Brass fittings play a crucial role in a variety of applications, ranging from plumbing and gas distribution to hydraulic systems and HVAC. Their durability and corrosion resistance make them a popular choice in both residential and industrial settings. However, the effectiveness of brass fittings largely depends on the integrity of their seals. Proper sealing is essential for preventing leaks and ensuring reliable performance in various environments. This article will explore the different sealant technologies available for brass fittings and guide on selecting the appropriate sealant for specific applications.
Understanding Brass Fittings
What Are Brass Fittings?
Brass fittings are essential components used to connect various plumbing, hydraulic, and gas systems. They are primarily made from an alloy of copper and zinc, with some variations incorporating small amounts of other metals like lead or tin for improved machinability and corrosion resistance. This unique composition grants brass fittings several advantages, including exceptional durability and resistance to corrosion, which makes them suitable for both indoor and outdoor applications. Additionally, their ease of installation is a significant benefit, as they can often be joined without the need for specialized tools or techniques, making them user-friendly for both professionals and DIY enthusiasts.
Common Applications of Brass Fittings
Brass fittings find widespread use across multiple industries due to their reliability and performance. In plumbing, they are integral to water supply systems, connecting pipes, fixtures, and appliances, ensuring a leak-free flow of water. In gas lines, their robust design helps facilitate the safe distribution of natural gas and propane, crucial for residential heating and cooking. In hydraulic systems, brass fittings are used to connect hoses and tubes, playing a vital role in machinery and industrial equipment that require high-pressure fluid transfer. Moreover, in HVAC systems, brass fittings are essential for linking various components, contributing to efficient heating and cooling processes.
Challenges with Brass Fittings
Despite their advantages, brass fittings are not without challenges. One of the most common issues is leaks, which can occur due to improper installation, wear over time, or thermal expansion. Such leaks can lead to significant water loss and potential damage to surrounding areas. Corrosion is another concern, especially when brass is exposed to harsh chemicals or moisture. Factors such as pH levels and the presence of dissimilar metals can accelerate corrosion, making proper material selection and maintenance crucial. Lastly, compatibility issues can arise when connecting brass fittings with different types of materials, such as plastic or steel. Ensuring that fittings are compatible with the specific application and environment is essential to prevent failure and maintain system integrity.
Importance of Brass Fittings Sealant
Why Sealants Are Necessary
Sealants are indispensable in ensuring the optimal performance and longevity of brass fittings. Their primary function is to prevent leaks by filling the microscopic gaps and imperfections that naturally occur when fittings are connected. Even precision-manufactured threads have tiny spaces that can allow fluids or gases to escape under pressure. In applications involving water, gas, or hydraulic fluids, such leaks can lead to decreased system efficiency, environmental hazards, or even catastrophic failures.
By creating a tight, impermeable barrier, sealants effectively block the passage of liquids and gases, maintaining the desired pressure within the system. This is crucial not only for the efficient operation of the system but also for safety reasons. For instance, in gas lines, a minor leak can pose significant fire or explosion risks. In hydraulic systems, fluid loss can lead to decreased performance and potential damage to machinery.
Furthermore, sealants enhance the reliability of connections by accommodating thermal expansion and contraction. Brass fittings, like all materials, expand and contract with temperature changes. Sealants remain flexible enough to maintain a consistent seal despite these movements. This adaptability reduces the risk of leaks over time, ensuring that the system remains secure under varying environmental conditions.
Sealants also offer protection against corrosion. By sealing off the metal surfaces from moisture and other corrosive elements, they help extend the lifespan of the fittings. Some sealants contain additives that inhibit corrosion, providing an additional layer of defense. In systems subject to vibration or mechanical stress, such as industrial machinery, sealants can prevent fittings from loosening, maintaining a secure and leak-free connection.
