the advantages and considerations for each handle type and help you decide which is best for your needs.
Lever Handles
Quick Operation and Compact Design Lever handles are designed for fast, efficient operation. With a simple quarter-turn mechanism, they can quickly open or close the valve, allowing for rapid adjustments in flow. The compact design makes them ideal for situations where space is limited, and speed is a priority. Lever handles are especially popular in smaller ball valves where the flow control does not require precise adjustments.
Ideal for Smaller Valves or Quick Shut-off Lever handles are commonly used in smaller ball valves found in residential plumbing, HVAC systems, and some industrial applications. Their ability to provide a rapid on/off operation makes them perfect for applications that demand quick shut-off capabilities, such as waterlines, gas systems, and hydraulic systems.
Handwheel Handles
Greater Torque and More Controlled Operation Unlike lever handles, handwheel handles offer greater torque, which is the force needed to turn the valve. This is due to the mechanical advantage provided by the rotating wheel design. Handwheels allow for more controlled valve operation, which is especially useful when precise adjustments to flow rates are required. This makes them ideal for applications that need finer control over the fluid or gas being regulated.
Preferred for Larger Valves or Precise Flow Control Handwheel handles are typically used on larger ball valves or valves that regulate high-pressure systems. They are well-suited for industrial applications, such as in chemical processing, oil and gas production, and high-pressure water systems, where operators need to control the flow gradually or make more precise adjustments. The handwheel’s design makes it easier to operate valves that are not easily turned with a lever due to their size or pressure levels.
Feature | Lever Handle | Handwheel Handle |
Operation Type | Quick, quarter-turn | Gradual, continuous turn |
Torque Requirement | Low torque for quick adjustments | More effort is required,but offers precision |
ldeal Size of Valve | High torque for more controlled, precise operation | Larger valves requiring high torque and precise control |
Common Applications | Residential, quick shut-offs, general industrial | More effort is required, but offers precision |
Ease of Use | Easy to operate, quick response | High-pressure, industrial flow control, large systems |
Space Considerations | Compact, can fit in tight spaces | Requires more space due to wheel size |
Speed | Fast, immediate shut-off | More effort is required, but offers precision |
Key Considerations for Ball Valve Handle Selection
Choosing the right ball valve handle is essential for ensuring the smooth operation, longevity, and safety of your system. Several factors should be taken into account when selecting the ideal handle for your application. Let’s dive into the key considerations that will help guide your decision-making process.
Environmental Factors
Environmental conditions have a significant impact on the performance and durability of a valve handle. It’s important to consider:
Temperature: Extreme temperatures (both hot and cold) can affect the material properties of the handle, potentially leading to brittleness or warping. Some handles are designed specifically for high-temperature applications (e.g., steam systems), while others may be better suited for cold environments.
Pressure: Higher pressure systems often require stronger handles, as they need to withstand increased stress. For instance, handwheels with larger diameters are often used in high-pressure systems where more torque is necessary to operate the valve.
Corrosive Elements: If the ball valve is exposed to chemicals, saltwater, or other corrosive substances, choosing a corrosion-resistant handle material (such as stainless steel or plastic-coated handles) is crucial to ensure the handle lasts and remains safe to operate.
User Ergonomics and Accessibility
The ease of operation plays a critical role in the efficiency of your system. When selecting a ball valve handle, it’s important to keep user ergonomics and accessibility in mind:
Comfort and Safety: Handles should be easy to grip and operate, even for extended periods. This is particularly important in high-frequency applications or where workers will need to use the valve multiple times a day.
Space Constraints: If you are working in a confined space, a lever handle might be more suitable due to its compact size and quick operation. In contrast, handwheels require more space to rotate fully and are better suited for larger, more spacious setups.
User Skill Level: For less experienced operators, handwheels offer more controlled operation with the ability to apply gradual force, reducing the likelihood of over-tightening or damaging the valve. Lever handles, however, might be ideal for skilled operators who need fast and efficient control.
The Role of Industry Standards in Handle Selection
Depending on your industry, certain standards or regulations might influence the type of ball valve handle you can choose. Many industries have established best practices and standards for valve operations, including handle designs, that ensure safety and uniformity.
Manufacturing Standards: Certain industries, like oil & gas or chemical processing, may require valve handles that meet specific standards for pressure ratings, temperature limits, and safety features.
Certifications: Some valves and their handles need to comply with certifications, such as ISO or ANSI, especially in high-risk applications. Choosing a handle that meets these requirements ensures both compliance and operational safety.
Impact of Valve Handle Selection on System Performance and Maintenance
The handle you choose doesn’t just affect the operation of the valve; it also has an impact on system performance and long-term maintenance. Consider the following factors:
Efficiency of Operation: A poorly chosen handle can cause leaks or improper flow control, which can lead to system inefficiencies, downtime, or costly repairs. For instance, if a handle is too difficult to turn, it can cause strain on the valve stem, leading to leaks or damage over time.