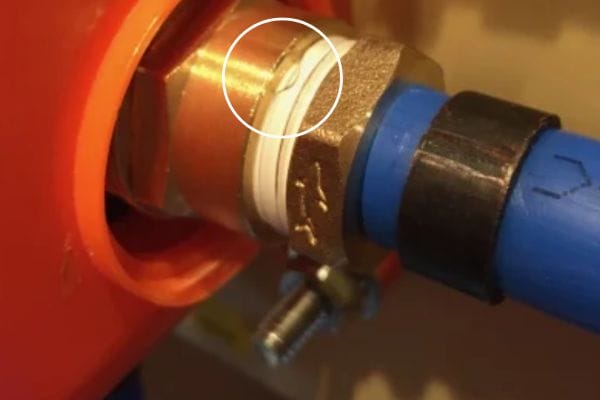
Types of Connections Requiring Sealants
Understanding the types of connections that require sealants is vital for achieving leak-free and reliable systems.
Threaded Connections:
Threaded connections are prevalent in plumbing, gas, and hydraulic systems. In these fittings, male and female threads interlock to form a connection. However, the inherent design of threads leaves small gaps that can become pathways for leaks. Sealants like PTFE tape or liquid pipe sealants are essential in these applications. They fill the voids between threads, creating a seal that prevents leaks. Additionally, these sealants lubricate the threads, allowing for tighter assembly without damaging the components. The lubrication also aids in disassembly, making maintenance tasks easier.
Compression Fittings:
Compression fittings consist of a nut, a compression ring (ferrule), and the fitting body. They create a seal by compressing the ferrule onto the tubing as the nut is tightened. While compression fittings are designed to seal without additional materials, using a specific type of sealant can enhance their performance, especially under high-pressure conditions. Sealants compatible with compression fittings, such as certain anaerobic sealants, can fill surface imperfections and provide additional leak protection without interfering with the mechanical grip of the ferrule.
Flare and Swage Fittings:
In specialized applications like refrigeration or high-pressure gas systems, flare fittings are used. These fittings rely on the deformation of the tubing end to create a seal. While typically not requiring sealants, in some cases, a small amount of sealant can be applied to the mating surfaces to ensure a complete seal, especially if the surfaces are not perfectly smooth.
Factors Influencing Sealant Choice:
When selecting a sealant for any connection type, it’s important to consider factors such as the type of media being transported (water, gas, oil), operating pressures and temperatures, and compatibility with brass and other materials in the system. Using the wrong type of sealant can lead to chemical reactions that may corrode the fittings or contaminate the media.
Best Practices:
Clean Surfaces: Ensure all threads and mating surfaces are clean and free of debris or old sealant before applying new sealant.
Correct Application: Follow manufacturer guidelines for applying the sealant, whether it’s wrapping PTFE tape in the correct direction or applying the proper amount of liquid or paste sealant.
Compatibility Checks: Verify that the sealant is suitable for the specific application, especially in systems carrying potable water or food-grade materials.
Types of Sealants for Brass Fittings
Thread Seal Tapes (PTFE Tape)
Overview:
Thread Seal Tape, commonly known as PTFE tape or Teflon tape, is a polytetrafluoroethylene film used to seal pipe threads. This thin, white tape is wrapped around the threads of pipes and fittings before they are assembled. PTFE tape fills the minute gaps between threads, creating a tight seal that prevents leaks of liquids and gases. It is widely used in plumbing, gas fitting, and other applications where threaded fittings are common.
Benefits:
Ease of Use: PTFE tape is user-friendly and requires no special tools for application. Its pliability allows it to conform easily to threads.
Chemical Resistance: It is inert to most chemicals, making it suitable for a variety of applications involving different media.
Temperature Tolerance: PTFE tape can withstand a wide temperature range, maintaining its sealing properties in both hot and cold environments.
Lubrication: The tape acts as a lubricant for threads, facilitating easier tightening and reducing the risk of damage during assembly.
Application Methods and Best Practices:
Proper Wrapping Direction: Wrap the tape in the direction of the threads (usually clockwise) to prevent it from unraveling during assembly.
Number of Wraps: Generally, 2-3 wraps are sufficient for most applications. Overwrapping can cause the tape to bunch up, leading to poor sealing.