Maintenance: Handles made from durable, corrosion-resistant materials typically require less frequent maintenance. However, a handle that is exposed to extreme environments (e.g., high temperatures or corrosive substances) may wear out more quickly and require more regular inspections and replacements.
Ease of Replacement: Some ball valve handles are easier to replace than others, which can affect your maintenance costs. Lever handles, for instance, can be replaced quickly, while handwheels may require more effort and time to remove or adjust due to their size and design.
Manual Ball Valve Handles vs Automated Valve Handles
When it comes to ball valve operation, there are two primary types of handle systems to consider: manual valve handles and automated (actuated) valve handles. Each has its unique benefits, and understanding their differences can help you choose the right system for your specific needs. Let’s break down these two options.
Manual Ball Valve Handles
Differences Between Manual and Automated Valve Handles
Manual valve handles require human intervention to open or close the valve. The operator physically turns the handle, which moves the internal ball mechanism to regulate the flow of fluid. This design is typically found on smaller ball valves and offers a simple, direct way to control flow without additional equipment.
Pros and Cons of Manual Operation:
Pros:
Cost-effective: Manual valves are usually less expensive to purchase and maintain compared to automated valves.
Simplicity: They are easy to operate, require no electricity or power supply, and have fewer mechanical parts that can fail.
Compactness: Manual valves are generally smaller and require less space, making them ideal for confined spaces or smaller systems.
Cons:
Labor-intensive: Manual operation requires physical effort, especially for larger valves or high-pressure systems.
Limited control: Manual handles provide less precise control compared to automated systems, which may be problematic in complex or high-precision environments.
Not ideal for remote operation: Manual valves need to be operated in person, which could be inconvenient in large facilities or hazardous environments.
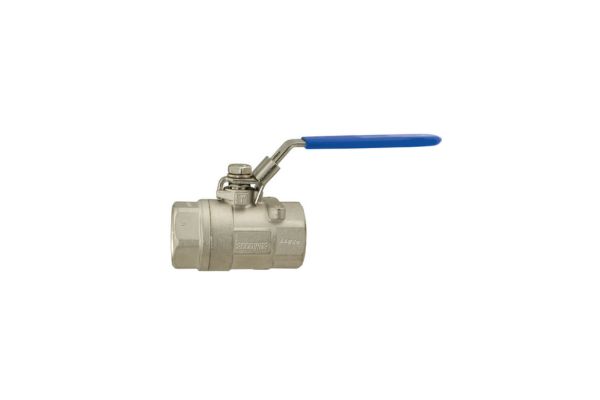
Automated Valve Handles (Actuated Ball Valves)
Advantages of Automated or Actuated Valve Handles for Larger Systems
Automated ball valves use an electric, pneumatic, or hydraulic actuator to control the valve’s position. The actuator receives a signal (either manual or remote) to move the valve into the desired open or closed position without requiring human intervention. These are commonly used in larger systems or where precision and speed are essential.
Advantages:
Precision and Control: Automated valves allow for much more precise control of fluid flow, particularly in high-pressure systems or systems that require specific flow rates.
Remote Operation: Automated valves can be controlled remotely, which is highly beneficial for large or hazardous systems where manual operation would be difficult or dangerous.
Integration with Control Systems: Actuated valves can be integrated with modern SCADA or PLC systems, offering advanced monitoring and control capabilities, making them ideal for automated plants and complex industrial processes.
Efficiency: Automation reduces the need for constant manual labor, especially in critical systems that require frequent adjustments or monitoring.
Cons:
Higher Initial Cost: Automated valve handles can be significantly more expensive than manual ones, especially when you factor in the cost of actuators, control systems, and installation.
Maintenance and Complexity: While they require less physical effort, automated systems come with additional components that can fail, requiring more maintenance and technical expertise.
Power Dependency: Actuated systems require a power supply (electric, pneumatic, or hydraulic), which could be a limitation in case of power failure.
Conclusion
Ultimately, choosing the right ball valve handle depends on your specific application requirements—from the size of the valve and flow control needs to the environmental conditions it will face. If you’re unsure which handle is best for your system, it’s always a good idea to consult with Topa.
FAQ
What is the function of a ball valve handle?
A ball valve handle is used to open or close the valve by rotating the internal ball mechanism, allowing or stopping the flow of fluid through the valve.
What are the most common types of ball valve handles?
The most common types are lever handles, handwheel handles, and specialty handles like T-handles and butterfly handles.
Which type of ball valve handle is best for small valves?
Lever handles are ideal for small valves as they provide quick operation with a simple quarter-turn mechanism.
What factors should I consider when choosing a ball valve handle?
Consider environmental factors (temperature, pressure, corrosiveness), user ergonomics, system performance, and the specific requirements of your application.
When should I choose a handwheel handle over a lever handle?
A handwheel handle is preferred for larger valves or systems that require more torque and precise flow control, such as in high-pressure or high-temperature applications.
What is the difference between manual and automated ball valve handles?
Manual handles require human operation for opening/closing, while automated handles are actuated by an external power source, ideal for larger systems requiring remote or automated control.