Avoid Overlapping the End: Start wrapping a thread or two back from the end to prevent tape fragments from entering the system.
Smooth Application: Ensure the tape lays flat against the threads without wrinkles or folds to achieve an optimal seal.
Compatibility Check: While PTFE tape is suitable for brass fittings, it’s essential to verify compatibility with the system’s media, especially in gas applications.
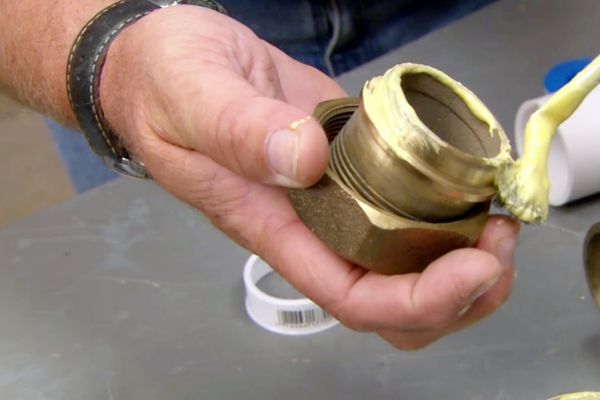
Liquid Pipe Sealants
Description:
Liquid pipe sealants are viscous compounds applied to threads before assembly. They cure to form a solid, leak-proof seal that fills gaps and imperfections in threaded connections. These sealants often contain anaerobic adhesives that harden in the absence of air when confined between metal surfaces.
Advantages and Limitations:
Advantages:
Strong Seal: Provides a durable seal that resists vibration and pressure.
Versatile: Suitable for a range of materials, including brass, steel, and copper.
Temperature and Pressure Resistant: Performs well under extreme conditions.
Limitations:
Curing Time: Requires time to cure, which can delay system pressurization.
Disassembly Difficulty: This can make future disassembly challenging without proper tools or heat.
Surface Preparation: Requires clean, oil-free threads for optimal performance.
Anaerobic Sealants (Threadlockers)
Mechanism:
Anaerobic sealants cure in the absence of air and the presence of metal ions. When confined between metal threads and isolated from oxygen, these sealants polymerize to form a hard, thermoset plastic that locks threads and seals gaps.
Advantages:
High Resistance: Excellent resistance to vibration, chemicals, and extreme temperatures.
Prevent Loosening: Secure threads to prevent loosening due to mechanical stresses.
Leak Prevention: Fill all voids, eliminating pathways for leaks.
Use Cases:
Hydraulic Systems: Ideal for high-pressure hydraulic fittings where leak prevention is critical.
Industrial Machinery: Used in equipment subject to constant vibration and temperature fluctuations.
Gas Lines: Suitable for sealing gas fittings, provided the sealant is rated for gas applications.
Pipe Dope (Paste Sealants)
Overview:
Pipe dope, or paste sealant, is a thick compound applied to threads to create a reliable seal. Composed of a base (such as mineral oil) and fillers (like PTFE or calcium carbonate), it remains pliable after application, allowing for adjustments during assembly.
Compatibility:
Brass Fittings: Generally safe for use with brass, but it’s crucial to select a pipe dope compatible with both the fitting material and the system’s media.
Media Considerations: Ensure the sealant is suitable for the specific gas or liquid being transported to prevent degradation or contamination.
Tips for Correct Usage:
Clean Threads: Remove any dirt, oil, or old sealant from threads before application.
Even Application: Apply a uniform layer covering all male threads without excess that could enter the system.
Avoid over-tightening: Assemble the fittings according to manufacturer specifications to prevent damaging threads or compromising the seal.
Storage: Keep the container sealed when not in use to prevent the paste from drying out.
Factors to Consider When Selecting a Sealant
Application Type
When selecting a sealant, the specific application plays a crucial role in determining the most suitable option. For plumbing applications, where water is the primary medium, sealants must be waterproof and capable of handling varying pressures without degrading. Common choices include PTFE tape and liquid pipe sealants designed for water exposure. In gas applications, where the risks associated with leaks are particularly high, it’s essential to use sealants specifically rated for gas, ensuring they provide a reliable barrier against flammable substances. Hydraulic systems, on the other hand, often operate under high pressure and require sealants that can withstand significant force without failure. Here, anaerobic sealants or specific liquid pipe sealants that are formulated for high-pressure applications are ideal.
Environmental Conditions
The environmental conditions in which a sealant will be used are critical to its performance. Temperature is a key factor; extreme heat or cold can impact the effectiveness of a sealant. Some sealants may lose their adhesive properties at high temperatures, while others may become brittle in cold conditions. Additionally, pressure is equally important. Sealants must be capable of withstanding the pressure exerted in plumbing or hydraulic systems. Choosing a sealant that matches the expected temperature and pressure range of the application ensures long-term reliability and minimizes the risk of leaks or failures.
Compatibility with Brass
Material compatibility is another vital consideration. Not all sealants are suitable for use with brass fittings. Certain sealants can react with brass or its alloys, leading to corrosion or degradation of the fitting over time. It is essential to select sealants specifically formulated for metal compatibility, particularly with brass, to avoid potential issues. For example, while PTFE tape is generally safe for brass, some liquid sealants may contain solvents that could corrode the brass surface. Always check the manufacturer’s specifications to ensure the chosen sealant is compatible with brass to maintain the integrity of the fitting and prevent future problems.
Ease of Application
Ease of application can significantly influence the choice of sealant, especially for professionals and DIYers alike. Some sealants, like PTFE tape, are straightforward and require minimal skill to apply effectively. Others, such as liquid pipe sealants or anaerobic sealants, may require a more careful application process to ensure they bond correctly and create an effective seal. User-friendly products can save time and reduce the likelihood of errors during application, making them attractive options for those with varying levels of experience. Additionally, if a sealant requires special tools or techniques, this may deter less experienced users from selecting it. Ultimately, choosing a sealant that balances effectiveness with ease of use can lead to better outcomes in both professional and home projects.
Conclusion
Selecting the right sealant for brass fittings is paramount to the integrity and performance of any plumbing, gas, or hydraulic system. A proper seal ensures that connections remain leak-free, secure, and capable of withstanding the operational pressures and environmental conditions they will encounter. Understanding the specific requirements of your application is essential. Factors such as the type of medium being transported, operating temperatures and pressures, and material compatibility all play significant roles in determining the most suitable sealant. By thoughtfully assessing these factors, you can make informed decisions that enhance system reliability and performance.
FAQ
Why do brass fittings need a sealant?
When brass fittings are connected, even though the threads are very precise, there may still be small gaps that can lead to leakage of liquids or gases. The use of sealants fills these gaps and prevents leakage, ensuring the reliability and safety of the system.
What type of sealant is best for brass fittings?
This depends on the specific application and environmental conditions. For general plumbing applications, PTFE raw tape (Teflon tape) is usually preferred. For high-pressure or high-temperature environments, a liquid pipe sealant or an anaerobic sealant may be required.
How do I properly apply PTFE Raw Material Tape?
Wrap the tape in the direction of the threads (usually clockwise), usually 2 or 3 turns. Make sure the tape is flat and tight against the threads, avoiding wrinkles or overlaps for the best seal.
Do sealants affect the corrosion of brass fittings?
Some sealants may react chemically with brass and cause corrosion. It is important to choose a sealant that is compatible with brass, typically PTFE raw tape and most liquid pipe sealants are safe for brass.
Which sealant should I choose for high temperature or high-pressure environments?
In high-temperature or high-pressure conditions, select a sealant designed for these environments, such as a high-temperature liquid sealant or a high-pressure resistant anaerobic sealant. Make sure the temperature and pressure ratings of the sealant meet the system requirements.
Which sealant is more appropriate if frequent removal of fittings is required?
If frequent disassembly is required, PTFE raw tape is an ideal choice because it is easy to apply and remove and will not bind threads. In contrast, anaerobic sealants may cure and make disassembly more difficult.